Production Planning for Small Manufacturers
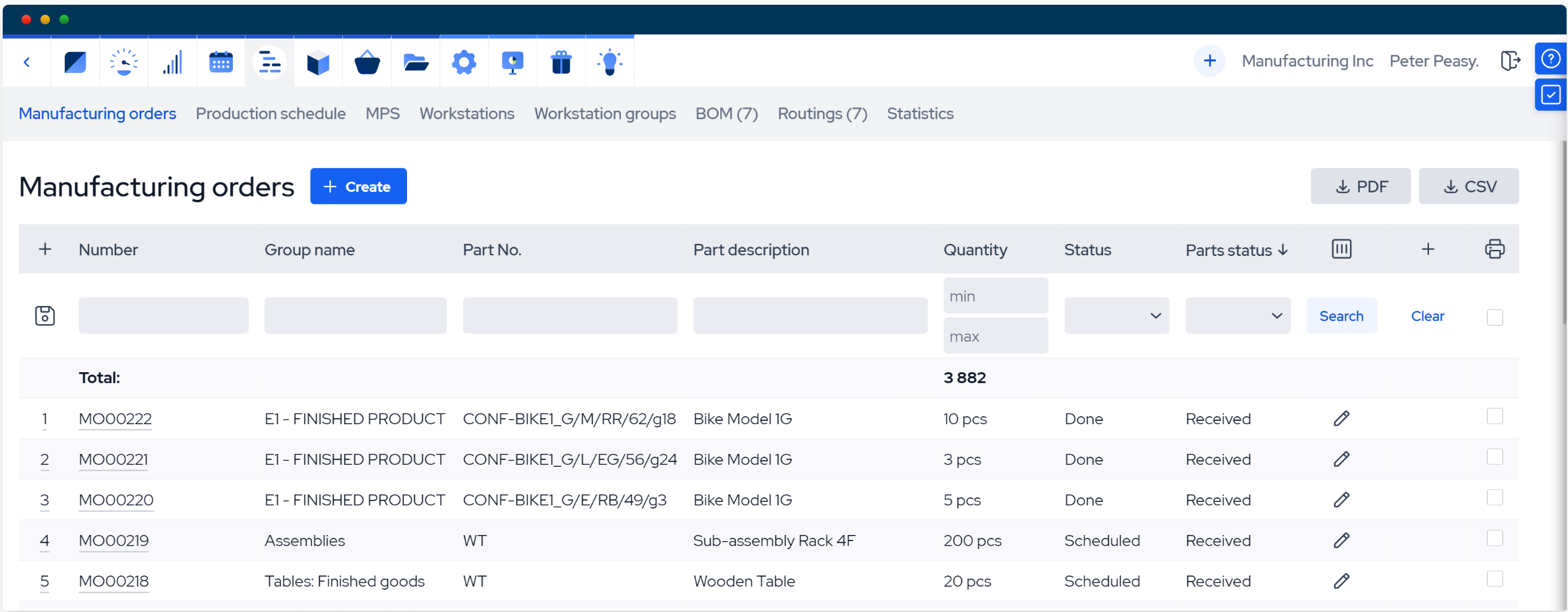
Table of Contents
What is production planning?
Production planning is the process of strategically considering and preparing all key variables of a company’s manufacturing process for an upcoming period before it begins. The process usually involves creating and following a production plan – a document or methodology detailing the key steps of the manufacturing operation. The main goals of production planning are to achieve more control over manufacturing and to maximize production efficiency in the process.
Production control means that there is a good overview of real-time workflows and the manufacturing operation writ large, that information on inventory is quickly accessible, and that there is a readiness to react immediately in an unforeseeable situation. Production efficiency, on the other hand, can be taken as a guided effort toward matching production volumes with demand, reducing overhead and production costs, eliminating waste, and shortening lead times.
In the past, thorough production planning used to be common only for large-scale manufacturers. These days, however, manufacturing processes as well as supply chains are becoming more and more complex also for small and medium enterprises. Having a well-planned-out production cycle is thus becoming a necessity for manufacturers of any size. Thankfully, means of conducting production planning have also become much more affordable and available in recent years.
Still, many business owners either plan their production using outdated methods or avoid investing time and resources into systemic planning or inventory management altogether, unaware that this can bring about opportunity loss and negatively affect competitiveness.
What is a production plan?
The production plan is the central document detailing all necessary information that an upcoming production timeline will entail. It should include all major production-related aspects of a manufacturing plant like capacities and schedules, production priorities, labor, workstations, and equipment, raw material availability, inventory movements, routings, etc.
The more comprehensive the production plan, the easier it will be to manage production. It is, therefore a good idea to also consider additional details of manufacturing, such as:
- Are there extra suppliers or backups for components with longer lead times?
- What possible bottlenecks and constraints might occur in different scenarios and how to alleviate them?
- Does the staff need additional training or will there be a need to outsource parts of production for a period?
- When and how should equipment maintenance be conducted within the planned production phase?
Thoroughness is crucial, however, the production plan also needs to be concise enough to be easy to follow. Too many loops in the decision-making process can constitute a planning constraint in itself. Included aspects should be weighed and redundant steps deduced. Another crucial factor is that once ready and accepted, the production plan should be adequately communicated to all relevant parties by the production manager.
How are production planning and production scheduling connected?
Whereas production planning is the strategic process of planning out activities related to manufacturing goods, production scheduling is the process of making the production plan work on a timeline. In other words, a production schedule is the production plan unfolding in time, and scheduling as such, is managing that unfolding.
So, if the production plan details all necessary processes required to achieve production goals for a time period, the production schedule details the sequence of these processes and their time dependence. Much like with production planning, achieving maximum efficiency is among the chief goals of production scheduling.
Also take a look at our guide to production scheduling.
The 5 steps of production planning
Production planning can be conducted in many ways. Ultimately, the right way to do it is specific to the company and its workflow particulars and requirements. Broadly speaking though, the production planning process can be divided into 5 steps.
1. Forecasting and capacity planning
First of all, there needs to be a precise understanding of the production volumes that the shop floor needs to meet in the upcoming manufacturing period. Historical sales data, surveys, market analysis, and other metrics are analyzed to create a demand forecast. This process is especially important to get right for make-to-stock manufacturers that need to avoid overstocking on finished goods inventory.
The data from the forecast can then be coupled with capacity planning. In capacity planning, production volumes for past periods, as well as manufacturing data on production capacities from the manufacturing system are analyzed to gain insights into optimal utilization rates. There are multiple analytical methods available for conducting capacity planning. In any case, comparing the data with the forecast enables making sure whether the production system is capable of meeting the anticipated demand or needs adjusting.
2. Production mapping and resource allocation
In this phase, production is mapped out in detail to determine the sequence and routings of the upcoming workflow. This involves organizing the production system and shop floor to handle upcoming production orders, planning out consecutive and sequential processes, decoupling points, as well as inventory movements to and from the shop floor. Resource allocation should be conducted as thoroughly as possible, factoring in everything from equipment maintenance to labor availability.
Raw material availability is equally important to plan for. It should be determined whether raw materials are stocked or available to order and from which suppliers, whether delivery and shipping lead times are up to date, whether some critical components can be outsourced if the need arises, or if there is an adequate backup in place for their availability. It really pays to plan out these types of questions beforehand. In essence, significant parts of the overall procurement and supply chain management fall into this phase.
3. Scheduling production
Once the capacities, production methods, and material availability are mapped, the production plan is finalized. It is now time for production scheduling i.e., the plan needs to be allocated to a timeline with detailed production schedules generated for the upcoming period. It is not uncommon for manufacturers to create a master production schedule (MPS) in this phase. The MPS shares many facets with a production plan and includes all relevant information regarding what needs to happen to produce the required quantities and when it needs to happen.
These days, large parts of the scheduling process can be simplified and organized by using manufacturing scheduling software. For example, capable MRP systems include detailed production scheduling tools like interactive Gantt charts, on-the-fly drag-and-drop rescheduling, automatic order management tools, per-worker individual schedules, etc.
4. Production and quality control
This next phase involves having a number of continuous control steps built into the production management process to ensure that the previous effort of forecasting, scheduling, and planning doesn’t go to waste and that manufacturing proceeds according to plan. Production control systems track the performance of work processes and compare them with target capacities. Quality control, on the other hand, is strategically placed steps aimed at ensuring production conforms to targets.
These tracking systems should provide near real-time feedback of the production system because it’s crucial to ensure a minimal response time, should anything unexpected occur or if readjustments need to be made. Production control methods include the continuous monitoring and reporting of workflows, tracking various production KPIs and metrics, integrating quality control checks into the manufacturing process, etc.
5. Continuous adjustment
Finally, no matter how well production is planned out and executed, forecasts and projected capacities are still approximations. The actual data on performance is only compiled as production occurs. For this reason, a concrete part of production planning is continuous adjustment and improvement.
After all, there is no real guarantee that the production plan, based on past data and the planners’ best efforts, will ideally reflect current circumstances. Production plans and production management systems should be designed to be flexible enough to allow for changes to be made on the fly. After all, a constant effort of striving toward further efficiency in all aspects of manufacturing from stock movements to scheduling is paramount for maintaining a competitive edge.
Types of production planning
As there are many different types of production workflows, planning out production is not a one-size fits all process. While the above 5 steps are adaptable to many different scenarios, let us look at three different production methods that manufacturing businesses can be set up in and how it could affect planning.
- Job shop or project planning. The job or project-based method involves manufacturing products one piece at a time. Employees are usually not differentiated and instead, all work on the same project. Used mostly in make-to-order (MTO) or engineer-to-order (ETO) workflows, the job method needs distinct planning as all phases of the production process are specific to the project. Due to the custom nature of job shop manufacturing, production plans here are usually created and followed per job or project, not per manufacturing period.
- Batch production planning. Batch production is a workflow type in which a batch of identical goods is produced at a time. It is in essence a middle way between job shops and process manufacturing. In batch production, the shop floor is set up to handle one type of goods at a time, instead of producing many different items consecutively. Each product has a different production plan according to which the shop floor is set up before manufacturing begins. If a company manufactures many different products with the batch method, batch production planning should definitely include specific additional instructions for how to optimally switch layouts.
- Flow, process, and continuous production planning. In the flow-type manufacturing workflow, large sequential assembly lines are set up to enable a continuous flow of goods. Each workstation in the production line completes a single process before the components move on to the next phase. This type of production is mostly used in make-to-stock operations with high production volumes. Here, it is crucial that the sequence and movement of goods advances like clockwork. Flow-type production plans must be extremely detailed in how production is mapped and material availability is achieved. Increasing efficiency and minimizing waste is paramount in these large-scale production operations, as a mere fraction of a percentage of raw material wasted or a few seconds longer process step can translate into huge differences by the end of a workday.
The importance of production planning
With the modern manufacturing industry becoming more and more complex and supply chains spanning across the globe, more control over the production process translates directly into more business opportunities and competitiveness. Here are some of the most important benefits of good production planning:
- Increased efficiency: By optimizing the utilization of resources like machinery, labor, and raw materials, proper production planning significantly improves operational efficiency. This translates into reduced waste, streamlined production flows, and cost savings.
- Improved customer satisfaction: A good production plan ensures timely manufacturing and delivery of goods, which leads to improved customer satisfaction. By helping to maintain consistent product quality and meeting delivery timelines, thorough production planning is a path towards building a stronger reputation and fostering long-term customer relationships.
- Reduced production time: By streamlining the manufacturing process, production planning helps to eliminate bottlenecks, better arrange the shop floor, and reduce waiting times between production stages. This leads to a shorter production cycle and lead times, enabling faster delivery of products.
- Lower production costs: By marrying demand with capacity, maximizing resource usage, and reducing downtime, production planning helps to significantly lower production costs. This increases profitability and provides more headroom for investments in other areas of the business.
- Inventory Management: Naturally, effective production planning also helps manage inventory levels to ensure that enough raw materials are in stock to meet production demand, avoiding overstocking at the same time. This prevents the added cost of both excess stock and shortages and keeps the warehouse clutter-free and organized.
- Quality Control: Quality control is an integral part of production planning. By establishing standards and checkpoints in the production process, firms can detect and correct any flaws early on. This ensures that the final product meets or exceeds customer expectations, crucial for maintaining brand reputation and market position.
- Risk Management: Production planning includes anticipating potential disruptions in the supply chain or production process and having contingency plans to address the risks. Being proactive minimizes downtime and ensures the continuity of operations even in unexpected situations. Thus, production planning contributes to the overall resilience and stability of the business.
Picking the right production planning tool
In the modern manufacturing landscape, traditional production planning methods like spreadsheets or manual tracking are becoming increasingly inadequate. The complexities and dynamics inherent in modern manufacturing simply demand a more agile, accurate, and efficient approach to managing production. Not only do manual methods fall short of managing large datasets or traceability, but they also lack the ability to handle complex production methods like multi-level bills of materials (BOM), integrated procurements, dynamic scheduling, parallel execution, etc. – crucial aspects of modern production planning.
The best solution for businesses looking to effectively navigate the complexities inherent in the manufacturing market is dedicated manufacturing software. These types of manufacturing ERPs (enterprise resource planning) provide a robust solution for managing all aspects of production from bill of materials (BOMs), routings, and inventories, to procurements, human resources, financials, and customer relations.
ERPs or MRP systems automate many of the previously manual tasks involved in production planning, helping to eliminate human error and providing more accurate data for real-time decision-making. It is no surprise then that well-implemented production planning software can significantly reduce production times, improve resource optimization, and increase profitability and competitiveness with a high return on investment.
When it comes to small and medium-sized manufacturers seeking affordable yet powerful production software, MRPeasy stands out as an easy choice. This all-in-one manufacturing software is specifically designed to meet the unique requirements of smaller manufacturers without the complexity and price tag often associated with traditional ERP systems. MRPeasy’s user-friendly and 100% cloud-based interface and comprehensive suite of tools make it perfect for managing every aspect of production planning, all in one place.
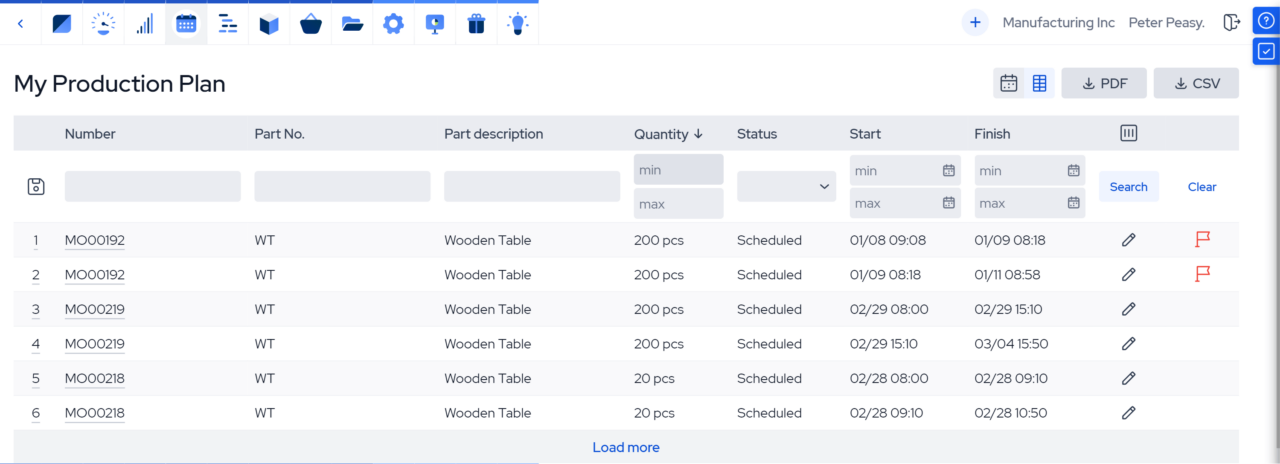
Integrated Manufacturing Software for Business Growth
-
Production Planning
Accurate automatic planning and realistic production schedule. Reschedule dynamically by just dragging and dropping manufacturing orders and operations in the calendar or Gantt chart.
-
Stock
Inventory management, stock movements, batch and serial number tracking. Set and optimize stock levels and avoid stock-outs. Have a clear history of your stock operations.
-
CRM (Sales Management)
Just a few clicks to calculate the product cost and the best delivery time. Send quotations and invoices, prepare shipments. Send confirmed customer order to production. Track the sales process all the way from quotation right down to delivery using a simple pipeline view.
-
Team
Simple environment for line workers to follow tasks on desktop or mobile device. Real-time shop floor reporting. Real-time overview of the need and availability of human resources.
-
Purchasing
Manage purchases and raise pre-filled purchase orders with a single click. Vendors, prices, lead times, it’s all there. Manage your supply chain with the help of accurate statistics. Forecast your procurement needs.
-
Accounting
Enjoy clear visibility to your business performance. Follow your cash flow, balance sheet and profit/loss in real time. Understand the profitability of the business, and more.
More than 2000 manufacturers trust MRPeasy software
Reviews

Ann Richmond
Development Director, Randr
You guys are truly the best and the software is such a lifesaver for small companies like ours. Also just a note, our ISO auditors really liked everything that MRPeasy had. Everything is documented within the system!! And we do not need any additional systems.

Benjamin Raffiani
CEO, Sox Trot
Best value in the small manufacturing space by far. With MRPeasy, our capacity doubled. It streamlined our production, and procurement so well that I’m now able to spend a lot more time on growth and sales. Extremely comprehensive and works seamlessly with Xero and Shopify.

Brandon Ames
CEO, Anicell Biotech
MRPeasy gives us the ability to track all of our manufacturing lot costs right down to the individual serial number of our products. MRPeasy provides the software as a remote service and has never been unavailable to us except in very rare maintenance windows.
Some of our customers
Start a Free Trial to Test MRPeasy - 15+15 Days for Free
MRPeasy is a simple yet powerful manufacturing ERP system that helps small manufacturers organize production. Just sign up to test MRPeasy, select the features plan that meets your requirements and access additional functionality as you grow your business.
No upfront costs
Easy to use
No credit card required