Kontinuierliche Verbesserung – Implementierung von CI in der Fertigung
In der heutigen wettbewerbsorientierten Fertigungslandschaft ist die kontinuierliche Verbesserung (Continuous Improvement, CI) eine entscheidende Strategie zur Steigerung von Effizienz, Qualität und allgemeiner Unternehmensleistung. In diesem Artikel stellen wir Ihnen verschiedene Modelle der kontinuierlichen Verbesserung vor und geben Ihnen praktische Hinweise, wie Hersteller CI-Initiativen umsetzen und von ihnen profitieren können.
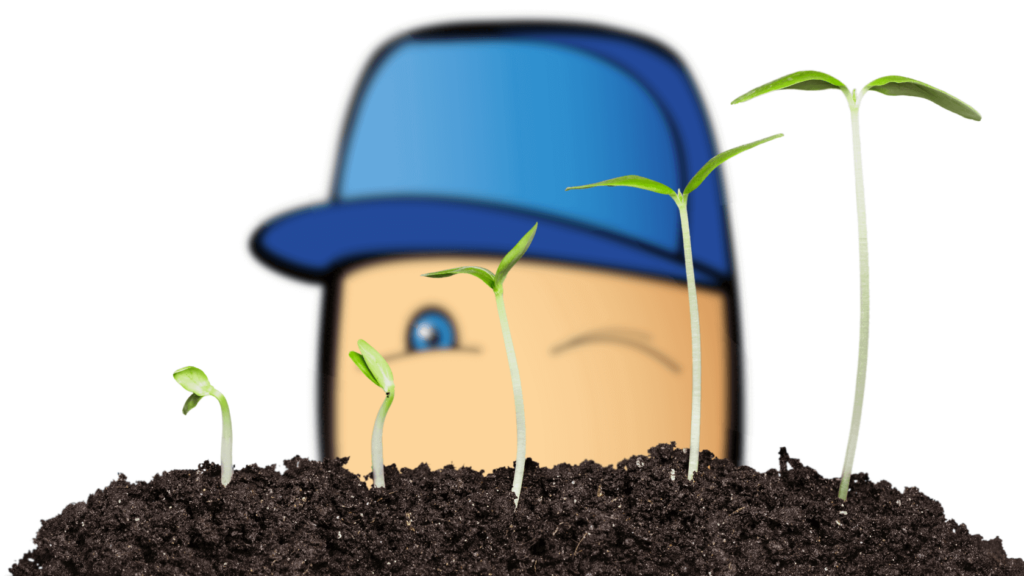
Was ist kontinuierliche Verbesserung?
Kontinuierliche Verbesserung (Continuous Improvement, CI) ist ein strategischer Prozess, bei dem zyklisch Verbesserungen von Arbeitsabläufen und Produkten identifiziert, analysiert und umgesetzt werden. Das Ziel von CI lautet, die Produktivität und Effizienz von Fertigungsprozessen zu steigern und gleichzeitig Verschwendung und Fehler zu minimieren. Diese Verbesserungen können in Art und Umfang sehr unterschiedlich sein. Sie können im Laufe der Zeit schrittweise erfolgen oder durch bedeutende Durchbrüche oder „Breakthroughs“ erreicht werden. Ein wichtiger Aspekt von CI ist, dass sie sich bei der Entscheidungsfindung auf empirische Daten und Leistungsindikatoren stützt, damit die Verbesserungen zu echten Vorteilen führen.
Fortschritts und die sich ändernden Erwartungen der Verbraucher machen CI für moderne Produktionsunternehmen unverzichtbar. Die Einführung von kontinuierlicher Verbesserung in der einen oder anderen Form ermöglicht es Unternehmen, ihre Anpassungsfähigkeit zu erhöhen und ihre Arbeitsabläufe an die sich verändernden Anforderungen der Märkte anzupassen und gleichzeitig eine hohe Qualität und Effizienz zu gewährleisten.
Für kleine und mittlere Unternehmen (KMU) ist CI von besonderer Bedeutung, da ihre Ressourcen oft begrenzter sind und sich Ineffizienzen im Vergleich zu größeren Unternehmen nachteilig auswirken können. Mit Hilfe von kontinuierlicher Verbesserung können KMUs ihre Ressourcennutzung optimieren, ihre Abläufe rationalisieren und ihre Wettbewerbsfähigkeit verbessern, oft ohne umfangreiche Investitionen tätigen zu müssen.
Inkrementelle CI und Breakthrough CI
Inkrementelle CI bedeutet, dass im Laufe der Zeit regelmäßig kleine Verbesserungen vorgenommen werden. Inkrementelle Änderungen sind oft einfacher zu implementieren und weniger riskant als die Einführung neuer Prozesse im großen Stil. Inkrementelle CI konzentriert sich darauf, bestehende Prozesse zu verfeinern, Verschwendung zu reduzieren und die Effizienz schrittweise zu steigern.
Bei der Breakthrough CI geht es dagegen um größere Veränderungen, die schnell zu erheblichen Verbesserungen führen sollen. Dieser Ansatz kann die Implementierung neuer Technologien, die Überarbeitung von Produktionsprozessen oder das Überdenken ganzer Geschäftsstrategien umfassen. Obwohl sie potenziell wirkungsvoller sind, bergen Breakthrough-CI-Projekte höhere Risiken und erfordern erhebliche Investitionen und umfassendere Bemühungen im Bereich des Änderungsmanagements.
Vorteile der kontinuierlichen Verbesserung
Initiativen zur kontinuierlichen Verbesserung bringen Unternehmen eine Vielzahl von Vorteilen, indem sie verschiedene Aspekte der Betriebsabläufe verbessern und langfristig erhebliche Gewinne erzielen. Im Folgenden finden Sie einen detaillierten Überblick über die wichtigsten Vorteile der Integration von CI-Verfahren in einem Unternehmen.
Operative Effizienz
Kontinuierliche Verbesserung zielt strategisch auf die betriebliche Effizienz ab, indem Prozesse gestrafft, unnötige Schritte eliminiert und die Ressourcennutzung optimiert werden, während gleichzeitig eine proaktive Einstellung der Mitarbeiter gefördert wird. Dieser Ansatz führt zu schnelleren Produktionszyklen und einer effizienteren Nutzung der Arbeitskräfte. Infolgedessen können Unternehmen mit weniger Ressourcen eine höhere Produktivität erzielen, was letztlich zu einer höheren Rentabilität und Wettbewerbsfähigkeit führt.
Verbesserte Qualität
Die Verbesserung der Qualität ist ein weiteres grundlegendes Ergebnis von CI. Durch die kontinuierliche Bewertung und Verbesserung von Prozessen, Menschen und Produkten können Unternehmen die Häufigkeit von Mängeln und Fehlern erheblich reduzieren. Auf diese Weise verbessert CI direkt die Praktiken zur Qualitätssicherung und fördert die Herstellung hochwertigerer Produkte, die die Bedürfnisse der Kunden befriedigen und gleichzeitig den Ruf des Unternehmens verbessern und es auf langfristigen Erfolg ausrichten.
Kostenkontrolle
Mehr Effizienz ist gleichbedeutend mit weniger Kosten. Neben der Senkung der Ausgaben bietet CI jedoch auch einen tieferen Einblick in die Bereiche, in denen Kosten anfallen, sowie proaktive Möglichkeiten zur Optimierung der Qualitätskosten und zeigt Einsparmöglichkeiten auf, ohne dass die Qualität darunter leidet. Indem sie die Feinheiten der Kostenfaktoren in den Prozessen verstehen, können Unternehmen fundierte Entscheidungen treffen, die ein Gleichgewicht zwischen Kosteneffizienz und Qualitätsleistung herstellen und so zu nachhaltigeren Geschäftspraktiken führen.
Einbindung der Mitarbeiter
Die Einbindung der Mitarbeiter ist ein entscheidender Aspekt der kontinuierlichen Verbesserung, da sie das Gefühl der Eigenverantwortung und des Verantwortungsbewusstseins der Mitarbeiter für ihre Arbeit erheblich stärkt. Diese stärkere Einbindung führt zu mehr Motivation und Engagement, da sich die Teammitglieder stärker mit den Ergebnissen ihrer Bemühungen verbunden fühlen.
Viele CI-Initiativen sehen eine aktive Beteiligung vor und ermutigen Mitarbeiter auf allen Ebenen, Ideen und Lösungen beizusteuern. Diese aktive Beteiligung fördert die persönliche und berufliche Entwicklung und trägt direkt zu einem dynamischeren und erfüllteren Arbeitsumfeld bei. Durch die Verknüpfung der individuellen Bemühungen mit den größeren Zielen des Unternehmens können die Mitarbeiter die greifbaren Auswirkungen ihrer Beiträge sehen, was das Engagement steigert.
Geringere Verschwendung
CI-Methoden, insbesondere solche, die von Lean-Praktiken abgeleitet sind, konzentrieren sich stark auf die Reduzierung von Verschwendung – nicht nur physische Verschwendung, sondern auch verschwendete Zeit, Energie, Kosten und Arbeit. Die Identifizierung und Beseitigung von Verschwendung in allen betrieblichen Bereichen trägt dazu bei, Ressourcen zu sparen und nachhaltige Praktiken einzuführen, die für die betriebliche Effizienz und das zunehmende globale Umweltbewusstsein von entscheidender Bedeutung sind.
Chancen und Innovation
Kontinuierliche Verbesserung fördert ein Umfeld, das Innovationen begünstigt. Durch die Förderung einer Mentalität, die stets nach besseren Wegen sucht, werden Unternehmen auf natürliche Weise innovativer. Dieses ständige Streben nach Verbesserung kann zu Durchbrüchen bei Produkten und Prozessen führen, die neue Möglichkeiten für Wachstum und Wettbewerbsfähigkeit eröffnen.
Erhöhte Kundenzufriedenheit
Die Steigerung der Kundenzufriedenheit ist ein weiterer wichtiger Vorteil von CI. Indem sie die Qualität ihrer Produkte und Dienstleistungen kontinuierlich verbessern und proaktiv auf das Feedback ihrer Kunden reagieren, können Unternehmen engere Beziehungen zu ihren Kunden aufbauen. Zufriedene Kunden sind mit größerer Wahrscheinlichkeit loyal, wiederholen das Geschäft und empfehlen es weiter, was wiederum zu einem nachhaltigen Geschäftswachstum beiträgt.
Reduzierung von Risiken
Die Einführung von CI-Praktiken hilft, die mit den Geschäftsprozessen verbundenen Risiken zu verringern. Durch die kontinuierliche Bewertung und Verfeinerung von Abläufen können Unternehmen potenzielle Risiken frühzeitig erkennen und Präventivmaßnahmen ergreifen. Dieser proaktive Ansatz des Risikomanagements schützt das Unternehmen vor operativen Fehlern und verbessert gleichzeitig die Einhaltung von Branchenvorschriften und -standards.
Zentrale Modelle der kontinuierlichen Verbesserung
Kontinuierliche Verbesserung ist keine Einheitsmethode, sondern ein Spektrum von Strategien, die auf die spezifischen Bedürfnisse eines Unternehmens zugeschnitten werden können. Diese Modelle bieten einen Rahmen, durch den Unternehmen methodisch an die kontinuierliche Prozessverbesserung herangehen können. Im Folgenden stellen wir vier zentrale CI-Modelle vor, von denen jedes seine eigenen Prinzipien und Praktiken hat, die für unterschiedliche betriebliche Anforderungen und Ziele geeignet sind.
Kaizen
Kaizen bedeutet übersetzt „Veränderung zum Besseren“ und ist eine japanische Philosophie, die eine kontinuierliche, schrittweise Verbesserung unter Einbeziehung aller Mitarbeiter – vom Topmanagement bis zum Fließbandarbeiter – in den Vordergrund stellt. Es ist eine der wesentlichen Methoden, die die kontinuierliche Verbesserung als systematischen Prozess zur Leistungssteigerung in der Produktion hervorgebracht hat. Es war ein zentraler Bestandteil des Toyota-Wegs, einer Reihe von Prinzipien, die innerhalb der Toyota Motor Corporation entwickelt wurden, um Innovationen in die Unternehmenskultur einzubringen.
Kaizen ermutigt alle Mitarbeiter, Vorschläge zu machen und sich einzubringen, um ein Umfeld zu schaffen, in dem sich jeder befähigt fühlt, zu den Verbesserungsbemühungen beizutragen. Das Modell basiert auf dem Gedanken, dass kleine, fortlaufende positive Veränderungen erhebliche Vorteile bringen können. Zu den gängigen Praktiken im Rahmen von Kaizen gehören die Organisation von Brainstorming-Sitzungen, die Verbesserung der Funktionalität des Arbeitsplatzes und die Vereinfachung von Prozessen.
PDCA (Plan-Do-Check-Act)
Der PDCA-Zyklus, auch bekannt als Shewhart-Zyklus oder Kontrollzyklus, ist eine vierstufige, iterative Methodik zur kontinuierlichen Verbesserung von Geschäftsprozessen. Er bietet einen einfachen, aber effektiven Ansatz für die Lösung von Problemen und das Management von Veränderungen und gewährleistet, dass Ideen effizient umgesetzt, getestet und optimiert werden. Der Zyklus wurde von Dr. W. Edwards Deming populär gemacht, einem Mann, der von vielen als der Vater der modernen Qualitätskontrolle angesehen wird. Ursprünglich wurde die PDCA jedoch von Dr. Walter A. Shewhart von Bell Laboratories entwickelt.
- Planen (Plan). Der erste Schritt besteht darin, ein Problem zu identifizieren und eine Hypothese zu formulieren, wie es gelöst werden kann. Er umfasst die Analyse der aktuellen Situation, die Festlegung von Zielen und die Planung der zur Erreichung dieser Ziele erforderlichen Änderungen. Eine detaillierte Planung in dieser Phase stellt sicher, dass die Prozessänderungen gut durchdacht und auf die Unternehmensziele abgestimmt sind.
- Durchführen (Do). In dieser nächsten Phase wird die geplante Änderung in kleinem Maßstab umgesetzt. Der Zweck besteht darin, die Änderung zu testen und zu sehen, ob sie zu einer Verbesserung führt. Es handelt sich um eine Testphase, in der Störungen minimiert werden und die Anwendbarkeit der vorgeschlagenen Änderungen in der Praxis beobachtet werden kann.
- Überprüfen (Check). Nach der Implementierung der Änderung werden in der Überprüfungsphase die Ergebnisse anhand der erwarteten Ziele bewertet. Daten und Ergebnisse werden gesammelt und analysiert, um festzustellen, ob die Änderungen zu einer Verbesserung geführt haben. Dies ist von entscheidender Bedeutung, da auf diese Weise festgestellt wird, ob die Hypothese unterstützt wird oder ob weitere Anpassungen erforderlich sind.
- Handeln (Act). Wenn die Ergebnisse aus der Überprüfungsphase erfolgreich sind, werden die Prozessänderungen standardisiert und in größerem Umfang im gesamten Unternehmen umgesetzt. Hat die Änderung jedoch nicht zu Verbesserungen geführt, werden die gewonnenen Erkenntnisse genutzt, um die Hypothese zu verfeinern, und der Zyklus wird mit einem neuen Plan wiederholt.
Der iterative Charakter des PDCA-Zyklus ermöglicht kontinuierliche Verfeinerungen und Anpassungen, was ihn zu einem unschätzbaren Werkzeug für die kontinuierliche Verbesserung in jeder Organisation macht. Durch das wiederholte Durchlaufen dieser Phasen können Unternehmen eine Kultur des kontinuierlichen Lernens und der Verbesserung fördern und so die Effizienz und Effektivität ihrer Prozesse schrittweise verbessern.
Lean Manufacturing und Just-in-Time-Produktion
Lean Manufacturing und Just-in-Time (JIT) sind zwei eng miteinander verbundene Philosophien, die sich auf die Maximierung der Effizienz und die Reduzierung von Verschwendung im Fertigungsprozess konzentrieren. Beide sind integraler Bestandteil der kontinuierlichen Verbesserung und verfolgen das Ziel, die Abläufe reaktionsschneller und kostengünstiger zu gestalten.
Lean Manufacturing oder schlanke Produktion konzentriert sich auf die Beseitigung von Verschwendung – definiert als eine Vielzahl von Dingen, die dem Kunden keinen Mehrwert bringen und oft als die 8 Verschwendungen von Lean bezeichnet werden. Die Lean-Methode erreicht dies durch die Optimierung von Produktionsprozessen, die Verkürzung von Zykluszeiten, die Verbesserung der Produktqualität usw. Der Schwerpunkt liegt auf dem Verständnis des Kundenwerts, der Ausrichtung der Prozesse auf die Bereitstellung dieses Werts und der kontinuierlichen Verbesserung dieser Prozesse auf der Grundlage von Kundenfeedback und empirischen Daten. Techniken wie die Wertstromanalyse, der kontinuierliche Fluss und die Befähigung der Mitarbeiter sind für Lean von grundlegender Bedeutung. Sie alle tragen dazu bei, die Verschwendung durch Überproduktion, Defekte, unnötige Transporte usw. zu reduzieren.
Just-in-Time (JIT), das häufig als Schlüsselelement der Lean-Produktion eingesetzt wird, konzentriert sich speziell auf die Bestandsverwaltung und die Arbeitsabläufe in der Pull-Produktion. Der Kerngedanke von JIT ist die Minimierung des Lagerbestands und die Reduzierung der Verschwendung, die mit der Lagerung ungenutzter Materialien verbunden ist. Indem Komponenten nur dann produziert und geliefert werden, wenn sie benötigt werden, trägt JIT dazu bei, Kosten zu senken und die Effizienz der Produktionssysteme zu steigern. Dieser Ansatz erfordert eine präzise Koordination und stützt sich häufig auf Lieferantenbeziehungen und zuverlässige Bedarfsprognosen, um Verzögerungen und Fehlbestände zu vermeiden.
Die Synergie von Lean und JIT ist offensichtlich, denn die Reduzierung der Bestände trägt direkt zu den Lean-Zielen bei, indem sie die Lagerkosten senkt und das Risiko von Verderb oder Veralterung verringert. Darüber hinaus verstärkt JIT den Fokus von Lean auf Qualität, da Fehler und Probleme umso schneller erkannt und behoben werden können, je weniger Bestände und laufende Prozesse es im System gibt.
Lesen Sie mehr über Just-in-Time-Produktion.
Six Sigma
Six Sigma ist eine strenge, datengestützte Methode, die darauf abzielt, Fehler und Ineffizienzen in jedem Prozess zu beseitigen, die Qualität zu erhöhen und die Ergebnisse zu verbessern. Six Sigma wurde in den 1980er Jahren bei Motorola entwickelt, um Fertigungsprozesse durch statistische Methoden zu verbessern, die die Variabilität des Prozessoutputs verringern. Der Schwerpunkt liegt auf der Identifizierung und Beseitigung von Fehlerursachen und der Minimierung von Schwankungen in Fertigungs- und Geschäftsprozessen mithilfe einer Reihe von Qualitätsmanagementmethoden.
Die Methodik ist in erster Linie um das DMAIC-Rahmenwerk herum aufgebaut – Definieren (Define), Messen (Measure), Analysieren (Analyze), Verbessern (Improve) und Kontrollieren (Control).
- Definieren Sie die Probleme, die Projektziele und die (internen und externen) Kundenanforderungen.
- Messen Sie die wichtigsten Aspekte des aktuellen Prozesses und sammeln Sie die relevanten Daten.
- Analysieren Sie die Daten, um Ursache-Wirkungs-Beziehungen zu untersuchen und zu verifizieren. Ermitteln Sie die Zusammenhänge und versuchen Sie sicherzustellen, dass alle Faktoren berücksichtigt wurden.
- Verbessern oder optimieren Sie den aktuellen Prozess auf der Grundlage der Datenanalyse mit Hilfe von Techniken wie der Versuchsplanung, Poka Yoke (Fehlersicherung) und Standardarbeit, um neue, zukünftige Prozesse zu schaffen.
- Kontrollieren Sie den zukünftigen Prozess, um sicherzustellen, dass alle Abweichungen vom Ziel korrigiert werden, bevor sie zu Fehlern führen. Dies trägt dazu bei, die Gewinne zu erhalten, indem der verbesserte Prozess durch die Erstellung von Richtlinien, Verfahren und Kontrollen institutionalisiert und im gesamten Unternehmen angewendet wird.
Six Sigma-Experten verwenden häufig die Begriffe Black Belt, Green Belt usw., um den Grad der Kompetenz und Ausbildung in diesen Methoden zu bezeichnen. Diese Zertifizierungen spiegeln die Fähigkeit des Einzelnen wider, Projektteams zu leiten, Verbesserungsprojekte zu definieren, die sich an strategischen Zielen orientieren, und die strenge Methodik anzuwenden, um messbare Verbesserungen zu erzielen. Bei Six Sigma geht es nicht nur um Techniken, sondern auch um eine Philosophie, die eine Kultur der Verbesserung durch disziplinierte Datenanalyse und Entscheidungsfindung fördert.
Andere Methoden im Zusammenhang mit der kontinuierlichen Verbesserung
Zusätzlich zu den oben genannten Modellen, auf die sich viele Unternehmen bei ihren CI-Bemühungen stützen, sollten wir uns vier systematische Strategien zur Übernahme und Förderung verschiedener Grundsätze der kontinuierlichen Verbesserung in der Fertigung ansehen.
Ursachenanalyse
Die Ursachenanalyse (Root Cause Analysis, RCA) ist ein methodischer Ansatz, um die zugrunde liegenden Ursachen von Problemen oder Vorfällen zu ermitteln und sie effektiv zu lösen. RCA basiert auf dem Grundsatz, dass eine wirksame Problemlösung mehr erfordert als die bloße Behandlung der Symptome eines Problems, sondern vielmehr die Identifizierung und Behebung seiner Ursachen. In der Fertigung kann dies zu erheblichen Verbesserungen bei der Produktqualität, der Effizienz und der Sicherheit der Mitarbeiter führen.
Ein beliebtes RCA-Tool ist die 5-Whys-Methode, bei der die Frage „Warum?“ mehrfach gestellt wird, bis die grundlegende Ursache eines Problems aufgedeckt ist. Wenn zum Beispiel eine Maschine nicht mehr funktioniert, kann das erste „Warum“ ergeben, dass ein Teil ausgefallen ist. Ein erneutes Nachfragen nach dem „Warum“ könnte ergeben, dass das Teil unsachgemäß gewartet wurde. Fortwährendes Hinterfragen würde dann zu tieferen Einsichten führen und vielleicht einen Mangel an planmäßiger Wartung als Grundursache aufdecken. Wenn Sie sich damit befassen, liegt die Lösung auf der Hand: Verbessern Sie den Wartungsplan.
Theorie der Beschränkungen
Die Theorie der Beschränkungen (Theory of Constraints, TOC) ist eine Methode, die sich darauf konzentriert, den wichtigsten einschränkenden Faktor (sprich die Beschränkung) zu identifizieren, der dem Erreichen eines Ziels im Wege steht, und dann diese Beschränkung systematisch zu verbessern, bis sie die Leistung nicht mehr einschränkt. TOC wurde von Dr. Eliyahu M. Goldratt in seinem 1984 erschienenen Buch The Goal entwickelt und geht davon aus, dass nahezu jedes komplexe System, einschließlich der Fertigungsprozesse, durch die Konzentration auf seine Beschränkungen erheblich verbessert werden kann.
TOC verwendet eine Methodik, die unter dem Namen The Five Focusing Steps bekannt ist, um identifizierte Beschränkungen anzugehen und zu optimieren. Diese Schritte bieten einen systematischen Ansatz für das Management von Verbesserungen und sind so konzipiert, dass sie einen kontinuierlichen Fortschritt in Richtung der Ziele des Unternehmens gewährleisten. Die Schritte sind:
- Identifizieren Sie die Einschränkung. Der erste Schritt besteht darin, den spezifischen Teil des Prozesses zu bestimmen, der die Fähigkeit des gesamten Systems einschränkt, eine höhere Leistung zu erzielen. Dabei kann es sich um eine Maschine, eine Richtlinie, ein Verfahren oder sogar eine Marktnachfrage handeln.
- Nutzen Sie die Einschränkung aus. Sobald die Einschränkung identifiziert ist, suchen Sie nach Möglichkeiten, den Durchsatz ohne größere Investitionen zu maximieren. Das bedeutet, dass Sie das Beste aus dem machen, was Sie haben. Stellen Sie zum Beispiel sicher, dass der Engpass nie untätig ist, reduzieren Sie Ineffizienzen unmittelbar vor oder am Engpasspunkt oder bereiten Sie Materialien im Voraus vor.
- Ordnen Sie alles andere unter. Der dritte Schritt besteht darin, das gesamte System oder die Prozesse so auszurichten, dass sie die Anforderungen des eingeschränkten Prozesses unterstützen. Das bedeutet, dass andere Elemente des Prozesses so gestaltet werden müssen, dass die Einschränkung mit maximaler Effektivität durchgeführt werden kann.
- Heben Sie die Einschränkung auf. Wenn die Einschränkung nach der Ausnutzung und Unterordnung immer noch besteht, besteht der nächste Schritt darin, dauerhafte Änderungen vorzunehmen, um sie zu überwinden. Dies könnte bedeuten, dass Sie die Kapazität am Engpass erhöhen, zusätzliche Ressourcen einsetzen oder Teile des Prozesses auslagern.
- Wiederholen Sie den Prozess. Dieser letzte Schritt unterstreicht den Fokus von TOC auf kontinuierliche Verbesserung. Sobald der aktuelle Engpass überwunden ist, kehren Sie zum ersten Schritt zurück und identifizieren den nächsten Engpass. Das Ziel ist es, einen kontinuierlichen Verbesserungszyklus zu erreichen.
Durch die Konzentration auf das restriktivste Element im Herstellungs- oder Geschäftsprozess hilft TOC Unternehmen, ihre Leistung signifikant und nachhaltig zu verbessern. TOC ermutigt Unternehmen dazu, Einschränkungen positiv zu sehen und sie als Chance und Katalysator für Innovation und Wachstum zu nutzen.
Die 5S
Ähnlich wie Lean und Kaizen ist das 5S-System eine weitere japanische Methode, die oft mit kontinuierlicher Verbesserung in Verbindung gebracht wird. 5S ist ein systematischer Ansatz für die Organisation und Standardisierung von Arbeitsplätzen, der dazu beiträgt, die Effizienz zu verbessern und das Verantwortungsgefühl der Mitarbeiter zu fördern. Zu den 5S-Prinzipien gehören:
- Seiri (Sortieren): Entfernen Sie unnötige Werkzeuge, Teile und Anweisungen. Behalten Sie nur das Nötigste und streichen Sie alles, was nicht benötigt wird, um Hindernisse bei der Arbeit zu beseitigen.
- Seiton (In Ordnung bringen): Ordnen und kennzeichnen Sie die benötigten Gegenstände so, dass sie leicht zugänglich sind und verwendet werden können. Ordnen Sie die Komponenten nach ihrem Verwendungszweck, wobei häufig benötigte Gegenstände näher an den Arbeitsbereichen liegen sollten.
- Seiso (Glänzen): Reinigen Sie den Arbeitsplatz und die Ausrüstung regelmäßig, um die Standards aufrechtzuerhalten und sicherzustellen, dass Defekte schneller sichtbar werden.
- Seiketsu (Standardisieren): Die Arbeitspraktiken sollten einheitlich und standardisiert sein. Alle Arbeitsplätze für einen bestimmten Auftrag sollten identisch sein.
- Shitsuke (Durchhalten): Behalten Sie die Standards bei und überprüfen Sie sie. Sobald die vorangegangenen 4 S etabliert sind, werden sie zur neuen Arbeitsweise. Konzentrieren Sie sich weiterhin auf diesen neuen Weg und lassen Sie nicht zu, dass Sie allmählich zu den alten Methoden zurückkehren.
Kanban
Kanban ist ein visuelles Managementsystem, das JIT und Lean Manufacturing unterstützt, indem es die logistische Kette aus der Sicht der Produktion steuert und so die Produktion mit der Nachfrage in Einklang bringt. Bei Kanban werden die Arbeitsaufgaben visualisiert, um den Beteiligten ein klares Verständnis des Fortschritts und der Prozessabläufe zu vermitteln und die in Arbeit befindlichen Produkte auf der Grundlage der Systemkapazität zu begrenzen.
Dieses System soll die Effizienz fördern, indem laufende Projekte auf ein überschaubares Maß begrenzt werden. Dies kann eine Überproduktion verhindern – eine der größten Verschwendungen im Lean Manufacturing. Kanban fördert einen reibungslosen Arbeitsfluss und ermöglicht die schnelle Identifizierung und Beseitigung von Engpässen.
Der Prozess der kontinuierlichen Verbesserung
Die Umsetzung der kontinuierlichen Verbesserung ist ein dynamischer und iterativer Prozess. Die spezifischen Anwendungen und Schritte von CI können je nach Unternehmen, Branche und Zielsetzung sehr unterschiedlich sein. Unabhängig von der angewandten Methodik konzentrieren sich die Instrumente der kontinuierlichen Verbesserung jedoch meist auf die Optimierung von Prozessen, die Beseitigung von Verschwendung und die Steigerung der Gesamtproduktivität.
Die Variabilität liegt in der Art und Weise, wie diese Ziele priorisiert und erreicht werden und wie die individuellen Bedürfnisse des Unternehmens, die Marktbedingungen und die verfügbaren Ressourcen sie beeinflussen. Dies macht CI anpassungsfähig und ermöglicht es jeder Organisation, es auf ihren spezifischen Kontext zuzuschneiden.
Der CI-Prozess hat jedoch einige gemeinsame Grundzüge, unabhängig vom Wo, Wer und Wie. Er umfasst häufig eine zyklische Abfolge von Schritten: Planung, Durchführung, Bewertung und Verfeinerung. So wird sichergestellt, dass Verbesserungen auf präzisen Daten und echtem Feedback beruhen, dass positive Veränderungen nachhaltig sind und im Laufe der Zeit weiter ausgebaut werden, usw.
Beispiel für die CI-Implementierung
Um einen CI-Prozess effektiv zu implementieren, gehen Unternehmen in der Regel ähnlich vor wie bei den folgenden Schritten:
- Identifizieren Sie Ziele. Der erste Schritt einer erfolgreichen CI-Initiative besteht darin, klar zu definieren, was Sie zu erreichen hoffen. Eine gute Möglichkeit, Ziele festzulegen, ist die SMART-Methode, sprich herauszufinden, ob Ihre Ziele spezifisch, messbar, erreichbar, relevant und zeitgebunden sind. Wenn Sie sich zu Beginn klare Ziele setzen, erhalten Sie eine Orientierung und einen Maßstab, an dem Sie Ihren Fortschritt messen können.
- Legen Sie den Prozess fest und definieren Sie ihn. Sobald die Ziele festgelegt sind, besteht der nächste Schritt darin, die bestehenden Prozesse abzubilden, um Ineffizienzen und verbesserungswürdige Bereiche zu ermitteln. Ein detailliertes Mapping hilft dabei, den Arbeitsablauf zu verstehen und Engpässe oder Verschwendungen im System zu identifizieren.
- Kommunizieren Sie den Prozess und setzen Sie ihn ein. Nachdem Sie herausgefunden haben, wie die Prozesse verbessert werden können, besteht der nächste Schritt darin, die Änderungen zu implementieren. Dazu gehört nicht nur der physische Einsatz neuer Methoden oder Tools, sondern auch eine effektive Kommunikation innerhalb des Unternehmens. Es muss sichergestellt werden, dass alle Beteiligten die Änderungen und die Gründe dafür verstehen, denn nur so können die Änderungen akzeptiert und eingehalten werden.
- Verfolgen und messen. Wenn die neuen Prozesse eingeführt sind, ist es wichtig, die Ergebnisse zu verfolgen und die Auswirkungen der Verbesserungen anhand der gesetzten Ziele zu messen. Bei dieser Überwachung sollten relevante Leistungsindikatoren (Key Performance Indicators, KPIs) verwendet werden, um datengestützte Erkenntnisse darüber zu gewinnen, wie gut die Verbesserungen funktionieren.
- Überprüfen und neu starten. Der letzte Schritt besteht darin, die Ergebnisse und den gesamten Prozess zu überprüfen. Dazu gehört, dass Sie analysieren, was funktioniert hat und was nicht, dass Sie die notwendigen Anpassungen vornehmen und sich darauf vorbereiten, den Prozess erneut zu durchlaufen. Bei der kontinuierlichen Verbesserung geht es darum, aus jedem Zyklus zu lernen und darauf vorbereitet zu sein, laufend Änderungen vorzunehmen, um das System weiter zu verbessern.
CI – Bewährte Praktiken für kleine Hersteller
Für kleine Hersteller kann die Einführung von Verfahren zur kontinuierlichen Verbesserung sowohl ein strategischer Vorteil als auch eine Notwendigkeit sein, um in einem sich schnell entwickelnden Markt wettbewerbsfähig zu bleiben. Hier sind fünf bewährte Praktiken, die kleinen Herstellern helfen können, CI effektiv in ihre Abläufe einzubinden:
- Führen Sie regelmäßige Schulungen und Weiterbildungen durch. Bei der kontinuierlichen Verbesserung geht es sowohl um die Weiterbildung der Mitarbeiter als auch um die Verbesserung der Prozesse. Die Einführung regelmäßiger Schulungsprogramme kann den Mitarbeitern helfen, neue Technologien zu beherrschen, CI-Methoden wie Lean oder Six Sigma zu verstehen und diese Fähigkeiten bei ihrer Arbeit effektiv einzusetzen. Darüber hinaus trägt das Engagement für kontinuierliche Weiterbildung dazu bei, die Mitarbeiterzufriedenheit und -bindung zu erhöhen.
- Binden Sie Ihre Mitarbeiter stärker ein. Holen Sie sich Erkenntnisse von denen, die die Arbeit am besten kennen – den Mitarbeitern. Die Einbeziehung von Mitarbeitern aus der Praxis liefert wertvolle Perspektiven, die zu erheblichen Prozessverbesserungen führen können. Fördern Sie die Ideenfindung durch Umfragen oder Think Tanks und geben Sie Ihren Mitarbeitern die Möglichkeit, regelmäßig Feedback zu den Prozessen zu geben. Dieser integrative Ansatz kann nicht nur zur Verbesserung der Prozesse beitragen, sondern auch die Mitarbeiter stärken, was zu einer engagierteren Belegschaft führt.
- Verbessern Sie den Arbeitsplatz. Die Verbesserung der physischen und organisatorischen Umgebung des Arbeitsplatzes kann zu effizienteren Abläufen und einer zufriedeneren Belegschaft führen. Dazu gehört eine effiziente Organisation des Arbeitsplatzes (unter Verwendung von Konzepten wie 5S), die Einhaltung von Sicherheitsstandards und die Schaffung eines ansprechenden und komfortablen Arbeitsumfelds. Verbesserungen am Arbeitsplatz können zu einer höheren Produktivität führen und die Mitarbeiter motivieren, ihr Bestes zu geben.
- Setzen Sie digitale Technologie und Automatisierung ein. Investitionen in Technologien, die sich wiederholende Aufgaben automatisieren und Prozesse optimieren, sind für kleine Hersteller von entscheidender Bedeutung. Tools wie Enterprise Resource Planning Systeme (ERP), Bestandsmanagement sowie Tracking- und Analysesoftware können die Effizienz erheblich steigern.
- Nutzen Sie IoT und maschinelles Lernen. Die Integration von Internet of Things (IoT) und maschinellen Lerntechnologien kann Fertigungsprozesse dramatisch verändern. IoT-Geräte können Daten aus dem gesamten Fertigungsbereich in Echtzeit überwachen und sammeln, während Algorithmen für maschinelles Lernen diese Daten analysieren, um Ausfälle vorherzusagen, Abläufe zu optimieren und die Entscheidungsfindung zu verbessern. Dies kann zu tieferen Einblicken, vorausschauender Wartung und intelligenteren Fertigungsprozessen führen.
Wie kann Fertigungssoftware bei CI helfen?
Fertigungssoftware, insbesondere MRP-Systeme (Manufacturing Resource Planning), spielen eine zentrale Rolle bei der kontinuierlichen Verbesserung. Diese Systeme integrieren verschiedene Aspekte des Fertigungsmanagements, von der Bestandskontrolle und Produktionsplanung bis hin zur Qualitätssicherung und Rückverfolgbarkeit. Fertigungssoftware bietet eine solide Grundlage für CI, indem sie die Transparenz erhöht, die Kommunikation verbessert und Manager mit Analysetools ausstattet, die auf realen Fertigungsdaten basieren.
MRPeasy zum Beispiel bietet kleinen bis mittelgroßen Herstellern eine intuitive und umfassende Lösung, die die Ausführung und Überwachung von CI-Strategien unterstützt. Es ermöglicht Unternehmen die Verwaltung von Produktionssteuerung, Lagerbeständen, Kundenbeziehungen und Beschaffung in einem einheitlichen System, wodurch die Wahrscheinlichkeit von Fehlern und Ineffizienzen verringert wird.
MRPeasy ermöglicht darüber hinaus Datenanalysen in Echtzeit, die Verfolgung von KPIs und umfassende Berichte, die für die Identifizierung von Engpässen, die Vorhersage der Nachfrage und die Optimierung der Ressourcenzuweisung entscheidend sind. So können Sie Entscheidungen auf der Grundlage echter Erkenntnisse treffen und Änderungen schnell und zuverlässig umsetzen.
Die wichtigsten Kernpunkte
- Kontinuierliche Verbesserung ist ein strategischer Prozess der wiederkehrenden Identifizierung, Analyse und Implementierung von Verbesserungen an Arbeitsabläufen und Produkten, um die Produktivität und Effizienz von Fertigungsprozessen kontinuierlich zu steigern.
- Es gibt viele verschiedene Arten von Modellen, Methoden und Initiativen zur kontinuierlichen Verbesserung wie Kaizen, Lean, Six Sigma, Plan-Do-Check-Act oder Just-in-Time-Produktion.
- Die kontinuierliche Verbesserung bringt den Herstellern eine Fülle von Vorteilen, von der Verringerung der Verschwendung und der Verbesserung der Teamarbeit bis hin zur Vereinfachung des Prozessmanagements, zur Kostensenkung und zur Förderung der Innovation am Arbeitsplatz.
- Ein Beispiel für einen CI-Zyklus umfasst die Schritte zur Ermittlung der Ziele, zur Festlegung und Definition des Prozesses, zur Einführung und Kommunikation des Prozesses, zur Verfolgung und Messung der Ergebnisse und zur Umsetzung der Veränderung in großem Maßstab.
- Zu den bewährten Praktiken der kontinuierlichen Verbesserung gehören die Suche nach innovativen Wegen zur Steigerung des Mitarbeiterengagements, die Verbesserung des Arbeitsumfelds, die Nutzung digitaler Technologien wie IoT und maschinelles Lernen usw.
Häufig gestellte Fragen
Um den ROI von Initiativen zur kontinuierlichen Verbesserung zu messen, müssen sowohl die direkten als auch die indirekten Vorteile quantifiziert werden, z. B. reduzierte Kosten, erhöhte Produktivität und verbesserte Produktqualität. KPIs wie Zykluszeit, Fehlerrate oder Durchsatz können direkt mit Finanzkennzahlen korreliert werden, um den ROI zu bewerten. Darüber hinaus können weichere Kennzahlen wie Mitarbeiterengagement und Kundenzufriedenheit Aufschluss über die breitere Wirkung von KI-Investitionen geben.
Die Integration fortschrittlicher Technologien wie IoT und maschinelles Lernen in bestehende CI-Rahmenwerke ist oft mit Herausforderungen verbunden, wie z.B. hohen Anfangskosten, der Komplexität der Implementierung und dem Bedarf an Spezialkenntnissen. Außerdem kann es bei Mitarbeitern, die an traditionelle Methoden gewöhnt sind, Widerstand gegen Veränderungen geben. Die Überwindung dieser Hindernisse erfordert in der Regel eine gründliche Planung, kontinuierliche Schulungen und eine klare Kommunikation der Vorteile, die diese Technologien bieten.
Kontinuierliche Verbesserung kann die Beziehungen zwischen Lieferanten und Kunden erheblich verbessern. Auf der Lieferantenseite können eine engere Zusammenarbeit und gemeinsame CI-Ziele zu einer verbesserten Materialqualität und Liefertreue führen. Auf Kundenseite können kontinuierliche Verbesserungen der Produktqualität und des Kundendienstes die Zufriedenheit und Loyalität erhöhen.
Ihnen könnte ebenfalls gefallen: Statistische Prozesskontrolle – Ein Leitfaden für Hersteller