Radar Systems Manufacturer Hits the Mark with MRP Software
In 2015, a few experienced engineers from a reputable technology consultancy firm decided to go it alone and design a novel radar system. They engineered a prototype using, in part, an ordinary tea-tray. The finished product surpassed expectations and landed the team a government contract. Blighter Surveillance Systems was born.
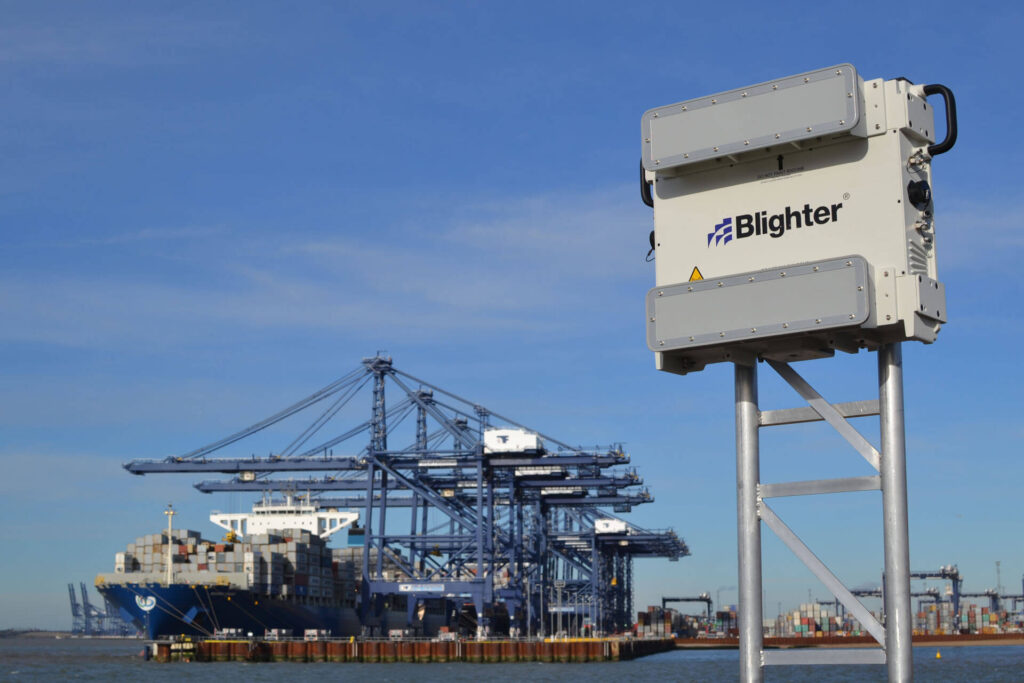
You can also listen to this article:
High-tech providers of ground-based radar systems
Blighter Surveillance Systems is a manufacturing company situated near Cambridge, UK. The firm designs and produces solid-state ground-based radar systems, supplying them to a diverse client base that includes a host of organizations in 35 countries around the globe. To date, Blighter has sold over 600 radar systems.
Today, the company employs around 25 staff in its design house, mostly comprising engineers and product designers. Its trusted subcontractors meet most of Blighter’s manufacturing requirements, so very little assembly is taking place in-house. However, Blighter manages a substantial inventory that it free-issues to its contractors.
Since the company’s inception, Blighter managed its workloads and bills of materials (BOMs) with spreadsheets. A challenging task considering the complexity inherent in radar manufacturing. In 2019, however, the management team concluded that without a robust manufacturing software solution to replace the spreadsheets, Blighter Surveillance Systems would not be able to align the production effort with its expanding market ambitions. Thus, the search for suitable manufacturing software began.
Multi-level BOMs with up to 60,000 components
Blighter had been formulating its engineering database and assigning its own part numbers for years. They needed a system that could build on the existing work, while also tracking manufacturing processes and providing visibility on stock movements.
James Watt, supply chain coordinator for Blighter explains that a BOM for their product can consist of up to 60,000 components. He describes the situation Blighter was facing: “We needed a system where we could define our own individual part numbers, control revisions, and manage multi-level BOMs. We weren’t looking for something with all the bells and whistles that would take a hundred thousand pounds to implement like SAP. But we still needed a solution for controlling production and the flow of materials through the business.”
It was one of the team’s accountants who came across MRPeasy while looking for an MRP system that would integrate well with the firm’s chosen accounting system, Xero. There were many other systems they checked out, but after starting a trial with MRPeasy, playing around with the software, and uploading some BOMs, it quickly seemed like the right balance between functionality and ease of use at an attractive price point.
Implementation revealed a host of useful functionalities
Implementation of MRPeasy began in Autumn 2020 and at first, different departments had quite different priorities in terms of setting up the system. Watt comments: “Finance wanted a use-case that would best benefit accounting simplicity but production had a different view of how to set up the system. We had a lot of initial negotiations inside the company on how best to go about this.”
Still, MRPeasy managed to consolidate everyone’s needs very well. The system perfectly met Blighter’s requirements for capable multi-level BOM management, and enabled a high level of control over inventory movements, all while aligning seamlessly with the accounting team’s requirements. Furthermore, the team also managed to implement many other useful functions like a suitable new part numbers system, user-defined fields, a PDF editor, version and revision control, and more.
The initial implementation was completed in just under 6 months and Blighter managed it without the aid of external consultants. The task was largely simplified by the software’s professional support team, which generally answered functionality queries within the same working day.
For other companies looking to implement the software, James Watt recommends thoroughly setting up the basics before putting the system to work: “Take the time, if possible, to get things like part numbers, item descriptions, and vendors set up beforehand. Importing large amounts of critical data in hindsight is much more work.”
Efficiency gains bolster operational health
With MRPeasy properly set up and running, Blighter Surveillance Systems has gained a lot more control over its operations. The largest efficiency gains have come from stock control and managing inventory turnover. James Watt shares his insights: “MRPeasy has helped us hugely with controlling the flow of goods and making sure we haven’t got loads of bits sitting around that we don’t know the use of. It has saved us from having too much cash tied up in stock.”
The system has also been a big help with stock counting. Currently, Blighter is still doing quarterly stock counts, but as MRPeasy’s use case expands, the company is moving towards continuous cycle counting that would enable presenting constant and accurate stock figures to the accounts at all times.
Since Blighter predominantly uses subcontractors for their assembly and manufacturing needs, another game-changer has been managing and tracking transfer orders. James explains: “We are different from other customers in that we use modified transfer orders for our production. As outside contractors do things on our part, we have to send stuff out to them. But we still own that stock. With MRPeasy, we can issue things to another site but still see the value of stock in our system and have it tracked and controlled. The transfer orders make it more straightforward for contractors to look at our things. Especially the companies that have accreditation and need everything to be displayed on the delivery note. Being able to manage all this within our internal MRP system has been great.”
All in all, MRPeasy has helped Blighter reach a sophisticated level of control over their manufacturing and stock management. The new system is providing ease of mind in assuring the company’s continued growth without breaking the bank.
Continue reading: Test Equipment Producer Gains a New Level of Control with Manufacturing Software