Order Picking – A Quick Guide to Greater Efficiency
Order picking is a fundamental process in warehouse management, essential for ensuring timely and accurate customer order fulfillment. In this post, we explore various manual and automated picking methods to enhance efficiency and reduce costs, each tailored to different warehouse sizes and operational needs.
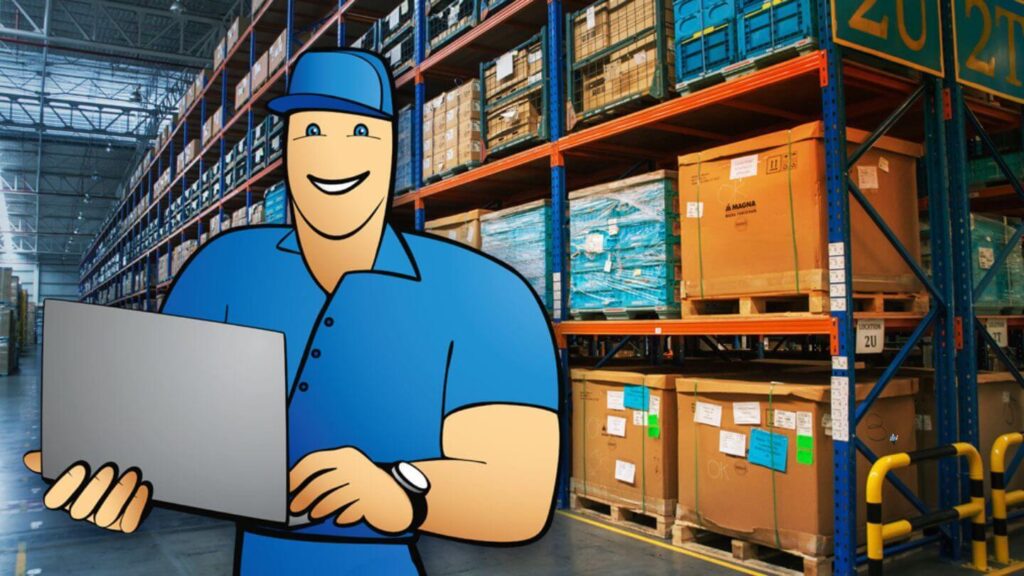
You can also listen to this article:
What is order picking?
Order picking is a warehouse management term that signifies physically collecting goods from inventory in order to fulfill customer orders. It’s an important part of the order fulfillment process that helps to save time and reduce costs when conducted efficiently. Picking is often assigned to warehouse workers or, in the case of larger operations, specialized order pickers.
Warehouse order picking is equally important for e-commerce fulfillment centers as it is for local distributors or independent manufacturers. The chief difference lies in the volume of orders and the scale of the inventory or warehouse.
Order picking vs material handling
Order picking should not be confused with material handling. Material handling is an internal logistics process that involves getting raw materials or work-in-process items like sub-assemblies or half-finished components, to the next step in their manufacturing routing, like a workstation.
While material handling also involves shop floor or warehouse workers picking items from inventory, it is not considered order picking. Material handling, along with its associated costs, is a part of the manufacturing process whereas order picking is associated with the order fulfillment process – getting goods from stock to ready them for shipping. However, both terms are essential in inventory management.
The importance of efficient order picking
Order picking done right can have a considerable effect on order fulfillment efficiency. This is as relevant for manufacturers as it is for distributors. Here are four reasons why it’s important to put emphasis on increasing order picking efficiency.
- Reduction in operational costs. Order picking can be labor-intensive and time-intensive, especially for scaling operations. Minimizing the manpower, time, and effort required to fulfill orders allows companies to keep operational costs in check.
- Improvement in customer satisfaction. Faster and more accurate picking means quicker fulfillment with fewer errors. This responsiveness enhances customer satisfaction, important for maintaining a competitive edge and encouraging repeat business.
- Scalability. A well-implemented and efficient order picking system means that a warehouse is well-equipped for increases in order quantities, whether sudden or incremental. Efficient picking practices allow for handling increased order volumes without a proportional increase in errors or delays, vital for growth during peak demand periods or business expansion.
- Enhanced inventory management. Order picking processes are often integrated with robust inventory management systems. This helps maintain accurate inventory levels throughout the shipping process and reduces inventory errors.
Manual order picking methods
There are a number of tried and tested order picking methods to choose from, depending on the warehouse layout, the scale of the operation, the type of goods a company purveys, etc. Let’s go over the primary manual methods of order picking.
Single order picking
Single order picking, sometimes also called discrete picking, is the most straightforward order picking method. One picker is responsible for picking up and compiling all the stock keeping units (SKUs) that an order consists of at a time, after which the process repeats for the next order.
Single order picking is applicable for small-scale operations with limited SKUs, incoming orders, and usually a small warehouse.
Batch order picking
This picking method, also called multi-order picking, emphasizes fulfilling similar or identical orders at a time, and or picking identical SKUs for somewhat different orders at the same time. In either case, batch picking helps save time as the picker needs to visit a warehouse location of an SKU only once for multiple orders, instead of needing to pick the same SKU multiple times for each separate order.
Cluster picking
Much like batch picking, cluster picking involves picking an SKU for many orders at once. However, the picked goods are placed in bins that the picker brings with them for example on a picking cart. The bins are separated by individual orders or pick lists, allowing for many items for different orders to be picked up in a single trip through the warehouse.
Cluster picking can also eliminate the need for order sorting at the picking area because the orders get sorted on the go by the pickers.
Zone picking
In zone picking, the warehouse is divided into zones and each zone is assigned its own pickers. If a customer order consists of items located across many zones, different pickers will only pick the items in their corresponding zones and bring them to the picking area. The order is then sorted and finalized. Zone picking is popular among larger warehouses or businesses that often get complicated orders with many SKUs.
The zones can be created based on any number of classifiers like warehouse shape, item types, item age, etc., or by methodologies like the ABC rule which divides stock into categories based on its popularity or utilization frequency.
Pick and pass
Pick and pass is essentially a combination of zone and cluster picking. Like in zone picking, the warehouse is divided into sectors. And like in cluster picking, items are sorted into bins or containers while they’re getting picked. Once all items for an order have been picked in a zone, the container is passed to the next picker in the next zone. This way, orders get sorted while they’re getting picked.
Wave picking
Wave picking is also a combined picking method. It’s a cross between zone and batch picking. In wave picking, the warehouse is also divided into zones, however, orders are grouped based on order times and importance and then picked up in “waves” to further optimize warehouse movements, avoid congestion, and eliminate excess labor.
Pallet picking, piece picking, and case picking
Aside from the picking methods above, there are other picking-related terms in use in warehouse management. Pallet, piece, and case picking are not picking methods as such, they simply refer to the type of item that’s picked.
Pallet picking becomes relevant when a group of items such as a product batch or bundled goods are packed and placed on an individual pallet in a warehouse. When an order comes in for the package, the full pallet of goods is moved to the shipping area for fulfillment. Palletized orders are usually heavy and require a forklift or other heavy equipment to move.
Piece picking, on the other hand, refers to any type of picking in which one item is picked at a time. Any of the abovementioned picking methods may employ piece picking. Case picking, meanwhile, refers to picking a whole case or carton full of items, needed for either different orders or a single larger order, instead of picking just one item at a time.
Automated order picking systems
Next to manual picking, automated order picking systems are potential means of further increasing picking efficiency. These may be employed in any type of manufacturing or distribution setup. However, as they presume some form of specialized equipment or installation, they are perhaps more cost-efficient for larger operations or ones with larger order volumes and higher SKU complexity. Let’s look at four examples.
Pick-to-light
As the name suggests, pick-to-light systems use LED lights installed on racks and shelves of the warehouse to provide visual cues to guide pickers to the correct storage locations. This system also needs a barcode system to be integrated. Once a barcode for an outgoing order is scanned, relevant location LEDs light up in the warehouse.
This method can significantly boost picking efficiency and reduce error rates and pickers’ workloads. It’s a good option for environments with high product turnover.
Voice picking
Voice picking systems involve using wearables or two-way radios that enable the picker to communicate or get voice guidance from an administrator. The picker receives instructions on where to go and what to pick through their headset. This hands-free operation allows workers to move more efficiently, simplify picking, and stay safe as they can keep their eyes and hands free for navigating the warehouse and handling goods.
Voice picking enhances multitasking and reduces the likelihood of picking errors. Many warehouses and manufacturers use voice picking in tandem with other methods.
Conveyor belt and sorting systems
Conveyor belt systems are automated paths that transport items from one point to another in the warehouse. When integrated with automated sorting systems, they can streamline the entire picking process by automatically transporting and sorting items based on the destination, order priority, or other criteria. These systems are particularly effective in larger-scale operations where goods need to move quickly or over longer distances within a warehouse or distribution center. Implementing them is rarely cost-efficient for smaller companies, however.
Scanner-aided picking
Scanner-based systems utilize barcode or RFID scanners to enhance the accuracy and efficiency of the picking process. Pickers use handheld scanners to scan items as they pick them, which sends data to the inventory management system in real-time. This data can help keep inventory optimized, reduce errors, and provide insights into warehouse operations. Scanner-based picking is versatile and can be integrated with other technologies such as ERP systems for a comprehensive management solution.
How to track order picking efficiency?
Traceability is as important in warehouse management as it is in production and inventory management. Without knowing how a picking method is performing, there is no way to accurately gauge picking efficiency. Here are three order picking KPIs to consider including in your stock performance dashboard.
Picking accuracy
Picking accuracy measures the error rate of the picking process before shipping. It’s calculated by dividing the number of orders picked correctly by the total number of picked orders. Picking accuracy is critical to measure as correctly fulfilled orders directly impact customer satisfaction.
Picking accuracy = (number of error-free orders / total orders picked) * 100
Order picking time or units per hour (UPH)
This KPI measures the average time it takes to complete the picking process. To find it, the total time spent on picking is divided by the total number of orders that were picked for a time period.
Order picking time = total time spent on picking orders / total number of orders picked
Another version of this KPI is the units picked per hour (UPH) KPI. This divides the number of units picked by the total time spent on picking them and returns the average number of orders picked per hour.
Cost per pick
Finally, cost per pick calculates the average cost associated with picking each item or order. This KPI is useful for understanding the financial impact of the picking process and identifying cost-saving opportunities. Cost per pick can be calculated by dividing the total cost of picking operations (pickers’ labor and picking equipment costs) by the total number of picks for a time period.
Cost per pick = total cost of picking operations / total number of picks
Next to the above KPIs, it might also be smart to combine picking-centric metrics with other fulfillment and inventory management KPIs like travel time, fill rate, turnover rate, etc. For example, tracking order picking time alongside the fulfillment turnaround time metric, which tracks the time it takes to complete the fulfillment process, provides insights into how much time is proportionally spent on picking in the fulfillment process.
Order picking best practices for small manufacturers and distributors
Finally, here are 5 order picking tips to help you boost picking efficiency and usher in more streamlined warehouse management practices.
- Implement a suitable order picking method. Choosing the right picking method is crucial based on your operation size, SKU variety, and order volume. For smaller operations, methods like single order picking or batch picking can be particularly effective. Experimenting with different methods can help identify the most efficient approach for your specific needs, potentially reducing picking time and minimizing errors.
- Track picking efficiency with KPIs. Regularly monitoring key performance indicators such as picking accuracy, orders picked per hour, and order cycle time can provide insights into the efficiency of your picking process. Use these metrics to identify trends, pinpoint inefficiencies, and make informed decisions about how to improve your operations, ensuring continuous improvement in your order fulfillment process.
- Optimize the warehouse and storage area layout. Design your warehouse layout to minimize travel time between frequently picked items and ensure that popular products are easily accessible. Consider implementing zoning or adding strategic picking paths. An optimized layout not only speeds up the picking process but also reduces worker fatigue and enhances safety.
- Invest in warehouse equipment. Invest in quality warehouse equipment such as ergonomic picking carts, forklifts, ladders, or adjustable shelving to enhance the speed and accuracy of your warehousing and picking operations. Also consider technologies like barcode scanners or mobile printers to streamline fulfillment and handling processes further and reduce manual errors.
- Implement a warehouse management system (WMS). A WMS can dramatically improve order picking efficiency by automating many aspects of warehouse management, from inventory tracking to generating optimal picking lists. For small businesses, a cloud-based warehouse management system can be a cost-effective solution, providing the benefits of automation without the need for substantial investments.
MRPeasy offers a powerful warehouse management system that significantly enhances inventory and warehouse efficiency. Designed specifically for small manufacturers and distributors, MRPeasy facilitates detailed tracking of all inventory movements and helps with warehouse organization. Additionally, MRPeasy seamlessly integrates with sales and manufacturing processes, enabling automatic updates to inventory levels and ensuring that materials are efficiently managed across the entire supply chain.
Key takeaways
- Order picking is a warehouse management process of physically collecting goods from inventory to fulfill customer orders. Order picking is distinct from materials handling – a manufacturing process in which raw materials are transported to workstations.
- Increasing order picking efficiency is important for reducing operational costs, improving customer satisfaction, enhancing scalability, and increasing overall inventory management efficiency.
- Tried and tested order picking methods include single order picking, batch picking, cluster picking, zone picking, and wave picking. Each of these is suited to different operational scales and complexities.
- Ways to automate parts of the order picking process include implementing pick-to-light or voice picking systems, conveyor belts, scanner-aided picking systems, etc.
- Tips for increasing order picking efficiency include selecting the most appropriate picking methods, optimizing warehouse layout, investing in proper warehouse equipment, and implementing a warehouse management system (WMS) to streamline operations.
Frequently asked questions
An order picker refers to a worker or a type of warehouse equipment dedicated to collecting products from storage in order to fulfill customer orders. In contexts involving personnel, it’s the staff member responsible for gathering items from the shelves based on the specifics of customer orders. When referring to equipment, it’s specialized machinery designed to navigate warehouse aisles and reach various storage heights efficiently.
Picking involves the process of selecting and gathering the specific items listed in a customer order from the warehouse inventory. This step is crucial in the order fulfillment process, ensuring that all components of the order are accurately collected before packaging and shipping. Picking must be precise to maintain order accuracy and customer satisfaction.
Different order picking methods affect ROI by varying the balance between operational efficiency and labor costs. For example, single order picking is less efficient for high volumes but minimizes errors, while batch or cluster picking enhances ROI by reducing travel time and increasing throughput, ideal for high order volumes. The chosen method should align with the company’s operational scale and order volume to maximize financial benefits.
You might also like Lean Warehouse Management Guide for SMEs