Bill of Materials (BOM) – A Complete Guide with Examples
Regardless of the size of the manufacturing operation, a bill of materials (BOM) is vital for production. Manufacturers utilize them as the guide and recipe for creating a final product and as such, they are tied into production, quoting, purchasing and many other areas of manufacturing.
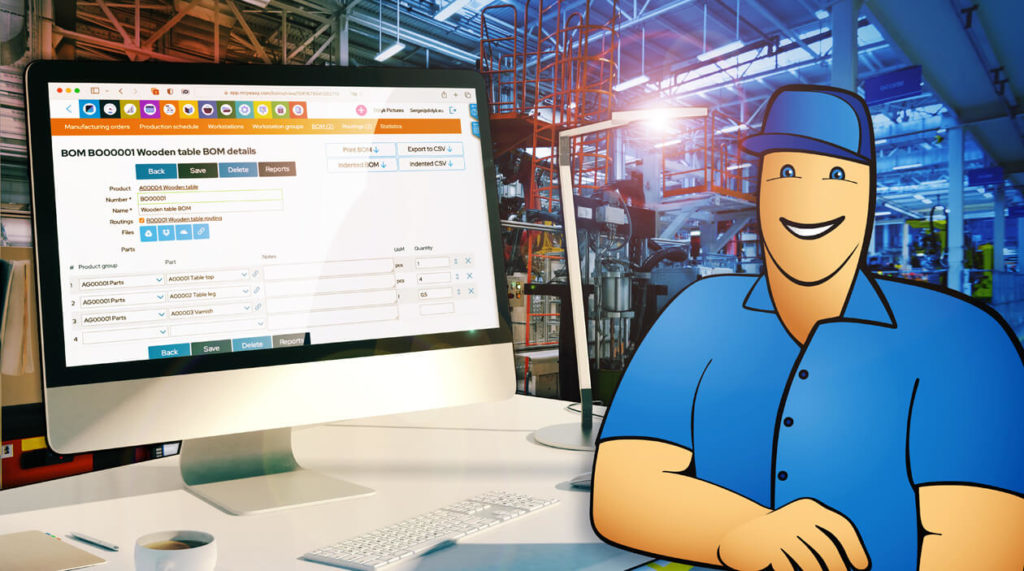
You can also listen to this article:
What is a bill of materials (BOM)?
A bill of materials (BOM) is a comprehensive list of all the materials, components, and subassemblies required to manufacture a product. A BOM essentially provides a structure for making a product repeatably every time, thereby introducing a basis for standardization in the production process.
A bill of materials will contain the quantity or volume of each component used but it may also include additional information such as:
- production routings
- production cycle times
- production costs
- waste factors
- other work-center data required to produce the finished item.
It is easy to assume that small manufacturing companies may not need structured and well-crafted BOMs because with their size and smaller product portfolio, they are well aware of all the parts and raw materials required. It is also easy to assume that because a product is simple or consists of only a small number of components (or a single component), BOMs are not necessary.
However, both of these assumptions are incorrect.
BOMs are a company’s guide and recipe for building their product. Not having a bill of materials, or having an inaccurate BOM, can lead to waste, inefficiency, and errors in the manufacturing process.
It also means that rather than having systemized process data that can be passed on to future employees as the company scales or as employees leave the company, knowledge is fragmented and siloed across several employees or software systems, leaving the company exposed to loss of repeatability.
BOMs are also important as part of materials management, being the jumping-off point for material requirements planning. In addition, having defined bills of materials aids in production process optimization.
Types of bills of materials
There are several types of BOMs used in manufacturing. Bills of materials can be divided into types by their function or their current product lifecycle stage, by their configurability, or by their structure. Let’s take a look at three different ways to categorize them:
Types of BOMs by function
1. Engineering bill of materials
The engineering bill of materials is used in the design and engineering of a new product. It is the ground zero for a finished product that lists all parts, components, and materials for the finished product as it was originally designed.
The EBOM is also used by planners, purchasing, and finance to trigger purchases for materials from existing vendors or to source vendors for new materials. They may also include drawings for new parts that will become standard in the manufacturing bill of materials.
An example of an Engineering BOM would be a company that produces a new scooter using 3D printed parts or a revolutionary technology for propulsion. It would contain a detailed list of all parts required to bring the new product to market.
2. Manufacturing bill of materials
A manufacturing bill of materials (MBOM) is the most recognized form and consists of all materials, assemblies, formulas, or components required to produce a shippable product. This type of BOM may also be tied to the required processes that are to be performed in its production.
It is also used by planners and schedulers for calculating purchase requirements as needed for an MRP or ERP run in companies that utilize automated software to integrate MRP functionality, BOMs, purchasing, and other production-related operations into a single system. Because they also include time factors such as lead time and production time, they help material planners determine when to purchase as well as when to start the production of a particular item.
An example of a manufacturing BOM would be a wooden table. The basic BOM would specify the parts and materials used: four table legs, a table top, and varnish for finishing.
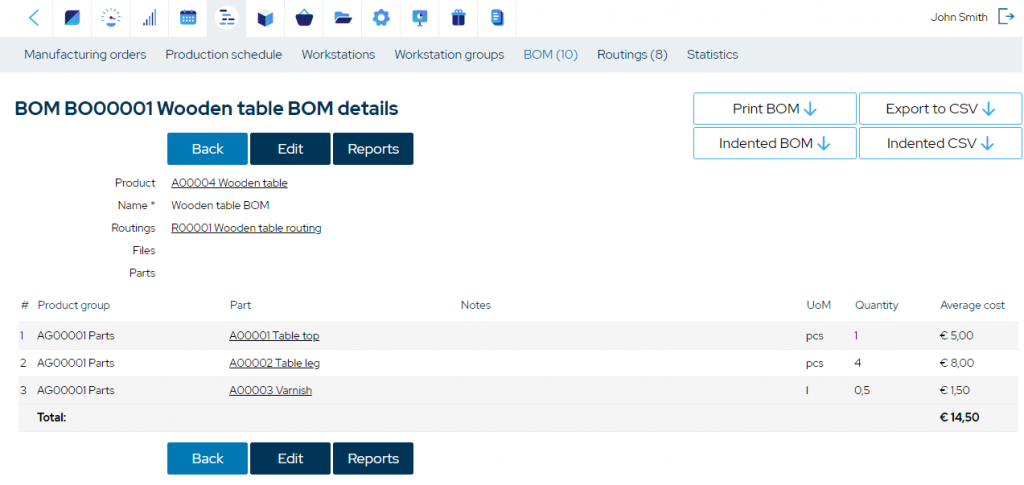
Types of BOMs by configurability
1. Standard bill of materials
A standard BOM is a type of BOM that represents a fixed, unchanging list of components and materials required to manufacture a specific product. In other words, it is a BOM for a product with consistent features and specifications across all units produced. A standard BOM is used when the products being manufactured are uniform and do not have variations or options. The components and quantities listed in a standard BOM remain the same for every unit produced.
2. Configurable bill of materials
A configurable BOM (also called a Matrix BOM, a BOM with parameters, or simply a product configurator) is a type of manufacturing BOM used to manage the production of configurable products.
Many manufacturing companies produce the same product in a variety of sizes, colors, or other parameters. Some manufacturers also produce the same goods for different brands under a “white label” arrangement. This means that the core product and bulk of manufacturing will be the same, but the final version may differ slightly depending on the customer. This could mean different packaging, volume, unit count, branding or stamping, and other differences to make the product applicable to the customer’s use or brand. The core product, however, is the same.
An example of a configurable BOM would be a furniture manufacturer offering coffee tables in various colors and finishes. The basic structure of the bill of materials would be the same, but the color would be configurable.
A bill of materials with parameters allows for easy management of products with variations in color, size, components, etc.
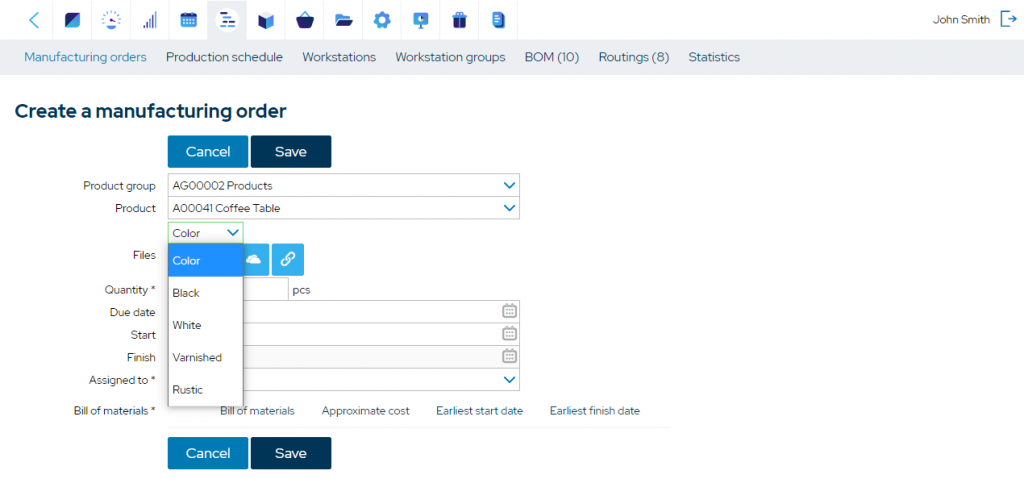
Types of BOMs by structure
1. Single-level bill of materials
This is the high-level BOM that lists the materials required to manufacture or assemble the product. If there were subassemblies, mixes, blends, or other components required to produce these materials, they are not listed and the finished component for the final manufacture is all that is shown.
Single-level BOMs may be used as the only guide for production in companies where the product is simple or where it contains few components or where no sub-processing is required downstream.
An appropriate bill of materials example for a single-level BOM would be a furniture assembly and finishing facility where components for tables would be pre-purchased, i.e. a BOM of a table would consist of four table legs, a table top, and varnish.
2. Multi-level bill of materials
Like a single-level BOM, multi-level BOMs contain materials and quantities for producing a finished good. However, for complex manufactured products, a multi-level BOM may have several sub-levels that feed into the final top-level BOM.
In multi-level BOMs, the top level acts as the parent item with the second level of one or more components that are blended or assembled acting as the child item. This process may be repeated for third, fourth, and other subsequent levels where the manufacturing company may be vertically integrated enough to produce its own subassemblies or formulations to be added to others and thus feed the next level up.
Information such as cost, lead time, work process, etc. may be added all the way down to the lowest level. This data can then be tied to integrated automation software such as MRP or ERP software to automate purchasing, plan labor, develop schedules, and other operational tasks.
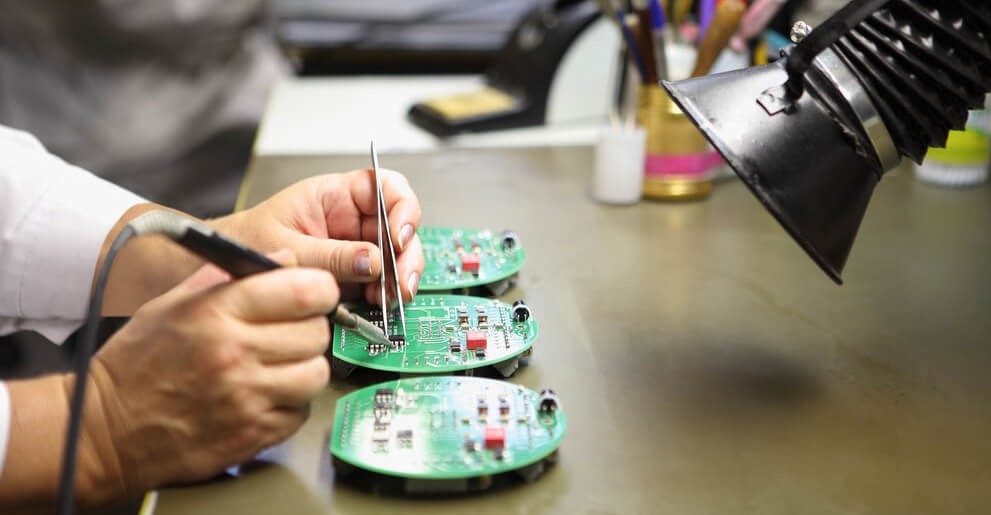
Benefits of an effective bill of materials
An effective bill of materials brings numerous advantages to product development, manufacturing, and supply chain management:
- No missed components. An effective BOM ensures that all individual parts and components necessary for the final product are documented, reducing the risk of missing items during assembly.
- More effective collaboration. Clear and detailed BOMs foster better communication and collaboration among cross-functional teams, including designers, engineers, and procurement specialists.
- Efficient manufacturing. BOMs provide step-by-step guidance for assembling products, enabling smoother production processes with minimal delays or errors.
- Precise cost estimation. A well-structured BOM aids in accurate cost estimation by outlining the quantities and costs of each component, supporting accounting and budgeting as well as finished product pricing decisions.
- Inventory control. BOMs assist in effective inventory management by defining required quantities and preventing overstocking or shortages of specific parts.
- Enhanced quality control. BOMs ensure that all components meet the required specifications, contributing to higher product quality and reducing defects.
- Customization and variants. For products with options or configurations, BOMs with parameters allow the easy creation of different product versions while sharing common components.
- Smooth supply chain operations. Supply chain managers benefit from clear BOMs that specify parts, quantities, and specifications, streamlining the procurement process and enabling supplier quality assessments.
- Reduced rework and waste. By accurately specifying components and their relationships, BOMs help avoid errors and rework during manufacturing. Because all levels of components are accurately measured for quantity and volume, waste can be measured and controlled better.
- Design iterations. During the design phase, BOMs facilitate iterations by outlining the product structure, allowing engineers to refine prototypes efficiently. Within a manufacturing ERP system with BOM version control, product iterations can be tracked and reverted back to.
- Planning and forecasting. BOMs support production planning and forecasting by detailing the materials needed for upcoming orders.
- End-to-end visibility. From individual parts to the final product, BOMs provide end-to-end visibility into the assembly process, enabling comprehensive monitoring and control.
In essence, an effective BOM serves as a blueprint for successful product development and manufacturing, driving efficiency, accuracy, and collaboration across various stages of the product lifecycle.
Who creates bills of materials?
The creation of BOMs may vary between companies or industries. In companies where products are very technical, this may be a technical designer or product designer. In many Make-to-Order companies, it may be an engineer or an industrial engineer. BOMs may also be built by those within administrative functional areas such as purchasing, planning, or scheduling provided the person entering the data has the information required to ensure its accuracy.
What is production routing?
Production routing is a document that determines the production order of an item, i.e. the sequence of operations that go into manufacturing an end product. In enterprise resource planning systems, the bill of materials and the production routing form a basis for production planning, cost accounting, and many other essential functions of a manufacturing business.
Read more about production routing.
BOM explosion vs. BOM flattening
Bills of materials serve as crucial blueprints guiding product creation, but their complexity can vary depending on the intended use. Two fundamental BOM structuring methods, BOM explosion and BOM flattening, stand at opposite ends of this spectrum.
BOM explosion involves dissecting a high-level BOM into its minutest components and materials. This process is essential for precise material planning, accurate cost estimation, and efficient procurement. By unraveling the hierarchical BOM structure, manufacturers gain a clear understanding of the intricate web of components needed, streamlining the production process and ensuring quality control. Engineering software and Product Lifecycle Management (PLM) tools play a pivotal role in automating this explosion process, transforming intricate designs into actionable production plans.
In the context of MRP software, the term ‘BOM explosion’ also refers to using the bill of materials to create demand forecasts for materials and components. For example, when a furniture manufacturer receives an order of 100 tables and 50 chairs, the BOMs of the tables and chairs are multiplied by 100 and 50, respectively, to arrive at the total quantities of the materials needed for fulfilling the order.
On the flip side, BOM flattening is about simplification. It condenses multiple levels of a BOM into a single layer, focusing on immediate parent-child relationships. This method is handy for quick overviews and simplifying communication, but it sacrifices the depth of information that a BOM explosion provides. BOM flattening is particularly useful when presenting summaries to stakeholders or for preliminary discussions, as it emphasizes the main components without delving into granular details.
Both BOM explosion and BOM flattening are integral to efficient production, each serving specific purposes. BOM explosion uncovers the details, while BOM flattening offers a bird’s-eye view. Choosing the right method depends on the task at hand, whether it’s optimizing the production line or conveying project progress to a diverse audience.
What to include in a bill of materials?
An effective and accurate bill of materials requires specific information. This is true of all BOMs but is especially true for those BOMs tied to MRP/ERP software. Without accurate, in-depth data, the lower levels of the BOM may not “roll up” correctly or accurately to the single level. Missing data also degrades the capabilities of the software and makes its benefits less pronounced.
All BOMs should include:
- BOM level. This is the framework for a multi-level BOM. By assigning a BOM level, the BOM can be “exploded” to see all relevant parts at all levels including cost, lead time, and production time.
- Part numbers. Each part in a manufactured finished product should have a part number. Part numbers can be used for both references and for ordering replenishment parts. There are several different approaches to assigning part numbers.
- Intelligent. Intelligent part numbers depict meaning. This may mean that certain numbers in certain positions indicate the date or month produced. It may also indicate an alpha designation as a partial description of the part such as using MTR for a motor.
- Unintelligent. These part numbers indicate nothing about the part and are assigned using a predetermined numbering system decided upon by the manufacturer.
- Vendor-assigned. Many companies use vendor-assigned part numbers to reduce the matching required to tie internal and external numbers together for purchasing and planning purposes.
- Part name. As parts become common on the production floor, many employees on the line will come to know them by their common name. Assigning a part name helps staff in terms of referencing the part during production.
- Part description. Like a part name, a solid part description helps identify and differentiate a part from similar items.
- Procurement type. Procurement type tells purchasing and planning how the component is made. It may indicate that it is a purchased part and needs no additional assembly before adding it to the finished good. It may also indicate a made-to-specification item or a material that will need to be altered somehow (such as drying or cooking of material).
- Quantity. The quantity is the number of each item used in the manufacture of one finished unit.
- Unit of measurement. There are many units of measurement depending on the finished good being produced. This may include units of weight (e.g. kilograms), volume (e.g. liters), and area (e.g. square feet), or simply pieces. The unit of measure used in conjunction with quantity and lead time helps determine the amount of materials needed and when they should be ordered.
- Reference design. Some products such as printed circuit boards require reference design.
- BOM notes. BOM notes provide other relevant info related to the product.
- Phase. Many products have a lifecycle. By classifying parts by where they are in the lifecycle, change management can be made easier. Some examples include “In Production”, “In Design”, or “Unreleased”. This helps track changes as they occur during the product’s lifecycle. For example, an appliance may have started its lifecycle using metal bushings on a key assembly. However, a change to ceramic bushings for performance improvement may be underway with those parts carrying the designation of where they are in development.
Tips for creating an effective bill of materials
Having an effective BOM systemizes a lot of tasks to improve accuracy and efficiency. Without a BOM, manufacturing operations must create workarounds to determine valuable information related to production and assembly. An accurate and effective BOM streamlines the production process by providing a roadmap or recipe for each finished good, freeing up valuable hourly and management time to commit to the process of production.
Here are a few tips for creating an effective BOM:
- Enter data on the front end. The best time to create an effective BOM is at the beginning of the product’s lifecycle. If there is an existing EBOM, this can be used “as is” to create the manufacturing BOM. And some MRP and ERP software allow for the migration of electronic files to partially or fully populate BOM data. Whether using an existing EBOM or through the use of CAD (computer-aided design) drawings and other media, putting in the data upfront will help ensure the accuracy of the BOM.
- Formalize a change management process. As bad as having no BOM, failing to formalize a change management plan can lead to delays, quality failure, material shortages, and other issues. A BOM is not a static document. It is a dynamic document that will change as years go by. By making accommodations for change management, accuracy can be maintained throughout the lifecycle of the product. These changes can include things like price changes, drawing revisions, part substitutions, packaging changes, part and material substitutions, vendor changes (which often require their own validation and lot control), and others.
- Consider who will use the BOM. The more details included in the BOM the better. By understanding who within the operation is going to use the BOM, you can make the right choice about the amount and depth of information to be included. Many people accessing the BOM for day-to-day tasks will not always be familiar with one another and may not even be in the same facility.
- Plan for the little things. Small things may make a big difference in the accuracy of a BOM. One example is consumables. While many may not want to go to the trouble of adding glue, tape, labels, and shrink wrap, many product lines have missed ship dates due to one of these unforgotten components. While making time to measure, cost, and quantify an application of a small amount of something such as glue may seem like a headache, it is important for the BOM to be complete.
- Formalize access to the BOM. Most people within a manufacturing company can get by with “Read Only” access, where they can view a BOM on screen or in print form. But formalizing the process of who has access to the BOM can clear up confusion and limit errors. If the BOM is part of an automated MRP/ERP software, these changes may be permission-based, where purchasing people can only change costs and engineers can only substitute parts. And in some smaller and medium-sized companies it is not unusual to appoint one or two people to make all changes as they occur, which offers the opportunity to audit proactively before the change is made. Similarly, BOMs in a cloud-based ERP system can be made accessible to contract manufacturers that manufacture parts or the whole product. Regardless of the methodology, formalizing both “Read Only” and change access will help minimize mistakes.
- Formalize the audit process. Because a BOM is a dynamic document, a formal audit process should be defined. Some finished goods that have undergone many changes during their lifecycles can have inaccuracies add up thus creating off-quality products. The audit process can look for errors such as changes in the unit of measure, (for example, changing from a vendor who sells in gallons to one who sells in liters), part substitution, drawing, and iteration changes, cost changes, new process steps related to new OEM equipment in production, and more. It is important to formally audit BOMs on a schedule, note the changes where appropriate, correct errors as soon as they are identified, and document the changes that were required during the audit.
By following these steps, you can ensure that the product is made repeatably every time. And while using Excel or other spreadsheet applications to create and manage BOMs is still possible, by using templates or building a BOM from scratch, using dedicated BOM software such as a manufacturing ERP system automates much of the process and facilitates BOM management. This allows companies to customize and tie their BOM into planning, finance, maintenance, and more.
Key takeaways
- A bill of materials (BOM) is a comprehensive list detailing all materials, components, and subassemblies required for manufacturing a product, adding standardization to the production process.
- A BOM includes quantities, costs, lead times, and other data about each item, ensuring accurate planning and execution.
- Small manufacturing companies and products with few components still benefit from well-crafted BOMs, as they ensure repeatability and prevent knowledge fragmentation.
- An accurate BOM ensures effective collaboration, efficient manufacturing, precise cost estimation, better inventory management, quality control, customization, and more.
- BOMs are categorized by their function (EBOM, MBOM), configurability (standard, configurable), and structure (single-level, multi-level), serving different purposes in product development and manufacturing.
- Start with accurate data, formalize change management, consider user needs, plan for details, control access, and implement an audit process for maintaining accuracy. Dedicated BOM software like manufacturing ERP systems can streamline the process.
Frequently asked questions
An example of a bill of materials is a wooden table, the BOM of which would list all of the components and materials used in its production: four table legs, a table top, and varnish for finishing.
A Bill of Materials (BOM) outlines components for manufacturing a product, while a Bill of Quantities (BOQ) specifies quantities and costs of materials for construction projects.
The bill of materials for a car includes various components such as the engine, chassis, transmission, wheels, interior parts, electronics, and more, specifying their quantities, relationships, and specifications needed to assemble the vehicle.
You may also like: What Is a Master Production Schedule (MPS)?