Top Manufacturing ERP Systems: Best Software Solutions for 2025
Modern manufacturers need modern production management tools. Deciding on an ERP should involve a lot of comparison and analysis. In this post, we introduce six of the best manufacturing ERP systems you should shortlist for 2025.
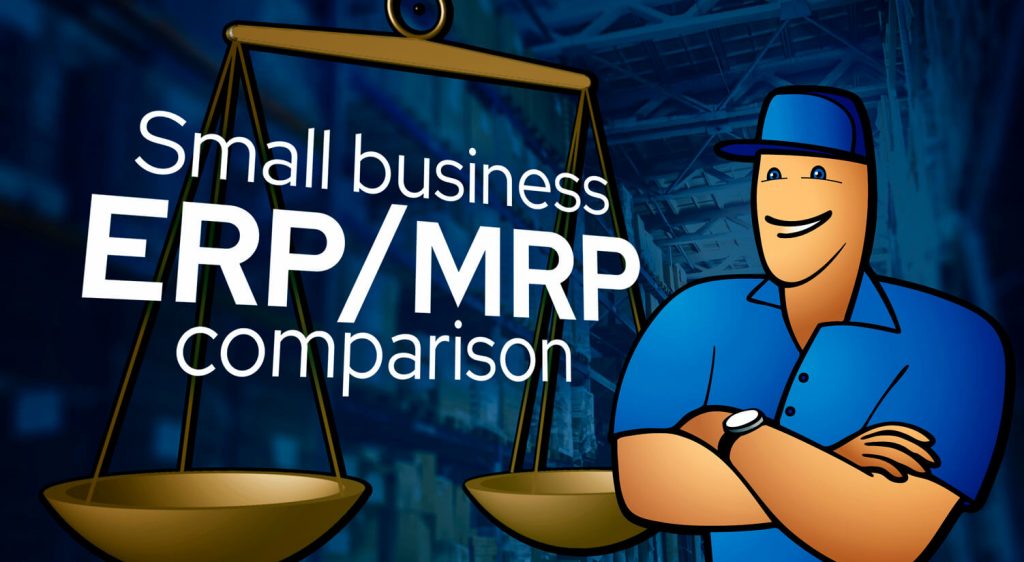
You can also listen to this article:
What is an ERP system?
An ERP system is comprehensive business software designed to unify all business processes into a single digital ecosystem. Enterprise Resource Planning software usually includes modules for customer relationship management (CRM), inventory and purchasing, supply chain management, HRM, project management, financials, and more.
ERPs integrate and automate real-time data synchronization between departments into a single database. For example, when a sale is completed on your connected e-commerce website, the relevant order data is automatically synced across all connected modules, such as inventory, production, and accounting.
ERP software has been around since the 1990s. These early systems were almost exclusively reserved for large enterprises. They required extensive on-premises implementation, often reaching millions of dollars in cost, and dedicated IT departments to maintain. Modern ERP solutions are much more versatile, often boasting fully cloud-based interfaces. They are much more affordable and easier to implement.
Are all ERPs suitable for manufacturers?
No, manufacturing ERP software is a class of ERP systems specifically tailored to companies whose business revolves around producing or distributing physical goods. It is distinct from other types of ERPs, such as those meant for service providers, engineering or tech companies, POS networks, etc.
Manufacturing ERPs include dedicated functionalities for manufacturing like production planning and scheduling, advanced bill of materials (BOM) management, demand forecasting, quality control, shop floor workflows, inventory management, etc. In short, they incorporate manufacturing resource planning (MRP) functionalities within their features.
ERP systems vs. MRP systems
An MRP system is sophisticated production software that automates and consolidates key production processes, such as material requirements planning, production scheduling, production tracking, forecasting, etc. MRP software often includes other key features manufacturers require, like inventory management, quality control, BOM control, etc.
MRP is about advanced production planning, material requirements planning, and inventory management. It’s designed to simplify workflows, increase production efficiency, reduce waste, and raise cost efficiency. Still, an MRP system is not the same as a manufacturing ERP system. The latter combines an MRP system with expanded functionalities, including CRM, HRM, financials, integrations with third-party software, and other modules.
Continue reading about the differences between ERP and MRP.
The benefits of manufacturing ERP systems
Fully integrated production management
A manufacturing ERP system brings all key business functions—such as production and inventory management, CRM, accounting, and HR—into a single platform. This eliminates the need for multiple disconnected software systems and streamlines operations across departments. The result is a unified workflow that minimizes manual data entry, reduces human errors, and improves operational efficiency.
Data-based decision-making
Manufacturing ERP systems enable companies to make more informed, data-driven decisions by providing a centralized source of accurate, real-time information. With production metrics, inventory levels, sales forecasts, and financials all in one place, managers can quickly analyze trends, identify inefficiencies, and make adjustments proactively. This is how ERPs help identify cost-saving opportunities, optimize resource allocation, and enable swift responses to market changes.
Better planning and forecasting
By automating large parts of demand forecasting and production scheduling, manufacturers can better predict material needs, allocate resources, and avoid stockouts or overproduction. This helps reduce waste, optimize inventory levels, and improve profitability by aligning production with actual demand.
Top 6 manufacturing ERP systems
The ERP market has hugely expanded in the past ten years. Today, literally hundreds of service providers are available, catering to diverse business needs, company sizes, and industries. Here are the top six manufacturing ERP systems for small and medium-sized businesses in 2025 by category.
Best for growing small manufacturers – MRPeasy
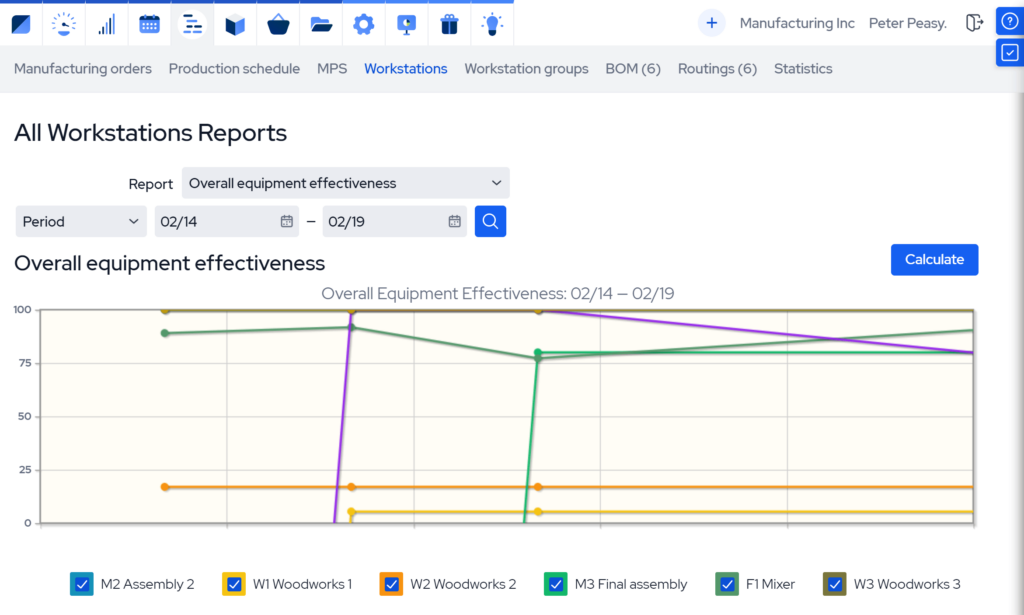
MRPeasy is a cloud-based manufacturing ERP system specifically designed for small and medium manufacturers (with up to 200 employees). Its rich feature set includes both essential and advanced functionalities that small manufacturers need the most while maintaining a simple and easy-to-use interface.
At the heart of MRPeasy lies a powerful MRP system that’s been in continuous development for more than ten years. The software is equally suitable for make-to-stock, make-to-order, or engineer-to-order companies, as well as job shops, distributors, and suppliers. Core functionality includes one-click production cost and lead time estimating, prefilled purchase order and manufacturing order generation, comprehensive material planning and bill of materials (BOM) management, dynamic production scheduling, and robust inventory management with end-to-end traceability.
There’s also a built-in MES (manufacturing execution system), a CRM module, workforce management tools, a B2B customer portal, quality control, and a host of more advanced functionalities like master production scheduling, product configurator, a returns system (RMA), and much more.
MRPeasy includes integrations with a growing number of third-party apps, such as accounting platforms Xero and QuickBooks, e-commerce platforms Shopify and WooCommerce, fulfillment platforms ShipStation and Ware2Go, CRMs Pipedrive and Salesforce, and workflow automation software like Zapier.
MRPeasy is available in four editions – Starter ($49/user), Professional ($69/user), Enterprise ($99/user), and Ultimate ($149/user). The system is highly scalable—basic functionality can be set up easily without having to pay upfront for advanced features. Users can easily jump to the next tier when needed to gain access to more advanced functionalities. The software’s price beyond the first 10 users is also greatly reduced in all editions ($79/10 users), so adding users as the company scales further increases its already impressive cost efficiency.
MRPeasy is designed as a self-service production management system, meaning it’s intuitive enough for independent implementation in most cases. However, an authorized consultant program is also available for those needing external assistance. A comprehensive user manual and FAQs, an extensive library of informative demo videos, and a highly professional support team help with setting up.
What customers say
MRPeasy’s clients laud the software for its ease of use and implementation, rich feature set, and great balance between functionality and value for money. The average time for successful implementation ranges from around two weeks to a few months. The software is also a good fit for micro-companies with 1+ employees, as it provides an easy-to-grasp overview of all core processes and enhances production and inventory visibility. MRPeasy consistently receives high praise for its responsive support team.
Alternative for integrated workflows – Microsoft Dynamics 365 Business Central
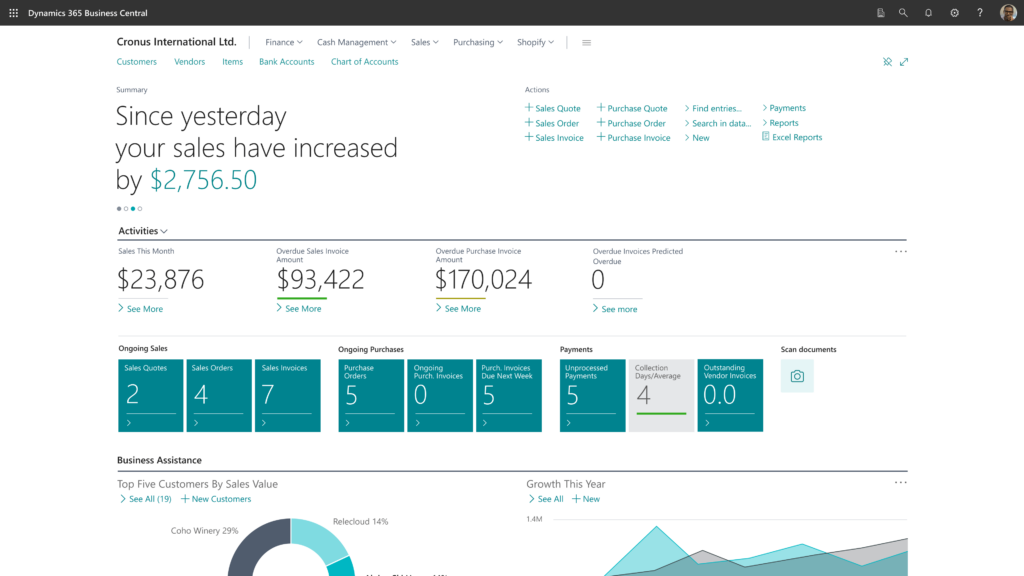
Microsoft Dynamics 365 Business Central is a cloud-based version of the on-premise Microsoft NAV ERP designed mostly for small and medium-sized enterprises. It’s a diverse ERP platform with features like financial accounting, business intelligence, human resources management, project management, CRM, inventory, purchasing, and more. Also included is a field service option for companies with extensive field technician operations that wish to integrate these into the ERP platform.
Business Central has considerable core features out of the box. However, it really shines in terms of its capability to bake in custom functionalities and integrate with Microsoft’s Power Platform. Business Central can also be hosted on Microsoft’s own cloud platform, fully integrating it into the Microsoft family of digital services like Outlook or Teams.
While add-ons make Business Central a great option for companies with complex processes or custom requirements, they usually add considerable cost to implementation. Adopting companies must cooperate with certified ISVs (Independent Software Vendors) for workflow programming, and the overall ERP implementation also mandates clients to partner with a certified partner company for programming and deployment.
Business Central has an intuitive user interface. However, onboarding and navigation can be cumbersome for new users. This gripe is often compounded when advanced customizations and integrations with third-party apps are installed.
The cost per user after infrastructure and implementation is $70 per user per month for the Essentials plan and $100 for the Premium plan, which adds a comprehensive manufacturing module. It is important to note that implementation costs for Business Central often reach tens of thousands of dollars and beyond.
What customers say
Business Central’s users report good integration between business operations, especially with Microsoft’s cloud platform. The software’s ability to allow custom programming is also reported as a strong suit. Negatives include an uneven level of customer support and a high required skillset to utilize self-service resources. Business Central is also reported to have a higher-than-average learning curve, especially when adopting customizations.
Alternative for omnichannel inventory management – Cin7
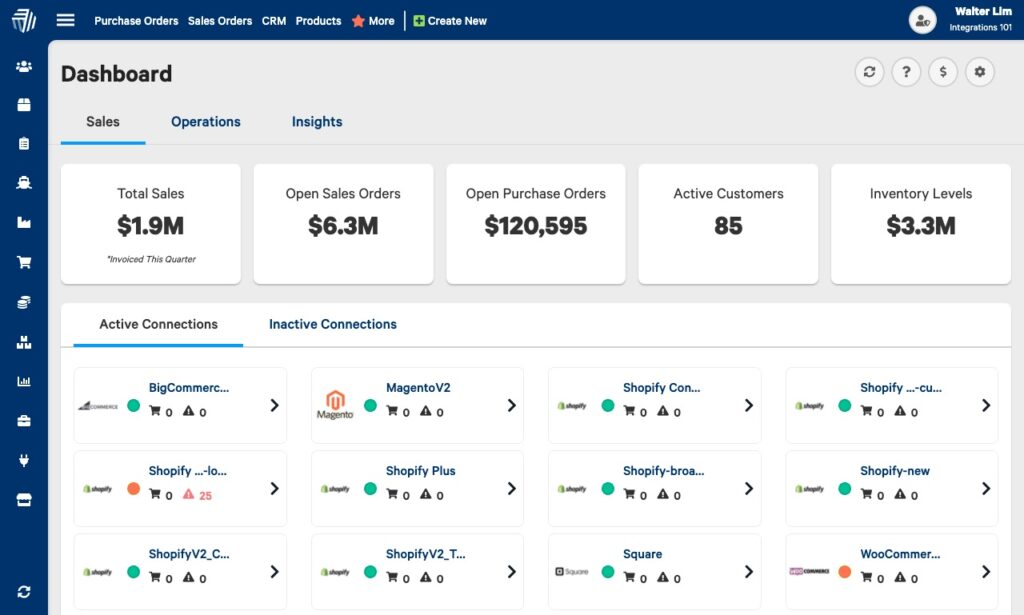
Cin7 is a cloud-based ERP solution that caters to businesses with multi-channel inventory and warehousing needs, making it a strong choice for small-to-medium wholesalers and manufacturers with distribution-intensive operations. Its main advantages lie in a strong inventory and CRM platform and extensive integrations with distribution, fulfillment, 3PL, POS, and e-commerce apps.
Cin7 enables comprehensive real-time visibility over inventories, warehouses, and supply chains. This allows companies to streamline their inventory and supply operations across multiple locations, manage vendor relationships and procurements, and easily track purchase orders and lead times.
The system also includes a production management module. However, Cin7’s primary strengths lie in inventory control, order automation, and warehouse management rather than advanced manufacturing features found in other manufacturing ERP solutions. Cin7’s production management features may feel limited in scope for manufacturers with complex assembly or production processes.
Cin7 offers flexible pricing plans starting at $349 per month, with advanced options available for $599 and $999 monthly for larger businesses needing increased order volume support or enhanced automation, reporting, and customization options. Due to its rich feature set, implementing Cin7 often requires assistance. The company provides onboarding packages and dedicated implementation support to simplify getting started.
What customers say
Cin7’s customers report a robust and scalable inventory management system, a relatively smooth user interface, and a good level of customization. The software’s host of supported supply and commerce-oriented integrations also function well. On the downside, Cin7 tends to be on the expensive end of inventory software for the intended business scale. It can also have a considerable initial learning curve, especially for setting up more complex operations.
Alternative for multi-location operations – Acumatica Cloud ERP
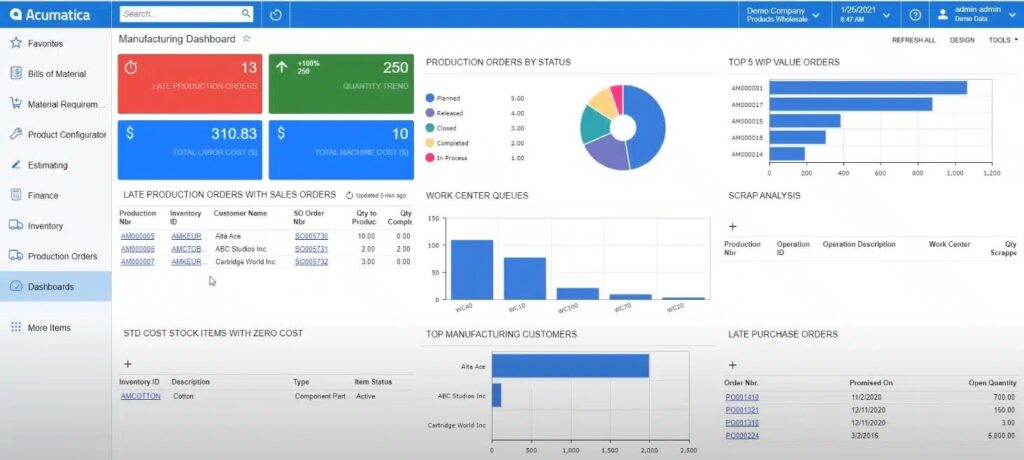
Acumatica is a cloud-based ERP platform tailored to companies of most sizes, save for microbusinesses or multinational corporations. It’s designed for diverse business cases and offers an impressive suite of functionalities. Its core strengths lie in project management, financials, CRM, and cost control. It has an intuitive consumption-based licensing system that allows unlimited users, making it a practical option for organizations with many departments or fluctuating headcount. Its robust API and low-code customizations support complex integrations, making Acumatica among the more adaptable all-purpose ERPs on the market.
Acumatica Cloud ERP also has a dedicated manufacturing edition complete with MRP, multi-level BOMs, production orders, and scheduling tools. It’s a capable module that integrates well with the software’s overall ecosystem. However, it can feel cumbersome for companies that need to manage manufacturing-centric operations without added complexities.
Acumatica’s impressive flexibility inevitably brings with it complexity. Implementations often involve lengthy deployments, and reliance on external partners is commonplace. Advanced features can be difficult to configure without technical assistance or previous insight. Licensing and maintenance costs also tend to accumulate, which can make Acumatica a costly option for companies looking for a streamlined, out-of-the-box ERP solution.
For these reasons, Acumatica is less suited to small and scaling manufacturers or distributors that prioritize rapid deployment, ease of use, and minimal third-party dependence. Running costs depend on the chosen modules, scale of business, and type of license. A typical implementation will cost a small or medium-sized company around $50,000 and up, with yearly costs also mostly landing in the five digits.
What customers say
Customers appreciate Acumatica’s modern interface, solid performance, and the ability to customize processes to match business needs. Many highlight the scalability of the platform and its flexibility across departments as major strengths. On the downside, users frequently mention a steep learning curve, especially during setup, and note that achieving full functionality often requires significant support from implementation partners or in-house IT resources.
Alternative for comprehensive business management – Odoo
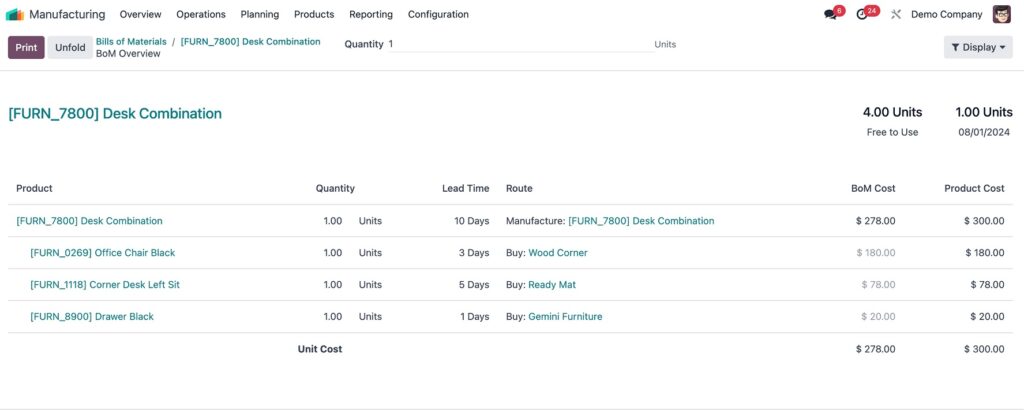
Odoo is an open-source ERP platform known for its extensive range of business applications. With modules for everything from human resources, CRM, and financial management to quality management, e-commerce, and marketing, Odoo is highly adaptable and can support nearly every area of a business. This makes it one of the best ERPs for companies who want an all-in-one system for centralizing diverse business functions alongside their core manufacturing processes.
Odoo’s manufacturing module includes essential tools like BOM management, routing, production scheduling, and work order tracking, offering solid support for basic manufacturing operations. However, some manufacturers may find its production features less specialized compared to dedicated manufacturing ERPs, as it is designed to balance functionality across all business areas rather than offer in-depth production features.
While Odoo’s manufacturing features capably support standard workflows, it lacks the depth in production planning and scheduling, production tracking systems, and shop floor control that manufacturers with more intricate manufacturing processes might require.
One of Odoo’s greatest strengths is its modular pricing model. Businesses can start with the free version, which gives access to one module, or opt for the paid Standard edition for multiple modules. There’s also a Custom edition that enables the creation of customized interfaces and lets users host Odoo on-premise. Pricing for the software’s paid editions starts at around $12/user, with additional costs depending on the number of modules used.
Odoo’s flexibility comes with one notable caveat. Its implementation process can be complex, and companies often need to work with certified Odoo partners to set up custom workflows and adapt modules to their exact requirements. This extensive customization can be complicated and often comes at a significant cost.
What customers say
Odoo is touted as very diverse in catering to different business needs due to its well-executed modularity. The software is reported to be intuitive and easy to use, great for tracking various business metrics, and highly customizable to suit different business needs. Often mentioned negatives include implementation and integration complexity, overly complicated workflows on some modules, a long learning curve, and at-times basic onboarding and support documentation.
Alternative on-premises manufacturing ERP system – SAP Business One
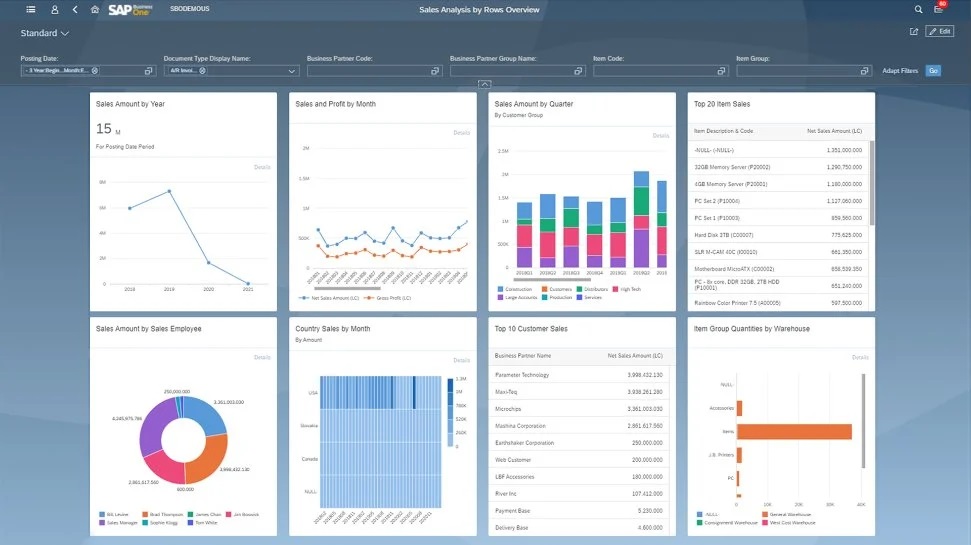
SAP Business One is an ERP solution developed to address the needs of small and medium-sized enterprises (SMEs) with complex manufacturing and business processes. The software has an extensive suite of modules for accounting, CRM, procurement, inventory management, production planning, quality control, and more. Although Business One is also available as a cloud service, this manufacturing ERP is best suited for on-premise deployment as it unlocks enhanced security and customization options for the software.
The system includes all essential manufacturing features like material requirements planning and bill of materials management, order tracking, shop floor control, and others. Business One also includes robust inventory tracking with serial and batch number management, providing ample traceability for stock, production, and quality control. The ERP’s capabilities further extend into financial management, project management, and business intelligence, enabling strategic insights across various business areas.
SAP Business One is highly customizable, allowing businesses to tailor workflows, fields, and reports to fit very specific manufacturing and business needs. However, this is also its biggest design flaw. Because the platform can accommodate such a wide range of customizations and features, implementation requires extensive professional assistance.
Opting for an on-premise rollout, which provides greater data control and system stability, involves even more setup and maintenance costs and can introduce disruptions or downtime as the new system is installed. As a result, Business One’s total implementation costs often reach hundreds of thousands of dollars.
What customers say
Customers report that SAP Business One is a powerful choice for manufacturers with complex production requirements, offering a level of customization and process control that many cloud ERP solutions cannot match. The ERP system’s ability to offer bespoke solutions is also well-received by users. On the other hand, Business One has a steep learning curve, especially during the implementation phase, and can be challenging for companies without ERP experience. The setup, customization, and maintenance costs are also considerable and don’t always pan out as initially planned.
What to look for in a manufacturing ERP
Adopting a manufacturing ERP system for your company is a big decision that requires careful deliberation and planning. Before jumping on the ERP bandwagon or choosing your next solution, here are a few suggestions to consider.
- Scalability. Choose an ERP system that can grow with your business. Ensure that the software can scale to support additional users, more complex workflows, and advanced features as your company expands. Look for flexible pricing plans that allow you to add features or upgrade without significant restructuring. Also, ensure that your data remains safe as you scale, with reliable options for data backups and seamless transitions when switching between modules or moving to higher service tiers. Scalable ERPs offer an extended lifetime and superior long-term value by adapting to your business’s changing requirements over time.
- Decide the level of manufacturing management you require. Your company might only need basic production workflows and inventory tracking. Or it could benefit from advanced IoT solutions, automatic production tracking, parallel execution, and a dozen other sophisticated features. The choice is entirely yours, so consider your current needs and future goals carefully. When deciding on integrations and automation levels, ensure the ERP solution aligns with your specific operational needs.
- Find the best ROI. Your ERP investment should deliver tangible improvements in your operations. Look for an ERP system that aligns with your manufacturing goals and offers benefits like time savings, inventory optimization, production efficiency, and data accuracy. To evaluate ROI, consider factors such as improved order fulfillment rates, reduced lead times, lower inventory carrying costs, or enhanced customer satisfaction. The right ERP should ultimately make your business more competitive by streamlining processes and enabling data-driven decision-making.
- Plan out expenses thoroughly. Capital expenditures can be especially critical for small and medium-sized companies, and user costs are only part of the equation. Over the ERP’s lifecycle, you may face additional costs for data entry, training, software updates, maintenance, support, and more. Thoroughly map out your expenses and leave some budget flexibility for unexpected costs along the way.
You might also like: Top 10 Mistakes Small Manufacturers Make with ERP Software