Process Costing – A Guide to Better Cost Accounting
To price effectively, everything it takes to manufacture a product must be accounted for. If priced too low, the sale won’t cover expenses. Too high, and the company risks pricing themselves out of the market. There are two main ways to implement cost accounting. This post will focus on process costing.
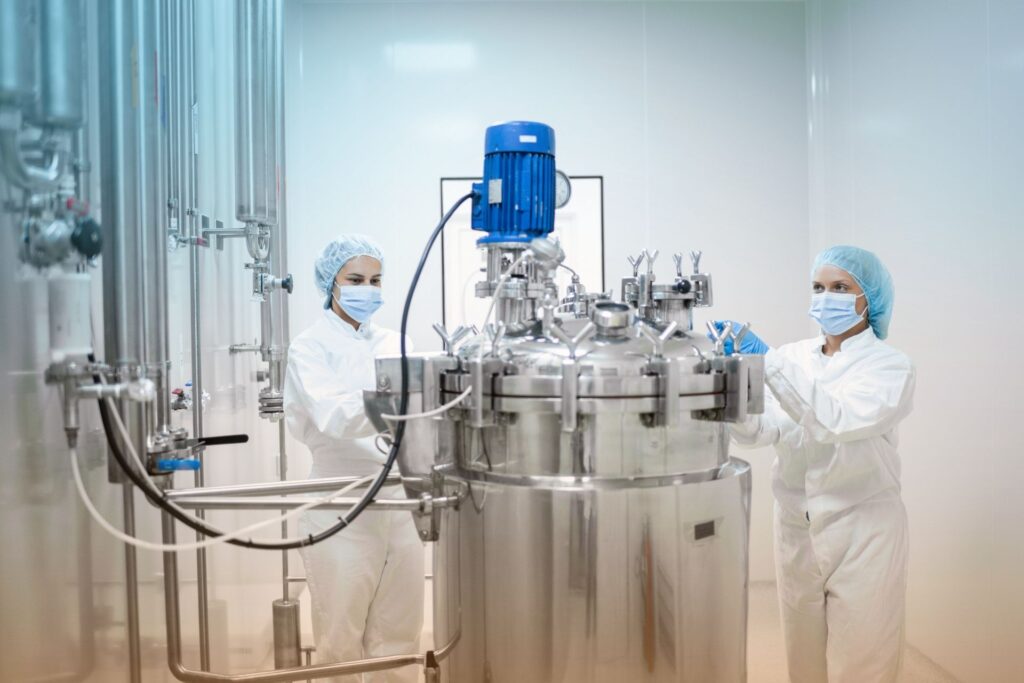
What is process costing?
Process costing is a production cost accounting method used for similar products with few variations. These products are often mass-produced in a continuous production process flow, normally in bulk quantities.
Because the products are identical or nearly so, it’s difficult to directly track the production costs for individual units. Some examples of products and industries that need process costing are paints and lacquers, food processing, supplements, and oil refining operations.
When should process costing be used vs. job costing
In manufacturing, some products are made of distinct components. Other products are manufactured as a mix of blended ingredients. This distinction determines the costing method used.
Job costing requires separately identifiable components to be assembled. For example, a table has distinct components (tabletop, legs, hardware) and well-defined direct labor costs associated with it. Therefore, the costing equation looks like this:
Cost per unit = Parts + labor costs + allocated manufacturing overhead
Process costing works differently. You’re looking for an average cost per unit or batch of product. In this model, you’ll consider everything associated with the product’s production, and divide it by the number of units or volume manufactured. The costing equation simplified is:
Cost per unit = Total manufacturing cost / number or volume produced
Process costing works best for bulk manufacturing
Instead of tracking costs per unit, as in job costing, process costing averages the costs up and down the manufacturing process. The costs can be allocated to both the finished product and WIP (work in process) inventory. Partially completed product is treated in the same manner as completed product by handling them all as equivalent units and then determining the average cost per each.
During the information-gathering stage of the process costing system, costs are tabulated by department and stage of manufacturing. When analyzed, this can actually help with process improvement, showing areas where efficiency can be increased.
Process costing methods
There are three basic costing methods in process costing: Weighted Average, FIFO (First-in, First-out), and the standard costing method. The standard costing method can also be used together with either of the first two. Which method to use depends on several variables. However, here’s a basic workflow for going about the process.
How to conduct process costing?
- Analyze inventory: You need to know the flow of products for the accounting period. This includes the beginning inventory of incomplete items, the number of units started and completed during the period, and the number of incomplete units at the end of the time period.
- Calculate equivalent units: Cost calculations are done using completed units. Any uncompleted work in process inventory items need to be converted to whole equivalent units of production. For example, if you have 500 incomplete units, but they are 50% complete, you will use 250 as an equivalent unit for cost calculations.
- Tally up total applicable costs: Any costs associated with production must be aggregated. This includes direct material costs, as well as indirect conversion costs. Conversion cost examples are direct labor costs, energy costs, and other manufacturing overhead necessary.
- Calculate the cost per unit: To arrive at the per-unit cost, divide the total production costs of the accounting period by the number of total equivalent units. Include both completed units and the unfinished equivalent units of production.
- Allocate costs: Finally, the total costs are allocated to the completed and equivalent units of unfinished product in proportion. Now the cost of goods sold and the value of the WIP inventory can be calculated.
1. Weighted average method
At its core, this method combines the beginning WIP inventory with the current period’s total production costs and then calculates a single cost per equivalent unit value. This includes the units completed and transferred out of the department or production line.
The weighted average method uniformly applies this average cost to all the units, both completed and partially completed, during the accounting period. It treats all units as though they were started and completed during the same time frame.
It’s the simplest method because it eliminates the need for tracking costs across different periods. However, it’s also the least accurate as it includes incomplete production units. But it’s adequate if cost fluctuations are modest.
2. FIFO (First-In, First-Out) method
This method differs from the weighted average method by keeping beginning inventory costs separate from current period costs. It follows the order in which units enter production and move through the process until the end of the period.
The key feature of FIFO is that it applies prior period costs to units that were already in process at the start of the period, while newly started units are assigned current period costs. Under FIFO process costing, costs per equivalent unit are calculated separately for:
- Units completed from beginning inventory
- Units started and completed during the current period
- Units still in process at the end of the period
Although more complex, the FIFO process costing method provides greater detail and a clearer chronological view of costs. This more precise recordkeeping improves both cost tracking and performance evaluation
3. Standard costing
This method allocates costs by averaging the costs assigned to each process or production stage across all units produced within a given time period. Standard costing relies on historical data, which is used as a benchmark to measure actual production performance.
There are three key components in standard process costing:
- Direct materials, calculated by multiplying standard prices by standard quantities.
- Direct labor, determined by multiplying the standard hourly rate by the standard hours worked.
- Manufacturing overhead, based on predetermined rates for indirect costs such as power consumption, property fees, and other factory expenses.
The standard costing method is particularly useful for analyzing variances between actual and standard costs. These variances help identify inefficiencies, guide adjustments to production processes, and ensure that standards remain accurate over time.
Standard costing can also be combined with either of the previous process costing methods (FIFO or weighted average) to provide deeper insights into cost management and rate adjustments.
The importance of accurate process costing for small manufacturers
Small- to mid-sized process manufacturers rely on process costing to help increase productivity and control costs. An accurate costing system is vital for informed budget decision-making. When appropriately implemented and analyzed carefully, proper process costing can help:
- Improve pricing strategies by understanding the true cost of production.
- Reduce waste by tracking costs, leading to better resource allocation.
- Ensure accurate financial reporting that maintains compliance with accounting standards and regulations.
- Identify innovations in processing, allowing SMEs to invest part of their budget in research and development of new processes, product improvements, and even market expansion.
Other advantages directly related to market standing include lower prices, higher profit margins, and often a combination of the two.
Process costing in modern manufacturing – the software advantage
Keeping track of inventory and raw materials, process efficiency, and production costs have always been important to manufacturing. However, since most SMEs now compete in a global marketplace, keeping tabs on these items that affect a company’s bottom line and profit margins is critical for ongoing success. Both hardware and software solutions help make process costing more efficient and accurate in determining the actual cost of finished goods.
Hardware advancements for record accuracy
Hardware-based technological advancements make production cost tracking easier at critical points in the process. For example, Internet of Things (IoT)-enabled sensors, meters, and gauges are often used in data collection.
These devices track utility consumption, such as gas, water, and electricity. Sensors can also track process efficiency and identify bottlenecks in production lines. Using IoT-connected systems, utility use in manufacturing processes can be separated and tallied by time or location. The indirect costs can be applied to the area or department used to calculate overall overhead costs.
While recording and analyzing the myriad data points in an operation used to be a human chore, process monitoring solutions now assist humans with speed, accuracy, and analytics that couldn’t be achieved in the past.
How software contributes to process costing
Manufacturing software solutions join with their human counterparts for inventory tracking, order planning, and yes, process costing. Because these programs work in real-time, their speed and accuracy help improve many facets of the manufacturing industry.
MRP (Materials Requirement Planning) software encompasses all manufacturing resources. It includes equipment tracking, workforce direct labor and allocation, overhead costs, financial accounting, and component costs.
Capabilities to monitor and report operational costs, labor, and other expenditures related to production processes, an accurate analysis of manufacturing costs can be generated for process costing.
MRP software eliminates guesswork and the potential for human error. These solutions are scalable and designed to grow in capability as the manufacturer’s capacity grows and expands. This makes it easier for a company to increase its bottom line.
5 key takeaways for understanding process costing
- Process costing is specifically designed for continuous process manufacturing, where bulk quantities of identical or similar products are produced. Almost any mixed rather than assembled product will benefit from process costing. Examples include paints, process foods, pharmaceuticals, and petrochemicals.
- There are three methodologies for process costing:
- The weighted average method is a simplified approach used for stable cost situations. It combines beginning inventory with the current period inventory to determine the cost per equivalent unit.
- The FIFO (First-in, First-out) method separately tracks the beginning inventory and current period costs, giving a chronologically accurate analysis.
- The standard costing method uses historical data as benchmarks for performance evaluation. It can be combined with either of the previous methods.
- Technological advancements in hardware (IoT-enabled devices) and software (MRP systems) enable businesses to track their process costs more accurately and precisely than before.
- The business impact an effective process costing program affords is measurable:
- It enables a more accurate pricing strategy.
- It supports waste reduction and better resource allocation.
- Compliance with accounting standards and regulations is augmented.
- It facilitates innovation by spotlighting areas for process improvement.
- Accurate process costing is the ticket to success for small and medium-sized process manufacturers wanting to compete in the global marketplace. It helps maintain competitiveness by allowing them to make informed decisions, not educated guesses, on their process costs.
Frequently asked questions
Process costing is used for mass-producing similar products in continuous processes, where costs are averaged over units. Job costing, in contrast, tracks costs for distinct, individual products or batches, accounting for unique materials and labor per job.
Process costing calculates the total manufacturing cost and divides it by the number of equivalent units produced. It tracks costs by production stages, allocating expenses to completed goods and work-in-process inventory to ensure accurate cost assessment.
Industries that produce large volumes of similar or identical products, such as food processing, paint manufacturing, pharmaceuticals, and oil refining, commonly use process costing to simplify cost tracking and enhance production efficiency.
Continue reading about: Manufacturing Automation: Benefits, Tips, and Budget-Smart Options