Stock Replenishment – Top Tips for Small Manufacturers
Inventory control, inventory optimization, inventory management – are they all just other words for stock replenishment? In a way, yes, but also, not at all! Let’s find out the difference.
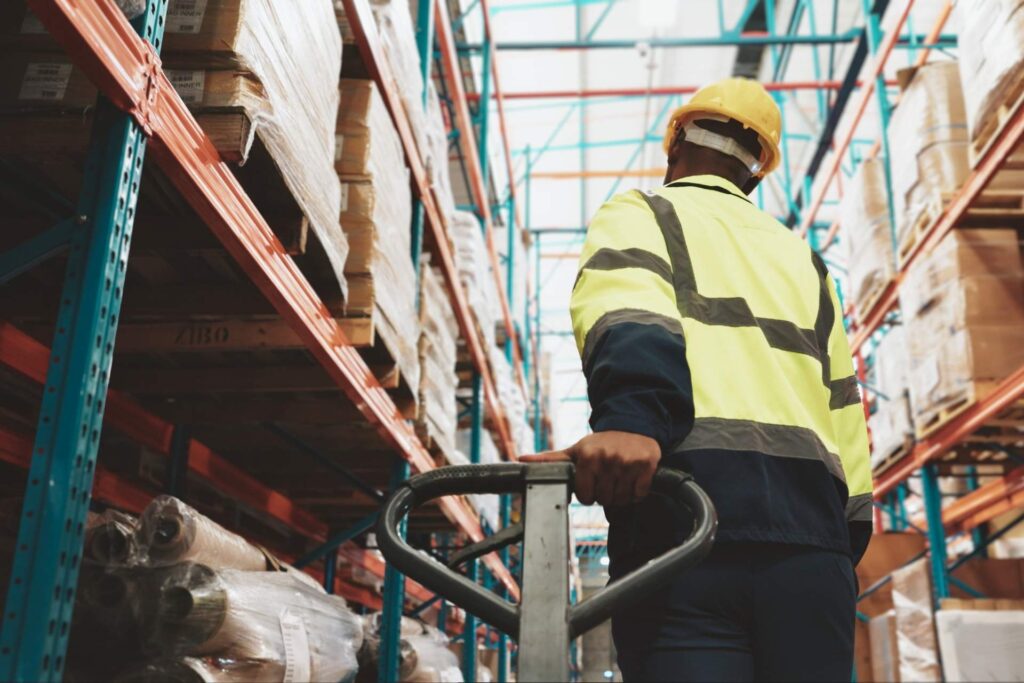
You can also listen to this article:
What is stock replenishment?
Stock replenishment, or inventory replenishment, is the process of monitoring inventory usage and conducting procurement to ensure the right stock levels and timely order fulfillment. Replenishment is a central aspect of stock control – an inventory management concept that balances financial liquidity with sufficient stock.
Manufacturers and distributors prefer to keep stock as low as possible to avoid excessive holding costs and reduce overstocking risks, yet high enough to ensure timely fulfillment. Finding this “ideal level of inventory” is the task of inventory optimization, which focuses on demand forecasting, analyzing historical consumption rates, and monitoring supply chain performance.
Stock replenishment is the operational mechanism for maintaining this balance.
Effective stock replenishment hinges on three key areas:
- Procurement. This is the most important facet of inventory replenishment. Effective procurement involves monitoring supplier relationships and performance, managing delivery lead times, and maintaining good purchasing practices. Procurement is equally essential for manufacturers restocking raw materials as it is for distributors stocking finished goods for resale.
- Inventory and production tracking: Timely and accurate replenishment can only be possible through an up-to-date overview of actual stock levels and, therefore, also of consumption rates. Robust traceability systems are essential for maintaining records, whether as dedicated inventory tracking software or more advanced MRP systems that keep tabs on the whole manufacturing process, inventory included.
- Warehouse management: In addition to ordering and keeping the right amount of goods in stock, inventory items must be received and stored appropriately. They need to be kept in the right conditions and be organized for quick accessibility for picking and transport.
The importance of timely stock replenishment
As you might imagine, replenishment is crucial to get right. Excess inventory can quickly spiral into crippling cash flow issues while stockouts hurt your ability to sell product and keep to promised lead times, reducing customer satisfaction and reputation.
Here are four main reasons why well-managed stock replenishment is important.
Optimized cash flow
Stocking only the required items means excess capital isn’t tied up in surplus inventory. Thought-out replenishment helps avoid over-ordering and stockpiling, thus controlling inventory costs and freeing up cash for other strategic investments like equipment upgrades, product development, or expanding sales channels.
Conversely, delays in replenishment can lead to last-minute purchases at premium prices or emergency production runs, which also strain financial resources. An optimized replenishment process smooths out purchasing cycles, making cash flow more predictable and manageable.
Maximized profitability
Timely replenishment also directly affects profitability. Namely, overstocking often leads to markdowns and wastage (especially for perishable goods) and unavoidably hikes up storage costs. By aligning stock levels closely with actual demand, businesses can improve their profit margins by reducing unnecessary expenses.
Furthermore, a good handle on critical raw materials makes production lead times more predictable for high-demand items. This reduces lost sales opportunities and boosts revenue, making replenishment a direct contributor to profitability.
Timely production schedules
In manufacturing, materials must be available exactly when needed to avoid idle time and missing deadlines. A robust replenishment process ensures that components and raw materials are restocked in sync with production planning to create uninterrupted workflows.
Delays in replenishment can quickly cascade into bottlenecks and production downtime. More than hindering your financial performance, this impacts the entire supply chain. Consistent material availability enables manufacturers to respond faster to changes in demand.
Customer satisfaction
Stockouts and backorders don’t just hurt revenue. The real threat is eroding customer trust and loyalty. Without efficient replenishment, customers experience more frequent delays and can’t rely on the business to deliver as promised. This leads to lower satisfaction and less repeat business.
A well-controlled replenishment process helps to respond faster to trends or seasonal demand spikes, ensuring that popular products can be finished quickly and remain in stock. Agility is a competitive edge for small manufacturers. One that helps strengthen your brand’s reputation and meet customer expectations.
The inventory replenishment process
Any company that sells or produces physical goods depends on inventory for its livelihood. But maximizing inventory profitability is a tad more complex than simply buying when there’s a deficit and selling off excess.
For example, to avoid extra storage costs, stock should be available no sooner than there is actual demand for it. This means delivery lead times need to be taken into account. Order quantities also need to be considered, balancing bulk purchase discounts with excess stock. And in the case of perishables, shelf life becomes a crucial factor.
Good replenishment planning depends as much on good inventory and forecast data as it does on supplier management and reliable production practices.
Stock replenishment workflow
What effective replenishment looks like for you depends on your specific production setup, product lifecycle, market considerations, and even warehousing protocols. But here’s a look at the core components of a basic stock replenishment system.
- Inventory level monitoring.
In addition to knowing what should be in stock, you need to know what actually is. Consistent tracking of usage and depletion rates ensures that stock levels are always up to date, incoming and work in process (WIP) inventory are accounted for, and any discrepancies are detected early. Inventory tracking also informs demand forecasting by providing insight into historical consumption data, revealing changing trends, seasonality, or anomalies. - Accurate demand forecasting.
Forecasting demand means knowing which materials will be required, for what, and when. Analyzing sales data, seasonal trends, and market shifts enables the anticipation of future demand more accurately. Forecasting is critical for manufacturers that produce goods to stock, but make-to-order production companies can benefit from demand predictions, too. - Reorder points.
The reorder point (ROP) is the stock level at which a new order should be placed. It accounts for an item’s average utilization, lead time, and safety stock—a buffer often placed on critical items to prevent stockouts during delays or demand spikes. Incorporating economic order quantity (EOQ) into the mix further helps determine the most cost-effective order size to minimize ordering and holding costs. - Integrated procurement and production management.
Procurement involves more than sending out order requests to vendors. It’s about building strong supplier relationships and monitoring their performance, maintaining accurate lead time data, and handling the creation, tracking, and processing of purchase orders to ensure that purchasing activities are documented and coordinated. Procurement should be closely integrated with the overall inventory and production planning system to increase replenishment efficiency. - Optimized warehouse.
The replenishment process is only as efficient as the warehouse that supports it. Stock should be stored in accessible locations and optimized for picking, handling, and cycle counting. An optimized warehouse layout will reduce picking times and minimize inventory mishandling.
Types of inventory replenishment strategies
Here are three inventory replenishment methods commonly used by small manufacturers.
As you will see, analyzing and forecasting your demand patterns is inescapable, whichever method or combination of methods you choose.
1. Reorder point (ROP) replenishment
This replenishment strategy triggers restocking when inventory levels drop to a predefined threshold based on real-time tracking of stock usage and lead times. The reorder point is calculated by analyzing average customer demand and supplier lead times, with added safety stock to account for fluctuations. The ROP method is especially effective when customer orders follow relatively stable patterns.
Read more about the reorder point.
2. Periodic replenishment
With periodic replenishment, stock levels are reviewed at fixed intervals, such as once a day, weekly, or monthly, and replenished to meet forecasted customer demand until the next review. Although this method simplifies inventory planning and order batching, it relies heavily on accurate forecasts. As such, it’s not the most responsive stocking practice to sudden demand surges.
3. Just-in-time (JIT) inventory
As the name implies, JIT aims to keep the amount of inventory minimal by replenishing it only when there is actual customer demand—often triggered directly by customer orders. This on-demand replenishment strategy minimizes storage costs and helps free up capital, but requires highly reliable suppliers but also precise forecasting to work best. It’s thus ideal for manufacturers with stable demand and mature supply chains, but may not suit environments with high variability or fluctuating lead times.
5 top tips for effective stock replenishment
Replenishment might seem straightforward at a glance, but doing it effectively to optimize your profitability takes coordination, planning, and the right tools. Here are five key tips to help you build a resilient and efficient replenishment process.
1. Increase your forecasting accuracy
Understanding seasonality and customer order patterns through analyzing historical sales and supply data enables you to predict future needs and time your stock movements much better. The more reliable your forecasts, the more confidently you can minimize stock levels without risking shortages. It also enables leveraging advanced stocking techniques like economic order quantity more confidently.
Aside from make-to-stock operations, for whom demand forecasting is critical, make-to-order manufacturers benefit from forecasting too, when planning capacity and managing long-lead-time components. Pairing forecasting with real-time inventory visibility gives you a powerful decision-making tool for proactive stock control.
2. Assess supplier performance and keep good vendor relationships
Suppliers can make or break your replenishment process. Evaluate supplier performance on metrics like delivery reliability, lead time accuracy, quality, and responsiveness. Then use that data to guide your purchasing decisions. This helps prevent costly disruptions and enables you to keep tabs on how well vendors are meeting your expectations.
Strong supplier relationships are as important as their performance. Open, consistent communication builds trust and gives you more flexibility when you need it most, whether it’s a last-minute order or quickly adjusting delivery timelines.
Read more about supplier performance management and supplier relationship management to build a robust procurement strategy.
3. Enhance your supply chain visibility and production tracking
Inventory management encompasses far more than just the stuff you’re holding. A clear view of your entire supply chain is vital for accurate planning. When you can see upstream constraints, potential delays, and real-time stock levels, your forecasts improve, bringing responsiveness to changing customer demand.
On the other end of the pipeline, a good overview of production processes is required to ensure that what’s being made aligns with what’s being consumed. Tracking material usage, WIP, and output in real time will keep your inventory decisions grounded in actual manufacturing activities. This minimizes mismatches between production and what’s needed.
4. Automate inventory and warehouse processes
Manual tracking quickly becomes a bottleneck as operations grow. Automating your inventory and warehouse processes helps reduce human error, saves time, and ensures real-time data accuracy.
Implement barcode systems for fast, reliable SKU (stock keeping unit) identification and tracking. Give floor workers easy access points through tablets or access terminals to report inventory movement as soon as goods are received, picked, or consumed in production. This reduces blind spots and increases the stockroom’s efficiency.
5. Invest in inventory management software
Spreadsheets or paper-based systems won’t cut it in a growing business. A good inventory management system ties your replenishment activities together, giving you visibility into stock levels, reorder points, and lead times, all in one place.
Depending on your needs, different solutions provide different levels of stock control. For example, basic software might only help flag out-of-stock items or track SKUs via a barcode integration. More advanced solutions introduce expanded aspects of inventory management, from order management and write-offs to integrations with e-commerce apps.
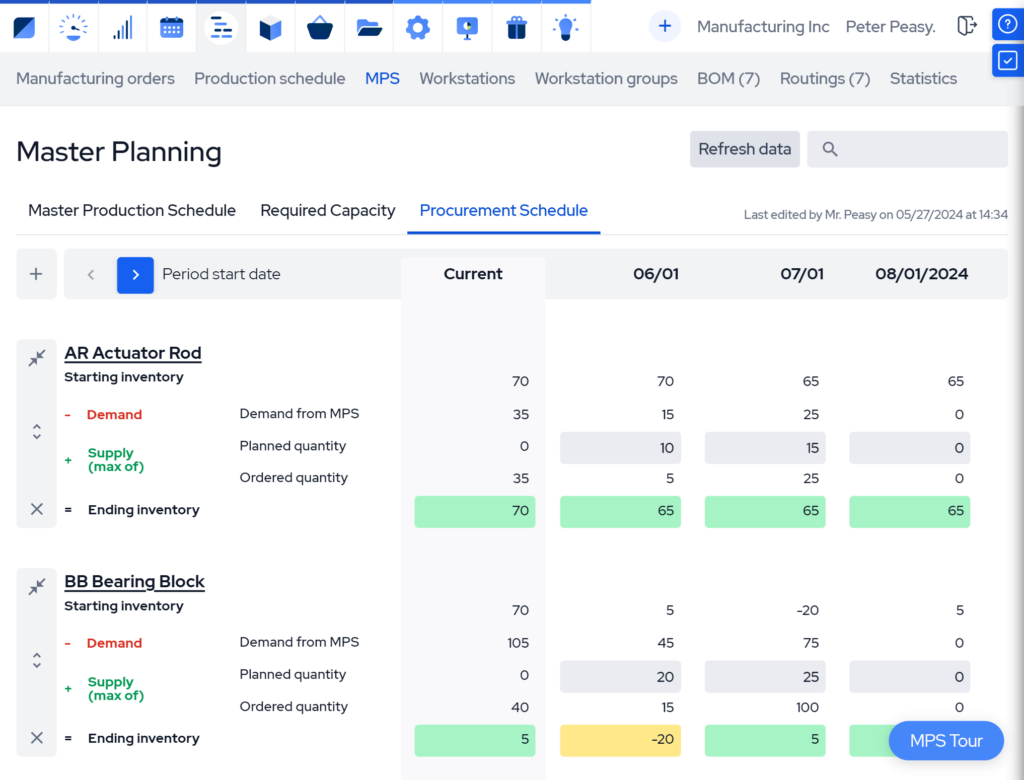
Simplify stock replenishment with manufacturing ERP software
Advanced manufacturing ERPs go ten steps beyond simple stock management systems for even greater control. This is achieved by integrating order management, sales, inventory and warehouse control, forecasting, production planning, cost tracking, and many other features into a single platform.
While they require some upfront investment, modern cloud-based solutions are easy to implement and use. Designed specifically for SMEs, they ensure a healthy return on investment by boosting operational efficiency and driving business growth.
MRPeasy gives small manufacturers access to powerful tools that support every aspect of the stock replenishment process, from forecasting demand and tracking material consumption to managing purchase orders and monitoring supplier performance. Real-time inventory visibility means you always know what’s in stock, what’s on order, and what’s needed next. Its integrated procurement and production modules ensure that raw materials are ordered in sync with production schedules, while warehouse management features like barcode scanning, quality control, and labeling help keep the stockroom organized.
Key takeaways
- Stock replenishment is the process of restocking inventory to maintain optimal levels for order fulfillment. It ensures that materials and products are available at the right time, avoiding overstocking or tying up excess capital.
- Accurate demand forecasting and real-time inventory tracking are essential for effective replenishment. They help reduce shortages, minimize excess stock, and align purchases with actual customer demand.
- Supplier performance and strong vendor relationships directly impact replenishment success. Reliable lead times and open communication reduce disruptions and improve delivery consistency.
- Key stock replenishment methods include utilizing reorder points and economic order quantities, periodic replenishment, or implementing just-in-time inventory practices.
- Manufacturing ERP systems integrate inventory, procurement, and production management. This enables a data-driven replenishment process to meet demand more effectively, boosting growth and profitability.
Frequently asked questions (FAQ)
Replenishment is the reordering of raw materials or finished goods when their stock drops below a certain level. For instance, a furniture manufacturer might restock planks and screws once inventory hits a predefined reorder point (ROP) to avoid production delays.
Replenishment should occur when inventory levels reach a predefined reorder point, at regular review intervals, or when there is actual demand for items in the case of make-to-order manufacturing. The timing depends on factors like customer demand, supplier lead times, and the item’s importance for production or sales.
Common stock replenishment methods include reorder point (ROP) replenishment, periodic replenishment, and just-in-time (JIT) replenishment. Each method helps maintain inventory levels based on either demand forecasts, review cycles, or actual customer orders.
You might also like: 11 Most Important Inventory Management KPIs in 2025