What Is the Cost of Quality and How to Calculate It?
The cost of quality quantifies the total cost of quality-related efforts and issues. While an effective measure to identify cash drains, it can also be used to balance the price and quality relationship of your products.
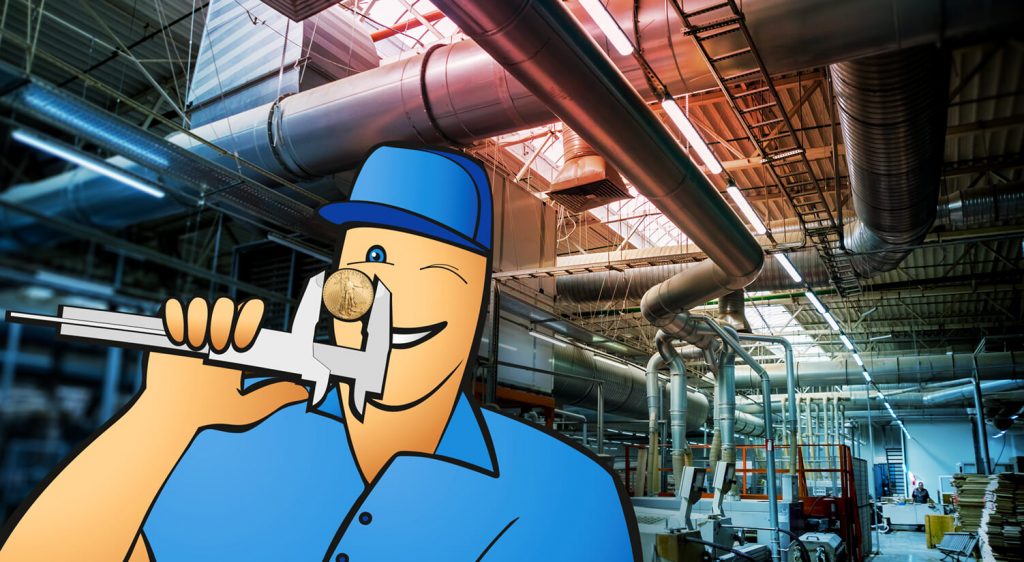
You can also listen to this article:
What is the cost of quality (COQ)?
The cost of quality (also referred to as quality costs) quantifies the total cost of quality-related efforts and issues. In other words, it highlights the financial impact of achieving and not achieving a high standard in the quality of a company’s products and production processes.
As a consumer, you probably know that when comparing two similar products, the more expensive one usually comes out as the winner in terms of quality and durability. This rule also applies to the manufacturing process: to build a product that is better than its rivals, you will often have to be willing to invest more in its production. On the other hand, great quality does not mean anything if a product is not affordable to its price-sensitive target market. Therefore, it is necessary to find a balance between a product’s quality and its manufacturing costs.
Benefits of tracking the cost of quality
Consistently tracking the cost of quality and using it as a feedback mechanism provides numerous benefits that can significantly impact a company’s production efficiency, product quality, and financial health. Here’s an overview of the key advantages:
Improved product quality
The cost of quality helps manufacturers detect and address issues in the production process, ensuring that products meet high standards. This proactive approach not only minimizes the occurrence of manufacturing defects but also improves overall product quality. As a result, customer satisfaction improves due to fewer complaints and product returns, fostering greater brand loyalty and repeat business.
Increased operational efficiency
Monitoring the cost of quality allows companies to identify inefficiencies within their production lines. By understanding where waste and defects occur, manufacturers can streamline operations, thereby reducing the amount of resources wasted on rework and scrap. This optimization leads to a more efficient production process that can deliver products faster and at a lower cost.
Reduced operational costs
Every increase in operational efficiency directly translates into a reduction in costs. Tracking your quality costs enables you to identify financial sinkholes such as frequent product returns or rework, determine their root causes, and eliminate them.
Financial management
Understanding the financial implications of quality-related activities enables better cost control and budgeting within manufacturing operations. Tracking these costs helps companies avoid unnecessary expenditures and focus financial resources on improving product quality and operational efficiency.
Strategic decision-making
The insights gained from analyzing quality-related costs are invaluable for making informed strategic decisions. This data guides everything from process improvements and supplier selection to product design, ensuring that efforts are focused on areas that yield the highest return on investment and align with long-term business goals.
Competitive advantage
Consistently delivering high-quality products improves your brand reputation and sharpens your competitive edge. This not only helps in attracting new customers but also allows your company to command premium pricing. A strong reputation for quality can also increase your market share, as consumers tend to prefer and trust brands known for their reliability.
How to calculate the cost of quality?
COQ is comprised of two factors:
- The costs of maintaining the high quality of products, or the cost of good quality;
- The costs incurred due to quality failures, both internal and external, or the cost of poor quality.
COQ = Cost of Good Quality + Cost of Poor Quality
The cost of good quality (COGQ)
The cost of good quality accounts for investments made to retain or improve the quality of your products. It comprises two smaller categories of expenses:
- Prevention costs. These signify resources used to prevent failures and poor quality. These include costs related to:
- The establishment of product specifications and standards
- Product development
- Quality planning
- Quality assurance
- Risk management
- Training
- Supplier qualification
- Appraisal costs. These are incurred by reviewing and auditing products and production processes to ensure their conformance to quality standards. Appraisal costs may include:
- Inspections of received goods
- Inspections of finished goods
- Testing
- Equipment monitoring
- Quality audits
- Process monitoring
- Supplier performance management
The cost of poor quality (COPQ)
The cost of poor quality comprises costs incurred due to bad practices, failures, and low product quality. It is sub-categorized as:
- Internal failure costs. These are costs related to the low quality of a product detected before it was shipped. Internal failure costs include:
- Unforeseen waste and scrap
- Re-work
- Machinery breakdowns and repairs attributable to substandard maintenance
- Failure analysis costs
- External failure costs. These are costs incurred when a customer detects quality issues after receiving a product. External failure costs include:
- Handling complaints and returns
- Product recalls
- Service and repairs
- Warranty claims
- Shipping damages
Out of all quality costs, external failure costs are the most expensive. The American Society for Quality estimates that the average thriving company’s cost of poor quality is about 10-15% of all operating expenses. In worse cases, however, these costs can even make up 40% of a business’s total expenses. Thus, using the COQ could prove to be a valuable addition to your cost-cutting arsenal.
How to determine which costs are quality costs?
Detecting your costs of quality is relatively straightforward. Use the following graph to identify and categorize your quality costs:
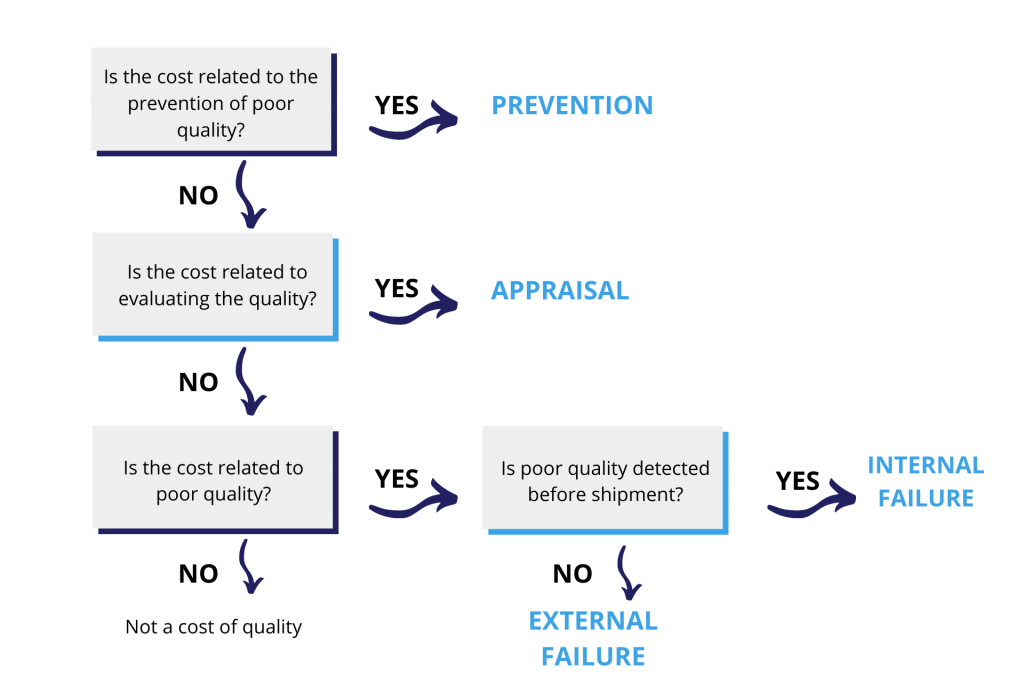
How to reduce the cost of quality?
As a rule, the costs of poor quality start adding up in a much steeper curve than the costs of good quality. Therefore, increasing the costs of good quality can actually bring down the total COQ. Here are some preventative measures you can take to reduce your total quality costs:
- Process standardization. The first step in reducing quality costs is standardizing your processes. Making your operations repeatable enables you to achieve an identical result each time. Having good standardized operating procedures in place therefore allows you to produce a quality product every time.
- Training. Providing your employees with the appropriate training will prevent a lot of foreseeable mistakes that could directly or indirectly affect the quality of your products.
- Quality inspections. Systematic inspections of received materials and finished goods enable you to prevent faulty products from reaching the end customers and to identify issues in the production process early on.
- Monitoring. Process monitoring allows you to fine-tune your operations so that the outcomes would be up to a high standard in terms of both quality and efficiency.
- Supplier performance management. Consistently evaluating supplier performance enables you to clearly communicate any shortcomings and ensure the high quality of incoming materials.
- Returns management. Tracking your product returns can help you identify recurring issues related to your products while reducing the cost of managing returns.
- Root cause analysis. Root cause analysis enables you to use data to identify and eliminate crucial underlying issues that affect the quality of your products.
By integrating these strategies, manufacturers can not only reduce the cost of quality but also improve product reliability and customer satisfaction. It is essential to view quality costs as an investment rather than just an expense; spending appropriately on prevention and appraisal often results in lower failure costs and greater profitability in the long run.
Using MRP software to track and reduce quality costs
Although an MRP system will not calculate the total cost of quality on its own, it can be very helpful both in tracking different quality costs and in implementing preventative measures that would improve your production processes.
Among the functionalities that lend a hand in determining the cost of quality are:
Inspections
The inspection functionality allows you to track the results of the quality reviews of both your received goods and your finished goods.
Return Merchandise Authorization (RMA)
The return merchandise authorization (RMA) functionality helps you manage and track returns, repairs, and replacements your customers have requested.
Write-offs
The write-off functionality allows you to track goods that have been written off from stock due to poor quality.
Service orders
The Service Orders (SO) functionality allows you to track goods that have failed quality inspections and have undergone further rework or repairs.
BOM and routing management
The bill of materials (BOM) and routing functionalities enable you to standardize your production processes by specifying the correct sequence of operations and the appropriate quantities of materials used. The BOM version control functionality enables you to track product iterations and ensure that the production team always operates according to the latest BOM version.
Manufacturing orders
The Manufacturing Orders (MO) functionality allows you to keep a meticulous ‘paper trail’ of each production run that helps to identify where things went wrong, the amount of waste and scrap, and more.
Supplier performance management
MRP software allows you to track various metrics related to the performance of your suppliers. This allows you to continuously evaluate your suppliers, communicate their shortcomings, and switch suppliers when needed.
Implementing and using an MRP system is therefore a cost of good quality that plays an important role in reducing the total COQ.
Key takeaways
- The cost of quality includes all costs associated with achieving and maintaining high product and process quality.
- Regular monitoring of COQ provides vital feedback that can help identify inefficiencies and quality issues early, allowing for timely corrections that improve customer satisfaction and reduce waste.
- The total cost of quality is the sum of the costs of good quality (prevention and appraisal) and costs of poor quality (internal and external failures). This calculation helps businesses understand the investment needed for quality initiatives versus the costs associated with quality failures.
- Effective strategies for reducing COQ include process standardization, employee training, rigorous quality inspections, and continuous monitoring, i.e increasing the costs of good quality to reduce the much more costly costs of bad quality.
- Modern MRP systems support quality management by tracking inspections, managing returns through RMA, monitoring supplier performance, and maintaining detailed records of manufacturing orders.
Frequently asked questions
Prioritizing investments between prevention and appraisal costs involves analyzing past quality data to determine which areas yield the highest return on investment. Typically, investments in prevention are prioritized as they tend to reduce the more costly appraisal and failure expenses by preventing defects before they occur.
Properly managed, reducing the cost of quality should not compromise the quality of the final product. Companies can maintain or even improve product quality while reducing unnecessary costs by focusing on efficient and effective quality practices, such as improving processes and training staff.
Companies should review their Cost of Quality metrics regularly, typically on a quarterly basis, to effectively track improvements and make timely adjustments. This frequent review helps maintain a focus on quality objectives and ensures that quality management strategies are yielding the expected financial and operational benefits.
You may also like: Quality Control in Manufacturing