On-Time In-Full (OTIF) – A Complete Guide
On-Time In Full (OTIF) is a supply chain management KPI that measures how accurately orders are fulfilled. Here is why it is important, how to calculate it, and how to improve your OTIF score.
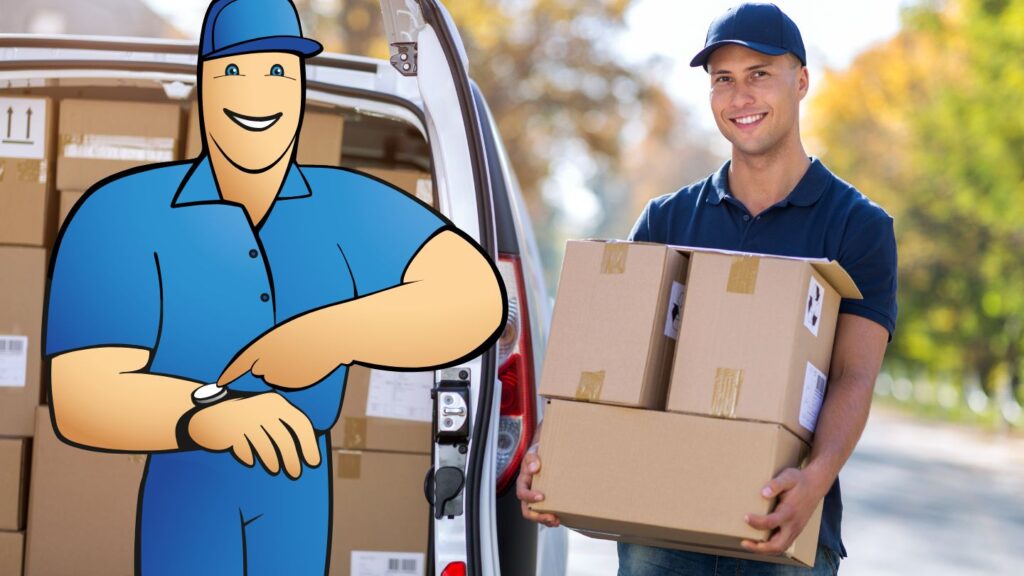
What is OTIF?
On-Time In-Full (OTIF) is a key performance indicator that measures the efficiency and accuracy of supply chain operations. It evaluates how often a company delivers the correct order quantities on the agreed-upon delivery date, thereby meeting customer demand.
OTIF consists of two components:
- On-time deliveries. This refers to the orders delivered to the customer at the right time as scheduled or earlier.
- In-full deliveries. This assesses whether the complete order was delivered without any items missing, as per the customer’s requirements.
OTIF is one of the most important supply chain metrics that can be used to assess both your own delivery accuracy as well as that of suppliers.
Key benefits of OTIF
The OTIF KPI is a comprehensive measure that impacts almost every facet of supply chain management. Here’s how it can help your company:
- Improves supplier performance. OTIF is an effective metric for assessing how well suppliers adhere to delivery schedules and order accuracy. High OTIF scores indicate reliable suppliers, while low scores may prompt a review of supplier contracts and performance.
- Improves inventory management. Proper implementation of OTIF helps ensure that inventory levels are optimized. By receiving goods on time and in the correct quantities, companies can avoid overstocking or stockouts, allowing for more efficient inventory turnover, and reduced holding costs.
- Reduces supply chain disruptions. OTIF directly addresses potential disruptions in the supply chain by highlighting issues in on-time delivery and in-full delivery. Identifying these issues in a timely manner allows businesses to implement corrective actions without significant delays, thus maintaining the smooth operation of the supply chain.
- Increases customer satisfaction. For manufacturers, distributors, retailers, and e-commerce businesses, the ability to deliver orders accurately and on time is crucial. High OTIF performance often correlates with increased customer satisfaction, as customers are more likely to be happy when they receive what they ordered within the promised timeframe.
- Supports effective order fulfillment. OTIF aids in improving the accuracy and timeliness of order fulfillment. This not only helps in reducing late deliveries but also ensures that customers receive complete orders, which is vital for maintaining trust and loyalty.
- Facilitates better supply chain management. By monitoring OTIF, businesses can identify and address bottlenecks in the supply chain more effectively. This continuous improvement process is essential for staying competitive in the market and meeting consumer demands efficiently.
- Benchmarking and continuous improvement. OTIF serves as a benchmark for measuring the success of supply chain initiatives. Companies can set specific OTIF targets and measure their progress over time, allowing for continuous improvement in supply chain performance.
Businesses that prioritize high OTIF performance are therefore better equipped to meet market demands and maintain a competitive edge.
How to calculate the OTIF rate?
Calculating the OTIF rate involves assessing the proportion of deliveries that are both on time and complete. Here is a detailed breakdown of how to calculate the OTIF rate.
- Define the delivery window. The delivery window is the agreed-upon time frame between a supplier and a customer for when goods should be delivered. This lead time is crucial for determining whether a delivery is considered “on-time.”
- Identify relevant deliveries. Compile data on all deliveries made within a specific period. This dataset should include the delivery date, the quantity of items ordered, and the quantity actually delivered.
- Count the deliveries made on time and in full. Count the number of deliveries that arrived within the specified delivery window and in the agreed-upon quantity.
- Calculate OTIF. The metric is calculated by dividing the number of orders delivered on time in full by the number of total deliveries.
The OTIF rate formula is therefore:
OTIF = On-time-in-full deliveries / Total deliveries
Example
Assume you have the following delivery data for a month:
Total deliveries: 100
On-time-in-full deliveries: 90
OTIF = 90 / 100 = 0.9 = 90%
What is a good OTIF score?
Good OTIF scores are those that meet or exceed industry benchmarks and company-specific targets. While a perfect OTIF score is 100%, meaning every order is delivered on time and in full, this level of performance is challenging to achieve consistently due to various uncertainties in supply chain dynamics. However, an OTIF score around 95% to 99% is often considered excellent in many industries. Such high scores indicate a highly efficient supply chain with effective optimization strategies in place, leading to high customer satisfaction and operational excellence.
A bad OTIF score, on the other hand, typically falls below 85%. Such scores may indicate significant issues within the supply chain, including poor supplier reliability, warehouse management problems, or ineffective supply chain strategies. Low OTIF scores can lead to customer dissatisfaction, increased operational costs, and potential loss of business and profitability as customers seek more reliable vendors.
Possible root causes of low OTIF scores
A low On-Time In-Full (OTIF) score can significantly impact a business’s ability to meet customer expectations and maintain efficient operations. Identifying the root causes of a low OTIF is crucial for implementing effective corrective measures. Here is a closer look at the potential factors contributing to underperformance in OTIF metrics.
Supplier-related issues
Poor supplier performance
If suppliers consistently fail to deliver goods on time or ship incorrect quantities or items, it will directly impact the OTIF score.
Ineffective communication
Lack of clear and timely communication between suppliers and the purchasing company can lead to misunderstandings about order specifications or changes in order requirements.
Logistics and transportation problems
Inefficient routing
Suboptimal transportation routes or logistic strategies can cause delays in delivery times.
Carrier issues
Problems with transportation providers, such as capacity constraints, operational delays, or errors, can prevent on-time delivery.
Customs and import delays
For international shipments, delays in customs can hinder the timely arrival of goods, especially if there is incomplete or incorrect paperwork.
Internal process inefficiencies
Inventory management shortfalls
Inaccurate inventory records or poor warehousing practices can result in being unable to fulfill orders fully from available stock.
Production delays
In manufacturing contexts, delays in production due to equipment malfunctions, workforce issues, or supply chain bottlenecks can prevent orders from being completed on time.
Order processing errors
Mistakes in order handling, from incorrect data entry to delays in processing customer orders, can lead to wrong or delayed shipments.
Demand forecasting and planning issues
Inaccurate demand forecasting
Poor forecasting of customer demand can lead to either inventory surplus or shortage, affecting the ability to fulfill orders promptly and completely.
Lack of flexibility in supply chain
Inability to adapt to sudden changes in market demand or supply chain disruptions can severely impact OTIF performance.
External factors
Market volatility
Fluctuations in the market can affect supply and demand unpredictably, impacting the availability of materials and final products.
Regulatory changes
New regulations or changes in existing laws can alter shipping routes, import and export conditions, or product specifications, leading to delivery delays or failures.
Natural disasters and pandemics
Events like hurricanes, earthquakes, or health crises can disrupt normal operations along the entire supply chain, from production to delivery.
How to optimize your OTIF score?
Optimizing your On-Time In-Full performance involves improving various facets of the supply chain and logistics processes. Achieving a high OTIF score not only requires real-time visibility into supply chain operations but also coordinated efforts among all stakeholders, including suppliers, shippers, and distribution centers. Here’s how businesses can streamline these processes and improve their OTIF scores:
- Strengthen supplier collaboration. Develop strong relationships with suppliers to ensure they understand and align with your OTIF goals. Regular reviews and feedback can help maintain high performance standards. Use supplier management best practices such as supplier scorecards.
- Improve forecasting and inventory management. Utilize historical data to predict demand more accurately and manage inventory levels to prevent overstocking or stockouts.
- Streamline logistics operations. Optimize routing and scheduling to improve the efficiency of transport operations. This involves working closely with shippers and logistics providers to minimize delays and maximize load efficiency.
- Implement real-time tracking. Deploy systems that offer real-time tracking of shipments, such as MRP software. This allows for proactive management of any potential delays or issues in the supply chain.
- Focus on continuous improvement. Regularly analyze OTIF performance data to identify trends and areas for improvement. Implement corrective actions based on these insights to continually improve supply chain processes.
As hinted above, the OTIF score can be significantly improved by adopting a software system that would integrate sales, purchases, inventory, production, and shipping.
The role of MRP software in optimizing OTIF
Modern Manufacturing Resource Planning (MRP) or Enterprise Resource Planning (ERP) systems are crucial tools for improving OTIF performance. These systems provide several functionalities that can significantly benefit the supply chain:
- Real-time visibility. MRP/ERP systems offer real-time visibility into all critical aspects of the supply chain, from production planning and inventory levels to the status of deliveries. This visibility is essential for making informed decisions quickly.
- Integrated information systems. By integrating various functions such as inventory management, order processing, and procurement, MRP/ERP systems ensure that all relevant stakeholders have access to the same information, facilitating better coordination and faster response times.
- Automated workflows. Automation of routine tasks helps reduce the risk of errors and speeds up processes across the supply chain, including procurement, manufacturing, and distribution.
- Improved demand planning. MRP/ERP software strengthens demand planning capabilities by analyzing historical data, helping you forecast future demand more accurately. This leads to better alignment of production schedules with customer needs.
As a result of implementing the system, MRPeasy’s clients achieve a 39% increase in on-time deliveries on average.
Key takeaways
- On-Time In-Full (OTIF) is a crucial supply chain management KPI that measures the accuracy and efficiency of order fulfillment by assessing both on-time deliveries and in-full deliveries.
- The metric is calculated by dividing the number of orders delivered on time in full by the number of total deliveries.
- A good OTIF score typically ranges from 95% to 99%, reflecting high supply chain efficiency and customer satisfaction. Conversely, a score below 85% is considered poor, indicating significant supply chain issues such as supplier unreliability or logistical inefficiencies.
- Low OTIF scores can stem from various issues, including poor supplier performance, logistical errors, inefficient inventory management, and inadequate demand forecasting. External factors like market volatility and regulatory changes can also adversely affect OTIF performance.
- Improving OTIF involves strengthening supplier collaboration, improving demand forecasting and inventory management, streamlining logistics operations, and utilizing real-time tracking systems. Continuous improvement practices are crucial for maintaining a good OTIF performance over time.
Frequently asked questions
To set realistic OTIF targets, companies should analyze historical performance data, consider industry benchmarks, and assess their own operational capabilities. Aligning these targets with customer expectations and the specific logistical challenges of their industry or product types also helps ensure that the goals are attainable and relevant.
Companies using MRP or ERP systems have found that real-time visibility into inventory levels and shipment status allows them to proactively manage supply chain disruptions and adjust plans swiftly, significantly reducing instances of late or incomplete deliveries. For example, a manufacturer may use real-time data to anticipate a shortage in raw materials and promptly reorder, ensuring production schedules remain unaffected.
Small businesses can improve their OTIF performance by using software to monitor supplier reliability, streamline their inventory management, and maintain clear communication channels with all supply chain stakeholders.
You may also like: 11 Most Important Inventory Management KPIs in 2024