Case Study: Utility Meters Warehouse and Libra Europe Consulting
Our partner – Authorized Consultant – Libra Europe Consulting Ltd helped Utility Meters Warehouse Limited to realize its ERP system project with MRPeasy and Xero
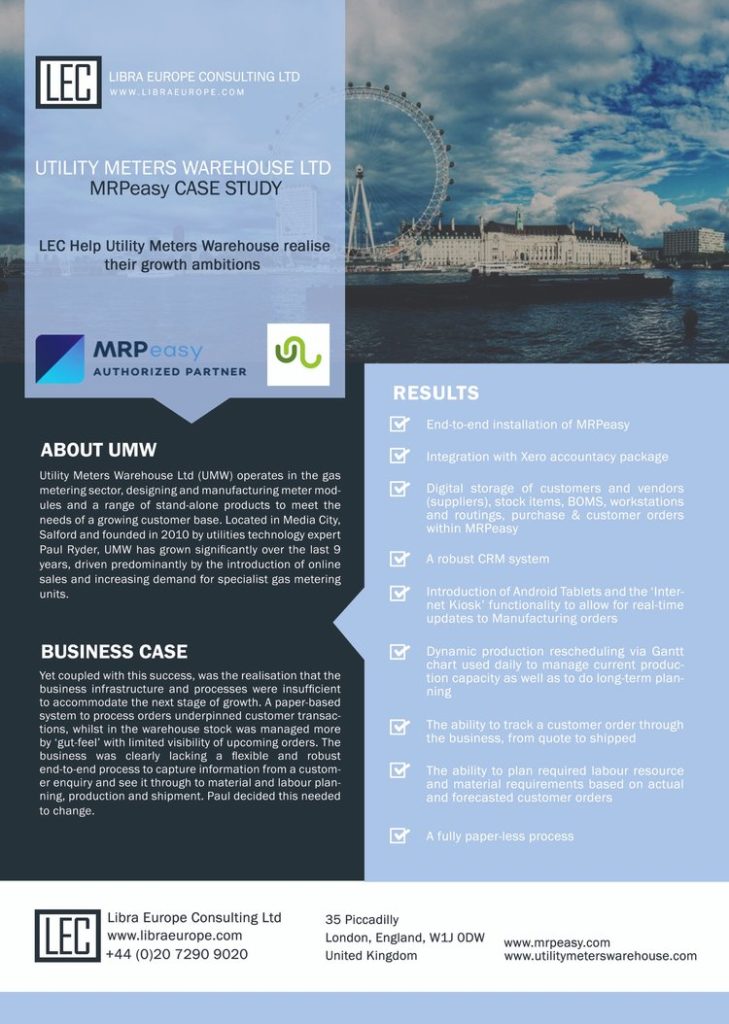
Utility Meters Warehouse Ltd (UMW) operates in the gas metering sector, designing and manufacturing meter modules and a range of stand-alone products to meet the needs of a growing customer base. Located in Media City, Salford and founded in 2010 by utilities technology expert Paul Ryder, UMW has grown significantly over the last 9 years, driven predominantly by the introduction of online sales and increasing demand for specialist gas metering units.
Business case
Yet coupled with this success, was the realisation that the business infrastructure and processes were insufficient to accommodate the next stage of growth. A paper-based system to process orders underpinned customer transactions, whilst in the warehouse stock was managed more by ‘gut-feel’ with limited visibility of upcoming orders. The business was clearly lacking a flexible and robust end-to-end process to capture information from a customer enquiry and see it through to material and labour planning, production and shipment. Paul decided this needed to change.
Approach
After researching ‘Material Requirement Planning’ and ‘Customer Relation Management’, Paul found MRPeasy. He liked the functionality and how easy and user-friendly the interfaces looked. Believing UMW could benefit from this solution, Paul contacted Libra Europe Consulting, one of MRPeasy’s UK implementation consultant teams, who were happy to help.
Libra Europe met Paul and his team during December 2018. Paul explained the challenges and limitations he thought the business had with its current processes and had plenty of questions around how MRPeasy could change this. Both parties agreed that MRPeasy would greatly improve current processes, as long as the culture and behaviour within the business accepted these changes and worked in synergy.
Working with the UMW team, Libra Europe started the implementation project by mapping out their current business processes and inviting the UMW team to critique them. The aim was to highlight key bottlenecks, duplication of work, restriction of current functionality and where they could potentially replace paper-based processes. The work demonstrated a lack of visibility around production planning and procurement, which had an impact on delivery times and being able to create stocked items. The paper-based system also meant there was a high risk of information being misplaced.
From this work, Libra Europe gained an understanding of the issues, the functionality requirements and where MRPeasy could help. A new ‘future state’ end-to-end process was mapped using the workflow of MRPeasy and the required functionality identified.
The UMW team were amazed that their business processes could be simplified significantly as well as gaining improved visibility of orders. Once seeing the potential, UMW agreed to a full implementation of MRPeasy.
Results
In just a few weeks, MRPeasy has been successfully implemented into the UMW business.
Key features of the implementation have been:
• End-to-end installation of MRPeasy
• Integration with a Xero accountancy package
• Digital storage of customers and vendors (suppliers), stock items, BOMS, workstations and routings, purchase & customer orders within MRPeasy that allow easy access to maintain and update
• A robust CRM system where contact details, last contact date and previous orders can all be stored and viewed quickly
• Introduction of Android Tablets in line with using the ‘Internet Kiosk’ functionality to allow for real-time updates to Manufacturing orders. This also enables workers on the shop floor to get access to documentation, utilising Dropbox and document attachment functionality within MRPeasy.
• Dynamic production rescheduling via Gantt chart used daily to manage current production capacity as well as to do long-term planning
• The ability to track a customer order through the business, from quote to shipped status
• The ability to plan required labour resource based on actual and forecasted customer orders
• The ability to plan material requirements based on actual and forecasted customer orders
• A fully paper-less process
Libra Europe revisited UMW a month after implementation to get feedback from the team:
“MRPeasy allows us to track our manufacturing costs and sales with ease. We are very happy with the product as it saves our employees a lot of time. It helped us to get rid of a lot of paperwork and it syncs very well with our previous accounting system ‘Xero’. We initially thought the transition would be tough, but with the help from Libra, it turned out to be a smooth process”
PAUL RYDER – MD, UTILITY METERS WAREHOUSE LTD