Industrial Cleaning Equipment Manufacturer Sees ‘Huge Improvements’ After Implementing MRP Software
After a disastrous experience with a different system, Arcus Cleaning Systems found the perfect software to manage their operations. “MRPeasy has been brilliant for us,” says Ryan Brogan, Director.
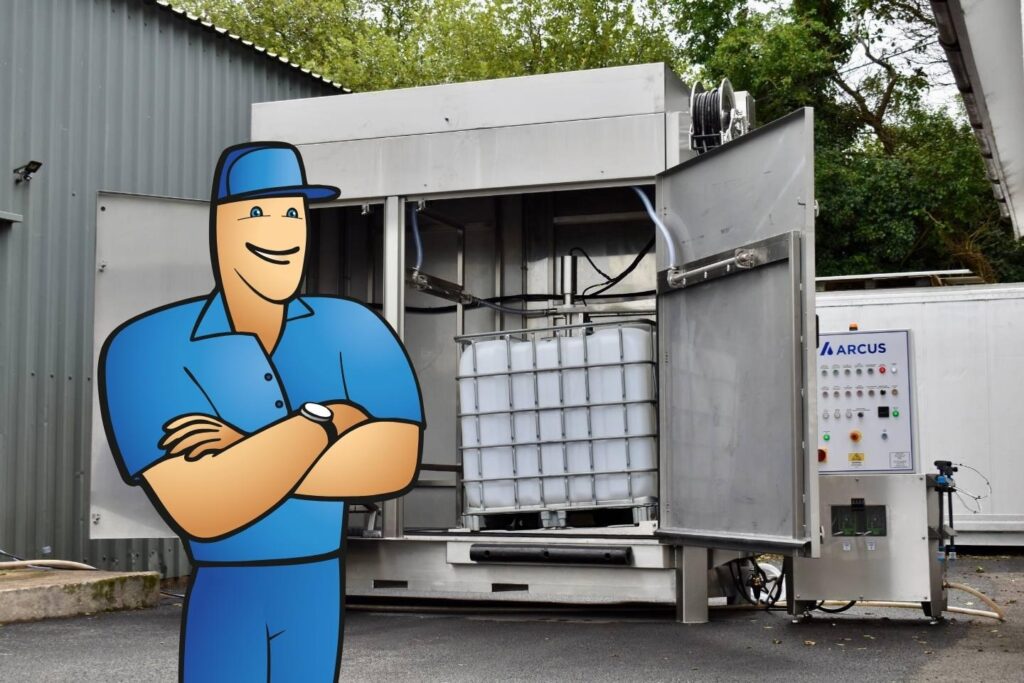
You can also listen to this article:
Specializing in industrial cleaning solutions for niche markets
Arcus Cleaning Systems is a manufacturer and supplier of industrial cleaning equipment based in Lisburn, Northern Ireland. Established in 2019 by brothers Ryan and Connor Brogan, the company focuses on creating tailored solutions for industries with specific cleaning needs. Their portfolio includes tank and container cleaning systems designed to handle anything from 25-liter drums to 1,000-liter intermediate bulk containers (IBCs).
Arcus caters to industries such as food production, chemical manufacturing, pharmaceutical processing, and waste treatment. Their specialized equipment supports low-pressure disinfection and multi-stage washing processes—essential for maintaining stringent hygiene standards.
Initially operating as a two-person venture, the company has grown to include five team members: the two founders and three engineers. The company balances in-house assembly with outsourced metalwork manufacturing, ensuring efficiency without compromising quality.
Recognizing the need for operational transformation
In its early years, Arcus relied on manual systems to manage its production and inventory. Excel spreadsheets were used to track BOMs, purchases, and inventory levels, while flagged emails served as a makeshift procurement system. However, as the company expanded, these manual processes became cumbersome and prone to errors.
“We knew from the start that we wanted an MRP system,” Ryan shares. “But finding one that suited our company size and budget was a challenge. Many systems felt too big or too complicated for what we needed.”
The inefficiencies in their processes began to impact operations, prompting the team to explore software solutions. Their first attempt with an MRP system, however, proved disappointing.
Early challenges with the wrong system
Arcus first found a system known for its simplicity and affordability, but it fell short in key areas. “Its functionality was too rigid for our needs,” Ryan recalls. “We assumed it would adapt to our operations, but it was quite the opposite.”
The tipping point came when a stock system update wiped out months of data, leaving the team frustrated and without recourse. “We spent weeks trying to recover the lost information,” Ryan says. “It was a costly and stressful experience.”
After this setback, Arcus resumed their search for a more reliable solution.
Discovering the perfect fit for a growing company
Through online research, Ryan and his team found MRPeasy. The positive reviews and the modular design of the software convinced them to give it a try.
“MRPeasy stood out because it was scalable and straightforward,” Ryan notes. “It had all the core functionalities we needed without the unnecessary complexity of larger systems.”
An additional benefit was MRPeasy’s compatibility with Arcus’s two distinct business operations: their Arcus Cleaning Systems brand for manufactured products and their 23B Solutions division for parts and pump supply.
“We operate both brands under one system, and MRPeasy handles it seamlessly,” Ryan explains.
A smooth and collaborative implementation
Drawing on their previous experience, the team approached the implementation methodically. Connor’s fiancée, who specializes in process documentation, played a key role in creating SOPs tailored to the system.
“MRPeasy’s online resources were also invaluable,” Ryan says. “We had quite a few questions, but the online guides and manuals made it easy to figure things out.”
The implementation process, which included data migration, SOP development, and staff training, took approximately five to six months. Despite balancing the setup with day-to-day operations, the team found the process straightforward.
“Compared to our previous experience, MRPeasy was night and day,” Ryan remarks. “The support team was responsive and genuinely helpful. Every issue we raised was resolved quickly and accurately.”
Huge improvements in purchasing and inventory tracking
Since adopting MRPeasy, Arcus Cleaning Systems has seen dramatic improvements across multiple areas of their business. Some of the most significant advancements have been made in the purchasing process.
“Our purchasing is now completely transformed,” Ryan explains. “We no longer rely on flagged emails or manual updates. Requirements come up at the right time based on supplier lead times, and we can create purchase orders directly from those requirements. We review pending POs each week, check if deliveries have arrived on time, and follow up with suppliers if needed. It’s a huge improvement.”
MRPeasy has also eliminated the reliance on Excel sheets for inventory tracking. The system’s real-time updates ensure that stock levels are always accurate, and aging stock can be identified and prioritized for sales.
“With MRPeasy, we know exactly when stock came in and can push older items for sale,” Ryan says. “It’s also easy to manage FIFO stock rotation, ensuring we use the oldest inventory first.”
Achieving a seamless order flow
From a wider perspective, the system provides Arcus with comprehensive insights into their operations, from project profitability to lead time accuracy.
“We can track every stage of a project, see our profit per project, identify delays, and adjust processes as needed,” Ryan explains.
According to Ryan, one of MRPeasy’s stand-out features is the Matrix BOM, which allows users to create manufacturing orders for configurable products without creating a separate bill of materials for each variant. Often missing from even much more expensive solutions, the Matrix BOM is essential for companies that manufacture multiple configurations of a base product.
Arcus has also integrated MRPeasy with their WooCommerce and eBay sales channels, streamlining order management across platforms.
“The integrations have been great,” Ryan says. “Orders flow seamlessly into MRPeasy, making inventory and order tracking effortless.”
Advice for manufacturers considering software
Reflecting on their journey, Ryan offers practical advice for manufacturers evaluating MRP systems. “Start with a clear plan for stock categorization and SKU creation,” he recommends. “We experimented with complex naming schemes, but a simple, structured approach worked best.”
He also emphasizes the importance of involving team members with ERP or MRP experience. “Our engineers had prior exposure to large systems, which helped them adapt quickly,” Ryan notes.
With MRPeasy, Arcus Cleaning Systems has not only optimized their operations but also positioned themselves for future growth. “The system has given us confidence in our processes,” Ryan says. “It’s streamlined everything from purchasing to production, allowing us to focus on innovation and customer satisfaction.”
Ryan concludes with a strong endorsement: “MRPeasy has been brilliant for us. It’s a reliable, flexible, and cost-effective solution I would recommend to any small or medium-sized manufacturer.”
You may also like: Manufacturing Consultant Finds Alignment with MRP Software