Standard Costing and Its Alternatives: When and How?
In manufacturing, there are several ways to cost a project or product. One of the earliest methods used was standard costing. While it’s still used today, how does it compare to other costing strategies and should you still use it?
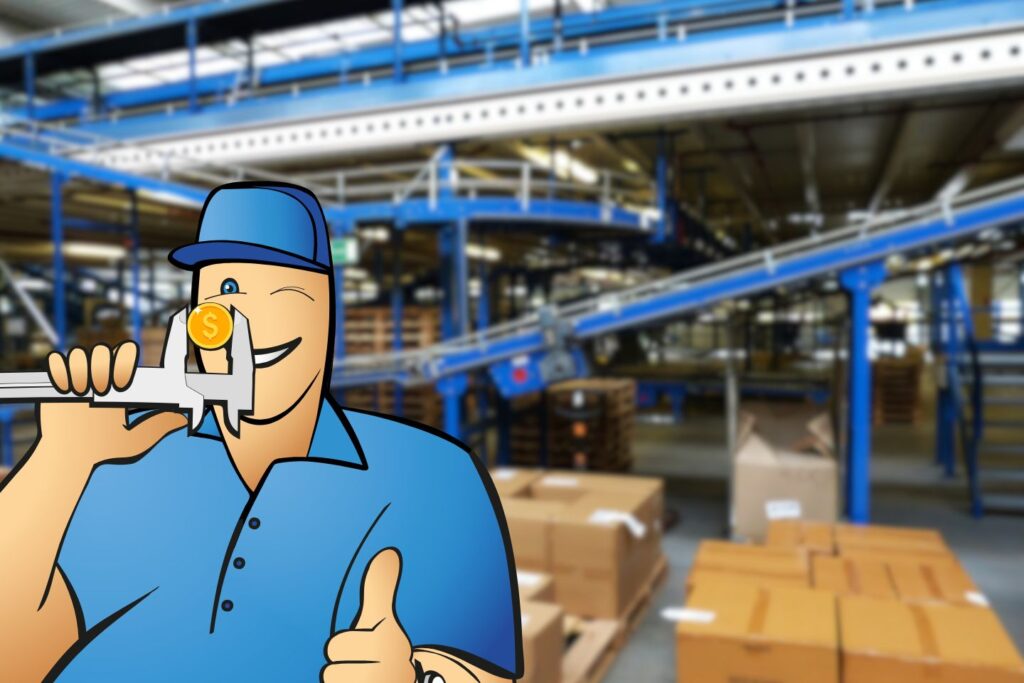
What is standard costing?
Standard costing is a costing method that is essentially like setting the par score for your production process. It establishes what your materials, labor, and overhead should cost before you even start production. Born in the 1920s when factory floors looked vastly different than today, this method gives you a yardstick to measure actual performance against.
Think of it as the difference between planning your route before a road trip versus just tracking the miles as you drive. With standard costing, you map everything out first—what materials should cost, how long tasks should take, what you’ll spend on overhead—then compare reality against those expectations.
These standards aren’t created from thin air. They’re built on historical data, engineering studies, time-motion analyses, and industry benchmarks. Good standard costs reflect what production should reasonably cost under normal operating conditions based on past experience and current market conditions.
A solid standard costing system breaks down into three essential parts:
- Direct materials standards — Predetermined costs for raw materials, covering both price (what you expect to pay per pound, gallon, or unit) and quantity (how much material each product should consume, including normal scrap)
- Direct labor standards — Expectations for worker time and wages, essentially saying: “This welding operation should take 2.5 hours at $28 per hour.”
- Manufacturing overhead standards — Predetermined rates for both fixed costs (the rent paid, whether you make one widget or a thousand) and variable costs (utilities that fluctuate with production volume)
When these components work in harmony, you get a clear picture of what production should cost under normal conditions. This provides practical information that helps with everything from bidding on new jobs to determining if that new production method is actually saving money.
It is important to note, however, that maintaining a standard costing system can be quite resource-heavy and is thereby more suited to larger companies.
Standard costing vs. other types of cost accounting
Let’s break down how standard costing stacks up against other methods without getting lost in the weeds.
Standard costing vs. actual costing
Standard costing uses predetermined benchmarks while actual costing tracks every penny as it’s spent. The difference? Standard costing says, “This should cost $10.42 per unit,” while actual costing meticulously records the costs, e.g. “This batch actually cost $10.67 per unit due to last week’s material price spike.”
Actual costing gives you pinpoint accuracy, especially when costs fluctuate wildly. But it can create an administrative headache when costs are tracked manually—imagine tracking exact costs for thousands of identical items manufactured under slightly different conditions. Standard costing simplifies this by valuating inventory consistently and flagging variances for investigation later.
Standard costing vs. normal costing
Think of normal costing as the compromise candidate. It uses actual costs for direct materials and labor but applies predetermined rates for overhead, based on measures like machine hours or direct labor hours.
While both methods use planned rates somewhere, standard costing applies this approach across the board. Normal costing makes much more sense when your material and labor costs swing but your manufacturing overhead stays relatively steady month to month. If you have a system that tracks costs automatically, however, the accuracy of normal costing always beats out standard costing.
Standard costing vs. activity-based costing (ABC)
Standard costing and ABC represent two different philosophies. Standard costing typically lumps overhead into broad categories and allocates it using simple drivers like labor hours. ABC drills down to identify specific activities driving costs—like machine setups, quality inspections, or purchase orders—and assigns costs based on how much each product consumes these activities.
ABC offers surgical precision for companies making diverse products with complex overhead structures, but it’s like using a micrometer when sometimes a tape measure will do. Standard costing provides straightforward efficiency with much less administrative overhead, making it ideal for simpler operations with homogeneous products.
Standard costing vs. target costing
These approaches tackle the same problem from opposite directions. Standard costing asks, “What should this cost to produce based on our current operations?” Target costing asks, “What must this cost to produce given what customers will pay?”
Target costing starts with the market price, subtracts the desired profit, and works backward to determine the maximum allowable cost. It’s inherently market-driven, while standard costing focuses more on internal efficiency. Target costing thrives in competitive markets where customers dictate prices; standard costing works better in environments where improving operational efficiency is the primary lever for profitability.
Advantages of using standard costing
While some folks claim standard costing is outdated, I’ve seen firsthand how it still delivers significant benefits for manufacturers who implement it properly. Let’s look at the practical advantages that make standard costing worth considering, especially for larger companies running repetitive production processes.
Simplified budgeting and forecasting
Standard costing gives you solid ground to stand on when building budgets. Instead of guessing what things might cost next quarter, you’ve got predetermined figures for materials, labor, and overhead that serve as reliable building blocks for financial planning.
Think about the confidence this gives you when bidding on new jobs or planning a product launch. You don’t have to reinvent the wheel each time you crunch numbers for a new project. Your standards provide a consistent starting point, allowing your team to focus on the variables that truly matter rather than debating what “normal” costs should be.
Efficient inventory valuation
Ask any controller what they dread most about month-end close in a manufacturing environment, and inventory valuation will likely top the list. Standard costing transforms this headache into a manageable process.
Instead of tracking exact costs for thousands of identical items manufactured under slightly different conditions, standard costing values inventory consistently throughout the period. This cuts days off the closing process in many companies and satisfies GAAP (Generally Accepted Accounting Principles) requirements for external reporting. The accounting team can focus on analyzing results rather than spending endless hours calculating inventory values.
Performance evaluation and benchmarking
Standard costing creates clear scorecards for your production departments. When everyone knows what “par” is supposed to be, it’s much easier to identify where inefficiencies happen.
These standards become the baseline for measuring efficiency. When the welding department consistently beats labor standards while the painting department regularly misses theirs, you’ve got objective data to guide where training, process improvements, or other interventions might be needed. No more relying on gut feelings about which areas need attention.
Cost control through variance analysis
The real power of standard costing shows up in variance analysis. For instance, if material usage climbs 15% above the standard in a product line, variance analysis can reveal that issue well before quarterly financials would. This gives you a chance to investigate and fix the root cause earlier, whether it’s due to a supplier quality slip, machine calibration drift, or a training shortfall.
Simplified decision-making
Standard costing creates a common language for discussing costs across your organization. When the sales team wants to offer a special price to a key customer, they can quickly reference standard costs to understand margin implications.
The system also streamlines make-or-buy analyses by giving you reliable in-house cost estimates to compare against supplier quotes. This consistency brings clarity to decisions throughout the organization, from daily operational choices to strategic planning discussions.
Disadvantages of using standard costing
Let’s be honest — standard costing isn’t perfect for every situation. Here are the key drawbacks I’ve observed over my career that you should weigh against the benefits.
Potential for outdated standards
Standards can quickly become obsolete, especially in volatile markets or rapidly evolving industries. When material prices fluctuate wildly or production methods change, your carefully calculated standards become about as useful as last year’s calendar.
Updating standards requires significant effort—collecting market data, conducting time studies, and revising accounting systems, which many companies struggle to prioritize. When standards drift too far from reality, the resulting variance reports become meaningless noise rather than actionable intelligence.
Not ideal for custom or non-repetitive manufacturing
If you’re making one-of-a-kind products or small custom batches, standard costing can be more trouble than it’s worth. The effort needed to establish standards for each unique item often exceeds any potential benefit.
Job costing or actual costing typically makes more sense in these environments. Standard costing shines in repetitive production where patterns emerge over time, not in shops where every day brings entirely different challenges.
Possible negative behavioral impacts
When standards become performance targets, workers sometimes game the system. I’ve seen operations managers delay preventive maintenance to avoid short-term labor inefficiencies, only to face catastrophic breakdowns later.
Overly aggressive standards demoralize employees, while overly lenient ones fail to drive improvement. Finding that sweet spot — challenging but achievable — requires both technical knowledge and good judgment about human motivation.
Oversimplification of complex processes
Standard costing often relies on volume-based allocations that mask the true complexity of modern manufacturing. As production becomes more automated and overhead grows as a percentage of total cost, these simplified approaches become less accurate.
This oversimplification can lead to poor decisions about product mix and pricing, especially in companies with diverse product lines that consume resources in significantly different ways.
Resource requirements for implementation
Setting up standard costing demands considerable upfront investment in system design, data collection, and staff training. Beyond initial setup, ongoing maintenance adds to these costs.
For smaller operations, these resource requirements may outweigh the benefits, making simpler approaches like ERP-supported normal costing more practical. Even for larger companies, the investment must be justified by measurable improvements in cost control and operational efficiency.
When to use standard costing
After decades in manufacturing, I’ve seen standard costing work brilliantly in some environments and fail miserably in others. Here’s my practical guide on when this method makes sense.
Ideal industry applications
Standard costing thrives in repetitive manufacturing environments where cost components remain stable. If you’re making the same products day in and day out, this system starts to shine. Process industries like food production, chemicals, or basic consumer goods are perfect candidates, unless raw material or labor prices are prone to fluctuations.
When your production runs are measured in thousands or millions of units with minimal variation, the effort of establishing standards pays off through consistent, comparable data across production periods. Companies making custom, one-off products should look elsewhere.
Company size and resource considerations
Medium to large manufacturers typically have the resources needed to implement and maintain standard costing properly. They can justify dedicating staff time to develop standards, track variances, and keep the system current.
Small shops with fewer than 50 employees often find the administrative overhead prohibitive unless they’re producing highly standardized products. Before implementing, be brutally honest about whether you have the resources to do it right. A half-implemented standard costing system creates more problems than it solves.
Business objectives alignment
Standard costing works best when operational efficiency and cost control top your priority list. If your competitive advantage comes primarily from driving down production costs, this method provides the visibility you need.
Companies with regulatory reporting requirements often find standard costing helpful for inventory valuation and GAAP compliance. However, if your strategy emphasizes rapid innovation, customization, or maximum flexibility, other costing approaches might better support these goals.
How to do standard costing
Setting up standard costing isn’t rocket science, but it does require methodical work and attention to detail. Here’s a streamlined approach based on what I’ve seen work in the real world.
Establishing standards
Start with material standards by determining both expected prices and quantities. Purchasing records, supplier quotes, and engineering specs provide your foundation. Don’t forget to build in allowances for normal waste—perfect material usage exists only in textbooks, not on shop floors.
For labor standards, analyze how long operations should take and at what wage rates. You can use detailed time-motion studies for critical operations, but don’t get bogged down measuring every movement. Historical performance data combined with reasonable efficiency targets often works just as well.
Overhead standards require identifying appropriate cost pools and allocation bases, then calculating predetermined rates based on normal volumes. Remember to separate fixed costs (which don’t change with production levels) from variable costs (which do) for more meaningful variance analysis later.
Implementation process
Start with thorough system design, defining how standards will be established, documented, and used. Create standard cost records, variance reports, and investigation procedures before you need them.
Staff training is crucial—everyone from production supervisors to accounting needs to understand not just how the system works, but why it matters to their job. The best-designed system fails when people don’t buy in. Address resistance head-on by explaining benefits for each department, not just accounting.
Documentation and procedures
Document your standards comprehensively with standard cost sheets detailing the components of each product’s cost. This transparency prevents the “black box” syndrome where nobody trusts the numbers because they don’t understand where they came from.
Establish formal procedures for reviewing and updating standards—typically annually during budgeting, with special updates when significant changes occur in production methods or input costs. Without this maintenance schedule, standards quickly drift into irrelevance.
How to do cost variance analysis
Variance analysis separates the winners from the also-rans in standard costing. Here’s how to turn those variance reports into actionable intelligence without drowning in data.
Types of variances
Material variances come in two flavors: price variances (paying more or less than the standard for materials) and quantity variances (using more or less material than the standard). Track these separately. Knowing whether your problem is purchasing or production makes a world of difference in finding solutions.
Labor variances follow the same pattern: rate variances from paying different wages than standard and efficiency variances from taking more or less time than standard. A negative efficiency variance with a positive rate variance often signals using higher-skilled workers who finish faster—sometimes a smart tradeoff.
Overhead variances include spending variances (actual overhead costs versus budget) and efficiency/volume variances (impact of production volume on overhead absorption). These tell you whether you’re controlling overhead costs and utilizing capacity effectively.
Variance calculation methods
For material price variance, multiply the difference between actual and standard price by the quantity purchased: (Actual Price – Standard Price) × Actual Quantity.
Material quantity variance is the difference between actual and standard quantity, multiplied by standard price: (Actual Quantity – Standard Quantity) × Standard Price.
Similar formulas apply to labor and overhead variances. The key is consistency—use the same calculation methods period after period so trends emerge clearly.
Interpreting variance results
Variances typically get labeled as “favorable” (actual costs below standard) or “unfavorable” (actual costs above standard), but these labels can be misleading. An “unfavorable” material price variance might result from buying higher-quality materials that reduce scrap, potentially a net win.
Focus on significant variances, not pennies. Most companies set materiality thresholds (often 5% or more) to focus attention where it matters. When investigating causes, look for patterns across product lines or time periods rather than isolated incidents.
Variance reporting best practices
Design reports that highlight exceptions rather than drowning managers in data. Use visual cues—traffic light colors work well—to quickly identify problem areas.
Monthly reporting is standard, but critical variances might warrant weekly or even daily monitoring. Ensure reports reach people who can actually address the issues, not just their bosses.
Make variance review a regular part of management meetings, with clear accountability for investigation and corrective action. Without this closing of the loop, variance analysis becomes an academic exercise rather than a management tool.
How manufacturing ERP helps you track costs
Modern MRP/ERP systems have transformed cost accounting from a paper-pushing nightmare into a streamlined process. Instead of standard costing, the best manufacturing ERP software solutions use normal costing to provide users with an accurate real-time overview of their production costs as well as historical cost data.
Automated data collection capabilities
Gone are the days of manually logging material usage or tracking labor hours on paper. Today’s systems automatically capture cost data throughout the production process—from material requisitions to labor time to machine utilization.
This real-time tracking eliminates most manual data entry errors while providing immediate visibility into performance. When shop floor workers enter information for material issues or clock in and out of operations, that data flows directly into your costing system without requiring an army of clerks to process paperwork.
Built-in reporting and analysis tools
ERP systems come loaded with cost reports, allowing you to cost products and generate cost overrun and profitability reports with a few clicks instead of days of spreadsheet manipulations.
Customizable dashboards provide at-a-glance visibility into cost performance. The best systems let you drill down from high-level summaries into the underlying transactions when questions arise. This ability to follow the cost trail from summary to source transforms accounting from historical scorekeeping into proactive management.
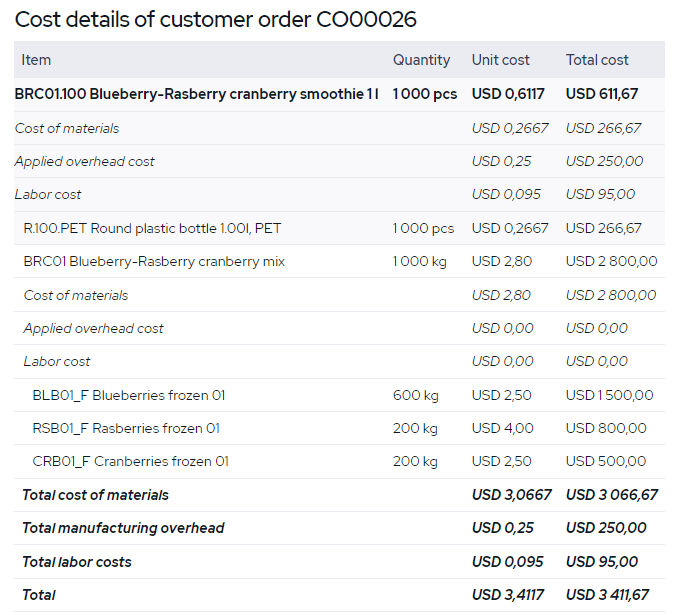
Implementation considerations
When selecting an ERP system with cost management in mind, evaluate how well it supports your preferred costing methods and the flexibility of its configuration. The best system on paper becomes worthless if it can’t handle your specific industry requirements.
Proper configuration is essential—setting up accurate bills of materials, routing operations, cost centers, and allocation methods that reflect your production reality. Any ERP implementation is only as good as the data that goes into it.
ROI of MRP-based cost management
A good manufacturing ERP solution dramatically reduces the administrative burden of cost accounting. Companies frequently report cutting days from their month-end close process after implementation.
But the real payoff comes from improved decision-making when everyone in the organization has access to timely, accurate cost information. From daily operational choices to strategic initiatives, solid cost data provides the foundation for continuous improvement and competitive advantage in today’s manufacturing landscape.
Key takeaways
- Standard costing sets predetermined costs for materials, labor, and overhead, allowing manufacturers to measure actual performance against these benchmarks. It simplifies budgeting, inventory valuation, and decision-making, especially in repetitive production environments.
- Standard costing thrives in industries where product runs are consistent and input costs remain relatively stable. It’s less suited for custom or volatile production environments.
- Variance analysis—comparing actual costs to standard costs—helps identify inefficiencies in material usage, labor, and overhead.
- If not regularly updated, standards can become irrelevant, leading to meaningless variance reports.
- Modern ERP systems often favor normal costing for real-time, accurate tracking of production costs.
- Standard costing suits medium to large manufacturers with the resources to maintain it properly. Small businesses with limited administrative capacity may benefit more from simpler costing methods or ERP-supported systems.
Frequently asked questions
A standard cost system might set material costs at $2.50 per unit, labor at 1.5 hours per unit at $20 per hour, and overhead at $5 per unit. These predefined costs are used to estimate production expenses and identify variances from actual costs.
No, standard cost is a predetermined estimate of production costs, while COGS (Cost of Goods Sold) reflects the actual expenses incurred to produce goods sold. Variance analysis compares standard costs to actual COGS to assess performance.
Standard costing simplifies budgeting, inventory valuation, and performance evaluation using predefined cost benchmarks. However, it can become outdated quickly, may not suit custom manufacturing, and requires significant effort to implement and maintain.
You may also like: Process Costing – A Guide to Better Cost Accounting