Control Estadístico de Procesos – Guía del fabricante
El control estadístico de procesos puede ser un método inestimable para descubrir y encontrar soluciones preventivas a los problemas de producción, garantizar la conformidad de los productos, aumentar la productividad y reducir los desechos.
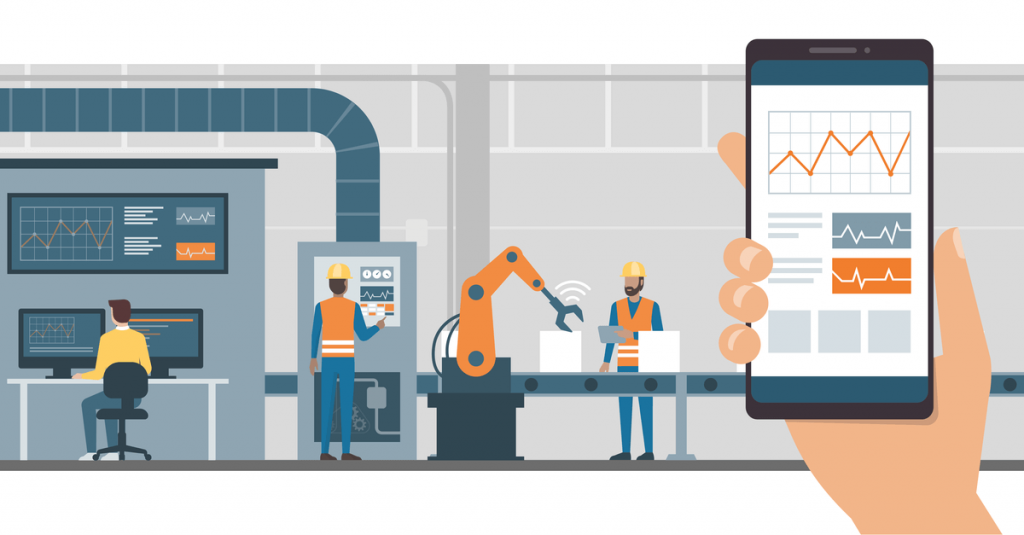
¿Qué es el control estadístico de procesos?
El Control Estadístico de Procesos (SPC) es un proceso industrial estándar basado en datos que utiliza métodos estadísticos para supervisar la calidad y descubrir incoherencias en los procesos de fabricación. El objetivo del SPC es determinar la conformidad de un proceso con los requisitos del cliente, garantizar su estabilidad e identificar cualquier incoherencia, a menudo antes de que el proceso se complete o incluso se inicie.
Una distinción clave entre muchos métodos de aseguramiento de la calidad y el SPC es que, mientras los primeros suelen basarse en la detección o determinan la conformidad de los artículos en la fase de inspección, el SPC intenta predecir cualquier problema antes de que surja, lo que lo convierte en un método preventivo. Por tanto, el SPC tiene un gran potencial para reducir los desechos, controlar los costos y aumentar la eficacia general de la fabricación.
Las empresas de fabricación recurren cada vez más a los sistemas MRP y ERP para impulsar la eficacia y el control de sus procesos. Pero incluso con el mejor sistema MRP de su clase, las empresas de fabricación necesitan una filosofía y una forma sistematizada de medir la producción para garantizar su calidad. El SPC representa una transición desde los procesos independientes de inspección posterior a la producción hacia la supervisión preventiva y continua dentro de la fabricación. Utiliza diversas herramientas, como gráficos de ejecución, gráficos de control, diseño de experimentos e iniciativas de mejora continua.
Historia del control estadístico de procesos
El control estadístico de procesos existe desde hace algo más de un siglo. Desarrollado por primera vez por Walter Shewhart, de los Laboratorios Bell, el concepto inicial y el uso de gráficos de control se pusieron a trabajar en el desarrollo de una base estadística para el muestreo de materiales producidos para municiones a principios de la década de 1930.
Con la ayuda de W. Edwards Deming en el desarrollo de cursos de formación sobre calidad utilizados en la industria estadounidense en la Segunda Guerra Mundial y posteriormente durante la ocupación, el SPC se introdujo también en Japón.
Shewhart, clave en la creación del SPC, identificó desde el principio dos tipos de variación en los procesos. La primera era la variación fortuita, definida como una variación inherente a un proceso. La variación fortuita es estable en el tiempo y, por tanto, puede medirse y contabilizarse. Dentro de la terminología del SPC, la causa fortuita pasó a conocerse como variación de causa común.
El segundo tipo de variación es la variación no controlada. La variación no controlada se atribuye a sucesos que ocurren fuera del sistema de producción. Este tipo de variación se conoce como variación de causa especial dentro del SPC.
A medida que Shewhart identificaba estos tipos de variación, desarrollaba gráficos de control que permitían a los fabricantes trazar datos sobre una curva temporal y discernir tanto la variación de causa común como la de causa especial. Estos gráficos y herramientas siguen formando parte del núcleo del SPC en la actualidad y, a medida que se ha desarrollado la metodología, también se han añadido otras herramientas.
Cómo funciona el control estadístico de procesos
Todos los procesos presentan variaciones. Sin embargo, Shewhart descubrió pronto que, a diferencia de los fenómenos naturales, la variación en los procesos de fabricación tenía un patrón de comportamiento diferente al de los sucesos naturales. Fue aquí donde se desarrolló la distinción entre causas comunes y especiales de variación.
La variación por causa común consiste en causas aleatorias y problemas que surgen de forma natural en relación con el proceso. Puede ser que un empleado tarde más en realizar una tarea que otro. O podrían ser variaciones que se producen en función de los cambios de temperatura ambiente dentro de las instalaciones, de turnos de tarde más fríos a turnos de día más cálidos. Un último ejemplo podría ser el desgaste medible de las piezas de una máquina, en cuyo caso pueden hacerse ajustes con el tiempo para mantener el proceso bajo control a medida que se desgastan las piezas.
Más información sobre Gestión del mantenimiento.
Otras causas pueden ser errores de medición, falta de procedimientos definidos y otras. Si la variación de causa común es predecible, históricamente comprendida y no afecta a valores excesivamente altos o bajos, entonces es probable que la variación esté dentro de 3 desviaciones estándar del promedio y se considera “En Control” o estadísticamente estable.
La variación por causa especial consiste en sucesos que históricamente no han formado parte del proceso medido y observado. También son impredecibles y a menudo causan una alteración que empuja los datos fuera del gráfico de control predecible para ese período medido.
Un ejemplo podría ser un apagón intermitente que detiene y pone en marcha la producción durante un periodo. Otro ejemplo sería un fallo informático o un problema de ciberseguridad en el que los ordenadores que controlan los equipos son pirateados.
La diferenciación entre variación por causas comunes y especiales permite a los responsables de fabricación adoptar respuestas adecuadas en función del tipo de variación.
Las variaciones de causa común pueden ajustarse o abordarse sin que todo el proceso quede fuera de variación, como cuando los mecánicos ajustan las piezas que se desgastan de forma natural para mantener el producto dentro de unos márgenes aceptables o cuando los directivos ofrecen formación adicional para ayudar a los empleados a mejorar el tiempo dedicado a la tarea.
Las variaciones por causas especiales pueden requerir medidas más agresivas o correctivas o recursos externos para devolver el sistema de producción a un estado en el que esté bajo control.
El SPC utiliza un conjunto estándar de herramientas estadísticas y analíticas para controlar las entradas del proceso. Estas entradas del proceso son variables independientes que se introducen en las herramientas específicas para proporcionar información y análisis que permitan determinar si el proceso está bajo control y qué medidas deben tomarse para mantenerlo.
Lea también sobre el Costo de la calidad y cómo calcularlo.
Herramientas de control estadístico de procesos
A medida que el Control Estadístico de Procesos se fue desarrollando a lo largo del siglo pasado, se fue utilizando un conjunto estándar de herramientas estadísticas y analíticas. Las siete primeras se denominan herramientas “QC”, o “7-QC”, de control de calidad. A medida que se desarrollaron la disciplina y la metodología, se desarrollaron 7 “herramientas suplementarias” adicionales (7-SUPP) para mejorar el proceso. Las siete herramientas de control de calidad (7-QC) son:
- Diagrama de causa y efecto: El Diagrama de Causa y Efecto también se conoce como Diagrama de Espina de Pescado. Se trata de un método de análisis de causas que permite identificar muchas causas diferentes que pueden haber sido responsables de la variación. Esta herramienta se utiliza cuando se desconocen las causas de la variación o quizá estén relacionadas con otras causas. Es bastante habitual utilizar el proceso de los “5 porqués” cuando se utiliza la causa y el efecto para determinar la causa raíz de la variación.
- Hoja de control – Una hoja de control es una herramienta básica de recolección de datos que permite el análisis a partir de los datos recogidos. Si los datos pueden ser observados y recogidos por un miembro del personal en el mismo lugar y con la misma frecuencia, una hoja de control puede ser una fuente de datos para determinar problemas y variaciones.
- Gráfico de control – Los gráficos de control se utilizan para representar los cambios del proceso a lo largo del tiempo. Cada gráfico de control tiene un límite de control superior e inferior, así como una línea promedio. Mediante la observación de los datos en tiempo real, se puede hacer una comparación en el tiempo para determinar si el proceso está bajo control o fuera de control. Los gráficos de control son excelentes para identificar las variaciones a medida que se producen o para determinar si un proceso es estable. También pueden utilizarse en variaciones por causas especiales y para ayudar a determinar qué medidas deben tomarse.
- Histograma – Los histogramas representan los datos como diagramas gráficos de grupos de datos utilizando rangos definidos por el usuario. En muchos sentidos, es como un gráfico de barras. Un histograma agrupa los datos en rangos donde pueden ser interpretados por el usuario. Ayudan a entender el número de veces que una variable específica ocurre dentro de un rango especificado.
- Diagrama de Pareto – Todo el mundo ha visto alguna vez un diagrama de Pareto. Los diagramas de Pareto se utilizan para delinear el valor o el tiempo como un gráfico de barras de mayor a menor. Esto proporciona al usuario una representación gráfica del uso del tiempo, el costo o la frecuencia empleados para un activo o variable en particular. Los diagramas de Pareto resultan útiles para determinar la frecuencia, analizar el costo por componente o determinar la causa más significativa para iniciar una acción.
- Diagrama de dispersión – Un diagrama de dispersión se utiliza cuando se analizan dos variables para determinar su relación y determinar lo estrechamente relacionadas que están. Si los puntos trazados están dispersos por el diagrama, menos se percibe su correlación. Si están cerca de la línea, más estrecha es la correlación. Los diagramas de dispersión se utilizan en situaciones en las que los datos pueden emparejarse, como para determinar si dos efectos se han producido por la misma causa.
- Estratificación – En pocas palabras, la estratificación se utiliza para agrupar y clasificar los datos en categorías. Como los datos brutos deben categorizarse para ser útiles, la estratificación se utiliza mejor antes de la recogida de datos para saber dónde asignar los puntos de datos individuales para su posterior análisis. Esto puede incluir turnos, semanas, proveedores o tipos de productos.
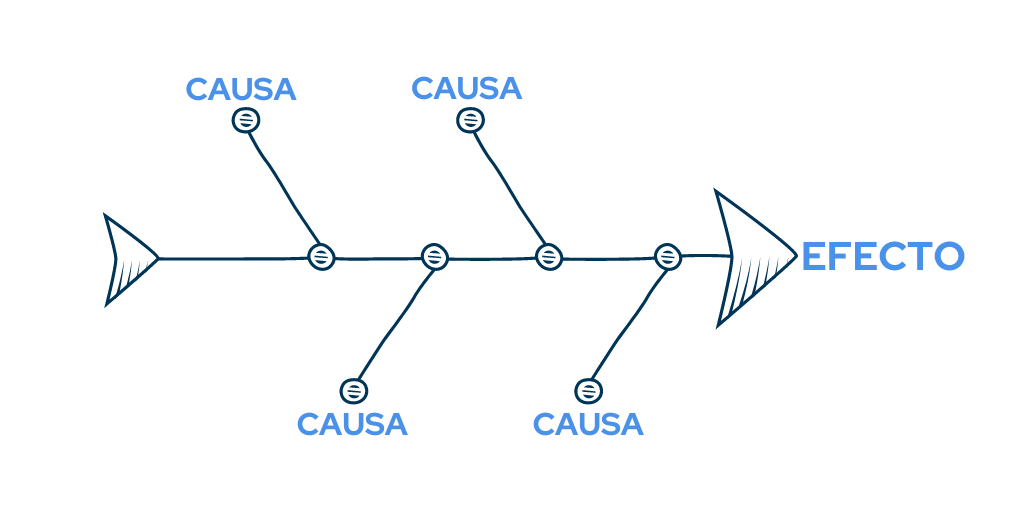
Las siete herramientas complementarias (7-SUPP) incluyen:
- Estratificación de datos – Al igual que la estratificación, la estratificación de datos agrupa los datos en categorías. Al dividir los datos en categorías como turno, máquina, departamento, material, proveedor y otras variables, se pueden determinar patrones para ayudar a definir y controlar la variación.
- Mapas de defectos – Los mapas de defectos son una forma de visualizar el artículo evaluado en cuanto a calidad. La visualización permite un análisis rápido por parte de un equipo Seis Sigma u otro equipo de mejora de procesos para la adopción de medidas correctivas. En un mapa de defectos, los operarios o técnicos pueden marcar el lugar donde han encontrado un defecto en un plano de especificaciones. Esta representación visual de la ubicación y el índice de defectos permite al equipo encargado de la mejora buscar las causas anteriores para corregirlas.
- Registros de eventos – A medida que la automatización a través de IIoT e incluso la automatización de ERP y MRP ha dado lugar a datos en tiempo real a nivel de máquina fácilmente accesibles, los registros de eventos han adquirido mayor importancia. Los registros de eventos son recopilaciones de datos con descripciones escritas de eventos en torno a una variable que ha introducido una variación. Permite a los usuarios ver lo que experimentó el personal de la línea de producción o el computador en el momento en que se produjo la variación.
- Diagramas de flujo de procesos – Es imposible mejorar un proceso sin comprender la progresión lineal del mismo. Un diagrama de flujo de procesos es una herramienta no estadística que traza las etapas del proceso. Al definir completamente los pasos del proceso, se pueden utilizar otras herramientas de SPC para todo el flujo del proceso o para los pasos dentro del diagrama de flujo. Ayuda a comprender lo que hay que medir y a crear un consenso sobre los pasos del proceso para poder aplicar otras herramientas de SPC.
- Centros de Progreso – Los centros de progreso son las herramientas utilizadas para centralizar y seguir el progreso para ayudar a guiar la toma de decisiones. Recopilando datos sobre el progreso del proyecto y trazándolos, los usuarios pueden determinar la probabilidad de que se complete en el tiempo previsto y adoptar medidas correctoras para volver a encaminarlo si se desvía de la programación prevista.
- Aleatorización – La aleatorización es un intento de hacer que una variación se produzca por casualidad. Se trata de un experimento para eliminar el sesgo y crear las condiciones para que se produzca una variación de forma natural y permitir a los analistas encontrar la causa raíz. La eliminación del sesgo significa que los usuarios pueden identificar la variación antes de que se produzca y ajustarla en consecuencia.
- Determinación del tamaño de la muestra – Hay un viejo refrán que dice que no se puede medir lo que no se puede contar. Pero también es importante tener un número estadísticamente aceptable de cosas que contar. La determinación del tamaño de la muestra se utiliza para ayudar a establecer el número de elementos, artículos, personas, turnos u otras unidades de recuento que se utilizarán en un grupo representativo para el recuento.
Variaciones en la fabricación
Dado que nunca habrá dos productos exactamente iguales, los procesos de fabricación basados en las mejores prácticas tratan de controlar la variación para garantizar que la producción cree el facsímil más parecido posible. Al reducir la variación hasta que sea estadísticamente insignificante, se garantiza la repetibilidad y los consumidores no pueden percibir los productos como diferentes entre sí.
He aquí algunos ejemplos prácticos de variaciones que pueden controlarse en la fabricación:
- Desgaste – Ejes, correas, poleas, engranajes y otros componentes se desgastan con el tiempo. Esto no significa que los componentes hayan llegado al final de su ciclo de vida. Es posible medir el grado de desgaste y analizar sus efectos para realizar ajustes que optimicen su ciclo de vida y mantengan el valor de la pieza sin dejar de producir bienes de alta calidad. Estos ajustes pueden medirse y trazarse utilizando el SPC para determinar cuándo realizarlos en función del tiempo y de las variables del producto que generan el desgaste.
- Condiciones – La mayoría de las operaciones de fabricación se desarrollan en un horario de 24 horas con funcionamiento continuo. Dependiendo de la geografía, no es raro que haya grandes oscilaciones de temperatura, humedad y presión barométrica de la noche al día y del turno de día al de tarde. El SPC puede determinar la cantidad y el grado de ajuste necesarios en función del intervalo y de la estación del año.
- Estacionalidad – Muchas empresas manufactureras tienen una plantilla estable durante todo el año. Sin embargo, otras tienen elementos totalmente estacionales en sus operaciones o al menos cierto grado de estacionalidad. Para aquellas cuya operación añade personal en diferentes épocas del año para aumentar la mano de obra regular, pueden producirse variaciones debido a la formación. El SPC permite a los gestores tener esto en cuenta en el tiempo, las unidades producidas y otros indicadores clave de rendimiento para ajustar la variación.
- Diferenciación de lote a lote – En muchas industrias, los lotes difieren de un proveedor a otro, de una temporada a otra o de un lote a otro. Un ejemplo serían los productores de productos básicos que dependen de materias primas de producción estacional, como el algodón. Ligeras diferencias en la longitud de la fibra, la densidad y otros factores pueden dar lugar a variaciones en los fabricantes de toallas o sábanas, donde el análisis SPC puede ayudar a mitigar estos efectos para permitir un rendimiento continuo según las especificaciones. Lo mismo puede ocurrir con los procesadores de alimentos que tienen problemas con el contenido de azúcar o las materias primas minerales con distintos niveles de impureza.
Control Estadístico de Procesos en la Fabricación
La aplicación del SPC en la fabricación requiere varios pasos básicos. En primer lugar, los fabricantes deben conocer su proceso, el flujo de trabajo, los puestos de trabajo y los requisitos de especificación de sus productos. En las grandes empresas, es posible que los ingenieros industriales hayan medido estos elementos durante la fase de diseño. Sin embargo, en las pequeñas y medianas empresas, es fundamental documentar y medir completamente estos procesos, especialmente a medida que la empresa crece, para que las variaciones no se salgan de control.
En segundo lugar, hay que esforzarse por eliminar las causas especiales de variación para que sólo queden las causas comunes. Esto permite a los directivos y planificadores desarrollar mejoras del proceso centradas en los aspectos comunes y controlables de la producción. Al minimizar los límites superior e inferior, muchas variaciones pueden volverse estadísticamente irrelevantes a medida que mejora el proceso.
Por último, las empresas pueden utilizar las herramientas y gráficos que han sido el pilar del SPC durante muchas décadas para proporcionar una supervisión continua del proceso. El proceso de supervisión puede ayudarse de herramientas de automatización como la tecnología IIoT e incluso la funcionalidad nativa del software MRP y ERP.
Utilizando todas las herramientas disponibles a través del SPC, el objetivo es mejorar continuamente un proceso que no presente variaciones por encima o por debajo de los límites superior e inferior. De este modo, el proceso se considera “estable”.
Ventajas de utilizar el control estadístico de procesos
Cuando se aplica correctamente, el Control Estadístico de Procesos puede ayudar a perfeccionar su proceso de fabricación para eliminar la variación. Algunas de las ventajas de utilizar el SPC son:
- Reducción de desechos – Al reducir la variación, se reducen o eliminan los desechos y los re-procesamientos. Esto tiene un beneficio directo en términos de costos, además de liberar capacidad.
- Productividad – Dado que la mejora continua de los procesos derivada del SPC es más eficaz, la productividad mejora.
- Mejora continua – Como el proceso se supervisa continuamente, se puede mantener el control de todos los procesos. Esto permite realizar análisis casi en tiempo real para detectar los problemas antes de que se produzcan y realizar los ajustes necesarios.
- Toma de decisiones más fácil – Como el SPC analiza los datos y utiliza el análisis estadístico para corroborar los resultados, la toma de decisiones es más fácil y el impacto de las decisiones es mayor.
- Evaluar la capacidad de proceso – Todas las empresas quieren crecer. Y a medida que crece la oferta de productos de una empresa, se tiende a sobrepasar la capacidad de los equipos existentes. El SPC puede ayudar a cotejar la capacidad del proceso con las especificaciones reales del producto. Esto permite a los responsables de la toma de decisiones comprender cuándo deben añadir equipos o maquinaria o actualizar la capacidad existente para reducir las variaciones en la oferta de nuevos productos.
Dado que todos los procesos tienen variaciones, el SPC puede utilizarse para predecir y mejorar con el fin de llevar esa variación a un rango aceptable o estadísticamente irrelevante. Al trazar un curso utilizando SPC, una empresa de fabricación puede determinar los principios rectores de su calidad para que coincidan con las capacidades de su software ERP o MRP o incluso utilizarlos junto con dicho software para multiplicar el valor de SPC.
Conclusión
El Control Estadístico de Procesos es un método para mejorar la calidad en el lugar de trabajo. Utiliza herramientas estadísticas para encontrar y detectar incoherencias en el proceso de producción e identificar las causas de la no conformidad del producto.
El enfoque distingue dos tipos de variaciones: Causas comunes y causas especiales. En general, las variaciones de causa común son previsibles y pueden remediarse, por ejemplo, con el mantenimiento de los equipos o la formación del personal. Las variaciones de causa especial son imprevisibles y a menudo requieren ayuda externa, por ejemplo, en el caso de una interrupción del servidor.
El SPC utiliza una plétora de herramientas que se dividen en las siete herramientas de control de calidad (7-QC) y las siete herramientas suplementarias (7-SUPP). Se trata de diagramas, gráficos, técnicas de categorización, etc.
Cuando se aplica correctamente, el Control Estadístico de Procesos puede mejorar notablemente los procesos de fabricación, ayudar a minimizar los residuos y contribuir a una mayor productividad y mejora continua.
También le puede interesar Gestión de materiales – Buenas prácticas para pequeños fabricantes.