What is Continuous Production? A Simple Guide
Continuous production has been a buzzword in the manufacturing sector for years. In this simple guide, we unpack its meaning, weigh its pros and cons, and explore whether it’s a viable option for small and medium enterprises.
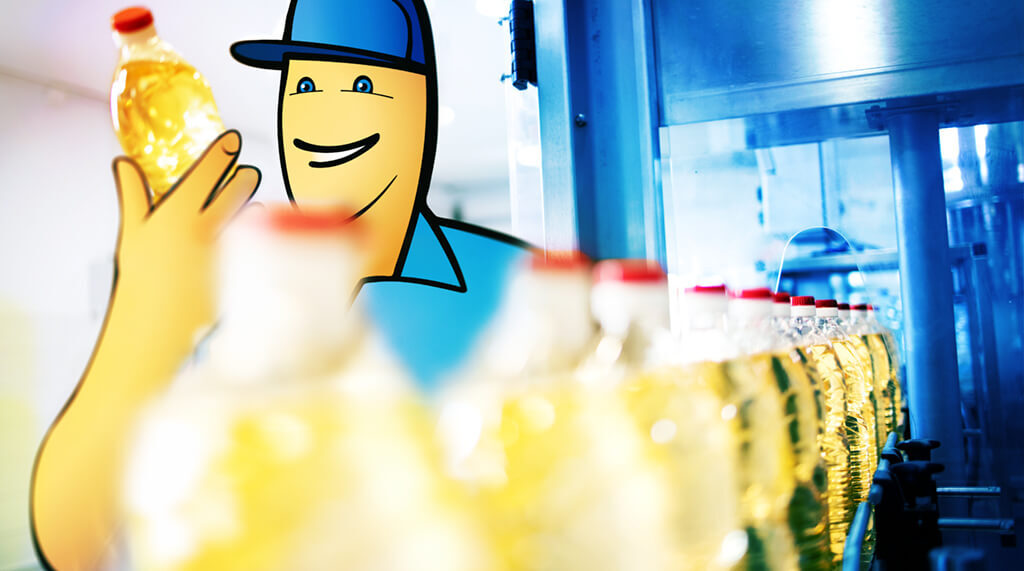
You can also listen to this article:
What is continuous production?
Continuous production is a manufacturing process designed to produce finished goods in a continuous flow without interruptions in the production line. The term is often used synonymously with continuous manufacturing or flow production. A flow production method signifies a production line set up so that raw materials enter at one end and finished products come out at the other, with zero or minimal stops or changeovers.
Continuous production relies heavily on automation, from handling materials and moving sub-assemblies between phases of the production cycle to quality control and even packaging. As setting up is complex and time-consuming, continuous production usually aims to produce high volumes of standardized products while minimizing downtime.
Traditionally, continuous production has been the backbone of industries such as steel manufacturing and oil refining which require around-the-clock operation due to the nature of the raw materials or processing required to treat them. Advancements in modern manufacturing technologies are extending the reach of continuous workflows to other sectors like food and beverages, the pharmaceutical industry, and even discrete manufacturing applications.
Thanks to the rising accessibility of automation, real-time monitoring systems, and powerful manufacturing software, even smaller manufacturers can increasingly integrate continuous manufacturing processes.
Continuous production vs. process manufacturing vs. batch manufacturing
While similar in some ways, continuous production is not analogous to process manufacturing or batch manufacturing.
Process manufacturing refers to the manufacturing technology used rather than the setup of the production or assembly line. Contrasted with discrete manufacturing, process manufacturing is characterized by mixing, boiling, or otherwise combining ingredients and materials in chemical or physical “processes.” It deals with formulas and recipes rather than bills of materials used in producing distinct units. A continuous production workflow may technically be set up in either the process or discrete method or even a mix of the two.
Batch manufacturing or batch production, on the other hand, refers to a production setup in which identical goods are created in set quantities or “batches.” For example, a bakery that produces 50 loaves of bread at a time. Some continuous manufacturing workflows can also be programmed to produce goods in batches for reasons like quality control or shipment tracking. However, the two production methods are distinct in the sense that a continuous workflow doesn’t constitute a finished production run after producing a batch of product. Even if in batches, a continuous production line will produce identical goods continuously, until it’s reset.
The pros and cons of continuous production
As with anything, continuous production comes with its own pros and cons that we will look at next.
Advantages of continuous production
One of the most significant benefits of continuous manufacturing is the increased production rate. With minimal downtime, factories can output large quantities of standardized products and ensure high turnover. Additionally, the use of high-level automation not only speeds up the production process but also contributes to worker safety by minimizing manual labor risks.
The other chief advantage is cost efficiency. Reduced labor costs and a streamlined workflow make it an economically attractive production method where applicable. The high degree of automation also provides more consistent quality control as real-time monitoring and process analytical technology enable complete control over any changes, helping to maintain meticulous product standards.
Challenges of continuous production
The complexity of setting up a continuous production system is usually very high. It demands a deep understanding of different technologies and a highly skilled workforce. The inherent nature of continuous production also makes it resistant to change. Implementing even minor adjustments to the production line can require a complete system overhaul, incurring additional costs and time.
Customization is another significant downside. The system is primarily designed for high-volume, make-to-stock production, so it usually doesn’t allow for product variations or customization. Instead, changes to the recipe or a workstation often necessitate halting the whole production line to make adjustments or re-engineer sequences.
Finally, the level of initial investment required in designing and implementing continuous production lines is very high. Continuous manufacturing can only truly be cost-effective with consistently high demand for the finished goods. Sudden dips in demand or disruptions in outgoing supply chains might lead to a rapidly growing excess of inventory. This can rapidly spiral a company’s finances out of control, forcing difficult financial decisions: stop the production line, quickly increase storage space availability, lower the product price, etc.
Markets associated with continuous production
Here’s a list of some of the more common sectors utilizing continuous manufacturing:
- Oil refineries. One of the earliest adopters of continuous production, oil refineries require a system capable of meeting consistent, high-volume demand. The production process is sequential, converting crude oil into an array of petrochemical products, from gasoline to plastics. The intricacies of refining different components without shutdowns make continuous production a natural fit.
- Paper and fabric manufacturing. In these industries, continuous production is critical for pumping out large rolls of paper or fabric. Raw materials like wood pulp for paper or fibers for fabric are processed through various stages. These include breaking down, treating, and reconstructing them into sheets or textiles. The end-to-end process is engineered for minimum interruptions, often making continuous production advantageous.
- Cement manufacturing. Cement plants operate based on a continuous flow of raw materials like limestone, clay, and shale. The market often demands large quantities of consistent quality, making continuous production a suitable choice. From grinding the raw materials to heating them in kilns and finally producing clinker, the process is a carefully coordinated sequence.
- Steel. Another stalwart of continuous production, the steel industry relies on this method for creating high-quality, standardized products. The journey from iron ore to finished steel involves several stages, including smelting, refining, and casting. The continuous production system ensures that the output meets the constant market demand for construction materials, automobiles, appliances, etc.
- Foodstuffs production. The food production sector frequently uses continuous processes, whether kneading large volumes of dough for bread, extruding pasta shapes, or grinding peanuts into butter. This ensures the product’s quality control standards are met while satisfying the ever-present consumer demand for foodstuffs.
Is continuous production suitable for SMEs?
As noted, continuous production has traditionally been associated with large-scale operations. However, new technologies and manufacturing types are opening up the possibility of adopting continuous processes to a wider range of businesses in diverse sectors. Small and medium enterprises (SMEs) face a pivotal decision when considering continuous or semi-continuous workflows. The high setup costs and complexities associated with continuous production systems often act as barriers. Then again, increased production rates and greater quality control can be powerful advantages in some markets.
Adopting the right manufacturing software, like a capable MRP system, can significantly affect this decision. These technologies can provide the automation and real-time monitoring required to make continuous processes feasible. On the other hand, SMEs may also find that batch manufacturing offers more flexibility and lower upfront costs, making it a more suitable option for smaller operations with varied product lines.
When considering adopting a continuous or semi-continuous workflow as an SME, we recommend going through this checklist to begin with:
- Gain a deeper insight into relevant supply chains. Existing agreements and contracts should accommodate consistently higher volumes of materials and goods flowing to and from the manufacturing facility.
- Get additional vendors or shippers. What kinds of failsafes are in place for sudden demand loss or supply chain disruptions? Is there potential to quickly increase storage space or lock in a new supplier or shipping contract? How would temporarily lowering the unit price affect profitability?
- Guarantee flexible investors and weigh financial risks. It’s vital to ensure that your financial backers are aligned with the risks and benefits of shifting to a continuous production system. This involves detailed discussions about setup costs, ongoing operational expenses, and potential ROI.
- Thoroughly forecast demand and analyze cost-efficiency. Predictive analytics and market research can help gauge future demand, while cost-benefit analyses can provide insights into the long-term viability of continuous production for your specific setting.
- Automate production and adopt manufacturing software. Implementing a cloud-based manufacturing ERP system brings high value at a low cost. It helps automate large segments of the production process and offers end-to-end traceability, hugely increasing overall efficiency while reducing the chance of human error. Modern solutions are versatile and flexible, capable of accommodating a broad spectrum of manufacturing methods, from batch to continuous.
Key takeaways
- Continuous production is a manufacturing process designed to produce finished goods in a continuous flow without interruptions in the production line.
- Continuous production relies heavily on automation, from handling materials and moving sub-assemblies between phases of the production cycle to quality control and even packaging.
- Advancements in modern manufacturing technologies are extending the reach of continuous workflows to novel sectors like food and beverages, pharmaceutics, and even discrete manufacturing applications.
- The main advantages of continuous production include increased production rate, cost-efficiency, low cost per unit, and quality control.
- The potential disadvantages of continuous manufacturing include highly complex and intricate assembly lines, low or no capacity for customization, long changeover times, and high initial investments.
- Thanks to advances in automation, real-time monitoring, and cost-effective manufacturing software, continuous production is increasingly becoming a viable option for smaller, more agile businesses.
Frequently asked questions
Continuous production lines are ideally suited for industries that require constant, uninterrupted flows and have consistent high-volume demand, such as the chemical, paper, and textile sectors.
Products that typically utilize continuous production methods include oil and petrochemicals, paper and textiles, steel, cement, an array of food and beverage items, and even pharmaceuticals.
The chief advantage of continuous production lies in the cost-efficient production of high volumes of standardized products. On the other hand, disadvantages include little flexibility for product modifications once the line is operational, steep initial investment costs, and a heightened risk of overstocking.
You may also like: Mass Customization – A Viable Option for Small Manufacturers