MRP System Series #1: What is MRP?
This is our first post in the series explaining the concepts surrounding MRP system.
MRP is a term that can be understood in many ways. We’ll try to shed some light on the history and relevance of the term and the characteristics of the MRP systems.
(Funnily, the answer to “What is MRP?” depends on the age of the respondent. Read on, and you’ll understand why.)
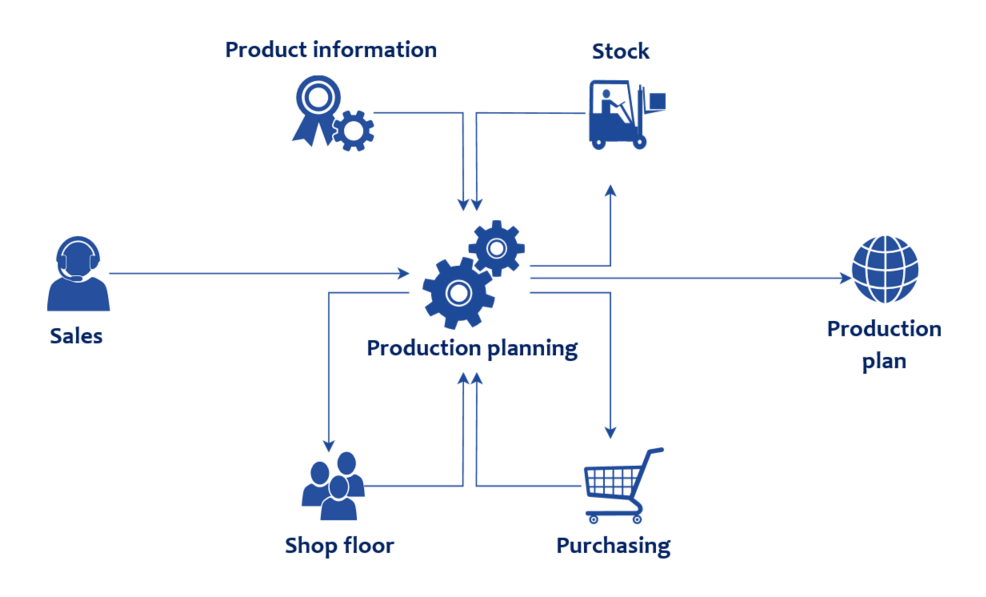
MRP was one of the first manufacturing software systems designed to increase productivity with the help of computers. It has led to great improvements in production efficiencies.
In general, MRP is a method for company management, which allows management to accurately and efficiently plan the company’s resources in terms of materials, equipment, and workforce. Even though MRP could be applied manually, it’s unthinkable without MRP software.
MRP can be applied to any kind of production: Make-to-stock or make-to-order, for simple products to complex products with sub-assemblies, where components are produced in-house, or even to managing outsourced production.
Inventory management, the processing of bills and materials and scheduling are the very basic functions of an MRP system. One of the primary goals of MRP is helping organizations maintain low inventory levels. Mainly, it is used to plan production, purchasing and delivering activities.
Nowadays, the term MRP is mainly understood as Manufacturing Resource Planning (aka MRP II), which allows for very accurate planning and management of resources. When it first emerged, MRP was coined Material Requirements Planning (aka MRP I).
Historically, most formal practices before the introduction of MRP were mainly only applicable for big manufacturers whose series produced standardized products year-after-year. Those methods mostly fell short in changing environments, or for smaller manufacturers with many or custom products, for which market demand cannot be easily predictable. In turn, this resulted in keeping higher inventory levels and more materials and products were obsolete since market demand changed.
To counter this, new manufacturing inventory management software emerged – Material Requirements Planning (aka MRP I). This enabled more accurate production and inventory planning based on demand. The greatest benefit was minimizing inventory (and waste also!) through highly accurate planning, which would have required enormous effort done manually.
(We could argue if MRP is for inventory management or for production planning, while it really is for both. If your job title has the word “inventory” in it, use the former… if “production,” use the latter!)
MRP I – Material Requirements Planning
Joseph Orlicky developed the concept in 1964 and the first company to utilize it was Black & Decker. This was just the time when computers slowly started dominating the industry.
Compared to today’s MRP systems, due to computational limitations, MRP I was a much more simplistic production planning and inventory management software. It wasn’t very integrated for live data collection from various parts of the company.
It was designed to answer a few central questions: What should be purchased? How many? When?
The main data inputs were:
- The produced items, bills of materials and production details (i.e. the routing)
- The material items and their lead time.
- Sales demand, a sales forecast, or a master production schedule
The main data outputs were:
- Recommendations as to what should be purchased.
- A basic production schedule when different production runs should start, without regard to actual machine capacity (infinite capacity is assumed)
The main benefit is that thanks to computers, a clear production schedule, and purchase requirements emerge with relative ease. Alternatively, this would take many hours-to-days for a team of planners for complex products (or just many parts and products!).
The greatest disadvantage is that the MRP I system is not very integrated, and, for good results, the data needs to be constantly updated. In addition, it does not provide such an accurate production schedule based on individual machine capacity, nor does it manage important manufacturing financials like product costing.
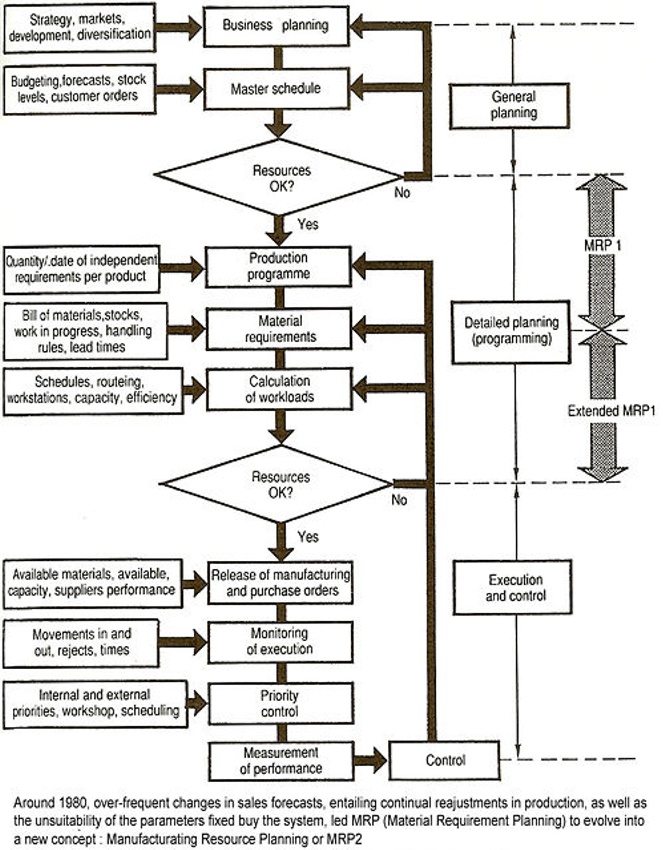
MRP II – Manufacturing Resource Planning
Manufacturing Resource Planning emerged in the 1980s when the MRP I systems were improved and integrated with other business applications. Therefore, a Manufacturing Resource Planning system is an integrated system, where many different operations within a manufacturing company are brought together into one, unified MRP system. It’s no longer just an application for one purpose.
Two of the biggest improvements of MRP II are
- The capability to produce a highly accurate production schedule by considering the production capacity.
- Live feedback information from the shop floor, reporting, and other functions, like inventory management, sales, purchasing etc.
All different departments in the company interface the same software in real-time – the salesperson, purchaser, stock clerk, production planner, shop-floor worker, engineer… they all have a common platform where they conduct some of their work.
Since everyone is using the same system at the same time, compared to MRP I, the data in the MRP II system is of much better quality. Data simply does not need to be carried from one system to another – while being the purchasing and sales software, it is also the inventory management software, manufacturing software, production scheduling system and much more.
What does this mean for production planning?
- Besides letting you know what should be purchased, the MRP II system can, itself, plan the capacity of all work stations, providing a detailed production schedule. Answering the question, “When will the products be ready?”
- Since material purchasing is done within the same system, it answers the question, “What do the materials cost?”
- Since it’s also a manufacturing execution system where workers do production scheduling and reporting, it also answers the questions, “What is the current situation on the shop-floor?”
- And importantly, also based on reported information, “What is the production cost?”
- Since sales are also managed from the same system, it greatly facilitates on-time delivery and shipment planning. Plus, it answers the critical questions, “How to price the quote?” “When can I deliver?” and “How much will the company profit?”
- And much more, depending on the specific way the MRP system has been built.
As many functions can be carried over to the MRP system, it greatly facilitates production planning and manufacturing execution. It is easier to manage the financials, there’s up to date information about inventory balance, exact product costs and reporting.
A modern MRP system is an Enterprise Resource Planning system – an MRP ERP system – not only a module like MRP I used to be in its infancy.
MRPEasy is also manufacturing software like this, designed to organize your production and give you all the information you need.
Manufacturing Inventory Management before MRP systems
Before the MRP concept, the main methods that were used in manufacturing inventory management were simply reactive or relied heavily on statistical data. For example, Reorder Point/Reorder Quantity, or Economic Order Quantity, methods that are more than 100 years old.
Reorder Point – Reorder Quantity
The Reorder Point method uses material consumption averages to estimate the minimum stock level for when to order new materials. It does this based on historical consumption rates so you wouldn’t run out of stock before new materials arrived. And the Reorder Quantity, calculated based on historical consumption, is the quantity you should purchase so you would survive until the next purchasing cycle.
Sounds like a good tactic? Yes, in very limited situations. But not very good if the production schedules vary, it’s make-to-order, there’s need for agility, market changes, etc. In these scenarios, this method will bring heightened inventory levels with parts and products that will never see the market.
Economic Order Quantity
The Economic Order Quantity is a method for minimizing the holding and ordering costs per item. It reports what is an optimal order size, from the perspective of financial management. The central idea is not about keeping a minimal inventory or having efficient production planning. This method can only be applied in a very constant production environment, where planning is done by long time frames (e.g. one year at a time).
The greatest weaknesses of these methods are that they do not consider the future needs of production, which change by market demand, or neither do these try to minimize inventory. The presumption is constant and uniform demand (based on historical data).
Of course, it is possible to apply these methods in today’s world, but it is not so straightforward, nor elegant as it might seem in the first place.
MRP system series:
MRP System Series #7: The right attitude for MRP system implementation
MRP system Series #6: Implementing Manufacturing Software. Benefits from Process Changes
MRP System Series #5: What Makes a Good MRP System?
MRP System Series #4: How Much Detail to Input into the MRP System?
MRP System Series #3: Top 5 Mistakes in Implementing Manufacturing Software
MRP System Series #2: What is the difference between MRP and ERP?
MRP System Series #1: What is MRP?