Production Routing – Definitions, Tips, and Examples
Manufacturing routing is a process as well as a document that standardizes, describes, and sequences manufacturing operations so that the product is manufactured as efficiently as possible. Effective routings can contribute to reduced costs, improved quality, accurate production planning, and the streamlined use of production resources.
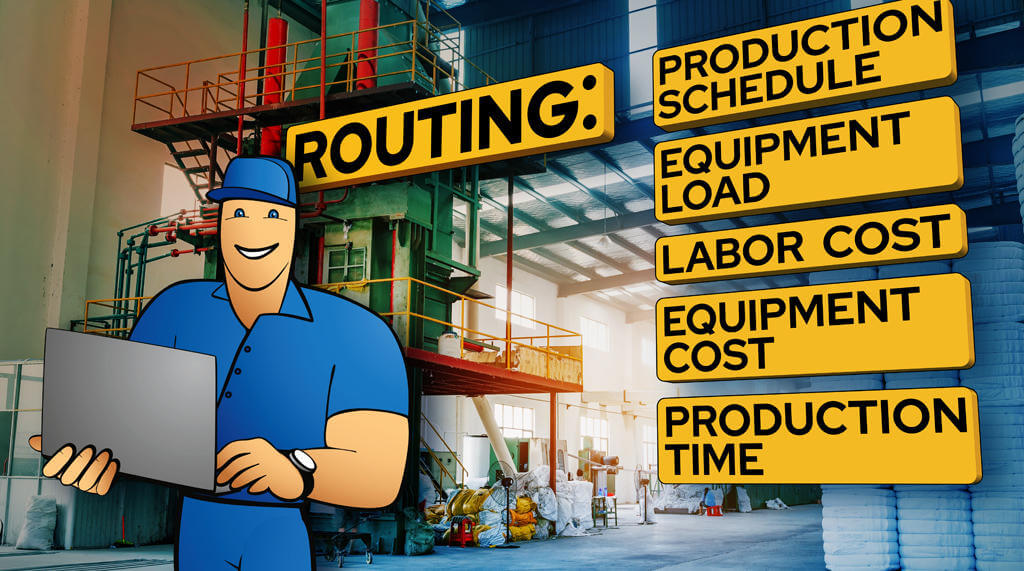
What is production routing?
Production routing means determining the order in which a product will be built, detailing the sequence of steps in the manufacturing process. Although in some cases, there are several different ways to build a product, the process of production routing aims to find the most efficient sequence possible.
For example, a textile manufacturer could route the production of an embroidered t-shirt as follows:
- Cutting the fabric
- Embroidering
- Sewing
- Packaging
While embroidering could be done after constructing the garment, doing it before sewing is much more efficient.
Manufacturing routing lays the foundation for capacity planning and production scheduling, production cost and lead time estimating, and tracking actual costs and production times – all essential functions of effective manufacturing businesses.
However, a production routing is not a technical instruction for building a product. Rather, it is a simple document that outlines:
- Workstation groups and their sequence. These are groups of work centers or pieces of equipment that perform similar operations. For example, all CNC machines would be part of a single workstation group.
- Short description of the operations. For example, “milling of cylinder head”.
- Setup times. This is the amount of time it takes to set up the workstation before the operation can be started.
- Cycle times. This is the amount of time it takes one unit or batch to go through a single production step.
In addition, companies can detail other necessary information, such as the tools used in the manufacturing operations, costs related to performing the operations, and quality control points between the production steps.
Why is production routing important?
Along with the bill of materials (a document that lists the raw materials and components that make up a product), a production routing is the core of manufacturing management. Mindfully routing your manufacturing process has several significant benefits:
- Optimized use of production resources. Determining the most effective sequence of operations allows you to utilize materials, machinery, and labor in a way that saves time and resources. In addition, standardizing your production processes allows you to set benchmarks for productivity, identify bottlenecks, and continuously improve efficiencies.
- Reduced costs. Each optimization in the production process directly translates into a reduction in cost, whether thanks to less time spent on changeovers or fewer materials wasted.
- Improved quality. The standardization introduced by proper manufacturing routing ensures that goods are produced in a consistent manner. In addition, it allows manufacturers to implement quality checks at certain stages of the production process, thereby detecting and correcting defects or errors early on.
- Accurate production planning. Defining your manufacturing routings and the cycle times of various sub-processes allows you to schedule production activities accurately, according to workstation availability. In addition, it enables you to compare actual cycle times with the ideal cycle time to identify and eliminate inefficiencies.
- Effective cost analysis. Setting up concrete production routings along with the fixed and variable costs allows you to accurately estimate production costs per order and track actual costs once the operations are performed and materials consumed.
The manufacturing routing and the bill of materials are therefore vital for achieving a consistent workflow on the shop floor that accommodates the effective manufacture of high-quality products.
Manufacturing routing and MRP software
MRP or manufacturing ERP systems are made to simplify production planning and production control in manufacturing companies. And it all starts with defining the bills of materials and routing operations. Upon those two pieces of master data, many of the modules and functions of the MRP system are built, from production cost and lead time estimations to capacity planning and production scheduling, from supply chain and inventory management to performance reporting.
Using the production routing specifically, MRP software can:
- Generate production schedules
- Estimate lead times
- Determine capacity requirements
- Track manufacturing order progress
- Calculate direct labor and manufacturing overhead costs
- Identify potential bottlenecks
MRP systems are therefore essential for making the most out of your production routings and your manufacturing operation in general.
Read more about routings in MRP software
Production routing in job shops vs. batch production vs. mass production
The production routing process could vary depending on the manufacturing environment and the company’s operational specifics. Let’s break down the difference in production routing in job shops, batch production, and mass production businesses:
- Job shops. Job shops typically deal with low-volume and highly customized products. Thanks to this, production routing in job shops tends to be very complex and variable as each job may require a different production order and use different equipment.
- Batch production. In batch production, goods are produced in batches, with a batch of items going through production steps at the same time. While small variations can exist, production routings are typically consistent in batch production companies. For example, a bakery’s typical bread production process consists of mixing, kneading, fermenting, dividing, proofing, and baking. The bakery can use the same routing to create several types of bread and a similar routing to produce a variety of baked goods.
- Mass production. In mass production, products and therefore production routings are highly standardized. The focus of manufacturing routing in mass production is on minimizing production times and maximizing throughput.
In conclusion, while the routing process always aims to find the most efficient sequence of operations for manufacturing finished products, the manufacturing environment determines whether routing has to be done continuously or not.
A step-by-step production routing procedure
The routing procedure is quite clear-cut. Here is the basic route to follow if you set out to find the best production routings for your business and manage them effectively:
- Define the operations. Determine all the operations required to create the final product.
- Sequence the operations. Put the operations in a logical order. If you assemble products from components, there could be several different ways to sequence the operations.
- Assign workstation groups. Determine the workstation groups that will handle the operations.
- Estimate cycle times. Try to estimate the time it takes to perform an operation from start to finish.
- Create documentation. Nowadays, the physical preparation of route sheets is increasingly substituted with establishing the routings within an MRP software.
- Establish quality checks. Determine the stages where quality checks could have the biggest mitigating effect so that your products would be up to the required standards.
- Review and update. Track metrics such as actual cycle times, production schedule accuracy, WIP inventory, lead times, setup times, etc. to get insights into routing inefficiencies.
Depending on the manufacturing environment, companies could also include lot size determination in their production routing process to specify the volumes that can be processed at each workstation.
Advanced production routings
In addition to the simple Operation 1 → Operation 2 → Operation 3 production process routing, some manufacturers need to use more advanced ways of routing their operations. Two of the more common types of complex routings are:
- Overlap of operations. This special routing is used if goods are produced in a way where the next production step can start while the previous one is still ongoing. For example, if you make a batch of tables, you could utilize one-piece flow or reduced batch sizes to already start painting the assembled tables while some are still in the process of being assembled. This can significantly reduce lead times, increase production efficiency, and save a lot of resources.
- Special sequence of operations. The special sequence of operations is used in case there is a need for converging or diverging chains of production. For example, when there are two independent operations that start in parallel and the next production step can only start when those two have finished.
- Parallel execution of production operations. Parallel execution is used when there is a need to divide one operation among several workstations. For example, when a manufacturing order for 1000 t-shirts comes in, that order can be divided between all available sewing machines.
- Subcontracted operations. If some operations in your production process are outsourced, you can set up subcontracting in your production routings. For example, if you use a contract packing company to package your goods, you can set the routing so that the copacker, instead of an internal workstation group, performs the packaging operation.
If you recognize the need for some of those routing methods in your company, there are not many manufacturing software solutions out there that can handle them. One of the MRP systems that can is MRPeasy.
Examples of production routings
Let’s illustrate the subject with examples from various industries.
Example 1: CNC job shop
Variables:
- Setup time 3 hours
- Cycle time 6 minutes
- CNC machine hourly rate (manufacturing overhead) $70
- Workers are assigned before starting the job, therefore the labor cost will be calculated based on their personal hourly wages.

Example 2: Electronics assembly
Variables:
- Pick-and-place machine hourly rate $140
- Oven hourly rate $70
- Computer terminal hourly rate $12
- Workers are assigned before starting the job, therefore the labor cost will be calculated based on their personal hourly wages.
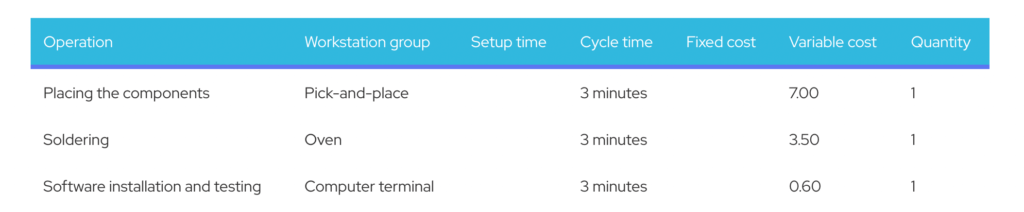
Example 3: Prefab construction with special sequence of operations
Variables:
- Preparation of frame and wall parts and preparation of internal parts takes place concurrently.
- Assembly starts once the frame and wall parts preparation (operation 1) is finished, internal parts are installed as they become available, and when all parts are installed, the construction is detailed and painted.
- Lastly, when operations 1, 2, and 3 are finished, the construction is packaged.
- All workstations hourly rate $10
- Workers are assigned before starting the job, therefore the labor cost will be calculated based on their personal hourly wages.
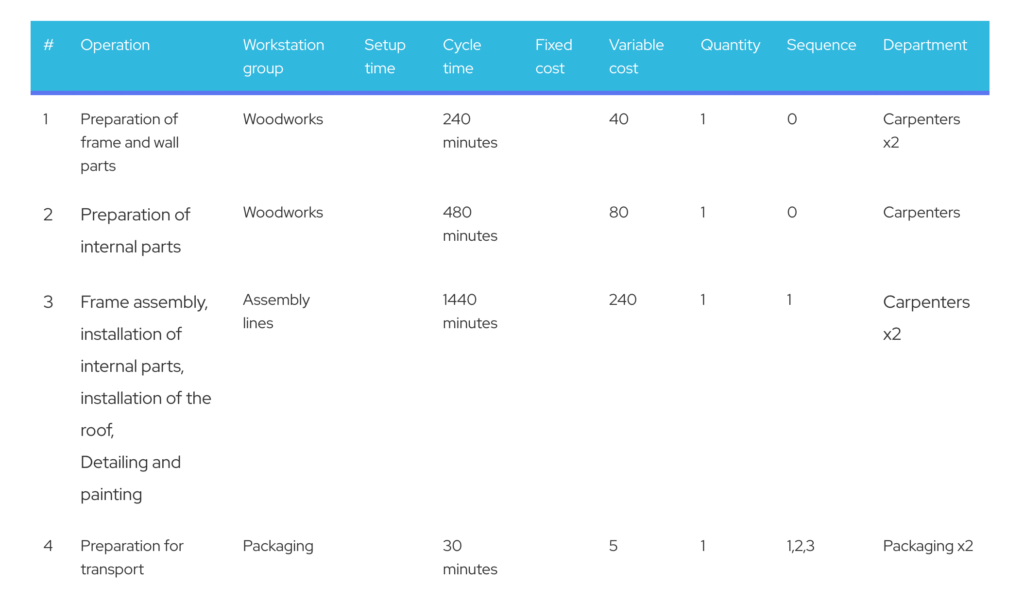
Example 4: Food processing with overlapping operations
Variables:
- Mixer batch size 80; setup time 5 min; cycle time 30 min; hourly rate $12
- Oven batch size 40; setup time 5 min; cycle time 15 min; hourly rate $12
- Packing machine batch size 4; cycle time 1.5 min; hourly rate $12
- There is an overlapping of operations as baking can start when the batter for the first 80 buns has finished mixing and packaging can start once the first 40 buns have finished baking.
- Workers are assigned before starting the job, therefore the labor cost will be calculated based on their personal hourly wages or piece payment rates.
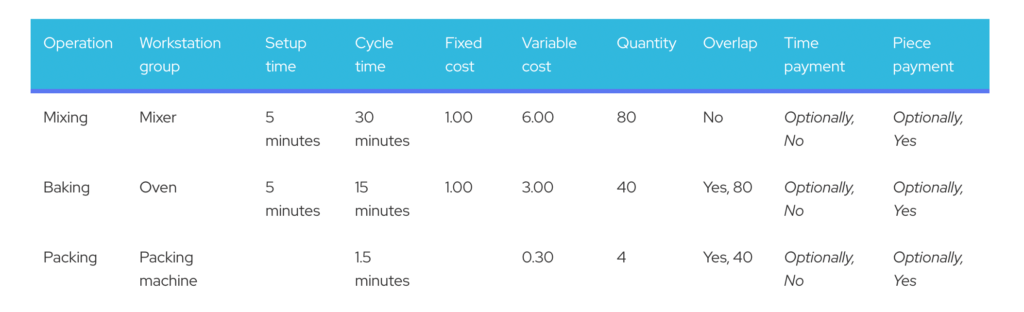
Key takeaways
- Production routing means determining the order in which a product will be built, detailing the sequence of steps in the manufacturing process.
- Manufacturing routing lays the foundation for capacity planning and production scheduling, production cost and lead time estimating, and tracking actual costs and production times.
- A production routing details the workstation groups performing each operation, the sequence of the operations, short descriptions of the operations, setup times, and cycle times. A routing can also include production cost data, the tools used, and quality control points between the operations.
- Effective manufacturing routings can contribute to greater efficiency and reduced costs.
- The best way to manage production routings, especially advanced routings such as operation overlapping or special sequences, is by using an MRP system.
Frequently asked question
The purpose of production routing is to standardize the production process and to implement the most efficient sequence of production operations, thereby reducing production costs and lead times, and increasing production efficiency.
In a garment manufacturing company, a production routing could be: 1. cutting the fabric; 2. embroidering; 3. sewing; 4. packaging. The routing should also include the workstations performing the operations, as well as setup times, cycle times, and cost data.
Routing in production control is the predefined path or sequence of operations that a material follows as it is transformed into a finished product in a manufacturing process.
You may also like: What Is Cellular Manufacturing?