Home Furnishing Innovator Deploys MRP Software Across Two Companies at Once
When a simple stock management system and a tangle of spreadsheets no longer supported his growing operations, Pennsylvania-based entrepreneur Robert Ogden knew it was time for a change. What followed was a double-implementation of MRP software that unlocked a new level of accuracy and collaboration.
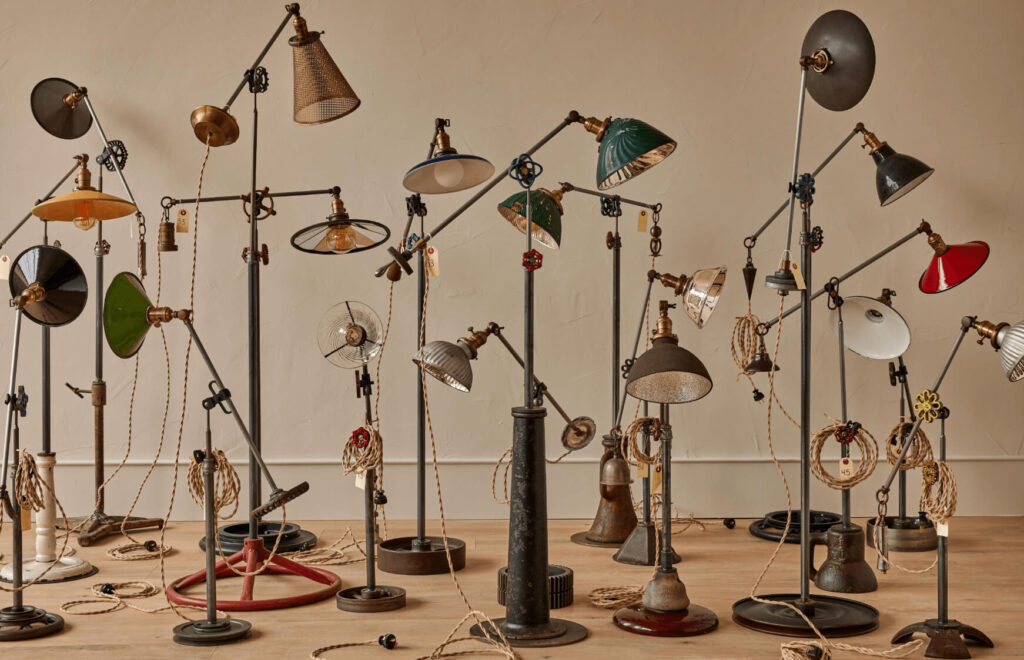
From garage startup to manufacturing success
RTO Lighting is a high-end custom lighting company from Pennsylvania. It specializes in designing and manufacturing high-quality custom light fixtures that blend artistic design with superior craftsmanship. Robert Ogden founded the company in 2002 as a side project to provide himself with a creative outlet for exploring custom lighting solutions. After a humble start at Robert’s home garage, RTO Lighting has grown into a sizeable operation.
In 2008, Robert and his wife acquired Lostine – a home furnishing company where the couple had previously worked as designers. Lostine offers a variety of high-end products, from mirrors and furniture to kitchen accessories and vintage-inspired home accents. Much like RTO Lighting, Lostine has become a well-known brand in the premium home furnishings market. Despite their separate identities, RTO Lighting and Lostine share a unique synergy and often manufacture products for each other.
Driven by the owners’ vision of producing high-quality, sustainably sourced, heirloom-worthy products proudly crafted in the USA, the businesses grew from a small initial team of seven to a combined workforce of nearly 60 full-time employees across both companies.
Growing businesses require scalable solutions
Operating two distinct yet interconnected businesses presented Robert and his wife with unique challenges, particularly in managing inventory, production schedules, and labor costs. For years, they juggled multiple tools, using a basic stock management platform for material tracking and a host of spreadsheets for costing and production planning. As the companies grew, the patchwork solution started showing its limits. Buckling under the pressure of inefficiency, the companies finally realized that a more robust solution was needed.
The turning point came when Robert noticed neither company could track labor costs or quote lead times accurately. “We had started using a stock management system, but realized that it doesn’t track time in manufacturing or labor. As a manufacturer, we needed to capture time as an expense, to quote lead times, and to know our costs more accurately,” Robert explains.
As the need for a unified system to provide efficient inventory management, labor and cost tracking, and production scheduling became increasingly urgent, management started looking for a suitable software solution to support the growth of the companies.
Discovering MRP systems and the decision to implement
At first, Robert was unsure what type of software to focus on in his search. Thankfully, a CRM software’s sales rep pointed him in the right direction. Recognizing that a CRM system couldn’t meet RTO Lighting’s needs, the salesman provided a list of MRP systems to look into, among them MRPeasy.
MRPeasy’s user-friendliness and comprehensive production scheduling capabilities immediately impressed him. “When I looked at how easily you could manipulate the production calendar in MRPeasy, I thought it was perfect. I showed it to my team, and everyone agreed once they saw the ease of use,” Robert recalls.
Other key factors in the decision were MRPeasy’s effortless labor tracking and accurate cost and lead time estimating features, promising to accurately analyze margins per product. He also found that MRPeasy had full built-in support for RTO Lighting’s preferred accounting platform, QuickBooks, which gave him the confidence to proceed.
“MRPeasy seemed capable of solving all of our needs for material requirements planning and offered functionalities that we didn’t even know we needed at the time of implementation, yet are using daily now,” Robert shares.
Challenging double implementation paid off in spades
Robert’s initial plan was to implement MRPeasy only in RTO Lighting. However, he quickly realized that managing two different manufacturing and purchase order systems alongside each other would be too cumbersome and unintuitive. Thus, he made the bold decision of implementing MRPeasy in both companies simultaneously.
While the original plan was to implement MRPeasy in RTO Lighting first, Lostine managed to go live with the new system a whole month sooner. While coming with its challenges, the double implementation proved beneficial overall as both companies supported each other, sharing knowledge and solving challenges together. This collaboration also proved instrumental in easing the learning curve and ensuring a smooth transition for both teams.
The process took around eight months in total, four of which were parallel testing with the old systems to ensure everything was accurate before continuing exclusively with MRPeasy. Robert initially thought one person could handle the implementation, but it eventually required the attention of two employees. Reflecting on the experience, Robert notes: “I wish I had put two people on it full-time from the start. It was a bigger task than we anticipated, but the benefits far outweighed the challenges.”
Robert also engaged with an authorized MRPeasy consultant to speed up the process and provide further guidance.
MRPeasy not just informs on lead times – it shortens them
Since successfully implementing MRPeasy in spring 2023, RTO Lighting and Lostine have reached heightened operational efficiency. The software has transformed many aspects of their manufacturing process, from accurate labor tracking to real-time inventory management and precise cost calculations.
Two full-time employees use MRPeasy daily—one handles order management and scheduling, and the other is responsible for procurement. However, the whole team benefits from the software and the data it offers, and has adapted to using it very well.
MRPeasy is allowing both companies to not only accurately predict lead times but also shorten them, thanks to time saved on managerial tasks. Labor utilization has also seen a significant boost, as has material tracking accuracy.
Robert describes the impact: “MRPeasy is a powerful and necessary tool for manufacturing. It’s like a forklift – when you finally buy your first one, you quickly wonder how you ever lived without it!”
Comprehensive is best when implementing manufacturing software
Reflecting on the implementation process, Robert points out that underestimating the time and resources needed for implementing an MRP system is probably one of the biggest mistakes a company can make. Looking back, he strongly advises allocating sufficient manpower – at least two employees familiar with the company’s production system, to ensure a smooth and efficient process.
Beyond internal resources, he also highlights the value of seeking outside expertise. RTO Lighting and Lostine both worked with external consultants who helped accelerate implementation and provide deeper insights into best practices. Robert recommends other manufacturers considering an MRP system not to be afraid to ask for help—whether through software vendors, consultants, or industry peers.
Robert is an active member of Makers Alliance, a network of 50 small to medium-size American manufacturers. Within this group, he has shared his MRPeasy experience and has seen firsthand how manufacturers benefit from learning from one another. He even hosted a fellow alliance member who came to observe their setup—proof that sometimes the best insights come from those who have already been through the process.
Roberts’s final piece of advice is to always keep the bigger picture in mind: “Accurate data leads to better decision-making. Understanding profit per square foot, per hour of labor, and material usage allows us to maximize capacity utilization and optimize efficiency. Investing in the right system—and the right people to implement it—has been a game changer for us.”
You might also like: MPW Precision cuts a short path to success with day-one MRPeasy implementation