Manufacturing Operations Management (MOM) Processes and Tips
Manufacturing Operations Management (MOM) is essentially the integrated management of a manufacturing business. Referring to both manual and software-supported systems, it covers functions from inventory management and production planning to quality management and maintenance.

You can also listen to this article:
What is Manufacturing Operations Management (MOM)?
Manufacturing Operations Management (MOM) is a methodological approach to managing, controlling, and optimizing manufacturing processes. It encompasses a wide range of functions, including production planning, scheduling, quality management, maintenance, and labor management, among others.
Manufacturing operations management can describe both software-based manufacturing management systems as well as general methodologies and practices used to manage a manufacturing business.
In both cases, MOM bridges the gap between shop floor management and the administrative side of a business, thereby playing a critical role in achieving operational excellence and maintaining a competitive advantage in the manufacturing industry.
Why is MOM important?
Manufacturing operations management is the backbone of any manufacturing business, ensuring the seamless operation of production processes. At its core, MOM encompasses the comprehensive oversight of everything from the shop floor to the delivery of the final product. It integrates various functions such as production planning, scheduling, quality control, and inventory management.
Here are the key reasons why MOM holds such significance:
- Optimizes resource use. MOM maximizes resource utilization, thereby reducing waste and minimizing downtime. This optimization leads to increased throughput and significant cost savings.
- Improves product quality and compliance. By implementing rigorous quality control measures, tracking inventory movements, and closely monitoring production processes, MOM ensures products meet or exceed customer expectations and comply with industry standards for quality and traceability. This reduces the risk of recalls and safeguards the manufacturer’s reputation.
- Supports strategic decision-making. With access to real-time data and analytics, MOM allows managers to make informed decisions quickly. This adaptability is crucial for adjusting production plans, managing inventory, and responding to market or supply chain changes.
- Enhances customer satisfaction. Efficient operations management ensures timely delivery of high-quality products, leading to increased customer satisfaction and loyalty. This, in turn, can lead to repeat business and positive word-of-mouth.
- Facilitates continuous improvement. MOM provides a framework for continuous analysis and improvement of manufacturing processes. This ongoing refinement process helps in identifying inefficiencies and implementing solutions to increase overall productivity.
In essence, manufacturing operations management is essential for any manufacturing business aiming to compete. It not only improves operational efficiencies and product quality but also empowers businesses to respond swiftly and strategically to various challenges.
Subprocesses of MOM
Manufacturing Operations Management encompasses a broad array of subprocesses, each critical to the seamless operation and efficiency of your manufacturing business. Here are some of the most important subprocesses within MOM:
Production planning and scheduling
This involves determining what to produce, in what quantity, and by when. Effective planning and scheduling optimize the use of resources, ensure timely delivery of products, and balance demand with production capacity. Tools such as the Master Production Schedule (MPS) help with long-term planning while production calendars, Gantt charts, and material requirements planning aid in shorter-term production scheduling.
Inventory management
Keeping track of raw materials, work-in-process (WIP), and finished goods to ensure that production runs smoothly without unnecessary capital tied up in stock is essential in manufacturing. It involves managing stock levels and order fulfillment, and minimizing holding costs. Using software to manage your inventory is essential to ensure that your data regarding standing inventory as well as your requirements is reliable.
Supply chain management
SCM coordinates and optimizes the flow of materials, information, and finances as they move from supplier to manufacturer to wholesaler to retailer to consumer. It aims to ensure that the right products are available at the right locations, at the right time, and at the right cost. Improving communication, strong management of supplier relationships, and streamlining procurement practices play a major role in this.
Quality management
Quality management ensures that the products meet certain quality standards and specifications. This subprocess includes quality control measures throughout the production process, from incoming raw materials to the final inspection of finished goods. Consistently tracking inspection results enables you to investigate the root causes of your quality issues.
Maintenance management
This focuses on the upkeep and repair of manufacturing equipment to ensure operational efficiency, minimize downtime, and extend the lifespan of machinery. Just a simple system for tracking uptime or days from last maintenance can make a huge difference in a small manufacturing business.
Shop floor control
Shop floor control involves the management of production operations on the shop floor, including workforce allocation, monitoring of production progress, and real-time adjustments to ensure that production targets are met. This is often achieved with a manufacturing execution system (MES). For example, tracking your processing times enables you to identify improvement opportunities related to specific workstations or employees.
Performance analysis and continuous improvement
The use of metrics and analytics to monitor the efficiency and effectiveness of manufacturing operations is vital for any business. This data-driven approach supports continuous improvement initiatives, identifying areas for enhancement and implementing strategies to boost productivity and reduce costs.
7 tips for effective manufacturing operations management
Incorporating modern technologies and methodologies is key to streamlining operations and boosting productivity. Here are seven tips that can help you improve your MOM practices:
Embrace digital transformation
Embrace digitalization by implementing comprehensive Manufacturing Operations Management software or a manufacturing ERP system. This software integrates production management, resource planning, purchasing, sales, etc., providing a unified platform for overseeing all manufacturing operations, from the planning stage to the plant floor to finished products.
Read more about MOM software.
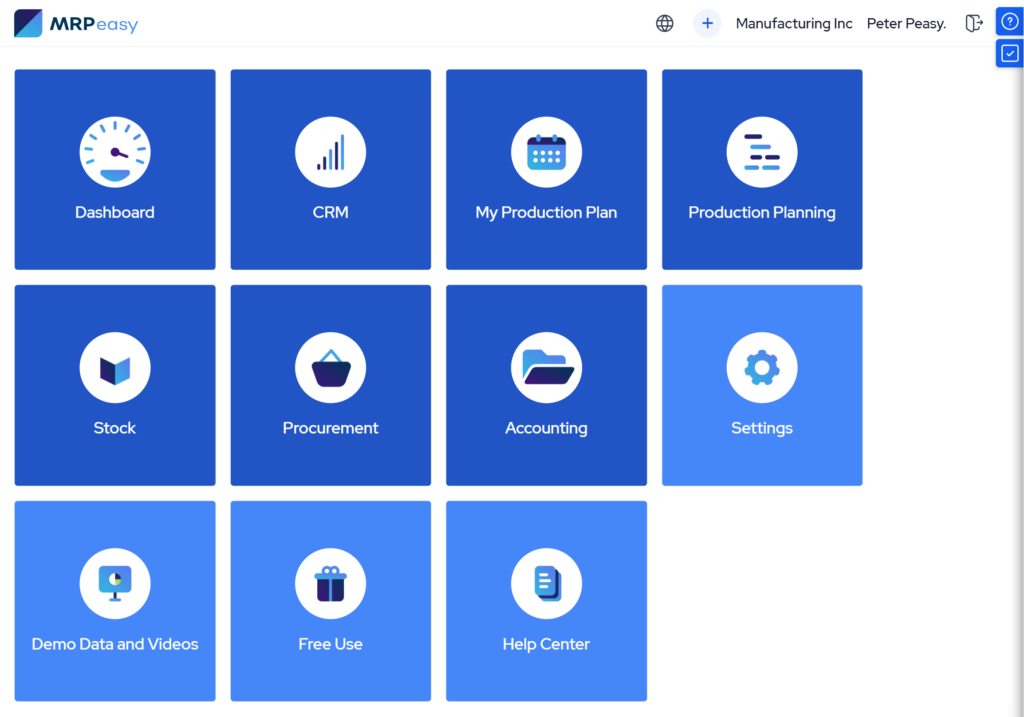
Implement lean manufacturing principles
Adopt lean manufacturing techniques to minimize 8 different types of waste and improve operational processes. By focusing only on value-adding activities, you can streamline business processes, improve product quality, and increase overall efficiency. For example, use production management software to accurately forecast your material requirements, minimizing the risk of stockouts and overstocking.
Focus on key performance indicators (KPIs)
Pull data from the shop floor to identify and monitor critical manufacturing KPIs related to production efficiency, quality, and performance. Use these metrics to identify improvement opportunities, targeting areas such as machine uptime, cycle times, overall equipment effectiveness (OEE), and yield rates for optimization. Introduce KPI visualization to make your data easily digestible.
Improve quality control and traceability
Use a manufacturing ERP system to achieve end-to-end traceability and improved quality control throughout the lifecycle of your products. ERP helps in tracking materials and components from receipt through to finished products, ensuring compliance and quality standards. Track your quality inspection results, record all events related to your materials and products, and find the root causes of any quality issues.
Invest in workforce development
Develop a skilled and knowledgeable workforce through continuous training and education. Empowered employees are more likely to identify improvements, contribute to efficiency, and maintain quality standards. Giving your employees the tools to improve and succeed can significantly raise their level of motivation.
Strengthen your supplier partnerships
Foster strong relationships with suppliers and partners to ensure transparency and reliability in the supply chain. Implementing collaborative platforms, such as for vendor-managed inventory, can improve communication, reduce lead times, and mitigate supply chain risks. Strong supplier relationships, in turn, can help you reduce both ordering and material costs. Be sure to continuously assess your vendors’ performance and communicate both their strengths and weaknesses to them.
Gradually introduce automation
Begin the journey towards manufacturing automation by eliminating repetitive, manual administrative tasks that can be automated with an ERP system. Start with simple automation in areas like inventory tracking or data entry, and progressively move towards more complex automation in production management and production control. Integrating automation technologies on the production lines and within operational workflows not only boosts efficiency but also improves the accuracy of tasks such as production scheduling, requirements forecasting, and resource planning.
Key takeaways
- MOM integrates all aspects of manufacturing operations, from production planning and scheduling to quality and maintenance management, ensuring a cohesive approach to manufacturing efficiency and productivity.
- The role of MOM in bridging the gap between shop floor activities and administrative management is crucial for achieving operational excellence and maintaining a competitive edge in the manufacturing industry.
- Through optimizing resource use and implementing strict quality control measures, MOM significantly improves manufacturing efficiency and ensures the production of high-quality products that meet customer expectations and compliance standards.
- Access to real-time data and analytics provided by MOM enables managers to make quick, informed decisions regarding production adjustments, inventory management, and response to market or supply chain changes.
- MOM facilitates a continuous analysis and improvement process that identifies inefficiencies and implements solutions to enhance overall productivity, ensuring the manufacturing operation’s adaptability and long-term sustainability.
- The gradual introduction of automation, leveraging digital transformation through MOM software, and adopting lean manufacturing principles are strategic moves to streamline operations, boost productivity, and improve product quality and traceability.
Frequently asked questions
MOM software typically offers robust integration capabilities with other enterprise systems such as Customer Relationship Management (CRM) and Human Resources Management Systems (HRMS). These integrations are facilitated through APIs (Application Programming Interfaces) or middleware solutions such as Zapier, allowing seamless data exchange and workflow automation across departments.
Implementing MOM in small manufacturing enterprises often involves challenges such as limited budgets, fewer IT resources, and a need for simpler, more intuitive systems. Solutions for small enterprises may include cloud-based MOM solutions that offer scalability, lower upfront costs, and user-friendly interfaces. Large enterprises, on the other hand, may face complexities related to integrating MOM across multiple sites, standardizing processes, and managing vast amounts of data.
MOM plays a significant role in promoting environmental sustainability by optimizing resource use, reducing waste, and facilitating the efficient use of energy. For example, MOM software can help identify overproduction, underutilization of resources, and inefficient processes that lead to waste, enabling companies to implement corrective measures. Furthermore, MOM can support the integration of recycling processes and the use of environmentally friendly materials by tracking material usage and ensuring compliance with environmental standards. By providing insights into energy consumption patterns across different production stages, MOM also aids in implementing energy-saving measures.
You may also like: ERP vs. MRP – Picking the Right Manufacturing Software for SMEs