Continuous Improvement – Implementing CI in Manufacturing
In today’s competitive manufacturing landscape, continuous improvement (CI) serves as a crucial strategy for enhancing efficiency, quality, and overall business performance. In this article, we explore various continuous improvement models and provide practical insights on how manufacturers can implement and benefit from CI initiatives.
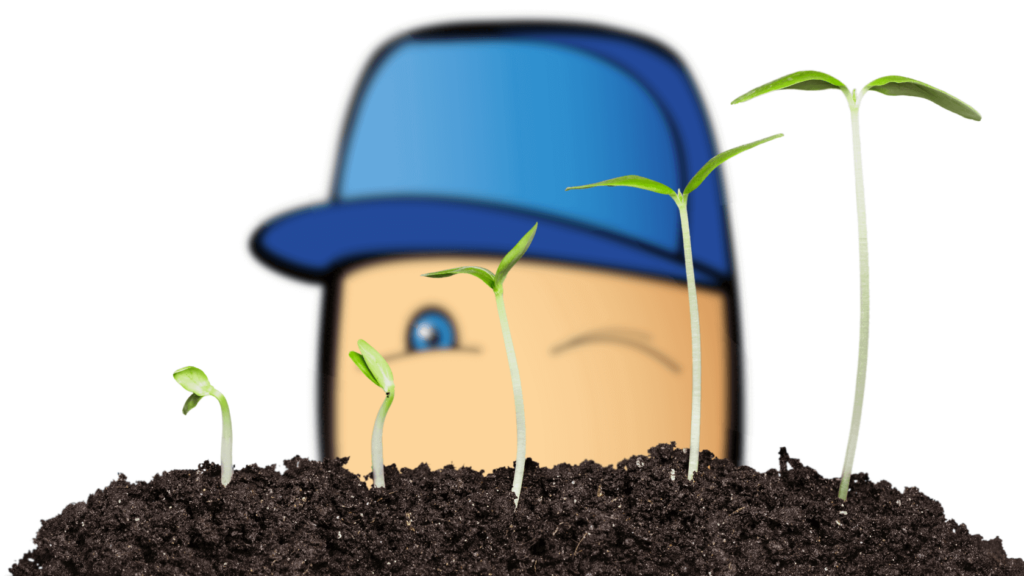
You can also listen to this article:
What is continuous improvement?
Continuous improvement (CI) is a strategic process of cyclically identifying, analyzing, and implementing enhancements to workflows and products. CI aims to keep manufacturing processes increasing in productivity and efficiency while minimizing waste and defects. These improvements can vary greatly in nature and scope. They can be incremental over time or achieved through significant breakthroughs. A key aspect of CI is its reliance on empirical data and key performance indicators to guide decision-making, ensuring that enhancements lead to real benefits.
The rapid pace of technological advancement and changing consumer expectations make CI crucial for modern manufacturing firms. Adopting CI in one form or another allows companies to increase adaptability and adjust their operations to meet the evolving demands of markets while maintaining high quality and efficiency.
CI carries heightened importance for small and medium-sized enterprises (SMEs) where resources are often more limited and the impact of inefficiencies can be more detrimental compared to larger organizations. Through it, SMEs can optimize their resource use, streamline operations, and enhance competitiveness, often without the need for extensive capital investments.
Incremental vs breakthrough CI
Incremental CI refers to making small improvements regularly over time. Incremental changes are often easier to implement and less risky than introducing new processes in scale. Incremental CI focuses on refining existing processes, reducing waste, and enhancing efficiency gradually.
Breakthrough CI, on the other hand, involves major changes that aim to achieve significant improvements quickly. This approach can include implementing new technologies, overhauling production processes, or rethinking entire business strategies. While potentially more impactful, breakthrough CI projects carry higher risks, requiring substantial investments and more comprehensive change management efforts.
Benefits of continuous improvement
Continuous Improvement initiatives bring a myriad of benefits to organizations, enhancing various aspects of operations and yielding substantial long-term gains. Here’s a detailed look at the core benefits of integrating CI practices within a company.
Operational efficiency
Continuous improvement strategically targets operational efficiency by streamlining processes, eliminating unnecessary steps, and optimizing resource use, while also fostering a proactive mindset among employees. This approach results in faster production cycles and more efficient manpower utilization. As a result, organizations can achieve higher productivity with fewer resources, ultimately leading to increased profitability and competitiveness.
Improved quality
Quality enhancement is another fundamental outcome of CI. By continuously assessing and improving processes, people, and products, organizations can significantly reduce the incidence of defects and errors. In this way, CI directly improves quality assurance practices and promotes crafting higher-quality products that satisfy customer needs while also enhancing the company’s reputation, aligning it for long-term success.
Cost control
More efficiency equals less cost. However, besides reducing expenditure, CI provides a deeper insight into where costs are incurred along with proactive ways to optimize cost of quality, highlighting opportunities for savings that do not compromise quality. By understanding the intricacies of cost factors within processes, organizations can make informed decisions that balance cost efficiency with quality output, leading to more sustainable business practices.
Employee engagement
Employee engagement is a crucial aspect of continuous improvement, significantly enhancing employees’ sense of ownership and responsibility towards their work. This heightened involvement leads to increased motivation and commitment as team members feel more connected to the outcomes of their efforts.
Many CI initiatives incorporate active participation, encouraging employees at all levels to contribute ideas and solutions. This active involvement fosters personal and professional development while directly contributing to a more dynamic and fulfilling work environment. By linking individual efforts to the larger goals of the organization, employees can see the tangible impacts of their contributions, enhancing engagement.
Reduced waste
CI methodologies, particularly those derived from Lean practices, focus heavily on waste reduction – not just physical waste but also wasted time, energy, cost, and labor. Identifying and eliminating wasteful practices across all operational areas helps conserve resources and adopt sustainable practices, essential for operational efficiency and the increasing global focus on environmental awareness.
Opportunity and innovation
Continuous improvement fosters an environment for innovation. By encouraging a mindset that always looks for better ways to do things, organizations naturally become more innovative. This continuous search for improvement can lead to breakthroughs in products and processes, opening up new opportunities for growth and competitiveness.
Enhanced customer satisfaction
Enhancing customer satisfaction is another significant benefit of CI. By continuously improving the quality of products and services, and responding proactively to customer feedback, companies can build stronger relationships with their clients. Satisfied customers are more likely to be loyal, provide repeat business, and offer referrals, all contributing to sustainable business growth.
Risk reduction
Implementing CI practices helps mitigate risks associated with business processes. By continually assessing and refining operations, companies can identify potential risks early and implement preventative measures. This proactive approach to risk management safeguards the company against operational failures while also enhancing its compliance with industry regulations and standards.
Central models of continuous improvement
Continuous improvement is not a one-size-fits-all methodology but rather a spectrum of strategies that can be tailored to an organization’s specific needs. These models provide frameworks through which companies can methodically approach continuous process improvement. Here we discuss four pivotal CI models, each with its unique principles and practices suited to different operational needs and objectives.
Kaizen
Kaizen, translating to “change for the better,” is a Japanese philosophy that emphasizes continuous, incremental improvement involving all employees from the top management to assembly line workers. It’s one of the essential methodologies that gave rise to continuous improvement as a systematic process for performance enhancement in manufacturing. It was a core part of The Toyota Way, a set of principles developed within the Toyota Motor Corporation to usher innovation in organizational culture.
Kaizen encourages suggestions and involvement from all employees to foster an environment where everyone feels empowered to contribute to improvement efforts. The model thrives on the notion that small, ongoing positive changes can reap significant benefits. Common practices under Kaizen include organizing brainstorming sessions, improving workspace functionality, and simplifying processes.
PDCA (Plan-Do-Check-Act)
The PDCA cycle, also known as the Shewhart cycle or Control cycle, is a four-step iterative methodology for achieving continuous improvement in business processes. It provides a simple but effective approach to solving problems and managing changes, ensuring that ideas are implemented efficiently, tested, and optimized. The cycle was popularized by Dr. W. Edwards Deming, a man considered by many as the father of modern quality control. However, PDCA was originally developed by Dr. Walter A. Shewhart of Bell Laboratories.
- Plan. The first step involves identifying a problem and formulating a hypothesis on how it can be solved. It includes analyzing the current situation, setting objectives, and planning the changes needed to achieve them. Detailed planning at this stage ensures that the process changes are well thought out and aligned with organizational goals.
- Do. This next phase involves implementing the planned change on a small scale. The purpose is to test the change and see if it brings about improvement. It acts as a trial period wherein disruptions are minimized and the real-world applicability of the proposed changes can be observed.
- Check. After implementing the change, the Check stage assesses the outcomes against expected objectives. Data and results are collected and analyzed to understand if the changes have led to an improvement. This is critical because it determines whether the hypothesis is supported or if further adjustments are required.
- Act. If the results from the Check phase are successful, the process changes are standardized and implemented on a wider scale across the organization. If the change did not lead to improvements, however, the insights gained are used to refine the hypothesis, and the cycle is repeated with a new plan.
The iterative nature of the PDCA cycle allows for continuous refinements and adjustments, making it an invaluable tool for achieving ongoing improvement within any organization. By repeatedly going through these stages, companies can foster a culture of sustained learning and improvement, progressively enhancing process efficiency and effectiveness.
Lean manufacturing and Just-in-Time
Lean Manufacturing and Just-in-Time (JIT) are two closely related philosophies that focus on maximizing production efficiency and reducing manufacturing waste. Both are integral to continuous improvement and share the ultimate goal of making operations more responsive and cost-effective.
Lean manufacturing focuses on eliminating waste – defined as any number of things that don’t add value to the customer and often referred to as the 8 wastes of Lean. Lean methodology achieves this by streamlining production processes, reducing cycle times, improving product quality, etc. It emphasizes understanding customer value, aligning processes to deliver that value, and continually improving these processes based on customer feedback and empirical data. Techniques such as value stream mapping, continuous flow, and employee empowerment are fundamental to Lean, each contributing to the reduction of waste arising from overproduction, defects, unnecessary transport, etc.
Just-in-Time (JIT), often implemented as a key element of Lean manufacturing, focuses specifically on inventory management and Pull type manufacturing workflows. The core idea of JIT is to minimize inventory and reduce the waste associated with storing unused materials. By producing and delivering components only as they are needed, JIT helps to reduce costs and increase the efficiency of production systems. This approach requires precise coordination and often relies heavily on supplier relationships and reliable demand forecasts to avoid delays and stockouts.
Lean and JIT’s synergy is evident as reducing inventory directly contributes to Lean objectives by lowering holding costs and reducing the risk of spoilage or obsolescence. Furthermore, JIT amplifies Lean’s focus on quality as defects and issues become more apparent and can be addressed more promptly, the fewer inventories and ongoing processes there are in the system.
Continue reading about Just-in-Time manufacturing.
Six Sigma
Six Sigma is a rigorous, data-driven methodology that aims to eliminate defects and inefficiencies in any process, enhancing quality and improving outcomes. Originating in the 1980s at Motorola, Six Sigma was developed as a way to improve manufacturing processes through statistical methods that reduce variability in process outputs. It focuses on identifying and removing the causes of defects and minimizing variability in manufacturing and business processes using a set of quality management methods.
The methodology is primarily structured around the DMAIC framework — Define, Measure, Analyze, Improve, and Control.
- Define the problems, the project goals, and customer (internal and external) demands.
- Measure key aspects of the current process and collect relevant data.
- Analyze the data to investigate and verify cause-and-effect relationships. Determine what the relationships are, and attempt to ensure that all factors have been considered.
- Improve or optimize the current process based upon data analysis using techniques like the design of experiments, poka-yoke (mistake proofing), and standard work to create new, future state processes.
- Control the future state process to ensure that any deviations from the target are corrected before they result in defects. This helps maintain the gains by institutionalizing the improved process by writing policies, procedures, and controls, and by applying them across the organization.
Six Sigma professionals often use the terms Black Belt, Green Belt, etc., to denote a level of competency and training in these methods. These certifications reflect the individual’s ability to lead project teams, define improvement projects that align with strategic objectives, and apply the rigorous methodology to achieve measurable improvements. Six Sigma is not just about techniques but is also a philosophy driving a culture of improvement through disciplined data analysis and decision-making.
Other methodologies associated with continuous improvement
In addition to the above models that many companies base their CI efforts around, let’s also look at four systematic strategies for adopting and fostering various tenets of continuous improvement in manufacturing.
Root cause analysis
Root cause analysis (RCA) is a methodical approach to identifying the underlying causes of problems or incidents to solve them effectively. RCA is based on the principle that effective problem solving requires more than merely treating the symptoms of a problem, but rather identifying and addressing its root causes. In manufacturing, this can lead to significant improvements in product quality, efficiency, and employee safety.
A popular RCA tool is The 5 Whys method, which involves asking the question “Why?” multiple times until the fundamental cause of a problem is uncovered. For instance, if a machine stops working, the first “why” may reveal that a part failed. Asking “why” again might show that the part was improperly maintained. Continual questioning would then lead to deeper insights, perhaps revealing a lack of scheduled maintenance as the root cause. By addressing this, the solution becomes evident: improve the maintenance schedule.
Theory of constraints
The theory of constraints (TOC) is a methodology that focuses on identifying the most significant limiting factor (i.e., constraint) that stands in the way of achieving a goal, and then systematically improving that constraint until it no longer limits performance. Developed by Dr. Eliyahu M. Goldratt in his 1984 book The Goal, TOC proposes that nearly every complex system, including manufacturing processes, can be substantially improved through a focus on its constraints.
TOC uses a set methodology known as The Five Focusing Steps to address and optimize identified constraints. These steps provide a systematic approach for managing improvements and are designed to ensure continuous advancement towards the organization’s goals. The steps are:
- Identify the constraint. The first step involves determining the specific part of the process that limits the entire system’s ability to achieve higher performance. This could be a machine, a policy, a procedure, or even a market demand.
- Exploit the constraint. Once the constraint is identified, find ways to maximize its throughput without major investments. This means making the most of what you have. For example, ensuring the constraint is never idle, reducing inefficiencies immediately before or at the constraint point, or preparing materials in advance.
- Subordinate everything else. The third step is to align the entire system or processes to support the needs of the constrained process. This means making other elements of the process work in a manner that enables the constraint to operate at maximum effectiveness.
- Elevate the constraint. If the constraint still exists after exploitation and subordination, the next step is to make permanent changes to overcome it. This could involve increasing capacity at the bottleneck, adding resources, or outsourcing parts of the process.
- Repeat the process. This last step emphasizes TOC’s focus on continuous improvement. Once the current constraint is overcome, go back to the first step and identify the next constraint. The goal is to achieve a continuous cycle of improvement.
By focusing on the most restrictive element in the manufacturing or business process, TOC helps organizations make significant and sustainable improvements in performance. TOC encourages businesses to view constraints positively as opportunities and catalysts for innovation and growth.
The 5S
Much like Lean and Kaizen, The 5S system is another Japanese methodology often associated with continuous improvement. 5S is a systematic approach to workplace organization and standardization that helps improve efficiency and foster a sense of ownership among employees. The 5S principles include:
- Seiri (Sort): Remove unnecessary tools, parts, and instructions. Keep only essential items and eliminate what is not required, thereby potentially eliminating obstacles to work.
- Seiton (Set in order): Arrange and identify the necessary items so they can be easily accessed and used. Place components according to their uses with frequently used items being closer to workplace areas.
- Seiso (Shine): Clean the workspace and equipment regularly to maintain standards and ensure defects become apparent faster.
- Seiketsu (Standardize): Work practices should be consistent and standardized. All workstations for a particular job should be identical.
- Shitsuke (Sustain): Maintain and review standards. Once the previous 4 S’s have been established, they become the new way to operate. Maintain focus on this new way and do not allow a gradual decline back to the old ways.
Kanban
Kanban is a visual management system that supports JIT and Lean manufacturing by controlling the logistical chain from a production point of view and thus harmonizing production with demand. In Kanban, work items are visualized to give participants a clear understanding of progress and process flows, and to limit work in process based on the system capacity.
This system is designed to promote efficiency by limiting ongoing projects to a manageable level. This can prevent overproduction—one of the major wastes in Lean manufacturing. Kanban encourages a smooth flow of work and allows for quick identification and resolution of bottlenecks.
The continuous improvement process
Implementing continuous improvement is a dynamic and iterative process. The specific applications and steps of CI can vary significantly across different companies, industries, and end goals. However, regardless of the methodology being adopted, continuous improvement tools mostly focus on streamlining processes, eliminating waste, and enhancing overall productivity.
The variability lies in how these goals are prioritized and achieved, and how unique organizational needs, market conditions, and available resources influence them. This makes CI adaptable, allowing each organization to tailor it to their specific context.
The CI process does have some common tenets, however, regardless of the where, who, and how. It often involves a cyclical series of steps: planning, executing, evaluating, and refining. This helps ensure that improvements are based on precise data and real feedback, that positive changes are sustained and built on over time, etc.
CI implementation example
To effectively implement a CI process, organizations typically follow a route similar to the following steps:
- Identify objectives. The first step in a successful CI initiative is to clearly define what you hope to achieve. One good way to map out objectives is by following the SMART method, i.e. figuring out whether your goals are Specific, Measurable, Achievable, Relevant, and Time-bound. Setting clear goals at the outset provides direction and a benchmark against which progress can be measured.
- Establish and define the process. Once objectives are set, the next step is to map out the existing processes to pinpoint inefficiencies and areas for improvement. Detailed mapping helps in understanding the workflow and identifying bottlenecks or where wastes lie in the system.
- Communicate and deploy the process. After identifying how processes can be improved, the next step is to implement the changes. This involves not only the physical deployment of new methods or tools but also effective communication across the organization. Ensuring that all stakeholders understand the changes and the reasons behind them is crucial for buy-in and compliance.
- Track and measure. With the new processes in place, it’s important to track outcomes and measure the effects of the improvements against the set objectives. This monitoring should utilize relevant key performance indicators (KPIs) to provide data-driven insights into how well the improvements are performing.
- Review and Re-Do. The final step is to review the results and the overall process. This involves analyzing what worked and what didn’t, making necessary adjustments, and preparing to cycle through the process again. Continuous improvement is about learning from each cycle and being prepared to make ongoing changes to enhance the system further.
CI best practices for small manufacturers
For small manufacturers, implementing continuous improvement practices can be both a strategic advantage and a necessity to stay competitive in a fast-evolving market. Here are five best practices that can help small manufacturers effectively incorporate CI into their operations:
- Establish regular training and development. Continuous improvement is as much about upskilling the workforce as upgrading processes. Implementing regular training programs can help employees master new technologies, grasp CI methodologies like Lean or Six Sigma, and apply these skills effectively in their work. Moreover, a commitment to ongoing education helps boost employee satisfaction and retention.
- Increase employee involvement. Gather insights from those who know the work best – the employees. Engaging hands-on workers provides valuable perspectives that can lead to significant process enhancements. Encourage ideation through surveys or think tanks and implement ways for employees to give regular feedback around processes. This inclusive approach can both help improve processes but also empowers employees, leading to a more committed workforce.
- Improve the workplace. Enhancing the physical and organizational environment of the workplace can lead to more efficient operations and a happier workforce. This includes organizing the workspace for efficiency (using concepts like 5S), ensuring safety standards are exceeded, and creating a more engaging and comfortable work environment. Improvements in the workplace can lead to enhanced productivity and motivate employees to contribute their best.
- Implement digital technology and automation. Investing in technology that automates repetitive tasks and streamlines processes is crucial for small manufacturers. Tools like Enterprise Resource Planning (ERP) systems, inventory management, and tracking and analysis software can substantially increase efficiency.
- Leverage IoT and machine learning. Integrating Internet of Things (IoT) and machine learning technologies can dramatically transform manufacturing processes. IoT devices can monitor and collect data from across the manufacturing floor in real time, while machine learning algorithms analyze this data to predict failures, optimize operations, and enhance decision-making. This can lead to deeper insights, predictive maintenance, and smarter manufacturing processes.
How can manufacturing software help with CI?
Manufacturing software, particularly Manufacturing Resource Planning or MRP systems, play a pivotal role in driving continuous improvement. These systems integrate various aspects of manufacturing management from inventory control and production planning to quality assurance and traceability. Manufacturing software provides a robust foundation for CI by enhancing visibility, improving communication, and equipping managers with analytics tools based on real manufacturing data.
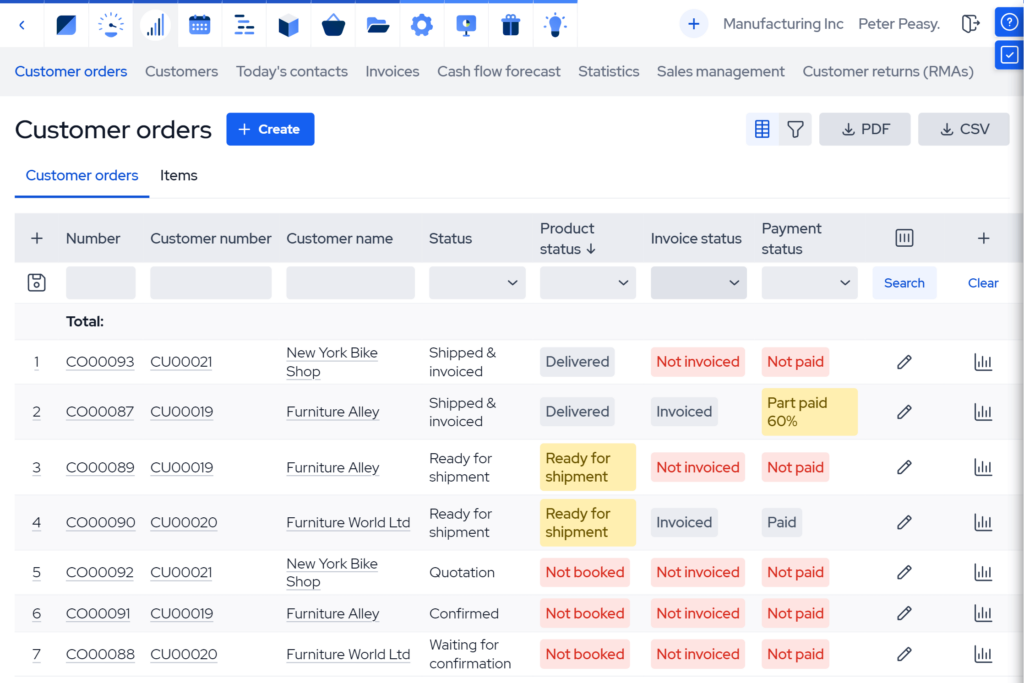
For example, MRPeasy offers small to medium-sized manufacturers an intuitive and comprehensive solution that supports the execution and monitoring of CI strategies. It enables businesses to manage production schedules, inventory, customer relationships, and procurement all in a unified system, reducing the likelihood of errors and inefficiencies.
MRPeasy further facilitates real-time data analysis, KPI tracking, and comprehensive reports, crucial for identifying bottlenecks, forecasting demand, and optimizing resource allocation, enabling you to make decisions based on real insights and implement changes swiftly and reliably.
Key takeaways
- Continuous improvement is a strategic process of recurring identification, analysis, and implementation of enhancements to workflows and products to keep manufacturing processes continually increasing in productivity and efficiency.
- Many different types of continuous improvement models, methods, and initiatives exist like Kaizen, Lean, Six Sigma, Plan-Do-Check-Act, or Just-in-Time manufacturing.
- Continuous improvement brings a wealth of benefits to manufacturers from reducing waste and enhancing teamwork to simplifying process management, cutting costs, and fostering workplace innovation.
- An example CI cycle includes steps to identify objectives, establish and define the process, deploy and communicate the process, track and measure the results, and implement the change at scale.
- Continuous improvement best practices include finding innovative ways to increase employee engagement, improving the workplace environment, leveraging digital technology like IoT and machine learning devices, etc.
Frequently asked questions
Measuring the ROI of continuous improvement initiatives involves quantifying both direct and indirect benefits, including reduced costs, increased productivity, and improved product quality. KPIs such as cycle time, defect rate, or throughput can be directly correlated with financial metrics to evaluate ROI. Additionally, softer metrics like employee engagement and customer satisfaction can provide insights into the broader impact of CI investments.
Integrating advanced technologies like IoT and machine learning into existing CI frameworks often presents challenges such as high initial costs, complexity of implementation, and the need for specialized skills. Additionally, there can be resistance to change from employees who are accustomed to traditional methods. Overcoming these barriers typically requires thorough planning, ongoing training, and clear communication about the benefits these technologies bring.
Continuous improvement can significantly enhance supplier and customer relationships. On the supplier side, closer collaboration and shared CI goals can lead to improved material quality and delivery reliability. For customers, consistent improvements in product quality and customer service can increase satisfaction and loyalty.
You might also like: Statistical Process Control – A Manufacturer’s Guide