Warehouse Management – A Comprehensive Guide
Warehouse management oversees the operations in a warehouse to ensure efficient storage, handling, and distribution of goods. Here is a comprehensive guide to the basics of effective warehouse management.
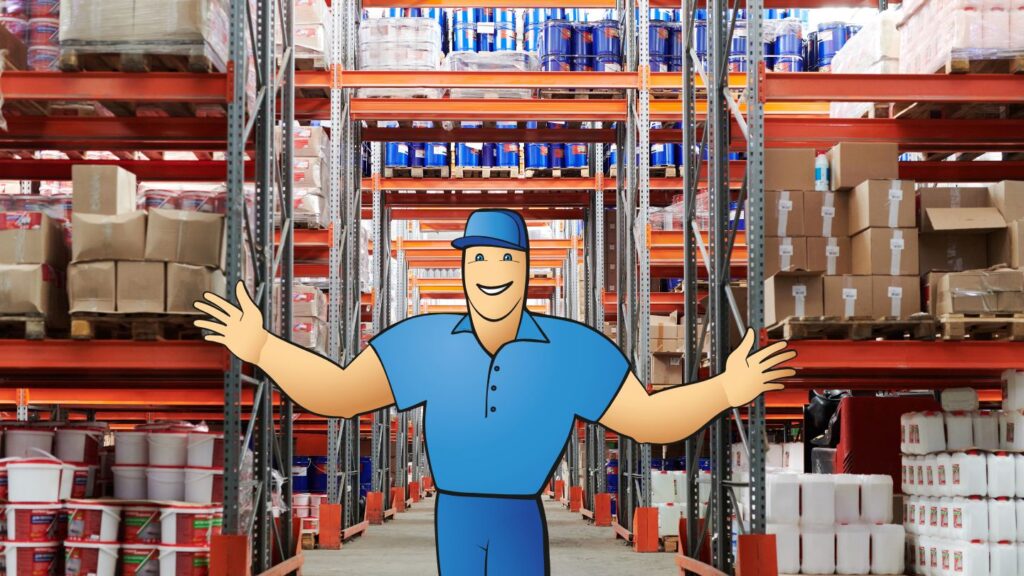
You can also listen to this article:
What is warehouse management?
Warehouse management involves overseeing the day-to-day operations of a warehouse to ensure efficient storage, handling, and distribution of goods and materials. This process encompasses a variety of tasks including inventory management, picking and packing processes, product slotting, and ensuring safety protocols are followed.
Why is warehouse management important?
Warehouse management stands as a critical component of the supply chain, aiming to control the storage and movement of goods within a warehouse and process the associated transactions, including shipping, receiving, put-away, and picking. Here are several reasons why effective warehouse management is essential:
- Optimized warehouse operations. Proper warehouse management ensures that goods are stored efficiently and are easy to locate, reducing the time and effort spent on handling items. This optimization leads to faster processing times and can significantly increase productivity.
- Accurate stock levels. Effective warehouse management helps maintain accurate records of inventory levels, reducing the likelihood of overstocking or stockouts. This accuracy is vital for maintaining production schedules and meeting customer demands.
- Reduced waste. By managing inventory better, companies can minimize the amount of expired or obsolete stock, leading to reduced waste and increased cost-efficiency.
- More efficient space utilization. Efficient use of storage space means that more goods can be stored in a smaller area, reducing the need for additional storage facilities and lowering storage costs.
- Reduced labor costs. Well-organized warehouses reduce unnecessary movements, leading to more efficient labor use and lower labor costs.
- Faster delivery times. With a well-managed warehouse, goods can be processed and shipped quickly, leading to faster delivery times for customers.
- Better order accuracy. Accurate picking, packing, and shipping processes reduce errors in order fulfillment, thereby increasing customer satisfaction and reducing return rates.
- Regulatory compliance. Good warehouse management helps ensure that the storage and processing of goods comply with relevant laws and regulations, which is particularly important in industries such as food, pharmaceuticals, and chemicals.
- Effective security measures. Effective management includes proper security measures to prevent theft and damage, safeguarding the company’s assets.
- Streamlining order fulfillment. Crucial for e-commerce, efficient warehouse management directly impacts the speed and accuracy of order fulfillment. This efficiency ensures that orders are processed and dispatched on time, enhancing the customer experience.
- Boosting customer satisfaction. Effective management of warehouse operations ensures on-time delivery and high-quality service, leading to increased customer satisfaction and loyalty.
- Meeting market demands. An adaptable warehouse management system allows companies to scale operations up or down based on current market demands, providing a competitive edge.
Proper warehouse management can therefore transform a business, propelling it to greater efficiency and growth.
Warehouse management vs. inventory management
While both warehouse management and inventory management are integral parts of supply chain operations, they focus on different aspects of handling materials and goods.
Warehouse management is primarily concerned with the operational aspects of managing a warehouse’s day-to-day functions. This includes the physical storage, movement, and distribution of goods, ensuring that everything from receiving to shipping is executed efficiently. Key tasks include inventory handling, optimizing warehouse layout, managing warehouse staff, and handling equipment to ensure smooth operations and safety standards are met.
Inventory management, on the other hand, focuses on controlling and overseeing the quantities of stock to maintain the balance between supply and demand. It involves activities such as monitoring stock levels, forecasting future demand to prevent overstocking or stockouts, managing stock replenishments, and keeping track of product sales to maintain the right amount of inventory at all times.
Efficient warehouse management facilitates better inventory management by improving the accuracy of stock records and speeding up the fulfillment processes, thus ensuring that inventory levels are kept optimal based on real-time supply chain dynamics.
Tips for optimizing your warehouse layout
Designing an optimized warehouse layout is critical for improving operational efficiency and productivity. An effectively planned layout reduces processing times for shipments, lowers operating costs, and improves safety. Below are the steps to create an optimized warehouse layout with examples of arrangements suited for various operational needs:
1. Understand your requirements
Evaluate the types and quantities of items stored to determine space requirements. Understand how goods move through your warehouse, from receiving to shipping, to identify the most effective arrangement.
For example, place high-demand items near the shipping area to reduce travel time and store bulky or heavier items in lower or ground-level racks to facilitate easier handling.
2. Plan your space usage
Divide the warehouse into distinct areas for receiving, storage, picking, packing, and shipping. Ensure each zone is logically placed to minimize unnecessary movement. Utilize vertical space effectively to maximize storage capacity.
For example, arrange zones in a sequence that aligns with your operations flow, such as placing the packing zone between the picking and shipping zones. In addition, quality control points should be situated near both receiving and shipping areas to efficiently handle incoming inspections and final checks before dispatch.
3. Optimize picking paths
Design the layout to minimize the distance that workers need to travel during picking operations. Implement picking methods such as batch or zone picking to increase efficiency.
Examples:
- Batch picking. Use for orders with multiple small items to reduce trips. This is particularly useful for e-commerce businesses with diverse but small orders.
- Zone picking. Assign pickers to specific zones to reduce movement and improve picking time. Ideal for larger warehouses with clearly segmented product categories.
4. Implement flexible storage solutions
Use adjustable shelving and modular storage units that can be reconfigured as inventory needs change. This flexibility allows for adaptation to seasonal fluctuations or changes in product demand.
For example, employ modular shelving for mixed merchandise environments where product sizes vary significantly and utilize adjustable racks in areas with varying product height requirements to optimize storage density and accessibility.
Read more about Warehouse Organization.
8 essential steps of warehouse management
Understanding each step of the warehouse management process can help businesses optimize operations and improve overall efficiency. Here’s a detailed look at how a typical warehouse management process works:
Step 1: Receiving goods
- Inspection and counting. Upon arrival, goods are inspected for damage and counted to ensure the quantity matches the purchase order.
- Labeling and documentation. All received goods are labeled and documented, and relevant information is updated in the warehouse management system (WMS).
Step 2: Put-away and storage
- Assigning storage locations. Items are assigned a specific location in the warehouse based on their type, size, and frequency of access. This process of determining the optimal placement of items in a warehouse is called slotting.
- Storing goods. Goods are moved to their designated locations using appropriate handling equipment to maximize space efficiency and accessibility.
Step 3: Inventory control
- Regular audits. Periodic inventory counts are conducted to ensure that the inventory records match the physical stock.
- Cycle counting. Frequent cycle counts for high-value or fast-moving items help maintain inventory accuracy without the need for complete inventory checks.
Step 4: Picking
- Order receipt. Orders are received, after which a picking list is created for the warehouse.
- Picking strategy. Depending on the order, different picking strategies like piece picking, batch picking, or zone picking are employed to optimize the picking process.
Step 5: Packing
- Verification. Items are checked against the order list to ensure accuracy.
- Packaging. Goods are securely packaged for shipment, considering factors like weight, dimensions, and type of goods to minimize damage during transit.
Step 6: Shipping
- Loading. Packaged goods are loaded into delivery trucks using equipment like forklifts or pallet jacks.
- Documentation. Shipping documents are prepared, including bills of lading, invoices, and shipping labels.
- Dispatch. Goods are dispatched to their destination, and the warehouse management system (WMS) is updated to reflect the shipment.
Step 7: Returns processing
- Receiving returns. Returned items are inspected and categorized based on their condition and the reason for return by using an RMA module within the WMS.
- Restocking or disposal. Items that are in good condition are restocked, while others may be disposed of or sent back to suppliers.
Step 8: Reporting and optimization
- Performance analysis. Regular reports generated by the WMS help analyze the efficiency of various processes.
- Continuous improvement. Insights from data analysis are used to optimize operations, reduce costs, and improve service delivery.
By following these steps, warehouse managers can ensure a smooth workflow from the moment goods enter the warehouse until they are shipped out.
Tips for effective warehouse management
Here are some practical tips for efficient warehousing:
1. Optimize layout and space utilization
Maximizing the use of available warehouse space can significantly improve operational efficiency. Consider re-evaluating your layout by positioning high-demand items closer to the shipping area to reduce picking time and utilizing vertical space for storage to free up valuable floor space for easier navigation and quicker access.
2. Standardize processes and procedures
Consistency in operations ensures that all tasks are completed efficiently and accurately. Develop and document standard operating procedures (SOPs) for all activities, standardize receiving, put-away, picking, and shipping processes to reduce errors and training time, and implement clear labeling and signage to help staff navigate and find items quickly.
3. Employ effective inventory management techniques
Maintaining the right inventory levels is crucial to prevent overstocking or stockouts. Use demand forecasting to adjust inventory levels based on anticipated needs and implement a cycle counting program to regularly verify inventory accuracy without disrupting daily operations.
4. Improve labor management
Optimizing your workforce is critical to boosting productivity and reducing costs. Implement cross-training programs to ensure employees can perform multiple tasks, increasing flexibility in workforce deployment, and use labor management software to track performance and identify areas for improvement.
5. Embrace technology and automation
Incorporating technology can streamline operations and reduce manual errors. Invest in automated material handling equipment like conveyor belts, automated guided vehicles (AGVs), or robotic pickers, and use barcode scanning to improve the accuracy and speed of inventory processing.
6. Focus on safety and ergonomics
A safe warehouse is more productive, and attention to ergonomics reduces injuries and boosts morale. Conduct regular safety audits and training sessions to keep safety front and center, and design workspaces that reduce strain and fatigue, such as adjustable workstations and ergonomic handling equipment.
7. Implement warehouse management software
Modernizing your warehouse operations with specialized software such as WMS, ERP, MRP, or inventory management software can lead to significant improvements. Choose a system that integrates warehouse and inventory management to get real-time visibility into stock levels, order status, and workflow efficiencies, and automate tasks such as inventory tracking, order processing, and reporting to reduce manual workload and minimize errors. Consider an MRP or manufacturing ERP system if you need to integrate your warehouse with production.
Important warehouse management KPIs
Key Performance Indicators (KPIs) are vital for evaluating the effectiveness of warehouse operations, helping managers identify areas for improvement and measure progress over time. Here are some of the most important warehouse management KPIs:
- Inventory accuracy. This KPI measures how accurately the physical inventory matches the recorded inventory in a management system. High accuracy reduces stock discrepancies, which can cause order delays and inventory write-offs.
- Order accuracy. Order accuracy refers to the percentage of orders shipped without errors. It’s crucial for customer satisfaction and reduces the costs associated with returns and reshipping.
- Order fulfillment cycle time. This measures the time it takes from when an order is placed until it is fully shipped. Reducing this cycle time can enhance customer satisfaction and operational efficiency.
- Carrying cost of inventory. This KPI tracks the total cost of holding inventory, including storage, handling, insurance, and depreciation. Optimizing these costs can significantly impact the overall profitability of operations.
- On-time shipments. On-time shipments are a critical measure of the warehouse’s ability to dispatch orders on the scheduled time. High performance in this area is often directly correlated with customer satisfaction and retention.
- Picking accuracy. Picking accuracy measures the percentage of picks that are correct, indicating the efficiency of the picking process and its impact on order accuracy.
- Rate of return. This KPI measures the percentage of goods returned by customers. Analyzing the reasons for returns can provide insights into underlying problems in product quality or order fulfillment processes.
- Capacity utilization. This KPI assesses how effectively the warehouse uses its available space and can indicate the need for expansion or reorganization.
- Labor productivity. Labor productivity metrics assess the output of warehouse staff, often measured as units picked per hour or costs per shipping unit. Enhancing labor productivity can lead to lower operational costs and improved throughput.
- Inventory turnover. Inventory turnover measures how often inventory is sold and replaced over a period. High inventory turnover rates can indicate effective inventory management and healthy demand for products.
Monitoring these KPIs allows warehouse managers to make data-driven decisions that streamline operations, enhance efficiency, and improve service quality. Implementing a robust warehouse management system can aid in tracking these KPIs accurately and in real time, providing ongoing insights into warehouse operations.
Benefits of ERP in warehouse management
Enterprise Resource Planning (ERP) software offers a multitude of benefits that streamline operations at manufacturing facilities, distribution centers, and retailers. Here’s a detailed look at how software can transform warehouse operations:
- Warehouse automation. ERP software automates complex warehouse processes such as inventory recording and tracking, and the picking and packing of orders. Automation helps speed up these processes, reducing the workload on staff, and minimizing the chances of bottlenecks.
- Reduction in human error. Human error in managing stock keeping unit (SKU) details, order entries, and other data-intensive tasks can lead to significant issues like inventory mismanagement and customer dissatisfaction. ERP reduces these errors by automating data entry and other repetitive tasks, enhancing data accuracy across the warehouse operations.
- Improved order management. ERP systems enable better tracking and managing of orders from the point they are received until they are fulfilled. This capability ensures that orders are processed efficiently, and customers receive their products on time, boosting customer satisfaction and loyalty.
- Overview of the operation. Modern ERP systems integrate the whole business, providing a unified view of operations and inventory across the entire organization. This integration facilitates better decision-making and offers end-to-end traceability of products and materials throughout the supply chain.
- Mitigation of disruptions. By providing accurate real-time data on inventory levels, order statuses, and material requirements, ERP software helps managers identify and address issues before they cause disruptions in the supply chain.
By leveraging these benefits, ERP software not only improves operational efficiency but also enhances the reliability and responsiveness of the supply chain, making it a critical investment for any business aiming to optimize its operations and reduce costs.
Choosing the right warehouse management software
When selecting a warehouse management software, consider the following factors:
- Specific needs and scalability. Understand your specific operational needs and future growth plans. Choose software that not only meets current requirements but can also scale as your business grows.
- Cloud-based vs. on-premise. Cloud-based solutions offer the advantage of lower upfront costs, easier updates, and remote accessibility. However, some enterprises may prefer on-premise solutions for enhanced control.
- Provider reputation and support. Choose providers known for their reliability and customer support. Research their service history and client testimonials to gauge their credibility and the quality of their support services.
- Pricing structure. Examine the pricing structure carefully. Consider both upfront and ongoing costs, including any fees for updates, support, or additional modules.
By carefully evaluating these factors, businesses can discover the right warehouse management solution that enhances operational efficiency, supports scalability, and integrates seamlessly with the broader supply chain management strategy.
Key takeaways
- Warehouse management oversees daily warehouse operations, focusing on efficient storage, handling, and distribution of goods and materials.
- Effective warehouse management optimizes operations, maintains accurate inventory levels, reduces waste, and improves order accuracy and delivery times, significantly boosting productivity and customer satisfaction.
- Warehouse management deals with the physical operations of a warehouse including storage and distribution, while inventory management focuses on maintaining optimal stock levels to balance supply and demand.
- To optimize a warehouse layout, assess your storage needs and operational flow, strategically place high-demand items, and use vertical space and flexible storage solutions to enhance efficiency.
- The warehouse management process includes receiving goods, efficient storage, inventory control, picking, packing, shipping, managing returns, and continuous optimization through regular performance analysis.
- Effective warehouse management involves optimizing layout, standardizing procedures, employing robust inventory management, improving labor productivity, utilizing automation, maintaining safety, and implementing comprehensive management software.
Frequently asked questions
Technology such as RFID tagging and barcode scanning can significantly enhance inventory accuracy by automating tracking and reducing the likelihood of human errors during inventory counts and data entry.
Current trends in warehouse automation include the use of autonomous robots for picking and transporting goods, AI-driven optimization for storage and retrieval, and advanced analytics platforms that predict demand patterns, all of which contribute to faster, more efficient operations and reduced operational costs.
Common challenges include integration with existing systems, staff training, and initial setup costs. These can be mitigated by choosing a WMS that offers flexible integration capabilities, providing comprehensive training programs for employees, and conducting a thorough cost-benefit analysis before implementation.
You may also like: On-Time-In-Full (OTIF) – A Complete Guide