Traceability in Manufacturing – A Comprehensive Guide for SMEs
Manufacturing traceability isn’t just a fancy catchword. It’s the mark of quality, compliance, and competitiveness for shops of all sizes. Find out what traceability really means for smaller manufacturers, learn how it protects your production process, and discover practical ways to implement it without blowing your budget.
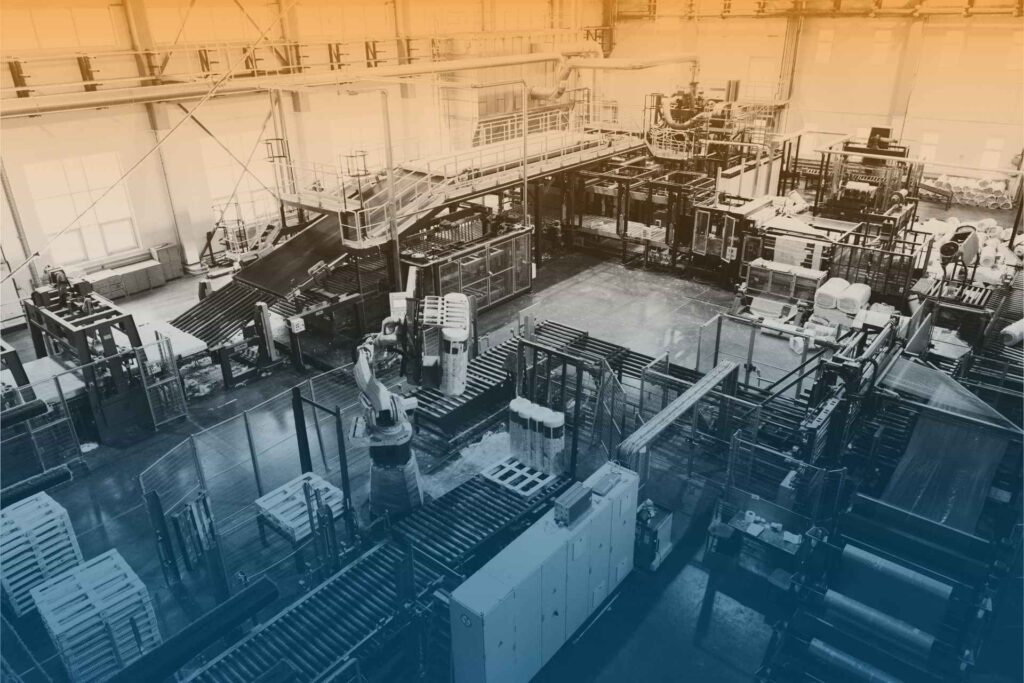
You can also listen to this article:
What is manufacturing traceability?
Manufacturing traceability is simply your ability to track the history of everything that happens to your products—from raw materials coming through the receiving dock to finished goods heading out to customers, maintaining a detailed history of every aspect of a product’s lifecycle.
Think of it as creating a permanent digital fingerprint that follows materials and components through every stage of production.
Good traceability captures the complete story of your manufacturing process. It answers critical questions like:
- Who supplied the materials?
- When did the materials arrive?
- Which workstation processed the materials?
- Who operated that equipment?
- Did it pass the quality inspection?
- When did it ship out, and where did it go?
All this information gets linked directly to physical items—whether individual parts, batches, or complete assemblies.
But effective traceability isn’t just about checking regulatory boxes. It fundamentally shifts your operation from “find and fix” to “prevent and improve.”
What was once a paperwork burden becomes a powerful decision-making tool. You’ll spot bottlenecks, identify waste, and catch quality issues before they become expensive problems.
That’s why forward-thinking shops see traceability not as overhead, but as a competitive edge that protects both quality and profits.
Types of traceability in manufacturing
Every shop floor has different tracking needs. Let’s cut through the jargon and look at how traceability actually works in the real world.
Directional traceability
Forward traceability looks ahead—tracking where your products go after leaving your facility for distributor shelves. This helps manage recalls and verify proper delivery. Backward traceability looks behind, tracing components back to their sources when problems emerge. Most modern shops combine these into bidirectional systems that connect the dots in both directions, giving you the complete picture from supplier to customer.
Scope-based traceability
This focuses on where tracking happens. Internal traceability stays within your facility, documenting every movement from receiving to shipping. When you need to track beyond your shop floor, external traceability follows parts through your entire supply network. The gold standard? End-to-end traceability that connects everything from raw material sources to customer doorsteps. With today’s tangled supply chains, seeing the whole picture matters more than ever.
Granularity-based traceability
How detailed should your tracking be? Material traceability focuses on specific raw materials and their journey. Batch traceability tracks groups of products made together, balancing practical needs with quality control.
Unit traceability assigns unique identifiers to individual products, essential for highly regulated industries or safety-critical parts where each item’s history matters. Your industry, regulations, and product value typically determine which level makes sense for your operation.
Importance and benefits of traceability in manufacturing
Sure, implementing traceability systems requires investment, but the returns go far beyond just checking compliance boxes. The real value comes from transforming what looks like paperwork overhead into a powerful competitive advantage that protects both your quality reputation and bottom line. Here’s why manufacturers of all sizes are making traceability a cornerstone of their operations.
Regulatory compliance
Regulations across many industries have tightened over the last three decades, and there’s no reversing that trend. Meeting requirements from FDA to ISO isn’t optional anymore—it’s your ticket to market access and avoiding penalties that can cripple smaller operations.
The documentation these systems generate creates your audit trail, transforming inspection days from panic-inducing events to straightforward verifications.
Too many shops scramble before audits, digging through paper files and hoping nothing’s missing. Traceability systems eliminate that stress completely.
Product quality and safety
Quality issues caught early cost pennies to fix; discovered later, they cost dollars; found by customers, they cost your reputation.
Traceability connects real-time monitoring with quality processes, allowing you to spot troubles before they cascade through production.
Manufacturers have cut defect rates by 40% simply by using track and trace data to facilitate root cause analysis to identify and address problems at their source. When every component has a history, maintaining consistent adherence to specifications becomes systematic rather than chaotic.
Efficient recall management
No manufacturer wants to think about product recalls, but smart ones plan for them anyway. Without traceability, you’re faced with broad, expensive market withdrawals that damage both finances and reputation.
With proper tracking, you can rapidly pinpoint exactly which products are affected and where they are. Companies have reduced product recall costs by over 80% through targeted action rather than sweeping withdrawals.
The difference comes down to answering one question quickly: “Which specific units contain the affected components?”
Supply chain transparency
Modern supply chains have numerous interconnected components, each representing a potential point of failure. Product traceability has saved manufacturers millions by proving when a supplier sent defective product parts or when a critical component wasn’t what it claimed to be.
The shop floor data doesn’t lie. It exposes those hidden wasteful steps that everyone’s been working around for years. Good traceability shines a light in those dark corners where money gets wasted.
Brand protection and customer trust
Customers are increasingly interested in detailed information about finished product components and origins—and for good reason. Thirty years ago, material sourcing was rarely, if ever, questioned. Today, it’s a primary concern for customers.
Being able to pull up a complete history of every component gives you instant credibility. A medical parts maker landed a huge contract simply because they could prove, on the spot, exactly where their materials came from and how they were processed. Their competitor couldn’t.
That transparency became their best salesperson. Plus, when knockoffs start floating around, you can prove yours is the real deal while your competitors are still scratching their heads. This is crucial for customer satisfaction.
Operational efficiency
The visibility that traceability provides doesn’t just prevent problems. It improves everyday operations. Process bottlenecks that once hid behind tribal knowledge become plainly visible in traceability data.
Waste reduction happens naturally when you can clearly see where materials are being underutilized. And inventory optimization becomes possible when you have accurate, real-time data on consumption patterns.
These systems support lean manufacturing by providing the factual foundation needed for continuous improvement, replacing gut feelings with data-driven decisions.
Risk mitigation
Risk in the manufacturing industry is real, not just theoretical. Good traceability helps manage that risk by documenting every step in your process.
When you have complete records showing exactly what happened during production, you’re in a much stronger position if questions arise about compliance or quality. Traceability helps catch potential issues with incoming materials before they affect your entire production line.
And if something does go wrong, having detailed tracking data means you can respond quickly and precisely. Instead of shutting down operations or recalling everything, you can focus on exactly where the problem occurred.
Key challenges and how to overcome them
No worthwhile shop floor improvement comes without hurdles. I’ve watched companies struggle with traceability implementation, but I’ve also seen smart shops navigate these challenges without breaking the bank. Here’s a rundown of what you’ll face.
Implementation costs
The initial cost estimates can be intimidating for smaller manufacturers. Don’t be discouraged by expensive enterprise-level solutions. Smaller operations typically need more modest systems.
Start small with your high-value products or most problematic processes. Build your ROI case on hard numbers: scrap reduction, quality costs, compliance penalties avoided.
Many shops find that material waste savings alone justify the initial investment. The key? Phase it in. Prove the concept in one area, then expand using the money you’ve already saved.
System complexity
Many fancy systems collect dust because nobody can figure them out. Keep it practical. Your traceability system should fit your actual operation, not some consultant’s ideal world. Focus on integrating with how your people already work.
Shop floor personnel need to understand the system without requiring specialized technical knowledge. And think scaleability—the system that works at your current size might limit your growth down the line. Select a system that meets current needs while accommodating future growth.
Data integration hurdles
This is where most implementation projects encounter their greatest difficulties. You’ve got old equipment, legacy software, or systems that weren’t designed to talk to each other. Start with a simple map of what information lives where. Figure out what absolutely must connect versus what would be nice to have.
Sometimes you need middleware to bridge the gaps and at other times basic data sharing will do. Remember, perfect integration is a fantasy. Aim for “good enough” to start, then improve as you go.
Lack of standardization
Standards overload is real. Food, medical, automotive, and aerospace all have their own requirements, and they don’t always play nice together. Get clear on the must-have standards for your industry. Don’t chase perfect standardization across your entire supply chain as it rarely exists. Instead, focus on making your systems flexible enough to adapt when standards change.
They always do.
Supplier collaboration difficulties
Your traceability chain is only as strong as your weakest supplier or distributor. Good supplier performance management is a crucial component of an effective supply chain.
Getting them on board can be difficult. Start by clearly explaining what you need and why it matters to their business. Set specific data requirements, not vague requests. Your best suppliers will step up. Begin with critical components and key suppliers, then expand. If a supplier can’t meet your needs, you’ve learned something valuable about their operation.
Resistance to change
People make or break traceability projects. Million-dollar systems have failed because nobody addressed the human factor.
Get buy-in from both top-down and bottom-up. Operators often know better than managers what will actually work on the floor.
Training needs to be practical and ongoing, not a one-time slideshow. The most significant mindset shift is getting people to see traceability data as a powerful tool that makes their jobs easier, not just more paperwork for the quality assurance department.
5 steps to implement traceability in manufacturing
Getting traceability right means following a logical path. Bypassing any of these implementation steps can lead to significant problems. Too many shops waste time and money by rushing into implementation without proper groundwork. Here’s how to do it right.
1. Assessment and planning
Start by taking a hard look at what you already have. Map your current processes—don’t assume you know them. Walk the floor, talk to operators, and follow materials from receiving to shipping.
Be brutally honest about gaps in your tracking. Define exactly what you need to achieve. Is it regulatory compliance? Quality improvement? Recall management? Supplier performance?
Set specific, measurable success metrics from the start. “Better traceability” isn’t a goal. “Reducing trace time from 4 hours to 15 minutes” is.
Your plan should include:
- A defined timeline.
- Specific budget.
- List of resource needs.
- Defined responsibility for each aspect of the plan.
Even the best plans will need adjusting once you start implementing, but having that roadmap prevents aimless decision-making.
2. System design
This is where the rubber meets the road. Determine what level of granularity makes sense for your operation: Material level? Batch? Serial number tracking? The right answer depends on your products, processes, and industry requirements. Don’t over-engineer this.
Next, select your identification methods. Barcodes work fine for many applications, while higher-value or safety-critical items might need RFID tags or direct part marking. Design your data capture workflow with the people who’ll actually use it. The perfect system on paper becomes useless if it creates bottlenecks on the floor.
Every data capture point should answer a specific business need, not just collect information for the sake of it.
3. Technology selection
Hardware and software decisions can make or break your traceability project. Start by evaluating what will work in your actual environment. For example, frequent touchscreen interfaces may be impractical in environments where workers must wear protective gloves.
Compatibility with existing systems is crucial. Can your new traceability solution talk to your current MES (Manufacturing Execution System)? If not, the integration costs might blow your budget. Balance capabilities against what you can realistically afford and support. A sophisticated system that breaks down constantly or requires hiring IT staff probably isn’t worth the hassle.
Sometimes, simpler really is better, especially for smaller operations just getting started with formal traceability. This is where cloud-based manufacturing ERP systems with integrated traceability capabilities can be a great cost-efficient solution.
4. Implementation
You’ve got two main approaches: full deployment or phased rollout. For most smaller shops, phased implementation makes more sense. Start with a critical process or product line, prove the concept, work out the bugs, then expand. Testing is non-negotiable—first in a sandbox environment, then with a limited pilot on your actual floor.
Validate everything: Is the barcode system working correctly? Is data flowing where it should? Are reports accurate?
Train your people thoroughly—not just how to use the system, but why each step matters. Document everything, because key personnel with system knowledge may eventually transition to other roles or organizations. Clear procedures for handling exceptions (like unreadable barcodes or system downtimes) prevent minor hiccups from becoming major headaches.
5. Continuous improvement
Launching your traceability system isn’t the finish line; it’s the beginning of a modern manufacturing process. Schedule regular audits to verify that your traceability system is working as intended. Run mock recalls to test how quickly you can track products in real-world scenarios. You’ll always find blind spots you never noticed before.
Watch what’s happening in your industry too. Regulations rarely get simpler—they just pile up. Customer quality demands keep shifting. Technology that seemed cutting-edge last year becomes standard next year.
Your traceability approach needs to flex with all this. Start basic, get good at it, then build from there. The shops that get the most from traceability are the ones that stick with it, learning and tweaking as they go.
Technologies powering manufacturing traceability
The backbone of any good traceability system is the technology that makes it work. Over the last decade, these systems have evolved from paper-based tracking and basic barcodes to sophisticated digital networks that capture and share data in real time. The good news? There are options at every price point and complexity level.
Let’s break down the key technologies that can power traceability efforts, from simple starter systems to comprehensive enterprise solutions.
Identification technologies
Manufacturers need to mark products before they can track them. For shops just starting, barcodes and QR codes are essential tech that won’t break the bank. They can be printed on labels, applied to products, and scanned with regular handheld scanners or even smartphones in a pinch. Many operations start with simple 1D barcode tags and gradually upgrade as needs evolve.
RFID tags become attractive when line-of-sight scanning is impossible or when simultaneous tracking of multiple items is required. RFID technology enables transmitting signals through radio waves to expand stock or production tracking capabilities.
For products that face harsh conditions, Direct Part Marking (DPM) becomes essential. This may be dot peening, laser etching, or similar permanent marking methods applied directly to the metal or plastic. While labels might come off, a properly executed laser mark will remain intact through heat, chemicals, and physical wear throughout the product’s lifecycle.
Data capture systems
Once items are marked, reliable data collection methods are essential throughout production. Companies that integrate their production machinery, inspection equipment, and packaging lines with traceability systems can eliminate thousands of hours of manual data entry.
Data can be accessed or entered through handheld devices or internet-enabled kiosks, gathered using barcodes, RFID systems, or automated integrated sensors. This substantially reduces labor costs and record errors that can compromise traceability and data integrity.
Software platforms
The software component of your traceability system matters tremendously. MES systems manage shop floor activities—tracking work-in-process, workstation performance, and quality data in real-time. ERP systems handle the business side—purchasing, receiving, orders, shipping, returns, etc., with varying degrees of traceability capability.
Many manufacturers have discovered that forcing general-purpose ERP systems not focused on manufacturing to handle specialized traceability can lead to extended customization efforts with mixed results. On the other hand, dedicated traceability software can be a cost-efficient solution for intricate tracking requirements, but it needs to be integrated with your ERP. One option is to look for dedicated manufacturing ERP systems with built-in tracking features.
Data analytics tools
Collecting traceability data only matters if it’s actually used. Modern analytics tools transform raw tracking data into actionable intelligence through dashboards, reports, and alerts. Real-time monitoring capabilities alert staff immediately when processes drift out of specification, allowing corrections before defects occur.
Some ERP/MRP software solutions integrate with data analytics tools like Microsoft BI for informed decision-making capability based on accurate, current information.
The ultimate goal of traceability isn’t simply data collection, but using that information to make informed decisions that prevent defects and eliminate recurring problems.
How manufacturing ERP enhances production visibility
MRP or manufacturing ERP systems might be the traceability tool many manufacturers don’t realize they already have. While most companies think of MRP/ERP strictly for materials planning and production scheduling, these systems actually store most of the critical data needed for effective traceability.
Smaller manufacturers can leverage their existing ERP investment before spending on dedicated traceability software. If a company is already running ERP, understanding how to maximize its tracking capabilities can save significant time and money while meeting many traceability requirements. Here’s how to make the most of existing systems.
Manufacturing ERP’s role in traceability
At its core, manufacturing ERP creates the critical connection between planning and execution, linking what was intended to be made with what was actually produced. Modern MRP/ERP systems track materials from purchase through consumption, maintaining the digital thread between raw materials, work orders, and finished goods.
This visibility extends beyond just inventory counts to include supplier information, receipt dates, and storage locations. These systems already contain much of the data needed for traceability, often requiring just minor adjustments to capture additional tracking details.
For smaller manufacturers, leveraging existing MRP/ERP systems is often the most cost-effective step toward comprehensive traceability, aside from production efficiency gains.
Key ERP features supporting traceability
Certain MRP/ERP capabilities directly support traceability efforts. Bill of Materials (BOM) management precisely documents what goes into each product, creating the foundation for component-level tracking.
Good BOM management tracks revision levels and engineering changes, critical for regulatory compliance. Inventory control and lot tracking functionality assigns and monitors unique identifiers for material batches, enabling supply chain traceability of exactly which materials went into which products.
Production scheduling and documentation features record who made what, when, and under what conditions. Together, these features create the essential data elements required for effective tracking. Organizations should look for ERP systems that make these connections explicit rather than keeping them in separate data silos.
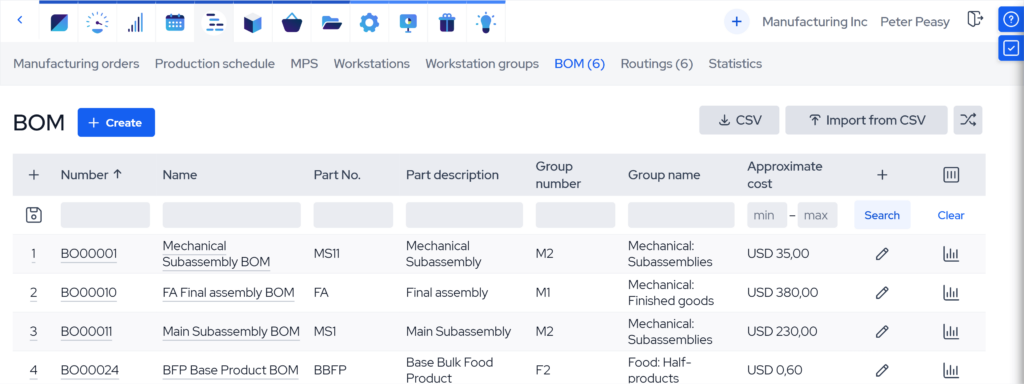
Quality manufacturing ERP software has robust production systems built in that integrate with every aspect of the business, from purchasing and warehousing to manufacturing BOMs and shipping.
Manufacturing ERP systems ensure that financial, purchasing, and customer data align with production records.
Shop floor data collection integration brings in real-time production information from barcode scanners, machine sensors, and operator terminals. Quality management system connections ensure inspection results, deviations, and corrective actions become part of the traceability record.
Many traceability projects fail because data exists but remains trapped in disconnected systems. Integration capabilities should be prioritized. Even simple automated data transfers between systems significantly improve traceability compared to manual reconciliation.
ERP selection considerations for manufacturing SMEs
Smaller manufacturers often walk a tightrope when choosing ERP systems. Avoid getting dazzled by fancy features you’ll never use. Instead, zero in on basics that matter like lot and order tracking, barcoding and serial numbering, production reporting and solid BOM management. These core functions create the foundation for effective traceability without breaking the bank.
Also, think about where your business is headed, not just where it stands today. That bargain system might look attractive now, but if you outgrow it in 18 months, you’ll pay twice. Look for something that can scale alongside your operation for at least 3-5 years.
Don’t overlook the human element either. The best system on paper becomes worthless if your team struggles to use it. Evaluate training needs realistically, check the vendor’s support reputation, and ask pointed questions about their experience with businesses your size. Too many manufacturers have purchased sophisticated systems with capabilities they never used because implementation proved too complex or training too inadequate.
Starting with core functionality that addresses the most pressing compliance and quality needs, then expanding as expertise develops is often the most pragmatic approach. Successful traceability ultimately depends more on process discipline than advanced technology.
Traceability in manufacturing is no longer optional
Industry regulations continue tightening while customers demand proof of quality standards, sustainability, and ethical sourcing. Manufacturers without robust traceability face both competitive disadvantages and significant financial risks. A single unmanaged recall can devastate a small operation. Meanwhile, the operational inefficiencies addressed by traceability (waste, rework, and quality issues) typically exceed the cost of implementing basic systems.
Implementation can be gradual. Start with your highest-risk products and simplest technologies that suit your operation’s scale. Even basic barcode systems deliver substantial benefits when thoughtfully deployed. The future belongs to manufacturers who can leverage modern production tracking software to verify their products’ complete history and. That future is already here.
The only question is whether you’re ready for it.
Key takeaways
- Manufacturing traceability is the ability to track every step of a product’s lifecycle, from raw materials through production to delivery. It ensures visibility, accountability, and control across the entire manufacturing process.
- Traceability helps improve product quality, reduce defects, and manage recalls efficiently by linking materials, equipment, and personnel data to each item produced.
- Different traceability approaches—forward, backward, internal, external, batch, or unit-level—can be applied depending on industry requirements and product risk.
- Technologies such as barcodes, RFID, MRP and ERP systems, and data analytics tools make real-time tracking and process optimization possible even for smaller manufacturers.
- Small manufacturers can start simple by focusing on high-risk products and using existing tools like manufacturing ERP systems, then gradually scale their traceability capabilities as needs grow.
Frequently asked questions (FAQ)
The three main types of traceability in manufacturing are directional, scope-based, and granularity-based. Directional traceability tracks product movement forward to customers or backward to suppliers. Scope-based traceability covers internal (within the facility) or external (across the supply chain) tracking. Granularity-based traceability ranges from raw material and batch tracking to unit-level traceability.
Traceability enhances quality control by linking each product to its materials, processes, and inspections. It helps identify defects early, trace root causes quickly, and ensure consistent adherence to specifications. Manufacturers can reduce waste, prevent recurring issues, and improve customer satisfaction through better process visibility.
Traceability software often integrates with MRP, ERP or MES systems to link production, inventory, and quality data. It connects data from suppliers, shop floor equipment, and inspection points to create a unified product history. This allows for real-time monitoring and accurate reporting. Some manufacturing ERP systems often include capable traceability tools out of the box.
You might also like: Production Routing – Definitions, Tips, and Examples