Inventory Accounting – A Quick Guide
Inventory accounting is a critical aspect of managing a business that sells physical products, ensuring that the value of physical assets is accurately tracked and reported. In this guide, we explore the key concepts, systems, and methods of inventory accounting.
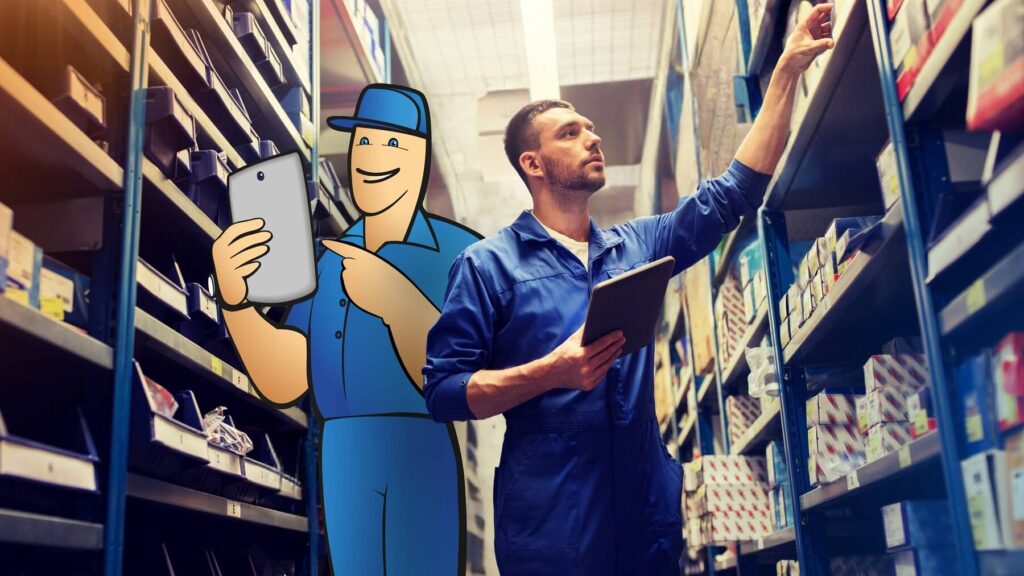
You can also listen to this article:
What is inventory accounting?
Inventory accounting is the process of tracking and managing the value of a company’s inventory. Sometimes also called inventory costing, inventory accounting involves recording and analyzing the costs associated with a company’s physical assets, namely the three main types of inventory – raw materials, work-in-process (WIP), and finished goods.
Inventory accounting is an indispensable part of overall inventory management. It is crucial for maintaining accurate financial statements, keeping costs in check, ensuring regulatory compliance, and also effectively managing production and purchasing.
In order to properly conduct inventory accounting, companies first need to set up an inventory accounting system and then decide which inventory valuation method to utilize. Let’s look at these next.
Inventory accounting systems
The two major types of inventory accounting systems are the periodic and perpetual inventory systems.
- Periodic inventory is the more conventional type of inventory system. As the name implies, stock levels, corresponding inventory movements, and the involved costs are calculated periodically with physical stocktakes and inventory counts. Periodic inventory is still widely in use in small businesses with limited inventory complexity.
- Perpetual inventory systems, on the other hand, keep track of and calculate stock movements and values continuously. As soon as an inventory item enters stock, is used in a manufacturing process, or is sold, the inventory system records it, calculates the involved costs, and leaves behind a digital trace of the action. This enables accurate stock records in real time. Perpetual inventory systems form the basis of modern inventory management software.
Inventory costing methods
The other crucial prerequisite of setting up proper inventory accounting is choosing a suitable costing or inventory valuation method. There are several inventory accounting methods available for companies to choose from.
In the US, the chosen method needs to follow the Generally Accepted Accounting Principles (GAAP), which presumes that all inventory values need to be recorded at their true cost or market value, whichever is less. However, other standards exist, such as the International Financial Reporting Standards (IFRS).
GAAP accepts four main methods – FIFO, LIFO, Specific Identification, and Weighted Average Cost:
- First-In, First-Out (FIFO). The FIFO method assumes that the oldest inventory items are sold first. It is widely used because it aligns with the natural flow of inventory, especially perishable goods. FIFO can result in lower costs for goods sold and higher profits during periods of rising prices. An adaptation of FIFO, popular among food and pharmaceutical manufacturing is FEFO – First-Expired, First-Out. FEFO prioritizes optimizing the use of perishable stock to avoid obsolescence.
- Last-In, First-Out (LIFO). This approach assumes that the most recently acquired inventory items are sold first. The LIFO method can be beneficial for companies looking to match current costs with current revenues, especially in times of inflation. However, it is not allowed under IFRS.
- Weighted Average Cost. The weighted average method calculates the average cost of all inventory items available for sale during the period. It smooths out price fluctuations over the accounting period, providing a stable cost basis. The weighted average cost method is simple to apply and useful for industries with large volumes of undifferentiated products.
- Specific Identification. This approach tracks the cost of each specific item in inventory. It is most suitable for businesses dealing with high-value or unique items, such as jewelry or engineer-to-order products. This method provides precise cost tracking but can be cumbersome to manage for larger inventories.
Key concepts of inventory accounting
Inventory classification
Inventory is a current asset on the balance sheet, representing the value of a company’s goods available for sale or in the process of being produced for sale. As a current asset, inventory is expected to be converted into cash within a year. Proper classification and valuation of inventory are essential for accurate financial reporting and analysis.
As we have seen, inventory is classified into three main categories: raw materials, work-in-process (WIP), and finished goods.
- Raw materials. These are the basic components required for production. Accounting for raw materials involves recording the cost of inventory purchases and their transportation to the manufacturing facility. Accurate tracking of raw materials helps in budgeting and forecasting production needs.
- Work In Process (WIP). WIP inventory includes items that are in the process of being manufactured but are not yet completed. WIP accounting is more complex as it must include not only the cost of raw materials but also direct labor and manufacturing overheads. These additional costs reflect the value added during the production process.
- Finished goods. Finished goods are completed products ready for sale. The accounting for finished goods involves transferring the total production cost from WIP to the finished goods inventory. This includes the cumulative costs of raw materials, labor, and overheads incurred during the manufacturing process.
Tracking production and inventory costs
Tracking stock movements and production costs is an indispensable part of the accounting process and major functionality of inventory software. Accurate tracking is crucial for several reasons. It enables companies to determine the true cost of their products, essential for setting competitive prices, financial reporting, and achieving profitability.
Tracking production costs further aids in identifying inefficiencies in the production process to allow businesses to implement cost-saving measures. It further provides critical data for budgeting, forecasting, and financial planning, ensuring that resources are allocated efficiently.
Inventory tracking can be achieved through various methods such as barcode scanning, RFID tags, and automated inventory management systems, providing real-time data to aid in efficient decision-making.
Cost of Goods Sold (COGS) and its importance
The Cost of Goods Sold (COGS) is a financial metric that represents the direct costs attributable to the production of goods sold by a company. It includes the cost of raw materials, direct labor, and manufacturing overheads. COGS is the central metric in inventory accounting as it directly impacts a company’s gross profit and overall profitability.
The basic calculation that informs COGS is:
COGS = Beginning inventory + Purchases − Ending inventory
For manufacturers, the COGS calculation also involves finding the Cost of Goods Manufactured which, simply put, is the value of labor and other expenses associated with the production of goods on top of purchases. For manufacturers, Purchases are replaced with COGM in the COGS formula.
Cost Of Goods Sold enables calculating gross profit by deducting the COGS value from sales for a period. Accurate calculation of COGS is essential for pricing strategies, financial analysis, and tax reporting. It also provides insights into production efficiency and cost management, helping businesses optimize their operations.
The importance of accurate inventory accounting
- Financial statement accuracy. Accurate stock accounting ensures that financial statements reflect the true value of the inventory. For example, if a manufacturer overstates its inventory, it may appear more profitable than it actually is, leading to potential issues with investors and regulatory bodies. Correct inventory values help maintain investor confidence and meet compliance requirements.
- Cost and cash flow management. Proper inventory accounting helps identify the true cost of production, essential for managing expenses and efficient budgeting. It also provides insights into the company’s cash flow by showing how much cash is tied up in inventory. This knowledge helps in planning future investments and ensuring sufficient liquidity to meet obligations.
- Regulatory compliance. Adhering to GAAP or IFRS is a prerequisite for operating in most markets. Accurate inventory accounting is essential for meeting tax obligations and avoiding fines. Non-compliance can result in penalties and legal issues, and negatively impact a company’s investor portfolio.
- Inventory control. Accurate accounting also aids in maintaining optimal inventory levels, preventing stockouts and excess inventory. This is crucial for manufacturers who need to balance having enough raw materials for production while avoiding the costs associated with overstocking. Proper inventory control is a basic requirement for more efficient production planning and higher customer satisfaction.
- Profitability analysis. By understanding the cost of goods sold (COGS) and inventory values, a company can analyze its profitability more accurately. This helps in making informed decisions about product lines, pricing strategies, and the overall business direction.
- Operational efficiency. Accurate inventory accounting supports better decision-making related to production schedules, procurement, and supply chain management. Manufacturers with precise inventory tracking can streamline operations, reduce lead times, and improve overall efficiency, resulting in cost savings and a more responsive supply chain.
- Risk management. Finally, proper inventory accounting helps to identify and mitigate risks related to inventory management. Detecting discrepancies or losses early prevents significant financial impact and helps maintain the integrity of inventory records, thus working to safeguard company assets.
Inventory accounting with inventory management software
Inventory management software is a powerful tool for ensuring accurate and efficient inventory accounting. By automating many of the manual processes involved in tracking inventory, these systems help businesses maintain precise records, manage costs effectively, and streamline various operational aspects.
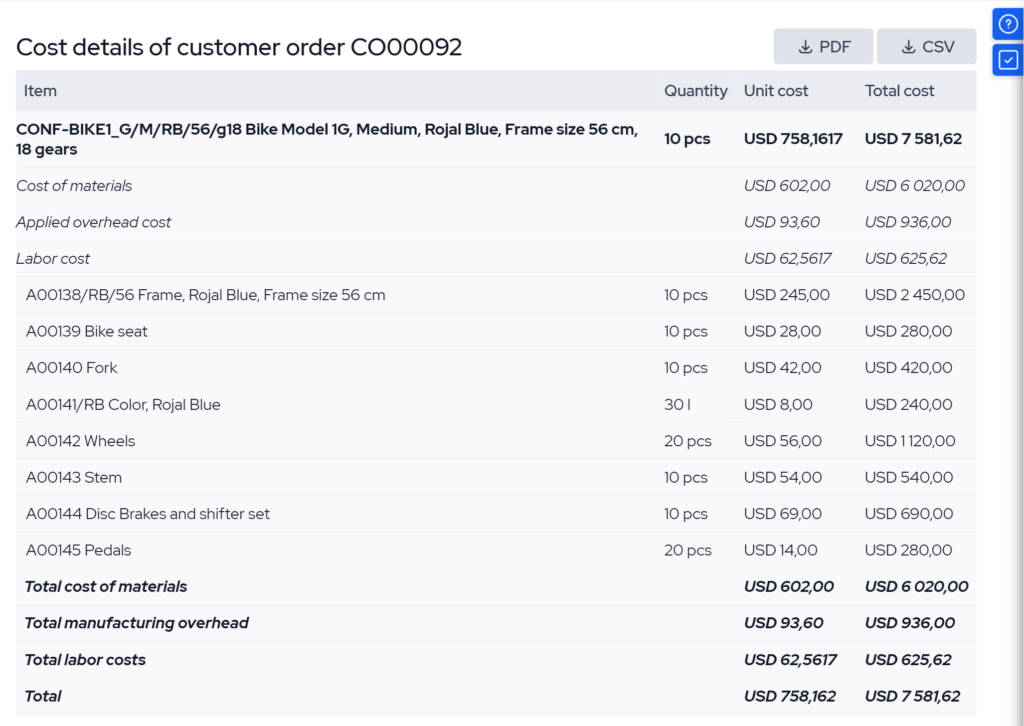
Inventory and cost tracking
These systems provide real-time visibility into stock levels, movements, and locations. This traceability eliminates the need for periodic physical counts and reduces the risk of errors. Cost tracking further allows monitoring the cost of raw materials, labor, and overheads throughout the production process. This helps businesses identify inefficiencies, control expenses, and improve overall profitability.
Simplified production planning and scheduling
Another significant advantage of using inventory management software is its ability to streamline production planning and scheduling. By integrating various business functions into a single system, the software ensures that all departments are aligned and working with the same data. This integration facilitates better planning, helps reduce lead times, and improves production efficiency.
The software also helps in managing procurement by automating large parts of the ordering process. It can generate purchase orders based on stock levels and production schedules, ensuring that raw materials are always available when needed.
Integration with other systems
Comprehensive inventory management software is purpose-built to help manufacturers and distributors manage their inventory accounting effectively. Aside from built-in tools like procurements and a standard accounting module, the best providers also integrate with popular accounting software like QuickBooks and Xero, allowing businesses to synchronize financial data seamlessly. On the other end, eCommerce and fulfillment platforms can be tied into the system, providing a cohesive overview and automating a large number of daily operations.
Key takeaways
- Inventory accounting is the process of tracking and managing the value of a company’s physical assets, including raw materials, work-in-process (WIP), and finished goods.
- Inventory accounting is conducted using either periodic or perpetual systems and involves selecting appropriate valuation methods such as FIFO, LIFO, Weighted Average Cost, or Specific Identification.
- The advantages of proper accounting include financial statement accuracy, optimal cost and cash flow management, regulatory compliance, inventory control, profitability analysis, operational efficiency, and risk management.
- Inventory management software can streamline inventory and cost tracking, simplify production planning and scheduling, and integrate with other systems like accounting software and eCommerce platforms for a unified and efficient operation.
Frequently asked questions
Inventory is recorded in accounting by tracking the cost of raw materials, work-in-process, and finished goods. This involves regularly updating inventory levels and costs using either a periodic or perpetual inventory system, ensuring that financial statements accurately reflect the value of the inventory.
The basis of inventory accounting is to provide a systematic approach to valuing and managing a company’s inventory. This includes classifying inventory into categories (raw materials, WIP, finished goods), selecting appropriate valuation methods (FIFO, LIFO, Weighted Average, Specific Identification), and ensuring compliance with accounting standards like GAAP or IFRS.
The four types of inventory are raw materials, work in process (WIP), finished goods, and maintenance, repair, and operations (MRO) supplies. Each type plays a crucial role in the production and supply chain, requiring accurate tracking and management to ensure efficient operations and financial reporting.
Choosing the right inventory valuation method depends on factors such as the nature of your products, your business goals, and financial reporting requirements. Consulting with an accounting professional and considering your industry’s best practices can help you make an informed decision.
You might also like: The 4 Types of Inventory and Tips on Managing Them