Flow Production – A Quick Guide for SMEs
Flow production means your manufacturing line rarely, if ever, stops. Materials enter at one end and finished products come out the other in a continuous stream. This continuous production method keeps operations moving fast while cutting waste and maintaining quality.
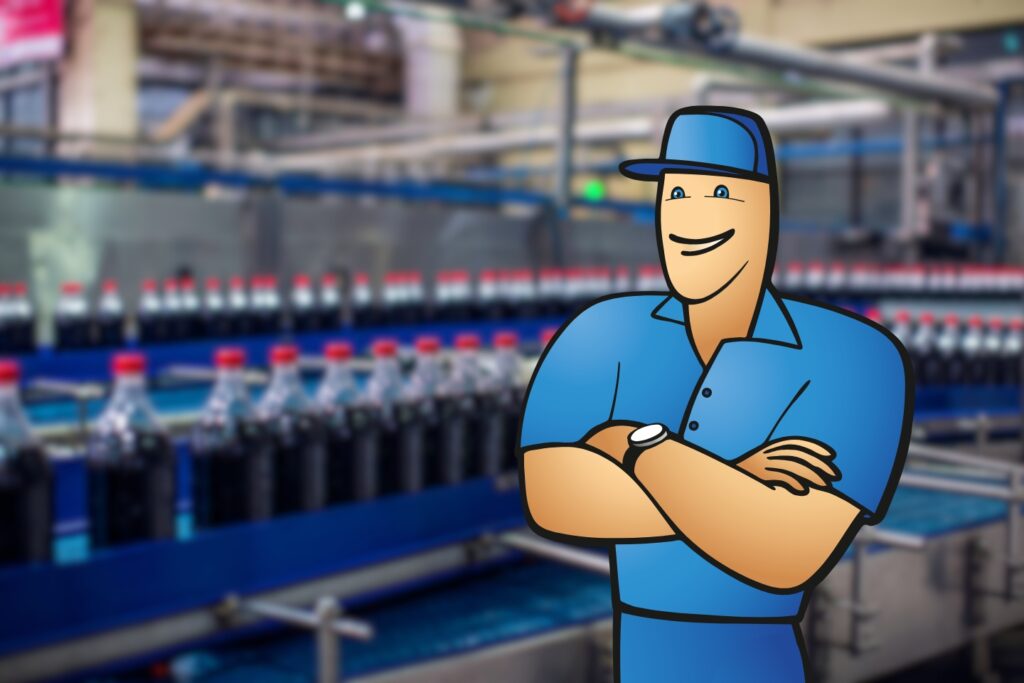
What is flow production?
Flow production is a type of manufacturing method where large quantities of product move continuously from station to station without stopping or waiting around. Picture an assembly line workflow. Each worker handles one specific job, finishes it, and immediately hands the product to the next person. No delays, no piling up parts between steps. In many cases, one machine hands off the product to the next.
Three things make flow production successful:
Continuous material movement. Parts keep moving instead of sitting around collecting dust. It could be assembly line conveyor belts, automated guided vehicles, or just workers carrying items to workstations. It doesn’t matter as long as everything stays in motion.
Standardized processes. Every flow production operation follows identical steps every single time. No variations, no shortcuts, no “we’ll figure it out as we go.” This consistency keeps product quality predictable and prevents one workstation from falling behind and jamming up the whole line. It also allows the manufacturer to take advantage of the economies of scale where production prices decrease as product quantities increase.
Balanced timing. Each workstation takes roughly the same time to complete its task. Otherwise, you get bottlenecks that shut down everything downstream, delaying the completion of finished goods.
The key to production volume is making lots of identical products and maintaining product quality by breaking the work into simple, repeatable steps. It works great for car assembly, food processing and packaging, and electronics manufacturing. It doesn’t work for custom fabrication or low-volume specialty products.
Flow production systems vs. process manufacturing vs. batch manufacturing
Flow production is often conflated with other types of manufacturing processes where products move through the process in stages. Here are the differences between flow production, process manufacturing, and batch manufacturing.
Flow production systems keep individual products moving continuously through workstations. Each unit gets processed separately as it moves down the production line. Take automotive assembly. Each car moves down the line getting doors, engines, and wheels added at specific stations at specified intervals. The cycle times are repeatable and consistent. Waiting times between cycles are relatively nonexistent as the workflow is streamlined to optimize throughput.
Process manufacturing means transforming raw materials through chemical or physical processes. This entails mixing, heating, reacting, and blending bulk materials into something totally different. Beer brewing, oil refining, and paint manufacturing are prime examples. While aspects of flow production can also be used in process manufacturing (e.g. in a bottling station, where bottles are filled, capped, and labelled continuously), process manufacturing doesn’t usually involve individual products moving through workstations.
Batch production creates a set quantity of similar or identical products. Then everything stops to switch setups for the next batch. Consider a bakery that makes French bread loaves. They have to clean all the equipment and replace the molds before switching over to my favorite product, blueberry cupcakes.
Here’s how these production processes compare in the real world:
Volume and flexibility: A flow production approach needs high, steady throughput volume to justify the investment. Batch production handles medium volumes with product variety—widgets in the morning, gadgets in the afternoon. Flow manufacturing locks you into making the same thing repeatedly. Process manufacturing works for anything from small specialty batches to massive continuous runs.
Inventory and labor: Continuous flow makes inventory management easier because materials move constantly. This method uses the least labor per unit once it’s running smoothly. Batch production creates inventory spikes when runs finish. Batch operations also need more hands-on work for loading, unloading, and changeovers that contribute to production downtime.
Pros and cons of flow production
Look, continuous production manufacturing can deliver impressive results when implemented correctly. But it’s not right for everyone. The challenges are real enough to give careful consideration. Success or failure usually comes down to whether you understand what you’re getting into before committing to major—sometimes expensive—changes to your assembly line. Mass production requires careful planning to implement effectively.
The advantages are compelling
Operating costs drop 15-25% typically. You eliminate waste in multiple ways—less material handling, better equipment utilization, fewer quality problems. Materials move efficiently instead of sitting around tying up cash.
Production speed improves dramatically. Most operations see production time drop 50-70% compared to batch operations. No more stop-and-start cycles where everything halts between batches. Each component follows a rigorous just-in-time arrival schedule for each workstation.
Quality gets much better. Defect rates often fall 90% because you catch problems immediately. When something goes wrong, you see it right away and fix it before affecting more products. Compare that to batch production where you might discover problems after making hundreds of bad parts.
Equipment utilization improves. Machines run consistently instead of sitting idle between batches. Workers stay productive instead of waiting around.
The challenges are significant
High startup costs hit immediately. Setting up flow production lines can require serious upfront investment: specialized equipment, automation systems, facility modifications. The numbers add up quickly, especially with training and debugging time.
Limited flexibility becomes obvious. Changing products is difficult and expensive because everything’s optimized for one specific manufacturing process. Market changes or customer requests for variations create real headaches.
Single point failures shut down everything. When one station goes down, the whole production line stops. Unlike batch operations where you might work around broken equipment, continuous flow creates production time dependencies that can halt everything. I saw this personally in poultry processing operations where a steady throughput was essential.
Workforce changes don’t affect everyone the same way. The human element remains one of the biggest variables in any manufacturing transition. Workers need time to develop skills for automated systems. Some workers struggle with the constant repetition and split-second timing that automated systems require. Training takes considerable time and money, and you’ll likely still see some people leave who simply prefer the old way of doing things.
Conduct an honest assessment of your current workforce and infrastructure before committing to continuous production manufacturing. Each facility has unique constraints that affect success.
Risk mitigation strategies
The manufacturers who succeed long-term think ahead. They know that continuous manufacturing brings unique challenges. They develop strategies to handle them before problems happen.
Equipment problems hit differently in continuous manufacturing. Instead of affecting just one batch or process, a breakdown can stop your entire operation. That makes maintenance management and monitoring systems essential rather than nice-to-have.
The technology keeps getting better at spotting trouble early by tracking vibration changes, temperature shifts, and performance patterns that signal equipment stress before it turns into expensive downtime.
Markets associated with flow production
Flow production works best in specific markets with predictable characteristics.
High-volume consumer goods represent the sweet spot. Food processing and pharmaceutical production both find continuous flow manufacturing beneficial. These industries have standardized products, predictable demand, and product quality requirements that this production method handles well.
Heavy industries with continuous processes also succeed with continuous flow approaches. Steel manufacturing, oil refining, cement production, and paper manufacturing use flow principles because stopping and starting is expensive and technically difficult. They lend themselves easily to lean manufacturing principles.
Assembly operations across industries work well with continuous flow approaches: assembling automobiles, appliances, machinery, and consumer products. Basically, anything where you’re adding components in sequence.
Here’s the pattern: Companies with stable products, high-volume production, and quality-sensitive customers benefit most.
Companies dealing with custom products, variable demand, or frequent engineering changes? They struggle with continuous flow constraints.
What works in different industries
Automotive pioneered most continuous manufacturing concepts that other industries borrowed. Toyota’s kanban-driven production system became the gold standard, but successfully implementing it means understanding both the technical changes and the cultural shift involved.
Food processing had to adapt continuous flow to handle perishable materials and strict safety requirements. Flow production makes better temperature control and contamination prevention possible.
Electronics manufacturing uses this process for high-volume consumer products. Automation handles precision requirements while flow principles manage the complexity of thousands of components per device.
Pharmaceuticals increasingly adopts flow production for better quality control and reduced contamination risks. Regulatory agencies now encourage this production method because it offers better process understanding.
Is flow production suitable for SMEs?
Small and medium-sized manufacturers face unique challenges when planning for flow production, but it can be a viable option.
Investment realities for smaller companies
Most SME flow production implementations require $500,000 to $5 million upfront. That includes equipment, automation, facility modifications, and training. For smaller companies, that’s often make-or-break money.
But financing options have improved. Equipment leasing spreads costs over time. Government incentive programs often subsidize manufacturing modernization. Some vendors offer performance-based contracts where payments depend on achieving productivity improvements.
Modular approaches work better for SMEs than complete system overhauls. Start with manual production lines using basic material handling. Add automation gradually as volumes and confidence increase. Each phase should pay for the next phase through improved efficiency.
Volume thresholds typically start around 10,000 units annually for simple products, but this varies by complexity. Electronics assembly might work at lower volumes due to automation potential. Heavy machinery requires much higher volumes to justify dedicated production lines. In this case particularly, raw materials inventory management is critical.
Success strategies for smaller manufacturers
Start small and prove the concept. Pick your highest-volume, most stable product line for pilot implementation of continuous flow production. Learn the technology and train people before expanding.
Partner with experienced vendors who understand SME constraints. Regional integrators often provide better support than large international companies because they respond quickly to problems.
Focus on workforce development. In smaller organizations, every person matters. Cross-training becomes essential because you can’t afford specialists for every function.
Track the right metrics. Focus on spotting problems quickly instead of sophisticated analysis. Modern cloud-based ERP systems and low-cost sensors make real-time monitoring affordable for small companies, but keep it simple and actionable.
Small companies that succeed with continuous flow manufacturing build capabilities gradually. The failures usually try to do too much too fast.
Supporting flow production with manufacturing ERP
Flow production demands software that can keep pace with continuous operations and provide real-time visibility.
Critical software capabilities
Material requirements planning must be more precise than traditional weekly buckets. This manufacturing process often requires daily or hourly precision for optimal lead times. Advanced systems use real-time consumption data to trigger material replenishment automatically.
Quality management needs to capture data at each process step instead of waiting for final inspection. Statistical process control spots trends before they create defective products. You get complete traceability linking finished products back to specific materials and process parameters.
Capacity planning becomes a balancing act between customer demand and production capabilities while keeping flow efficiency. Finite capacity scheduling prevents you from overloading bottleneck operations that would mess up the whole production process.
Integration requirements
Manufacturing Execution Systems (MES) collect real-time data from equipment and feed it back to update production status automatically. The production process requires immediate feedback when operations fall behind or quality drifts. Automated alerts notify supervisors when intervention is required.
Modern data collection systems give you visibility you’ve never had before, monitoring equipment performance and process parameters around the clock. Automated data processing provides immediate feedback while sending summaries to enterprise systems for analysis.
Implementation considerations
System selection should focus on manufacturing-specific functionality rather than general business features. Look for real-time data collection, shop floor integration, and mobile access for production personnel.
Training requirements need special attention because production personnel have limited classroom time. Just-in-time training delivered when workers need specific functionality often works better than comprehensive upfront training.
Don’t overcomplicate the software side. Match system complexity to what you actually need. Some companies blow millions on sophisticated systems they never fully use. Others succeed with simple solutions that solve specific problems.
The bottom line: Plan carefully, build gradually
Continuous flow manufacturing can absolutely transform your manufacturing operation. But here’s the reality. You need to be brutally honest about your situation, expect both wins and headaches, and plan this thing carefully. Keep on the lookout for areas where you can streamline and optimize your operations.
The manufacturers who pull it off know their limits and build up their capabilities step by step.
Key takeaways
- In flow production, products move seamlessly from one workstation to the next without stopping, minimizing delays and reducing waste. It’s ideal for high-volume, standardized production.
- Three elements drive success: continuous material movement, standardized, repeatable processes, balanced timing across workstations to avoid bottlenecks.
- Compared to batch and process manufacturing, flow production offers higher efficiency and quality for repetitive, high-volume products—but sacrifices flexibility and adaptability.
- High upfront investment in automation, layout redesign, and staff training is required. But once in place, it slashes operating costs and boosts quality and speed.
- It suits industries with stable, high-demand products, like automotive, food processing, electronics, and pharmaceuticals. It’s not ideal for custom or low-volume manufacturing.
- Starting with a modular approach, selecting the right product line, and focusing on simple, phased implementation with solid ERP support increases the chances of success.
Frequently asked questions
If you’re producing at least 10,000 units per year of the same or very similar product, flow production may be worth considering. The more standardized and stable your demand, the more value you’ll get from the efficiency gains.
Start with your highest-volume, most stable product line and map out the current workflow. Then reorganize the layout for smoother flow, reduce unnecessary handling, and introduce standard operating procedures before considering automation.
Yes, but it requires more advanced planning, modular workstations, and flexible tooling or automation. It’s doable with the right ERP system and production scheduling—but it adds complexity and reduces some efficiency.
You may also like: What Is Closed-Loop Manufacturing?