Track and report tasks in real time
- Have employees track their personal schedule and upcoming tasks in real time in the “My Production Plan” section.
- Report operation statuses on any internet-enabled device in the “Internet kiosk.” Multiple workers can use the same device as switching users is completed in a single click.
- Mark booked materials as “consumed from stock” once an operation is finished, finalizing the order and entering finished products automatically into stock.
- See worker data inputs instantly reflected in inventory and production schedules, ensuring always up-to-date process reports and better traceability.
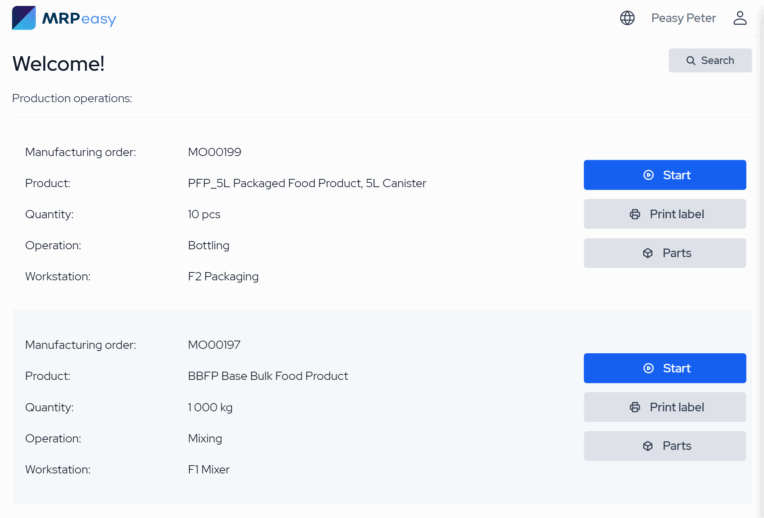