The 4 Types of Inventory and Tips on Managing Them
Inventory is any finite asset that a company uses for producing and selling its goods. In this article, we zoom in on the four basic types of inventory and how to manage them.
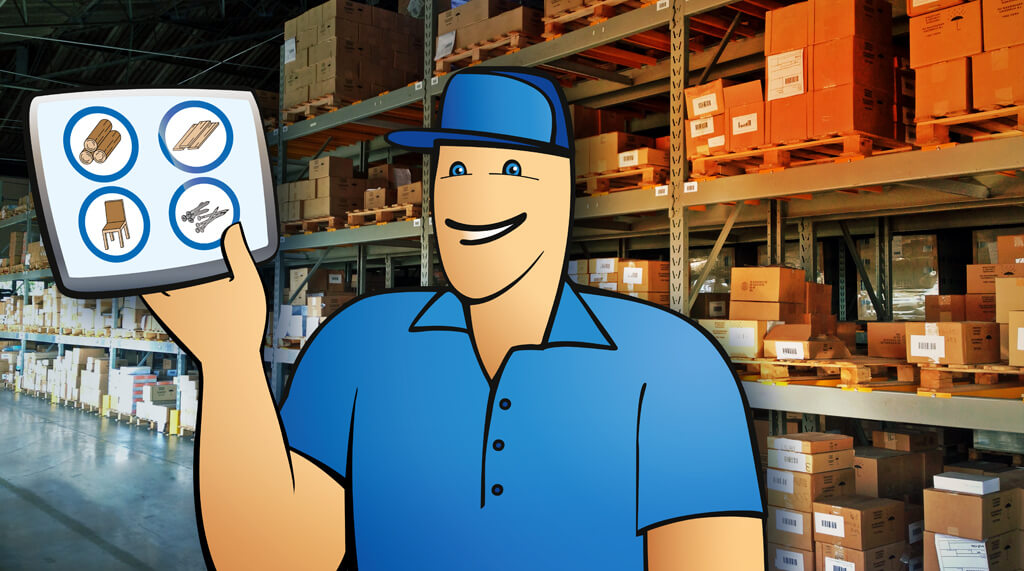
What is inventory?
Inventory is any finite asset that a business uses for producing or selling its goods. In most cases, inventory consists of physical items like raw materials, components, sub-assemblies, finished goods, as well as packing materials and maintenance equipment.
In the case of digital businesses, inventory may also include non-physical assets such as product licenses, subscriptions, etc., or anything else, as long as it has finite quantities. In this article, we will focus on physical inventories.
To keep track of stock levels and movements, inventory needs to be managed. This involves a plethora of activities like stocktaking, warehouse and stock optimization, replenishment, inventory tracking, and supply chain management. There are different ways to go about managing inventory from paper-and-pen solutions and spreadsheets to dedicated inventory management software.
The 4 types of inventory
The most common types of inventory that manufacturers and distributors use are raw materials, work in process, finished goods, and MRO, or maintenance, repair, and operating supplies. Let’s go over each of these in more detail and look at examples.
Raw materials inventory
Raw materials are items that get turned into products or sub-assemblies in a manufacturing process. All manufacturing companies add some kind of value to their procured items. This may be any type of processing or something as simple as repackaging the goods. In any case, before the value is applied, the items constitute the raw materials inventory.
Raw materials are sometimes also called direct materials, however, these terms have somewhat different connotations. Direct materials is an accounting term that signifies items directly used in the production of goods. The term is used in cost accounting to calculate the total manufacturing cost of products. Direct materials contrast with indirect materials – mostly non-inventory items that are indirectly used in manufacturing. Things like nails, glue, or anything else that isn’t counted or included in a product’s bill of materials.
Not all raw materials are basic products like timber or steel. If a company is a subcontractor or modifies other products, its raw materials are usually called components or assemblies. For example, for a table manufacturer, timber, varnish, and paint are all raw materials. For a phone manufacturer, batteries, power circuits, and screens are raw materials. In any case, the finished product of one vendor is the raw material for the next node in a supply chain before the end consumer.
Work in process (WIP) inventory
Work in process or WIP inventory constitutes all materials that work has begun on but that are not finished yet. Technically, raw materials become WIP as soon as a warehouse worker takes them from storage for processing in a workstation. They stop being WIP inventory only after completion as finished goods.
Because WIP is distinct from either raw materials or finished goods, managing this inventory has some special considerations both from an accounting point of view, as well as its storage and tracking. Most goods have many steps in their routing before they become finished goods. WIP items change form and incur added costs at each step in their routings in real-time. What’s more, most manufacturers rarely finish all started work in one go. WIP items may then be temporarily stored in decoupling points and form a decoupling inventory.
WIP items need to be tracked meticulously and accurate costs associated with them on their journey through manufacturing processes. This makes WIP inventory accounting an intricate affair best handled with a robust MRP system and good traceability practices.
Finished goods inventory
Finished goods inventory consists of all goods that have finished manufacturing and are ready to be sold. These are items that all manufacturing processes have finished on and are ready for shipping.
A note on packaging. Depending on the workflow, packaging may or may not be part of the final step of a product’s routing and hence, included in its bill of materials. In other words, it depends on the workflow, whether packaging is the last step of a product’s manufacturing process or a separate action after the fact.
It’s often included in a BOM if packaging the product is necessary to protect it from damage if the package is an important part of the final product’s branding, or if there are regulatory requirements for packaging, as is often the case in the medical and food industries. Otherwise, packaging goods before shipping may be a separate action finished just before the goods are shipped out. This, however, may complicate cost accounting as the work and materials won’t be included in the finished good’s cost.
MRO inventory
Maintenance, repair, and operations inventory, or MRO inventory, consists of items that companies use for maintaining their business and manufacturing goods but aren’t part of products’ bills of materials. This may include a plethora of items, for example, for equipment maintenance like spare machine parts or lubricants, worker gear like gloves or clothing, safety equipment like masks or goggles, facility items like lightbulbs, or consumables and support items required for assembling products like nails or glue.
Many MRO goods may be indirect materials. This is another accounting term designating items used in manufacturing that are not part of BOMs and are counted as manufacturing overhead.
In case packaging materials are not part of a product’s bill of materials, they are also usually classified as MRO inventory. If a returns system is implemented, returned goods may often be registered as MRO inventory, too, especially if damaged or requiring repairs.
Other types of inventory
In addition to the above main types of inventory which are present in pretty much any manufacturing company, many other terms denote inventory models, management types, or supply chain peculiarities. Let’s look at some of these for clarity.
Consignment inventory
Consignment inventory is a supply chain management model where goods are placed in the possession of a retailer or a third party, but the ownership remains with the supplier until the items are sold. The retailer does not pay for the inventory upfront, instead, payment is made to the supplier only when the goods are sold to the end customer.
As such, consignment inventory almost always consists of finished goods, parts or all of which have simply changed hands without being sold yet. The supplier only gets paid after their units have been sold.
Vendor managed inventory
Vendor-managed inventory (VMI) is similar to consignment in that a third party is handling a company’s goods. However, in VMI, a supplier – usually a manufacturer or distributor, is authorized to manage parts of a buyer’s – usually a manufacturer, inventory, on their behalf.
Like consignment, VMI is also a supply chain management method that does not define the type of goods being managed. In most cases, VMI consists of raw materials or sub-assemblies. VMI is almost exclusively managed using intricate inventory software which allows tracking and handling stock movements in parallel by different companies.
Pipeline inventory
Pipeline inventory, also known as in-transit inventory, refers to items that have been ordered and are currently being transported or only manufactured by the supplier but have not yet arrived. This type of inventory management is essential for understanding the total amount of inventory that a company will have at its disposal once deliveries are completed.
Pipeline inventory plays a critical role in supply chain management by providing insights into the flow of goods and enabling better production planning and forecasting. Managing pipeline inventory requires an MRP system capable of booking items into manufacturing orders before they have arrived in stock.
Dead stock
Dead stock encompasses items within a company’s inventory that have not been sold and are unlikely to be sold in the future. Although technically not finished goods or raw materials anymore, they are still part of the overall inventory. Dead stock may include obsolete inventory – products no longer in demand due to changes in market preferences or technology advancements. It can consist of damaged goods or expired or defective goods that cannot be utilized as originally intended.
Returned items
Returns inventory consists of items that have been sold and shipped to customers but are sent back to the company. This can be due to various reasons like product defects, dissatisfaction, or the wrong product being delivered. The classification of returned items may be challenging and depends on several factors like the items’ condition, company policies, or the reason for return. Generally, returned items are reclassified as finished goods inventory only if they can be sold as new.
Returned goods may also be classified into other categories like refurbished or reconditioned inventory. These items might later be sold at a discount or in a separate category. If damaged beyond repair or not cost-effective to refurbish, they might further fall into the scrap or dead stock category.
Finally, returned goods can also be deemed reverse logistics inventory, a specific classification for returned items undergoing inspection, repair, or restocking processes. Whichever the case, returned inventory is best handled with a proper return merchandise authorization (RMA) system in place.
Managing different types of inventory
Every category of inventory, from raw materials and work-in-process to finished goods and MRO supplies, presents its unique set of management challenges. However, there are underlying similarities for all four. Tracking accuracy, efficiency, and cost-effectiveness need to be assured. For instance, raw materials require precise demand forecasting in planning order sizes, and finished goods capacities need careful coordination to align production with customer demand. Though often overlooked, maintaining MRO inventory is also vital for uninterrupted production.
Central to effective inventory management is the principle of stock control – ensuring the availability of the right amount of stock at the right time. This is crucial across all inventory types to minimize inventory costs, avoid shortages, and ensure timely production and delivery.
Various stock control methods can be employed to achieve these goals. For one, ABC analysis prioritizes items based on their importance and consumption value, helping businesses focus their resources where they matter most. Economic Order Quantity (EOQ), on the other hand, optimizes order sizes to balance ordering and holding costs. The Just-In-Time (JIT) inventory system, meanwhile, aims to align material deliveries closely with production schedules to reduce the need for extensive inventory holding.
Inventory management challenges
Managing a single inventory type can be daunting in itself. Procurement, demand, production capacity, regulatory requirements, supply chain dynamics, as well as other factors need to be considered to ensure balanced stock. Here are some of the biggest inventory-related challenges manufacturers daily face.
- Avoiding stockouts and excess inventory. Striking the perfect balance between too much and too little inventory is crucial no matter the type of inventory. Overstocking ties up capital and increases holding costs, whereas stockouts can lead to missed sales opportunities and damage customer relationships.
- Traceability and regulations. Compliance with industry standards and regulations necessitates rigorous traceability of inventory, especially for raw materials and finished goods. This is compounded by the need for detailed documentation and tracking which can be particularly taxing for companies dealing with perishable items or goods requiring stringent quality control measures.
- Supplier relationships and delivery consistency. Maintaining strong supplier relationships is essential to ensure the timely delivery of high-quality inventory. This is critical for both raw materials and MRO supplies, as delays or subpar quality can disrupt the entire production process. Effective supplier management strategies can mitigate risks associated with delivery inconsistencies and quality issues.
- Demand fluctuations. Adapting to rapid changes in market demand is a constant challenge, particularly for manufacturers who use the make-to-stock production tactic. Flexibility and the ability to quickly adjust production plans and inventory levels are essential to successfully navigate sudden fluctuation.
- Optimizing inventory levels across multiple locations. For businesses operating across multiple sites or geographical locations, optimizing inventory becomes even more complex. Ensuring the right amount of each inventory type is available at the right location requires sophisticated forecasting and inventory management systems. This encompasses raw materials needed promptly on the production floor, WIP items that are location-dependent, finished goods distributed to various markets, and MRO supplies critical for maintenance tasks across all sites.
What type of inventory management solution to opt for?
Choosing the right system for inventory management is an important choice. It can be the deciding factor between maintaining a lean, cost-effective operation and grappling with mounting costs and inefficiency. An advanced inventory management solution streamlines processes, enables bulletproof stock control, enhances visibility across the supply chain, and adapts to the distinct requirements of different inventory types.
For example, a digital inventory management system or manufacturing ERP helps to keep stock levels balanced by integrating material requirements and capacity planning into the stock management process. Vendors and procurements are also integrated, simplifying managing vendor relationships and tracking supplier lead times. These systems’ manufacturing resource planning component further ensures that demand is planned out over the mid-to-long term, minimizing the risk of stockouts and production bottlenecks, for example, by utilizing the Master Production Schedule (MPS). Finally, many robust software solutions include intricate traceability tools for tracking stock movements throughout the supply chain.
In modern manufacturing, cloud-based inventory software is a viable choice for any size of manufacturing or distribution business. MRPeasy is a robust yet affordable manufacturing ERP system purpose-built for small manufacturers that combines comprehensive yet easy-to-use inventory management functionalities with a state-of-the-art MRP system, CRM platform, HR, shop floor control, and much more.
MRPeasy unifies, automates, and enhances stock control, procurement, quality inspections, serial number and stock lot tracking, order management, and many other inventory and warehouse management functions. This propels businesses towards achieving higher operational efficiency, reducing waste, and capitalizing on growth opportunities.
Key takeaways
- The 4 primary categories of physical inventory are raw materials, work-in-process (WIP), finished goods, and maintenance, repair, and operations (MRO).
- Effective inventory management requires tailored strategies to address the unique challenges of each inventory type, utilizing methods such as ABC analysis, EOQ, or JIT to maintain optimal stock levels.
- Chief inventory management challenges include achieving efficient stock control, ensuring traceability and compliance, managing supplier relationships effectively, and adapting to demand fluctuations.
- Implementing a versatile inventory management system allows businesses to streamline operations, enhance visibility, and improve decision-making across all inventory types, driving cost-effectiveness and operational efficiency.
Frequently asked questions
The four primary types of physical inventory are raw materials, work-in-process (WIP), finished goods, and maintenance, repair, and operations (MRO) inventory.
There are many inventory strategies that businesses utilize to ensure optimized inventories. Examples include ABC Analysis, Economic Order Quantity (EOQ), Just-In-Time (JIT), Material Requirements Planning (MRP), etc.
Inventory control is the process of managing and regulating the supply, storage, and access to inventory to ensure the right quantity of stock is available at the right time. Stock control involves systematically tracking inventory levels, orders, sales, and deliveries to optimize inventory flow and minimize costs associated with overstocking or stockouts.
You might also like: 11 Most Important Inventory Management KPIs in 2024