Forward Scheduling vs. Backward Scheduling in Production Planning
Do you need your products ready as soon as possible or just in time for the promised delivery date? Forward and backward scheduling are key concepts in production planning that allow production to be set up according to this fundamental question.
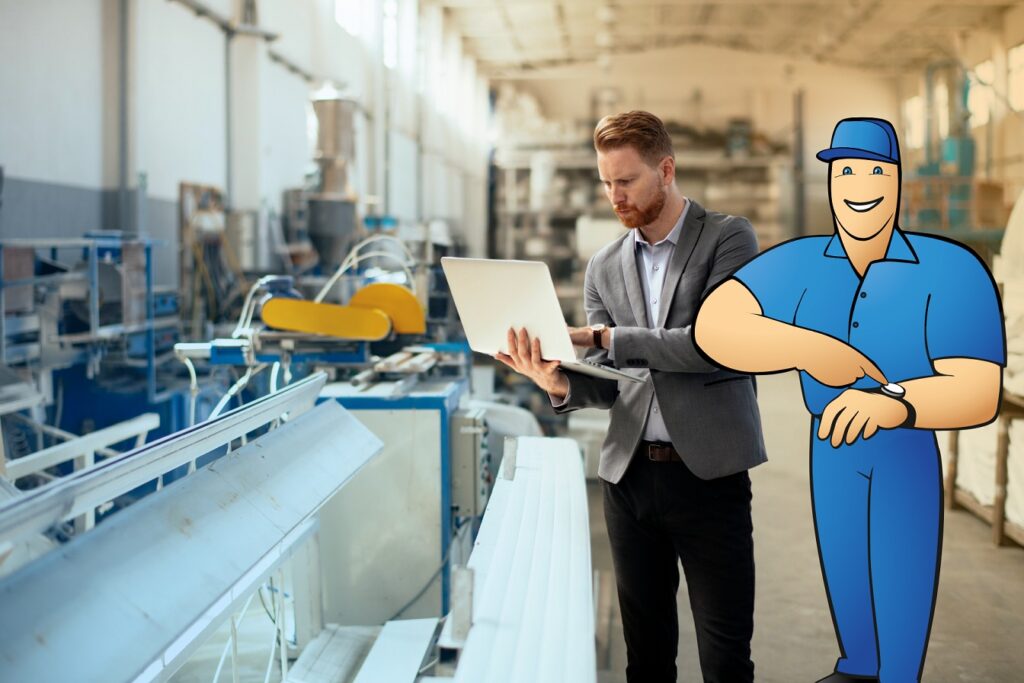
Forward vs. backward scheduling explained
Forward and backward scheduling are production planning methods that designate the direction in time in which production activities are planned out. In forward scheduling, production is planned and scheduled chronologically, while in backward scheduling, it’s planned in reverse order, going backward in time.
It’s important to stress that forward and backward scheduling are not production execution methods but production planning methods. Their difference lies in the order in which production operations are scheduled, not the order in which they’re executed.
The sequence of operations is the same in both methods—purchases and material availability first, then manufacturing, followed by fulfillment. However, the order in which these stages are planned in time is reversed in backward scheduling.
Both forward and backward scheduling largely rely on a capable MRP system to accurately schedule and estimate the planned duration of different production processes.
What is forward scheduling?
Forward scheduling is a production planning method where production orders are scheduled to be fulfilled as soon as possible. New orders are typically added to the production schedule on a first-come-first-served basis, and production lead times are calculated based on the number of preexisting jobs.
In forward scheduling, production operations like procurement, material assembly, manufacturing, and fulfillment are all scheduled to be completed at the first availability. When a customer order is received, manufacturing orders are scheduled to start as soon as materials are available. Shipping is then scheduled based on when production is set to finish.
Forward scheduling is often used by make-to-stock (MTS) and serial manufacturers who want the production line to run as efficiently as possible and avoid downtime. It can, however, also be used by make-to-order manufacturers, for example, if they want to leave a safety margin between the production lead time and the promised delivery date.
What is backward scheduling?
Backward scheduling, also called reverse scheduling, is a production planning method where production is scheduled to be completed no sooner than the promised delivery date. The goal is to finish production orders by the time they’re needed, thus avoiding any standing inventory.
In backward scheduling, production processes are scheduled in reverse order, going backward from a planned delivery date. First, the latest time for shipping is scheduled. Based on that, the latest time to start the manufacturing process is scheduled. Finally, the latest time to purchase materials is determined based on the planned manufacturing start date.
Backward scheduling is a key tenet of just-in-time manufacturing, a production and inventory management philosophy that aims to minimize inventory by synchronizing production with real demand. It thus aligns perfectly with make-to-order (MTO) and engineer-to-order (ETO) workflows. However, it can also be utilized in make-to-stock environments, for example, to guarantee stock for a specific date with assured demand to avoid overproducing early.
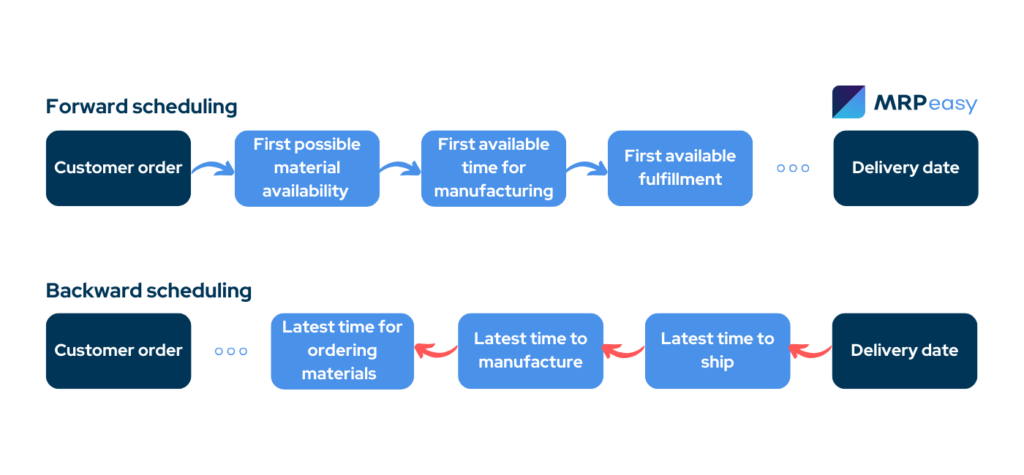
Forward scheduling benefits and challenges
Next, let’s examine the advantages and disadvantages of forward scheduling.
Advantages of forward scheduling
- High resource utilization rate. Forward scheduling allows manufacturers to start production as soon as the required resources are available, ensuring that machinery, labor, and materials are used efficiently and idle time is minimized.
- Supports continuous production. The forward scheduling method is ideal for manufacturers aiming to keep their production lines running consistently, helping to prevent bottlenecks or stoppages in the production flow.
- Simplified planning. Production planning is generally easier in the forward scheduling method since production operations are scheduled consecutively, from present to future.
- More headroom for fulfillment. In forward scheduling, production orders are typically aimed at being completed as soon as possible. This leaves wider timeframes between the production lead time and the promised delivery date and can lead to higher customer satisfaction as orders can be delivered ahead of time.
Disadvantages of forward scheduling
- Higher inventory costs. Because production starts immediately, finished goods may end up in inventory well before they are needed. This increases inventory holding costs and can tie up capital.
- Less control over delivery deadlines: Unlike backward scheduling, which works backward from a delivery date, forward scheduling does not prioritize specific deadlines, which may result in early or late deliveries.
- Difficult forecasting for complex products: In environments with complex, multi-stage production processes, forward scheduling may not provide enough flexibility for managing long lead times or fluctuating supply chain conditions.
- Longer lead times for new orders. The production schedule might already be fully utilized when new orders come in. This can dramatically increase production lead times for new orders, as old ones must be finished first.
Backward scheduling benefits and challenges
Here are the main advantages and disadvantages of backward scheduling.
Advantages of backward scheduling
- Reduced holding costs. Backward scheduling enables production to be timed to finish just in time for delivery or a specified deadline. This minimizes the amount of time finished goods are stored and reduces inventory holding costs.
- Optimized resource allocation: Because production starts as late as possible, resources are used optimally, meaning materials, labor, and machinery aren’t tied up too early. This helps avoid unnecessary resource allocation.
- Reduced overproduction: By aligning production schedules with confirmed demand or exact deadlines, backward scheduling minimizes the risk of overstocking and helps reduce manufacturing waste.
- Easier planning for complex workflows. Backward scheduling simplifies planning for complex products that require multiple stages or components. It ensures that each production phase is synchronized to complete at the right time, making managing intricate workflows and parallel tasks easier.
Disadvantages of backward scheduling
- No buffer time. Because production is scheduled to start later, there is often less room for potential errors or delays. Any disruption in the supply chain, production process, or material availability can put the entire schedule at risk, complicating meeting deadlines.
- More complicated planning. Backward scheduling requires careful planning and coordination, especially in multi-stage production processes. Ensuring that all materials and components are ready at the exact time needed can add complexity to the scheduling process.
- Dependency on accurate forecasts. In environments where demand is forecasted rather than fixed (such as make-to-stock), inaccurate demand forecasts can lead to scheduling issues, resulting in shortages or delays in meeting demand.
Forward and backward scheduling examples
Let’s look at an example of forward and backward scheduling. As we’ve seen, both scheduling strategies are suitable for either make-to-stock or make-to-order workflows in principle. However, it’s more common for MTS producers to use forward scheduling and make-to-order producers to use backward scheduling.
Forward scheduling example
A furniture company needs to produce a large number of standard office desks based on their demand forecast. Using forward scheduling, production is planned to begin as soon as possible, pending material availability for which purchase orders are sent out immediately.
The products are completed according to the availability of resources and labor. Once the goods are finished, they are stored in inventory until needed for sale or shipping. This ensures minimal production lead times and a continuously running shop floor at the expense of some added inventory holding costs.
Backward scheduling example
Our furniture company also utilizes a make-to-order workflow for custom-made furniture. An order comes in with a requested due date of 40 days. Using their scheduling software, the manufacturer first identifies the latest delivery date for timely fulfillment. Then, they work backward through the necessary production steps to determine when each stage should begin so that it finishes at just the right time for the next one.
Supposing the desks require 7 workdays for missing materials to arrive, 11 workdays to produce, 3 workdays for finishing and quality control, and 3 workdays to ship, the production schedule might look like this:
- Delivery date – Day 40.
- Shipping – Day 37.
- Quality control – Day 34.
- Manufacturing – Day 23.
- Material purchasing – Day 16.
With that, the manufacturer knows to order the materials to arrive 16 days from now so that the order’s completion date is as close as possible to the promised delivery date.
Which method should you choose?
Deciding which scheduling approach to take depends on many factors and business needs, such as:
- What am I producing? The complexity, customization level, and lead time of your products can influence whether forward or backward scheduling is more appropriate. For highly customizable products, backward scheduling might align better with strict delivery dates. However, forward scheduling can help maintain a consistent production flow for standardized products.
- Do I use sales forecasts? Many companies plan production based on sales forecasts. For example, even if a company operates 100% on a make-to-order basis, purchasing materials can still be done based on forecasts. In this case, backward scheduling can be used based on the sales forecast to predict when materials should be purchased and when they should arrive.
- How much flexibility do I require in planning? Forward scheduling generally allows for more flexibility if your production process requires adjusting to last-minute changes in demand or order specifications. However, if you’re optimized for on-time deliveries, backward scheduling offers better control by working backward from the final delivery date.
How can manufacturing software help with production scheduling complexities?
But what if you didn’t have to choose at all? Modern manufacturing ERP software can utilize both scheduling methods, switching between forward and backward planning based on your production needs and priorities.
These tools utilize dynamic scheduling systems, which allow manufacturers to adjust and reorganize schedules on the fly to accommodate real-time changes in production needs. Dynamic scheduling allows moving existing jobs around to optimize resource allocation. For instance, if a high-priority order comes in, lower-priority tasks can be shifted, ensuring that critical deadlines are met while maintaining overall efficiency.
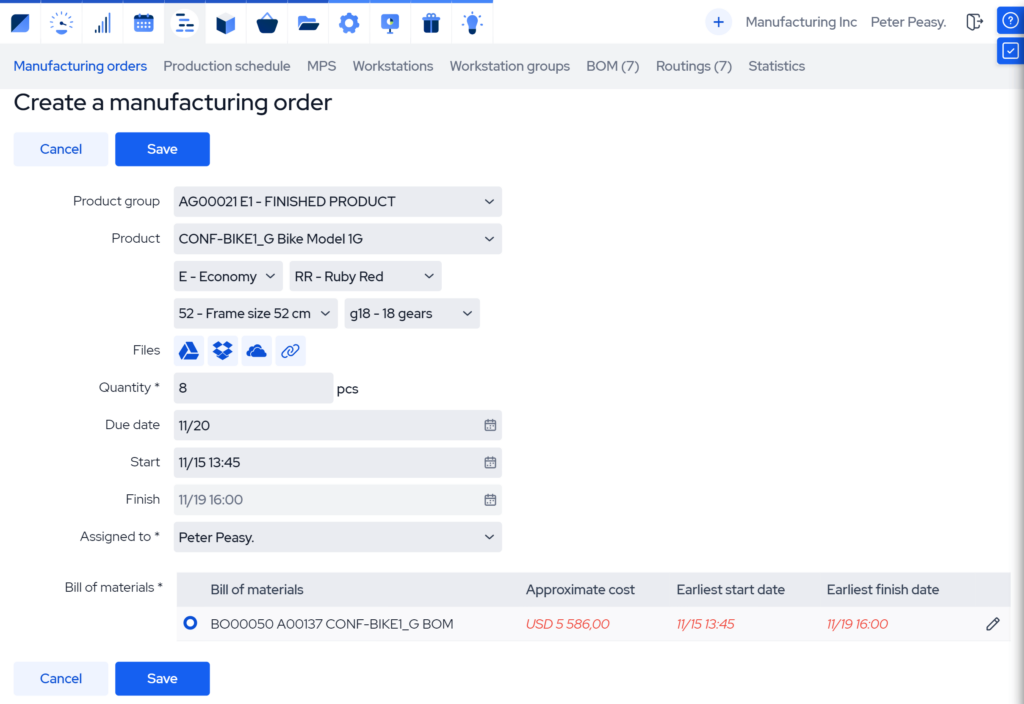
Modern MRP software also allows you to plan different types of workflows, adjusting scheduling for route optimization. Products with complex routing or shared resources between different product lines can be managed effectively by dynamically choosing the most suitable scheduling method at each stage.
Additionally, advanced software often includes master production scheduling (MPS) functionality. MPS takes into account demand forecasts, sales orders, and inventory levels to create a high-level plan for production. Based on this, forward or backward scheduling can be switched as needed. For example, forward scheduling could be used for stock replenishment to maintain consistent inventory levels. In contrast, backward scheduling can be applied for custom or time-sensitive orders to meet precise delivery dates.
Combining both scheduling methods in one integrated system ensures manufacturers can respond dynamically to changes in demand, production capacity, and material availability—making hybrid forward-backward scheduling the most versatile and efficient approach for modern production environments.
Key takeaways
- Forward scheduling is a production planning method that schedules production to begin as soon as resources are available, ensuring continuous operation and minimizing idle time.
- Backward scheduling is a planning method that works backward from a set delivery date, timing production to finish just in time for delivery and reducing inventory holding costs.
- Forward scheduling is ideal for maintaining a continuous production flow, but it may lead to higher inventory costs and less control over exact delivery dates.
- Backward scheduling’s main strength is avoiding overproduction and reducing holding costs by aligning production with demand. However, it can be challenging in case of disruptions or inaccurate forecasts.
- Choosing the best scheduling method depends on many factors, such as product complexity, delivery deadlines, and the need for flexibility in planning and resource management.
- Modern manufacturing software enables dynamic scheduling, allowing manufacturers to schedule production using a combination of forward and backward planning to optimize resource allocation and adapt to real-time changes.
Frequently asked questions
Backward scheduling is commonly used in make-to-order production. For instance, if a manufacturer receives an order with a strict delivery date, they will work backward from that date to determine when to start each production phase. This ensures that the product is completed just in time for shipping without creating excess inventory.
Forward and backward scheduling are production planning methods used to organize when different stages of production take place. In forward scheduling, production begins as soon as resources are available and continues sequentially. In backward scheduling, production is planned in reverse from a set delivery date, ensuring that the product is finished just in time.
A backwards schedule is a production plan that works in reverse from a final due date. It calculates when each step of the production process must start in order to meet the delivery deadline. This method is commonly used to minimize inventory holding costs and align production with exact customer demands.
Yes, it’s possible to use both forward and backward scheduling within a single production environment, but not typically within the same work order. Forward scheduling is easily applied for make-to-stock items, while backward scheduling can be used for make-to-order products. Modern MRP/ERP systems support dynamic scheduling, allowing you to switch between the two based on production needs.
You might also like: What Are Co-Products and How to Track Them?