Top ISO Standards Used in Manufacturing
Getting a relevant ISO certification can bring a wealth of benefits to manufacturers, which generally decisively offset the associated costs. In this article, we break down five ISO standards that are pivotal for manufacturers and offer insights into how they can elevate business processes and open doors to new opportunities.
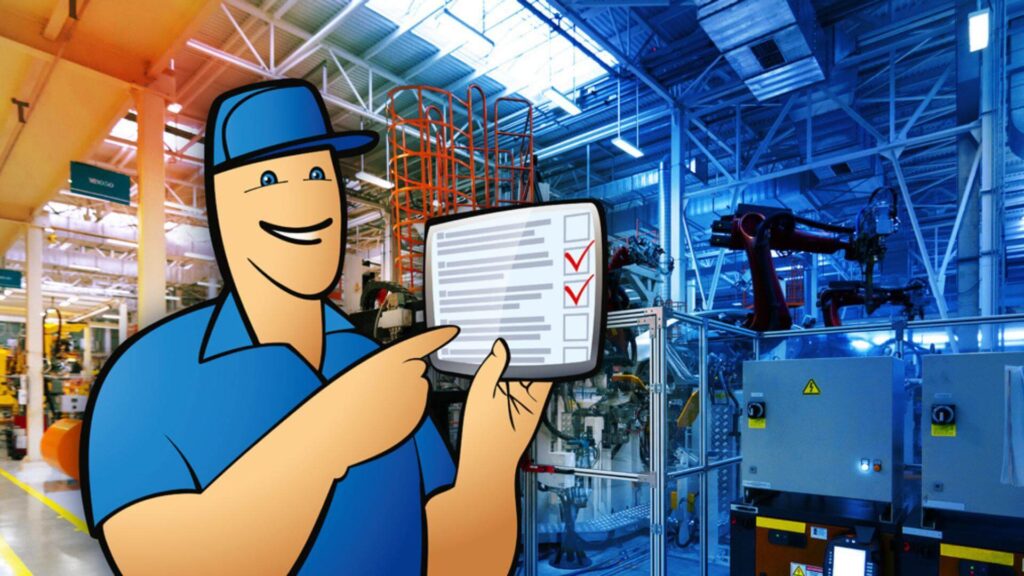
You can also listen to this article:
What are ISO standards?
ISO standards are guidelines set by the International Organization for Standardization (ISO) to ensure the quality, safety, efficiency, or other parameters of certified systems and processes across various industries. ISO certification guarantees that a service, product, system, process, or organization as a whole corresponds to certain standards as defined by the organization. ISO is a unifying body that develops the ISO standards and acts as a global authority, however, it doesn’t certify organizations. The certification process is instead conducted by ISO’s partnered member organizations present in 167 countries around the world.
A host of different ISO standards have been developed, each regulating specific aspects of organizational activities. The major fields in standardization include quality assurance, environmental management, energy management systems, food safety, health and safety, and IT security. The total number of ISO standards and their variants developed and certified to date exceeds 22,000.
Manufacturing is a highly regulated complex industry that incorporates a host of business activities from supply chain management and quality assurance to engineering, product standardization, health and safety, and much more. As such, most manufacturing sectors rely heavily on ISO certification and also have much to gain from the process.
The benefits of ISO certification for manufacturers
ISO certification is more than just a label or a compliance requirement in manufacturing. It serves as a strategic asset that can vastly contribute to the long-term growth and sustainability of a company. Certification drives improvements in many areas of business from compliance and quality control, to market reach, operational efficiency, and risk management. Here are some of the chief reasons to get ISO certified for manufacturers in essentially any sector.
- Quality assurance. ISO certification inherently involves streamlining processes and elevating quality standards. As a result, manufacturers can assure stakeholders and customers that their products meet or exceed established quality benchmarks.
- Global market access. Manufacturers with ISO certifications find entering and competing in broader international markets easier. As the standards are globally recognized, it’s easier for certified manufacturers to adhere to international regulations and market demands.
- Operational efficiency. ISO standards require manufacturers to follow best practices in operational processes from procurement to production and shipping. This leads to enhanced efficiency and reduced waste which positively impacts the bottom line.
- Risk management. Compliance with ISO standards often requires rigorous evaluation of operational risks. Identifying and addressing these potential pitfalls enables manufacturers to preemptively solve problems that might otherwise become costly affairs.
- Customer trust. An ISO certification serves as a vote of confidence for customers. It indicates that the manufacturing processes have been vetted and meet a certain standard of quality. This helps to reinforce customer trust and loyalty.
- Increased profitability. It is true that both the certification process as well as the consecutive audits inevitably incur expenses. Furthermore, adhering to ISO standards may necessitate a greater degree of quality control to be implemented in the manufacturing process. Regardless, however, having higher quality products, being active in more markets, and boosting the brand reputation that ISO certification entails, usually tip the scales decisively toward enhanced profitability and a high ROI.
The certification process
The ISO certification process is conducted between a company or conglomerate wishing to get certified, and an accredited ISO partner known as a certification body. External consultants may also be involved to make the process go smoother.
Getting certified implies intricately documenting the processes that a standard is applied for. After that, an asset or process management system is implemented that aligns internal processes with the requirements and provides traceability. Next, an audit is conducted to ensure conformity after which a notification of certification can be issued. As a continuous last step, regular surveillance audits are conducted to ensure continued conformity.
Certification can look very different depending on the company’s internal processes and the standard being applied. Still, here’s a basic rundown of the general process:
- Identify the applicable ISO standard. Decide which ISO standard applies to your manufacturing processes. Then contact an auditor and apply for certification.
- Evaluate existing systems. Conduct an internal audit to assess your current operations and identify gaps between existing processes and the chosen ISO standard.
- Develop an implementation plan. Create a plan detailing how your organization will align its operations with the chosen ISO standard. This includes implementing a process management system detailing procedural changes, documentation, and training sessions with employees.
- Execute the plan. Begin executing the implementation plan and making necessary operational changes. Ensure that employees are trained and aware of new procedures and standards.
- Third-party assessment. Submit your implemented process management system and documentation. The auditor will evaluate your operations against the chosen ISO standard.
- Address non-conformities. If the external audit reveals areas of non-conformity, these must be addressed before certification can be granted.
- Obtain certification. Upon successful external audit and resolution of any non-conformities, your organization will be granted the ISO certification.
- Ongoing compliance. Achieving ISO certification is not just a one-time activity but a continual process that requires regular audits and updates to ensure that the manufacturer stays in compliance with the evolving standards. With each renewal period, you’ll find opportunities for improvement, thereby enhancing your competitive advantage and increasing customer trust.
Certification inevitably implies costs. These roughly fall into three categories. Developmental costs for documenting processes and implementing organizational changes. Training employees and conducting internal audits to ensure a smoother certification process. And finally, registration and the external audit process.
Top 5 ISO standards used in manufacturing
Next, let’s look at the most relevant ISO standards for manufacturing companies of any size. We also go over some industry-specific certificates useful for manufacturers below.
ISO 9001
Part of the ISO 9000 series of certificates that focus on quality management, ISO 9001 is the most widely certified ISO standard for the private sector in the world with over 1 million companies certified to date.
ISO 9001 pertains to implementing a quality management system (QMS) that applies to any type of organization that wants to improve its ability to meet customer and regulatory requirements. The standard does not guarantee the quality of products, but rather the quality of an organization’s internal processes.
The comprehensive requirements set forth by ISO 9001 touch on various facets of an organization’s operations. These include customer focus, leadership, engagement, process approach, continuous improvement, data-based decision-making, and relationship management.
Achieving ISO 9001 certification often leads to an overall increase in production efficiency and reduced waste. It also boosts customer satisfaction as quality improvement is a key objective of the standard. The certification can open many doors to new markets where ISO 9001 is a minimum requirement for suppliers. Overall, ISO 9001 can be a game-changer for manufacturers looking to up their game in quality management and expand their market.
ISO 45001
Part of the growing focus on occupational health and safety, ISO 45001 is a globally recognized standard designed to mitigate risks and prevent injuries in the workplace. Like ISO 9001, it is applicable to organizations of all types and sizes, aiming to establish and maintain a safe working environment.
ISO 45001 emphasizes creating a framework that identifies potential hazards, assesses risks, and implements controls for a safer workplace. Unlike regulations that enforce minimum safety requirements, this standard pushes for continuous improvement in health and safety protocols. Meeting ISO 45001 requirements often leads to fewer accidents, lower insurance costs, and reduced legal liabilities.
For manufacturers, achieving ISO 45001 certification can differentiate them in competitive markets, making it a strategic asset for both safety and business growth. It also addresses unique risks inherent in a production setting such as machinery mishaps, chemical exposures, or ergonomic issues. Compliance both ensures a safer work environment but also promotes efficiency as fewer accidents mean less downtime and more productivity. Additionally, certification can be a competitive edge in marketplaces that prioritize occupational health and safety like the EU, United Kingdom or Australia, boosting a manufacturer’s reputation and client trust.
ISO 14001
ISO 14001 is part of the ISO 14000 series of certificates focusing on environmental management. This standard is designed to help organizations minimize their environmental impact and comply with relevant laws and regulations.
ISO 14001 centers on the implementation of environmental management systems (EMS) that help organizations identify, monitor, and control their environmental aspects. It encourages companies to consider the environmental aspects relevant to their operations such as air pollution, water and sewage issues, waste management, soil contamination, etc. Adhering to ISO 14001 usually results in more efficient use of resources and reduced waste, thus leading to cost savings. It also demonstrates a commitment to environmental stewardship which can enhance an organization’s reputation and stakeholder relationships.
For manufacturers, ISO 14001 is increasingly critical due to growing consumer and regulatory emphasis on sustainable practices. Compliance reduces the risks of regulatory fines but also appeals to eco-conscious customers and partners. Manufacturers with ISO 14001 therefore often have a competitive edge in markets focusing on sustainability.
ISO 50001
Like the aforementioned ISO 14001, the ISO 50001 standard also addresses sustainability concerns but focuses solely on energy management. Still, both are part of ISO’s broader commitment to responsible corporate behavior. This standard aims to help organizations improve their energy performance, reduce energy costs, and meet environmental and carbon reduction targets.
ISO 50001 mandates the creation of an energy management system (EnMS) akin to the EMS encouraged by ISO 14001. The standard emphasizes continual improvement, pushing organizations to constantly evaluate and optimize their energy performance across various operational aspects, from supply to production and transportation.
For manufacturers, ISO 50001 is a vital tool for optimizing energy-intensive processes and reducing operational costs. Given the increasing global focus on sustainability and carbon emissions, compliance with this standard can be a significant market differentiator. Manufacturers that achieve ISO 50001 certification not only stand to reduce energy costs thus increasing operational efficiency but also appeal to environmentally conscious stakeholders.
ISO 10204
While not as universally recognized as the above certifications, ISO 10204 is an invaluable standard for many companies in the manufacturing industry. It provides guidelines for material certification and test reports, aiming to verify the material composition of products to ensure they meet specified criteria.
ISO 10204 mandates that a manufacturer or supplier provide a formal document, often called a Mill Test Certificate or Mill Test Report (MTC/MTR), to certify the material specifications of a product. These reports confirm the chemical and mechanical properties of the materials used, creating an additional layer of assurance for buyers as well as regulatory agencies.
Much like many other ISO standards, ISO 10204 aims to foster a business environment emphasizing trust and reliability. Manufacturers adhering to it can assure customers that their products meet quality and material integrity benchmarks. ISO 10204 has a unique appeal in sectors where material composition is critical, such as aerospace, automotive, and healthcare. Meeting ISO 10204 standards not only demonstrates a commitment to quality but also to safety and compliance. It can be an important factor in differentiating a manufacturer in highly regulated or quality-sensitive markets.
Industry-specific ISO standards
Besides the more popular standards among manufacturers, a large portion of ISO standards are meant for distinct manufacturing sectors. They can also provide a competitive edge, simplify regulatory compliance, and sometimes even be a requirement for operating in certain markets. Here are a few notable ones:
- ISO 25.x family of certificates. These standards specifically relate to manufacturing engineering and include subcategories like 25.020 (Manufacturing forming processes), 25.030 (Additive manufacturing), 25.160 (Welding, brazing, and soldering), etc. For manufacturers focused on advanced production techniques or specialized engineering tasks, these standards can be instrumental in ensuring high levels of precision and quality while warranting a competitive advantage in many markets.
- ISO 22000. This standard is essential for food and beverage manufacturers focusing on food safety management systems. It helps ensure that food products meet strict safety criteria throughout the supply chain, instilling confidence in both consumers and regulatory agencies.
- ISO 13485:2016. Tailored for medical device manufacturers, this standard emphasizes meeting regulatory and client requirements, ensuring the effectiveness of medical devices, and driving continuous improvement efforts.
- ISO 27001. While not exclusive to manufacturing, this information security management system (ISMS) standard is increasingly important for manufacturers as cyber threats grow more sophisticated. It’s particularly relevant for manufacturers that deal with sensitive data or are parts of critical or strategic supply chains.
- ISO 55000 series. Focused on asset management, these standards (particularly 55001 and 55002) are essential for manufacturers with significant investments in machinery and infrastructure. They provide a framework for establishing and maintaining an efficient asset management system (AMS). By optimizing the life cycle of assets, these standards can also lead to cost savings, increased reliability, and enhanced asset longevity.
Implementing any of the above standards can help to streamline operations, improve risk management, elevate a manufacturing business’s reputation, and provide other direct, tangible benefits.
As you consider the path to ISO certification, also bear in mind how software like manufacturing MRP/ERP-systems can simplify compliance. Modern software can assist in maintaining high-quality records, aid auditing processes, and help increase preparedness for the unexpected at affordable price points. For example, a number of MRPeasy’s clients have noted that their ISO certification process was hugely simplified thanks to having integrated their manufacturing processes with the software.
Key takeaways
- ISO standards are guidelines set by the International Organization for Standardization (ISO) to ensure the quality, safety, efficiency, or other parameters of certified systems and processes across various industries.
- The chief benefits of ISO certification for manufacturers encompass improved quality assurance, reduced risks, heightened operational efficiency, and more. Achieving certification also helps to instill trust in customers and often gives the company a competitive edge in distinct markets.
- The certification process of ISO standards begins with evaluating existing systems and developing an implementation plan, after which a certification body conducts an audit to ensure conformity. Regular surveillance audits are also conducted to ensure continued conformity.
- The most important ISO standards for manufacturers include quality management related ISO 9001, occupational health and safety oriented ISO 45001, environmental management oriented ISO 14001, and energy management system oriented ISO 50001.
- A host of industry and sector-specific ISO standards also exist that can be crucial for manufacturers depending on their niche and target markets like food safety, medical devices, manufacturing engineering, etc.
Frequently asked questions
While ISO 9001 is exceedingly popular among manufacturing businesses, this quality management system-oriented standard is applicable to any type of organization that wants to maintain high-quality processes and improve its ability to meet customer and regulatory requirements.
ISO 45001 is designed to mitigate risks and prevent injuries in the workplace. It emphasizes creating a framework to identify potential hazards, assess risks, and implement controls for a safer workplace. Meeting ISO 45001 requirements may well lead to fewer accidents, lower insurance costs, and reduced legal liabilities.
ISO standards are crucial in the manufacturing industry by providing globally recognized frameworks for quality, efficiency, safety, and other business aspects. By adhering to these standards, manufacturers can improve their operations and efficiency, gain a competitive edge, and access new markets where ISO certification is a requirement or a significant advantage.
You might also like: 7 Real-Life Manufacturing Challenges Resolved with MRP Software