Material Planning – Definition, Tools, and Tips
Material planning is the process of figuring out what and how much is needed in order to produce goods within a specified timeframe, and ensuring the timely delivery of those materials. Accurate material planning can contribute significantly to the efficiency and profitability of a company.
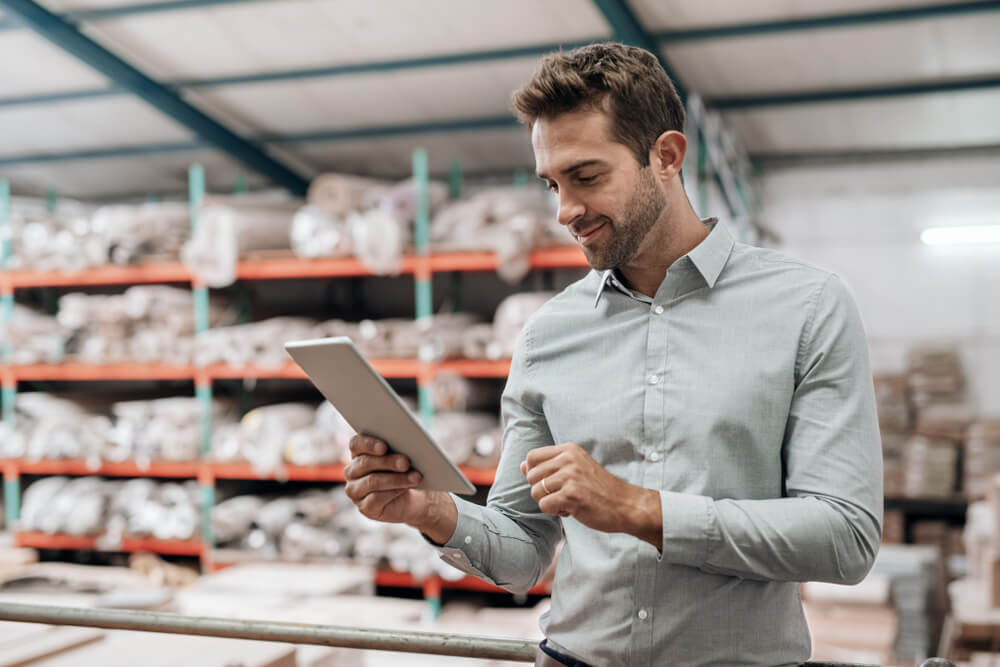
You can also listen to this article:
What is Material Planning?
Material planning is a process in manufacturing that deals with determining the materials and quantities required in production and managing their flow to ensure timely order fulfillment. As such, it is a sub-process of supply chain management.
The main responsibilities of material planners include:
- Analyzing demand forecasts
- Calculating material requirements
- Generating RFQs and purchase orders
- Ensuring the materials’ compliance with specifications, quality standards, and budget constraints
- Generating procurement plans and schedules
In small businesses, however, material planning is an area that often overlaps with inventory management, purchasing, supply chain management, and even production planning. That is why in small manufacturing companies, the person overseeing material planning may also be responsible for everything from material and component sourcing to production scheduling.
Why is Material Planning important?
Accurate and ongoing material planning is a critical activity for any manufacturer. Without it, you risk higher inventory costs, unhappy customers, inventory shortages, and fewer on-time deliveries. When raw materials or components are late, your production schedule can get out of whack, which will likely result in lower profits.
Effective material planning, however, helps with production planning, inventory control, and other areas like sales quoting, work orders, bills of materials, and shop floor management. With reliable material planning, manufacturers can expect to see improvements in customer satisfaction, overall efficiency, and their company’s bottom line.
Benefits of accurate Material Planning
Accurate material planning can provide a range of benefits, including:
- Cost savings. By accurately planning material needs, companies can avoid overstocking or understocking, which can result in unnecessary costs or lost business. Accurate material planning can also help companies negotiate better pricing with suppliers by providing visibility into long-term demand.
- Improved supply chain efficiency. Accurate material planning can streamline the flow of goods throughout the supply chain, reducing lead times and keeping inventory at optimal levels. This can help companies reduce waste, improve delivery times, and better meet customer demand.
- Better inventory management. With accurate material planning, companies can keep inventory levels optimized, reducing the need for costly storage and minimizing the risk of stockouts.
- Improved customer satisfaction. Accurate material planning can help ensure that finished goods are available when customers need them, reducing the risk of delays or backorders. This can help improve customer satisfaction and retention.
- Improved forecasting. While accurate sales forecasts are necessary for accurate material planning, accurate material planning can help improve collaboration between departments, reduce lead times, and optimize inventory levels, all of which can help refine forecasts.
To summarize, accurate material planning can help companies reduce costs, improve efficiency throughout the supply chain, and better meet customer needs.
The 7 basic steps of Material Planning
The material planning process involves several key steps:
- Forecast demand. The first step is to forecast the demand for finished products based on historical data, market trends, and other relevant factors.
- Determine required materials. Based on the demand forecast, the material planning team determines the types and quantities of raw materials, components, and other inputs required to manufacture the products.
- Create a purchasing plan. The material planning team collaborates with the purchasing team to create a procurement plan taking into account factors such as current inventory, lead times, safety stock, and minimum order quantities.
- Create purchase orders. The team creates purchase orders for the required materials, specifying the quantities and delivery dates.
- Track material delivery. The material planning team tracks the delivery of the ordered materials to ensure that they are received on time and in the correct quantities.
- Adjust plans as needed. The material planning team may need to adjust the production plan and purchase orders based on changes in demand, delays in material delivery, or other factors that affect the supply chain.
- Evaluate performance. After the production cycle is complete, the material planning team evaluates their performance against the plan, identifying any areas for improvement and making adjustments to the material planning process as necessary. In addition, you should track and evaluate your supplier performance.
By following a well-defined and structured material planning process, companies can optimize their supply chain flow and minimize waste and inefficiencies.
Material Planning tools and techniques
Reorder point
Reorder point is used to determine when to reorder a particular stock keeping unit. It is the inventory level at which an order should be placed to replenish stock, so that the stock level would not fall below a critical level.
By setting reorder points for their materials, businesses can ensure that they have enough inventory to meet customer demand without incurring unnecessary carrying costs associated with excess inventory. The reorder point is an important component of inventory management systems and is often used in combination with other tools, such as economic order quantity and safety stock, to optimize inventory levels and minimize costs.
Kanban
Kanban is a replenishment technique that uses visual cues such as signcards to trigger production or a new order of materials. The goal of the kanban system is to create a smooth and efficient flow of materials through the production process, while avoiding excess inventory and minimizing waste.
In a kanban system, each production stage has a designated inventory level that is maintained by a kanban card or other visual signal. When the inventory level falls below a certain point, the kanban signal is sent to the previous stage, indicating that more materials are needed. This triggers the replenishment of materials, either through internal production or external procurement.
Just-in-time
Just-in-time (JIT) is a manufacturing and material planning system that is designed to produce or procure materials and products just in time for their use. The just-in-time system relies on real-time demand signals such as customer or manufacturing orders to trigger the production or procurement of materials. Instead of purchasing large quantities of materials and holding them in inventory, JIT material planning systems procure only what is needed at a particular point in time. This reduces the amount of inventory that a company must hold, which in turn reduces the costs associated with storing and managing excess inventory.
Material Requirements Planning
Material Requirements Planning or MRP I is the predecessor of modern MRP and ERP systems. The first widespread computer-based production planning system, MRP I’s practically only function was material planning. The MRP process uses inputs such as the master production schedule, inventory status file, and the bill of materials to calculate the quantities of materials, components, or subassemblies needed to fulfill the expected customer orders during a specified period.
Although there are specialized material requirements planning software systems out there, this basic functionality could also be set up in spreadsheets by hiring an Excel professional or by using templates available online. If you need more advanced functionality for managing your manufacturing business, you need to look further than MRP I.
Read more about Material Requirements Planning.
Manufacturing Resource Planning software
Manufacturing resource planning (MRP II) or manufacturing ERP software allows you to manage manufacturing processes other than material planning, integrating the whole business within a single system. In addition to material requirements planning, this type of MRP system includes functionality that supports and streamlines sales and order management, inventory management, procurement, production planning and scheduling, making it a comprehensive operations management system for manufacturers.
Modern cloud-based MRP software provides manufacturers with a real-time overview of their production processes, inventory levels, purchase and customer order statuses, etc. MRP software allows you to calculate inventory requirements, set reorder points and safety stocks to avoid stockouts even when demand is greater than anticipated, and receive notifications when inventory drops below a determined level, creating an inventory control system that enables you to avoid stockouts and overstocking.
When an accounting module is added to the MRP software, it can also be considered a manufacturing ERP (Enterprise Resource Planning) system.
Some MRP/ERP systems also include backward scheduling functionality which allows you to implement the just-in-time model. In just-in-time manufacturing and inventory management, production is planned for the last minute, meaning that the finished goods are produced just in time for the requested delivery date. This also means that materials are ordered just in time for them to be used in production. This is done to reduce inventory to the absolute minimum, thereby minimizing inventory costs.
Read more about the benefits of MRP in our blog post about the Advantages and Disadvantages of Using an MRP System.
5 tips for making Material Planning more effective
1. Your inventory balances must be accurate
You’ve heard it since the advent of computer programming: “garbage in, garbage out.” If your inventory balances aren’t valid, you won’t be able to count on the data that your system generates for you. In other words, if your on-hand quantity is incorrect, your MRP system will plan around those inaccurate amounts.
Also, ensure that quality control has approved all the inventory in your system. If not, your usable inventory will be less than you’re counting on, and your material planning will be skewered and compromised by bad data.
While the importance of precise data is well understood, surprisingly enough many manufacturers don’t pay close attention to the accuracy of the data they input, and they end up compromising the rest of their material planning efforts. Those efforts should focus on all calendars, resources, inventory, and capacity. Checking the numbers and scheduling periodic reviews will help to make sure the data you’re using is up to date.
2. Proper forecasting should be a priority
MRP systems will typically take either your open or your forecasted sales to calculate your material demands. When you create your forecast, it can be based on anticipated or production figures. Whichever you choose, the system will use the information to generate your material requirements.
Using forecasted sales in conjunction with a master production schedule rather than open sales allows you to estimate your material requirements further out than the timeline that applies to your current sales orders. It also gives you the benefit of scheduling your production and staffing needs long into the future.
The forecast you come up with does not have to be chiseled in granite (nor should it be!). You’ll need to have some flexibility to make alterations as conditions change. Many manufacturers deal with fluctuations throughout the year. These disparities in demand can result from seasons, holidays, events, or trends. If you are going to avoid wasting surplus production or coming up short with demand, you need to make accurate forecasting a priority.
Excellent MRP and manufacturing ERP solutions can help you to augment material planning and forecasting. Your system will be equipped with historical sales data, which should provide you with invaluable insights into your future needs.
3. Take lead times into consideration during material planning
You need to have accurate dates in your system for sales and purchase orders. Ideally, you’ll want your MRP system to inform you when you’ll need your materials for production. For example: when will you need to release the purchase order so you’ll have those twenty sheets of stainless steel to fabricate that structure by the due date?
It’s critical to know how long it usually takes for materials to arrive from the time you order and how long it’s going to take to complete the finished product. To make things even more accurate, you can add in the time it takes for your quality control people to inspect and release the material for production or shipping.
Many of today’s MRP and ERP systems will have a series of fields where you can enter this information, and they will use it to recommend when to place the purchase order and when to start production.
4. Audit your vendors regularly
Along with paying attention to lead times goes performing reviews of transactions by vendor or item number. Through these audits, you can compare the scheduled lead times to actual lead times. You can see how your company is performing for your customers, and you can use the information to make adjustments.
Just a word or two about vendors: It can be comfortable to use the same suppliers each time since you can get consistent quality and pricing by doing that. By establishing a relationship with them, there’s a sense of trust that puts both you and the supplier at ease, especially when large orders are involved.
Just remember not to overemphasize the comfort factor. Perform those regular audits, and review the historical transactions between vendors. See how they compare in terms of anticipated lead time vs. the actual lead time. This information can be invaluable in helping you to improve your material planning process.
5. Understand your capacity
It’s not enough to create a production schedule that has been derived from accurate material planning, the availability of employees, and forecasted demand. You must also consider the various production limits of your work centers and the amount of space to which you have access.
Be sure to factor production capacity and space into the production equation, or you could end up with late deliveries or more inventory than you can store or ship.
By using these tips, your material planning efforts should become more effective as you and your MRP system gather accurate and reliable information that results in timely shipments, and a clearer picture of your inventory.
Key takeaways
- Material planning is a process in manufacturing that deals with determining the materials and quantities required in production and managing their flow to ensure timely order fulfillment.
- Accurate material planning can provide a range of benefits, including cost savings, improved supply chain efficiency, streamlined inventory, improved customer satisfaction, improved forecasting.
- Material planning is best done within a material requirements planning (MRP I) or manufacturing resource planning (MRP II) software.
Frequently Asked Questions
There are several techniques and tools that can be effectively used in material planning, including reorder point, kanban, just-in-time, material requirements planning, and manufacturing resource planning software.
The factors that influence material planning are demand forecasts, production plans, inventory requirements, order sizes, material prices, etc.
A manufacturing ERP or MRP software is a manufacturing management system that can be effectively used to manage material planning, as well as many other business processes. These systems typically include functionality that supports material planning, such as material requirements planning, inventory management, purchasing, production planning, and supplier management.
You may also like: Materials Management – Best Practices for Small Manufacturers