Plan Do Check Act – Implementing PDCA in Manufacturing
Continuous improvement is an important facet of the modern manufacturing landscape. One of the best-known among such methodologies is Plan-Do-Check-Act. In this article, we explore PDCA’s tenets, its benefits, and how best to conduct it.
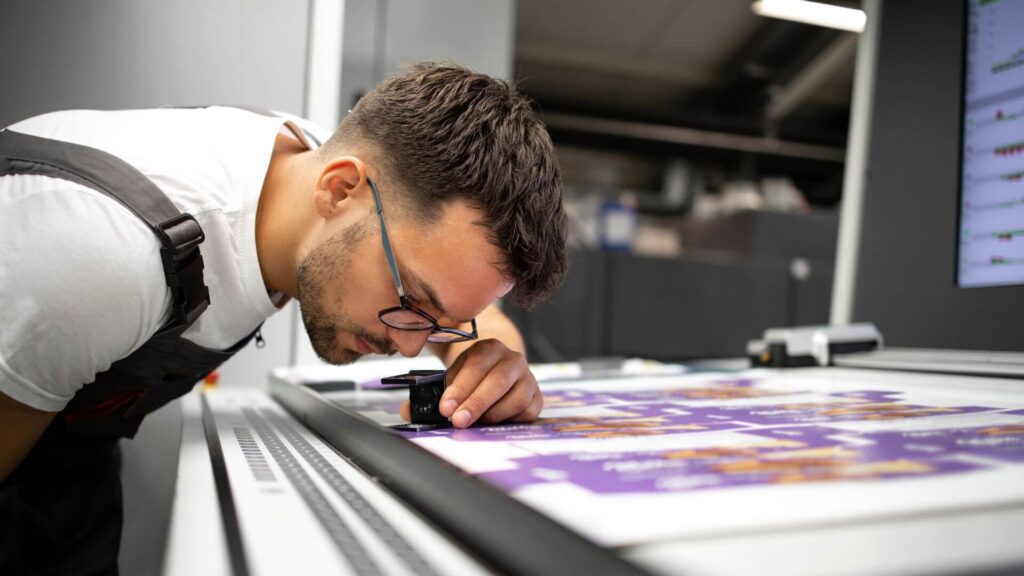
You can also listen to this article:
What is Plan Do Check Act?
Plan-Do-Check-Act (PDCA) is a four-step business management method that aims to implement continuous improvement in business process management. Sometimes also called the Plan-Do-Study-Act or the PDSA cycle, it is a repetitive model that encourages a disciplined, iterative approach to problem-solving. The four phases – Plan, Do, Check, Act – provide a simple but effective approach for managing change and ensuring that ideas are appropriately tested before committing to full implementation.
PDCA originates from Walter Shewhart, a statistician and innovator in quality management. However, it was the economist W. Edwards Deming who popularized the model. Deming stressed the importance of constant interaction among research, design, testing, and production as a basis for continuous improvement. As such, PDCA is sometimes also called the “Deming cycle”, “Deming wheel”, or “Shewhart cycle”.
Implementing the PDCA cycle in manufacturing has several benefits including the systematic approach to problem identification and resolution, enhanced communication across departments, and fostering a strategic culture of continuous improvement. In the fast-evolving manufacturing sector, PDCA helps companies stay competitive by increasing adaptability to change, improving efficiencies, and optimizing the quality of products.
PDCA and other continuous improvement methods
While PDCA is a prominent model for improving business processes, other continuous improvement (CI) models exist, each with its focus and toolset. Here are four such models and how they differ from and synergize with PDCA:
- Kaizen is a Japanese CI model that stresses involving everyone in the company from top management to shop floor workers, to focus on small daily quality improvements. Unlike the structured steps in PDCA, Kaizen encourages small changes that lead to major improvements over time. Similar to PDCA, Kaizen is also cyclical. although it’s more a mindset or part of a company’s culture rather than a single process.
- Lean manufacturing is a manufacturing-centric methodology aimed at reducing manufacturing waste such as wasted time, resources, skills, etc., while increasing productivity. It introduces specific tools like value stream mapping that help identify and eliminate waste. These can work well in conjunction with PDCA to pinpoint and solve specific manufacturing problems.
- Six Sigma is an American process improvement methodology developed in Motorola in the 1980s that mostly relies on data analysis to improve quality. It follows a specific set of steps known as DMAIC (Define, Measure, Analyze, Improve, Control) to pinpoint and address defects or bottlenecks in system processes. Compared to PDCA, Six Sigma is more detailed and data-driven, However, the two can complement each other.
- Root cause analysis is a quality management process that attempts to find the underlying reasons behind problems to ensure they don’t happen again. It’s often used within PDCA’s Plan or Check phase when a problem needs a deep dive to find out what went wrong.
The PDCA process
The Plan-Do-Check-Act cycle creates a structured process for identifying and testing changes systematically and then implementing successful strategies on a broader scale. Each phase builds on the previous one, ensuring that improvements are based on solid data and real-world testing, which helps to refine processes and achieve sustained enhancements in productivity.
Let’s go over the stages in a little more detail.
Plan
The Plan phase is where the groundwork is laid for potential improvements. In this phase, teams identify problem areas in need of enhancement, establish clear and tangible objectives, formulate hypotheses about what changes might lead to better outcomes, and map key performance indicators (KPIs) to measure the results of the upcoming PDCA cycle.
The Plan phase involves thorough research and data gathering to understand current processes and pinpoint inefficiencies. Plans are then developed for implementing solutions designed to address the identified issues, complete with manufacturing metrics to guide the next stages.
Let’s look at an example. A small manufacturer identifies a problem: excessive material waste in its production line. The team sets a clear objective to reduce waste by 20% within three months. They gather data on current waste levels, analyze workflow inefficiencies, and hypothesize that adjusting the cutting machine settings could minimize excess material. A detailed plan is then developed to test these new settings, including how they will measure the waste during the trial period.
Do
Next, the Do phase puts the plan into action on a controlled, small scale to test the effectiveness of the proposed changes. This experimental phase is crucial for mitigating risks as it limits the scope of implementation to a manageable size, making it easier to observe outcomes and collect valuable data without disrupting the whole operation. It’s essentially a trial run of what has been planned that provides a first look at potential improvements.
Continuing with our example, the manufacturer next implements the new settings on just one of its cutting machines. This allows monitoring changes without altering the entire production line, thus minimizing risk. During the Do phase, the manufacturer closely tracks the amount of material waste produced by the adjusted machine and observes any unforeseen issues as well as additional benefits that may arise from the new settings.
Check
The Check phase is where the outcomes of the Do stage are analyzed in detail. Here, the collected data from the trial implementation are compared against the expected results and baselines to evaluate the success of the intervention. The Check phase is critical for understanding the efficacy of the plan and the impact of the changes made.
It’s an opportunity for reflection and study where companies can identify discrepancies, gather insights, and determine whether the hypothesized improvements were realized. If further changes are deemed necessary, the cycle is often reverted back to the Plan phase.
In our example, the team next analyzes the data collected from the pilot project. They discover that the new machine settings have reduced material waste by 15% – slightly below the intended target, but still a significant improvement. However, an unexpected benefit has also emerged – cutting operation on the tested machine is now 10% faster. Reviewing these findings, the team uncovers why the target wasn’t fully met and determines that the improvement cannot be leveraged further.
Act
Finally, the Act phase involves making informed decisions based on the insights from the Check phase. If the trial changes prove successful, Act focuses on standardizing the improvements and implementing them on a larger scale across the organization.
If the results are not as anticipated, the Act phase serves as a feedback loop where the initial plan is revised and refined based on lessons learned, readying the team to enter the PDCA cycle again. The Act phase ensures that improvements are solidified in the company’s operations and that the cycle of continuous improvement is perpetuated.
In our example, the manufacturer decides to adopt the new machine settings across all cutting machines, given the successful reduction in waste and increased productivity. They update the training materials for machine operators to include the new settings and procedures, and schedule regular follow-ups to monitor the broader implementation. They also decide to revisit the PDCA cycle quarterly to identify further improvements.
PDCA best practices for manufacturers
Next, let’s take a look at four PDCA best practices for manufacturers and distributors.
Encourage cross-functional teams
Different perspectives can lead to more innovative solutions and increase the likelihood of spotting potential problems or improvements. Involve a variety of departments like engineering, production, stock, quality control, etc., in the PDCA cycle. This collaborative approach further enriches the planning and problem-solving process and also facilitates easier buy-in and implementation across the company.
Clearly define objectives and metrics
Clear and understandable objectives and concrete metrics are essential for measuring the impact of your actions in the PDCA cycle and ensuring alignment with your overall business goals.
Set specific, measurable, achievable, relevant, and time-bound, i.e. SMART objectives at the beginning of the Plan phase. Determine which KPIs will help you measure success most efficiently, and track them throughout the PDCA cycle to assess progress and the effectiveness of implemented changes. Documenting results consistently is also a must.
Engage and train employees
Engaging and training team members at all levels in the PDCA process empowers them to contribute to the improvement cycle’s efficiency. When employees understand how their actions can influence company performance, they are more likely to take ownership of their roles and actively participate in problem-solving and process optimization.
Tips on engaging employees:
- Develop training programs that outline the fundamentals of the PDCA cycle and its importance to the company’s goals.
- Use real-life examples from your operations to illustrate how each phase of the cycle works along with its impact.
- Involve employees in every PDCA cycle by assigning specific roles related to their expertise and interests.
Regularly review and adapt the cycle
Market conditions, technology, as well as internal business processes are always evolving. Therefore, the PDCA cycle itself should be subject to regular review and adaptation to remain effective.
Schedule regular reviews of your PDCA processes to examine their effectiveness and relevance in the current business environment. Update your approaches and strategies in response to new insights and changes in the industry to ensure that the PDCA model continues to drive meaningful improvements.
How can manufacturing software help usher in continuous improvement?
Manufacturing software can play a pivotal role in fostering an environment of continuous improvement within industrial operations. By integrating a unified software solution, manufacturers can streamline their processes, enhance cross-departmental communication, reduce errors, and maintain more consistent quality standards. Let’s take a look at some of the ways manufacturing software can effectively support your continuous improvement efforts.
Enhanced data collection and analysis
Manufacturing software automates the collection and analysis of critical data from various points in the production process. This provides live dashboards for performance metrics and real-time info on production bottlenecks and maintenance needs. With access to accurate and timely data, companies can identify areas for improvement, predict potential issues before they occur, and make better decisions faster.
Traceability and compliance
Manufacturing software significantly enhances traceability and aids in meeting stringent regulatory compliance requirements. By maintaining detailed records of the entire manufacturing process from raw materials to finished products, MRP systems ensure that every component can be tracked through each stage of production. This traceability is crucial for identifying the sources of defects, monitoring the effects of process changes, and ensuring that all products meet quality standards.
Standardization of processes
One of the key benefits of well-implemented manufacturing software is its ability to standardize operations across the production floor. Standardization is crucial for eliminating variability in product quality and production efficiency. Consistent processes make it easier to spot deviations and correct them, leading to higher quality and more reliable output.
Facilitating communication
Effective communication is critical in continuous improvement frameworks. Manufacturing software enhances communication and human resource management by providing a unified platform for information sharing between different departments. Updates, changes, and feedback can be disseminated quickly and clearly, ensuring that all team members are on the same page and can respond promptly to new information or adjustments in the production cycle.
Supporting proactive maintenance
Manufacturing software includes tools for monitoring machinery and equipment performance, which helps in implementing proactive maintenance strategies. By anticipating maintenance needs before they lead to downtime, manufacturers can keep their operations running smoothly and avoid interruptions that could affect productivity and quality. This proactive approach is integral to the “Check” and “Act” phases of the PDCA cycle, where ongoing adjustments are made to maintain optimal performance.
Key takeaways
- PDCA is a cyclical, four-step approach to continuous improvement that helps manufacturing organizations systematically address and solve problems to enhance productivity and product quality.
- The Plan-Do-Check-Act cycle is important for maintaining competitiveness in the manufacturing industry by fostering adaptability and continuous enhancement of processes.
- The PDCA cycle consists of Planning to identify and assess problems, Doing small-scale trials of potential solutions, Checking the results against expected outcomes, and Acting to implement successful changes broadly or to refine the plan and retest.
- PDCA’s best practices for manufacturers include starting with small, manageable projects, clearly defining objectives and metrics, engaging and training employees across all levels, and regularly reviewing and adapting the cycle to align with evolving market conditions and internal operational shifts.
Frequently asked questions
Small manufacturers can assess the financial impact of the PDCA cycle by tracking specific metrics before and after changes are made. Key performance indicators like production costs, waste reduction, time to market, and product quality defects can be analyzed to determine cost savings and revenue enhancements. Additionally, conducting before-and-after analyses on pilot projects can provide a clear picture of financial benefits.
Common challenges for small manufacturers include limited resources for extensive testing and resistance to changing established processes. To overcome these, manufacturers can start with small-scale pilot projects to demonstrate the effectiveness of PDCA without requiring significant upfront resources. Engaging employees through training and clear communication about the benefits of PDCA can also help mitigate resistance to change.
The PDCA cycle can be integrated with existing ERP systems or other technology solutions used by small manufacturers. Most modern manufacturing software supports data collection and analysis which are crucial for the Check phase of PDCA. Manufacturers can leverage these tools to automate data gathering and analysis, aligning PDCA activities with other operational processes and ensuring that improvements are based on accurate and timely data.
You might also like: What is Poka-yoke and How To Use it in Manufacturing?